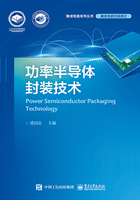
2.3 热设计
电子器件的电能集中在芯片处,并在芯片较小区域集中产生大部分热量,形成芯片最热部位,该部位称为结点(Junction),其温度称为结温。芯片的结温与封装体内部的温度分布、功耗、芯片的散热路径、热界面材料、散热条件以及所处系统的环境温度等因素密切相关。电子产品的热设计指的是通过采用合理的散热技术和结构,优化设计方案,使结温不超过器件所允许的最高温度(对于硅功率器件,通常最高允许温度不超过150℃,连续工作温度不超过125℃),保证器件及模块正常可靠地工作。
根据经验,电子器件温度每升高10℃,平均可靠性降低50%。这条经验基于阿伦尼乌斯方程(Arrhenius Equation),该方程表明了温度应力对物质的化学与物理变化的影响,在分析失效时未考虑湿度、机械应力、电学等因素的影响,存在一定局限性。芯片结温与10万小时故障率的关系如图2-6所示。根据美国空军航空电子设备完整性计划的统计结果,电子器件的主要失效原因包括振动、灰尘、湿气和温度,其中温度影响造成的失效占55%,如图2-7所示。

图2-6 芯片结温与10万小时故障率的关系
(来源:GEC Researh)

图2-7 电子器件的主要失效原因
(来源:US Air Force Avionics Integrity Program)
随着功率半导体封装集成度不断提高、体积不断缩小、功率密度不断增加,散热问题成为功率半导体封装中的重点和难点。功率半导体器件的作用主要是实现电能的变换和控制,在开关控制过程中会产生较大的功耗,热管理是封装设计中的关键环节。功率半导体器件封装所涉及的热问题主要包括稳态温度,由瞬态温度变化、温度循环、温度冲击、功率循环等造成的温度梯度,以及封装材料相互之间热膨胀系数不匹配所带来的热失配问题。其中,热失配问题会在封装结构内产生热应力,进而导致热应力疲劳损坏、断裂等热机械失效问题,易失效点通常出现在引线键合点位置、焊料层、芯片及基板上。
2.3.1 传热理论基础
热传递方式一般有热传导、热对流、热辐射三种。热传导是热量从高温向低温传递的过程;热对流是冷热流体各部分之间发生相对位移而相互掺混所引起的热量传递过程,常伴有热传导;热辐射是直接通过电磁波辐射向外发散热量的过程。
功率半导体器件封装涉及的热量传递方式主要有热传导和热对流。
热传导问题可以采用傅里叶方程来描述:

式中,q为热流密度,单位为W/m2;为法向温度梯度,单位为℃/m;λ为热导率,单位为 W/(m·K),表征了材料导热性能的优劣;等式中的负号表示热量传递的方向与温度升高的方向相反。
对流传热过程是流体流经固体表面时的热量传递过程,通常采用牛顿冷却公式进行描述:

式中,q为对流传热的热通量,单位为W/m2;h为对流换热系数,单位为W/(m2·℃);tw为壁温,单位为℃;t为冷流体主体温度,单位为℃。对流换热系数h与物体表面的几何形状和流体的物理性质相关,其典型值列于表2-4。
表2-4 对流换热系数典型值

2.3.2 热阻
热阻(Thermal Resistance)是热设计中最重要的参数。热阻表征了热量在热流路径上遇到的阻力。当有热量在物体上传输时,将物体两端温度差与热源的功率之比定义为热阻。当热量流经热阻时,就会产生温差,这与电流流经电阻产生压差类似。热阻越大,热量越难传导,器件温度也就越高。因此,热阻是衡量器件散热能力的重要指标。
在功率半导体封装中,热阻常表达为功耗和结温之间的关系,表征了封装的热学性能,公式为

式中,Rjx为热阻,单位为℃/W;P为单个器件的功耗,单位为W;Tj和Tx分别为结温和参考点温度(参考点的选取是任意的),单位均为℃。
功率半导体器件所产生的热量散发路径主要包括封装顶部到环境、封装底部到热沉和封装引脚到热沉。以下给出常用的参考点选取方法及典型封装热参数。
1.结-环境热阻(Junction-to-Ambient Thermal Resistance)
不管采用何种封装形式,热量最终都会从芯片扩散到周围环境中,因此,将结-环境热阻作为衡量封装热性能的有效指标之一。选取环境为参考点,则结-环境热阻Rja定义为

式中,Tj和Ta分别为结点温度和环境空气温度;P总为芯片总功耗。
2.结-壳热阻(Junction-to-Case Thermal Resistance)
芯片产生的热量从芯片开始,通过封装内部各种复杂路径传递到封装管壳,再扩散到空气中,因此,用结-壳热阻Rjc来表征热量传递到外部热沉的能力,Rjc越小,则意味着热量越容易流入外部热沉。需要注意的是,结-壳热阻Rjc只适用于绝大部分或全部热量都通过封装顶部或底部的热沉散出的情况。选取封装管壳为参考点,管壳为主要传热路径中的封装外表面,则结-壳热阻Rjc定义为

式中,Tj和Tc分别为结点温度和管壳温度;Pjc为芯片传递到封装管壳的功耗。
3.举例:IGBT模块热阻分析
传统IGBT模块在使用时,通过导热硅脂将模块贴装在具有翅片设计的热沉上,如图2-8 所示,封装结构紧凑,多热阻界面造成高热阻,散热成为封装设计的难点之一。

图2-8 典型IGBT模块散热结构及热阻网络示意图
很大一部分热阻来自模块的底板和内部绝缘陶瓷,且与材料的热导率、厚度、尺寸等密切相关。功率电子模块中常用材料的性能列于表2-5中。然而高热导率材料的使用势必造成封装成本的增加,在工业生产中并不适用。在满足电学性能和力学性能需求的前提下,减小各部件的厚度成为降低热阻较为有效的方法。
表2-5 功率电子模块中常用材料的性能

热阻的计算根据接口设计、热设计、电气设计形成的模块封装结构进行仿真计算。
稳态热阻是一个与恒定功率有关的概念。稳态热阻由模块的堆叠结构与组成材料的热特性决定,理论计算公式如下:

式中, Rjc为IGBT模块的结-壳热阻,单位为℃/W;λi为不同层材料的导热系数,单位为W/(m·℃);Ai为不同层材料的传热面积,单位为m2;δi为不同层材料的厚度,单位为m。
瞬态热阻是一个与热传递过程有关的概念。瞬态热阻不能用一个简单的数值来表示,应用一组与应用条件有关的函数曲线来表示:

式中,Z为瞬态热阻;Ri为各组成材料的稳态热阻,单位℃/W;Ci为各组成材料的热容量;τi为各组成材料的热时间常数;t为热传递过程的变化时刻。
根据IEC 60747,在输入等幅周期矩形脉冲时,当器件达到动态热平衡时,瞬态热阻可以简化为

式中,ΔTj(tq)为PN结的温升,单位为℃;P为矩形脉冲的功率,单位为W;Ri为各组成材料的稳态热阻,单位为℃/W;τi为各组成材料的热时间常数;t1、t2为矩形脉冲的波形参数。
由式(2-11)可以得到该工况下IGBT模块的关键参数,包括最高结温限值、受环境约束的壳温、模块结构的瞬态热阻模型。
2.3.3 常见功率半导体器件的冷却方法
对于功率半导体器件,散热方法可分为被动散热和主动散热。被动散热方法通过改变材料本身的性质或结构设计来实现散热,如应用热界面材料(如高热导率的导热硅脂、导热胶)、优化设计外部热沉(如翅片式热沉)、优化器件及系统结构配置等。主动散热方法利用外力来实现散热,如气体强迫对流(风冷)、应用材料相变原理的热量传递(如热管技术)、半导体制冷、液体强迫对流(微喷、微通道)等,有针对性地对热源进行高效散热。
以下列出几种功率半导体器件的常用冷却方法。
1.风冷
风冷由于应用便捷、成本低廉,在热管理中被广泛使用,但是其散热能力有限,适用于散热密度较低的场合。为了提高风冷散热能力,可采用散热片、翅片式热沉或其他强制对流方法。图2-9所示为翅片式和针状阵列式热沉结构。

图2-9 翅片式和针状阵列式热沉结构
2.热管
热管发明于1963年,通常由管壳、吸液芯和端盖组成,介质在热端蒸发后在冷端冷凝,其利用热传导原理和相变介质快速传递的性质,将发热物体的热量迅速传递到热源外。热管具有导热性高、温度均匀性高、对环境适应性强等优点。
热管技术现已广泛应用于功率半导体器件的散热。例如,直接在DBC基板中制作热管,减少热界面层,进而降低热阻,有效地解决了功率密度大于80 W/cm2的IGBT模块的散热问题,如图2-10所示[15]。

图2-10 DBC基板内置热管
3.微喷射流
微喷射流散热方法主要采用微泵驱动系统循环,利用微喷阵列将工作介质(水、冷却液、空气甚至液态金属)喷射到待散热器件上,将热量从器件传递到冷却系统中,从而实现高效散热。例如,将微喷阵列冲击制冷的方法应用到功率密度大于200 W/cm2的1200V、150A的IGBT模块中,如图2-11所示,试验结果证明了该方案的底板到环境的热阻Rba仅为0.013℃/W,相对于传统的带翅片强制风冷方案(Rba=0.05℃/W)及液冷冷却板方案(Rba=0.036℃/W),散热性能有较大的改善[16]。
4.微通道液冷
微通道散热技术于1981年由斯坦福大学的Tuckerman和Pease最先提出[17],由于可以与现有模块的基板直接集成,可适用性强、可设计性强,且散热能力卓越、热均匀性好而备受关注,其主要思路为在集成电路的硅衬底背面刻蚀出微米级的矩形微通道结构,通过冷却液流动回路将集成电路芯片的热量带走,实现高热流密度器件的高效散热。此后,微通道散热方法被广泛应用于电子器件中。将微通道和功率半导体封装中的基板或底板集成为一体,可缩短热传输路径,降低热阻,并且通过微通道的结构设计可以实现温度分布均匀并对微通道的散热能力进行优化。这种散热技术近年来在IGBT模块中被大量使用。

图2-11 微喷阵列散热
在微通道散热技术的基础上,研究人员进一步开发出双面制冷方案。例如,在两个DBC基板中间键合一层带有微通道结构的铜层,形成可水冷的三维结构[18];或者将双面制冷和高集成化要求结合起来,在芯片两侧各贴装一块DBC基板,并在DBC基板的外侧铜层中加工微通道,如图2-12所示,实现功率半导体器件中双层双面冷却的液冷散热。与单层冷却相比,双层双面冷却的散热效率提高了59%,并且温度均匀性良好[19]。还可以利用倒装焊技术,在芯片两侧均焊接DBC基板,再分别放置带微通道的水冷热沉,实现双面液冷[20]。

图2-12 芯片两侧各贴装一块DBC基板(在DBC基板的外侧铜层中加工微通道)
2.3.4 热仿真及优化设计
1.采用热沉散热的传统IGBT模块热仿真分析
由于 IGBT 芯片不能做得像双极型器件那样大,需将若干 IGBT 芯片进行并联才能满足几百安或上千安级别的应用需求。为了实现多芯片的 IGBT 模块封装结构的热管理,使模块内温度分布均匀,将IGBT芯片及其配套FRD芯片焊接在衬板上,并通过引线键合将芯片表面的电极与衬板电路互连;将衬板焊接在基板上,并通过将母排焊接在衬板上,实现衬板间的互连,同时提供与外部电路连接的接口;PCB则将每个衬板的控制极进行互连,并提供与外部控制电路连接的接口。然后通过安装管壳,在模块中注入硅胶,实现模块内部各器件的电气绝缘,同时可防止外部环境湿气和粉尘侵入模块,并注入环氧树脂确保模块的机械强度。灌封型IGBT模块的结构如图2-13所示。
应用过程中,IGBT 模块在开关过程中以及导通状态下都会产生热损耗,若不能及时将热损耗散发出去,就会形成局部热量聚集,造成芯片因结温过高而失效。为了实现及时将热损耗散发出去的目标,散热面积从内到外(芯片→衬板→基板→散热器)是逐步增大的。
为了分析采用带翅片热沉强制对流散热的 IGBT 模块的热性能,采用有限元法进行建模与仿真,对模块进行热分析。由于芯片位置不同,整体模块不呈现对称性,故对整体模块建立三维模型进行分析。硅基芯片通过无铅焊料SAC305贴装在DBC基板上,DBC基板再通过SAC305贴装在铜底板上,之后经过回流焊接工艺,一次性完成两层焊料层的焊接。然后通过引线键合工艺将粗铝线键合到芯片、DBC基板及电极端子上,实现模块的电气连接。最后通过点胶工艺将塑料外壳安装到铜底板上,并在模块内部灌注硅凝胶实现防振动、防潮和绝缘保护。
对IGBT模块进行热分析时,需要进行下述假设及简化:①由于键合引线相对整体模型所占比例较小,因此为了简化计算,在建模过程中忽略键合引线;②由于涂覆在芯片及键合引线表面的硅凝胶的导热系数很小[仅为0.5~1W/(m·K)],且热传递的路径主要是从顶部的芯片通过热传导方式传递到底部的底板的,其余表面假定为绝缘表面。

图2-13 灌封型IGBT模块的结构
IGBT模块在工作状态下,芯片的功耗为内部热源。由于分析的是模块级的宏观热性能,故不考虑芯片的内部结构,直接将功耗作为体热源加载到芯片体中。通常以英飞凌(Infineon)公司的IPOSIM软件的算法为基础,根据芯片和FRD芯片的特性参数取值,计算既定工况下的功耗。
IGBT模块的导通损耗Pcond为

式中,VCEO为IGBT模块零电流初始正向压降;r1为IGBT模块正向特性曲线的斜率电阻;m为PWM调制系数;cosφ为功率因数;Im为IGBT模块的工作电流。
IGBT模块的开关损耗为

式中,fsw为工作频率;Eon为IGBT模块开通能量损耗;Eoff为IGBT模块关断能量损耗;Im为模块工作电流,取Im=Inom;Vdc为模块工作电压,取Vdc=Vnom。
IGBT模块的功率端子由寄生电阻产生的功耗为

式中,Rter为功率端子寄生电阻;I为功率端子流经的电流。
IGBT模块的平均总损耗Pav =Pcond+Psw+Pter。
IGBT 模块所涉及的热量传递方式主要是热传导和热对流,其中,对于传统IGBT 模块,热对流主要通过带翅片的热沉进行强迫对流换热。采用商业有限元软件Fluent进行建模,采用热沉散热方式,IGBT模块金属基板底面所带来的对流换热系数设置为0.7W/(cm2·K)。IGBT模块相关材料特性如表2-6所示,采用热沉散热的IGBT模块温度分布如图2-14所示,最高温度为85.2℃。
表2-6 IGBT模块相关材料特性


图2-14 采用热沉散热的IGBT模块温度分布
2.热优化设计:采用微通道液冷方案实现IGBT模块散热
为了提高模块的散热能力,降低模块质量,去除热沉,采用预置微通道液冷的方法对模块进行散热。在铜底板中预置微通道结构,其底板结构示意图和加工完成的预置微通道底板的SAM测试图分别如图2-15和图2-16所示。图2-17为集成微泵底板预置微通道的IGBT模块装置图。

图2-15 预置微通道的底板结构示意图

图2-16 加工完成的预置微通道底板的SAM测试图

图2-17 集成微泵底板预置微通道的IGBT模块装置图
对预置微通道的 IGBT 模块进行热分析时,需要进行下述假设及简化:①假设微通道中流体的热物性为常数,并且流体不可压缩,忽略体积力作用;②由于键合引线相对整体模型所占比例较小,因此为了简化计算,在建模过程中忽略键合引线;③由于涂覆在芯片及键合引线表面的硅凝胶的导热系数很小,仅为0.5~1W/(m·K),且热传递的路径主要是从顶部的芯片通过热传导方式传递到底部的底板,因此除了微通道的内壁及暴露在空气中的底板底面存在对流换热,其余表面假定为绝缘表面。
根据上述假设,利用商业有限元软件Fluent对微通道单相湍流进行CFD有限元仿真。对于热性能分析,考虑到网格划分情况对有限元分析结果的影响,对网格进行合理划分,采用自由四面体网格,网格尺寸为1~2mm。有限元几何模型如图2-18所示。
对于预置微通道的IGBT模块,其对流传热的表面传热系数h(又称对流换热系数)取决于微通道中流体的物性、流速及微通道的形状、尺寸和位置分布等。分析底板预置微通道的 IGBT 模块热性能数值仿真结果的关键在于微通道中冷却液循环流通情况下底板表面传热系数h的计算。

图2-18 有限元几何模型
模拟矩形微通道和整个 IGBT 模块的热传递过程时,考虑到流固耦合效应,使用表面传热系数 h 来表征受迫流动的冷却液的热传递能力。入口水流速度为10 m3/s,温度为20℃,并假设为压力出口。底板底面加载恒定的热流(热流密度为5W/cm2),其余表面假设为绝缘表面。有限元计算出的微通道对流换热系数 h的结果如图2-19所示,再根据这一结果计算换热系数的体积平均值,为1.9618 W/(cm2·K)。
为了验证有限元分析的准确性,使用解析方法计算对流换热系数。1971 年Webb[21]通过解析和试验的方法研究了单相流体对流换热试验关联式,并指出在光滑管道中,当0.5≤Pr(普朗特数)≤2000并且104≤Re(雷诺数)≤5×106时,使用Petukhov-Kirillov关联式可以准确地描述对流换热情况。对于在底板中预置微通道的情况,努塞尔数Nu的表达式为

式中,f为摩擦因子:


图2-19 微通道对流换热系数
将相关参数代入后计算出对流换热系数h的解析值为2.0688 W/(cm2·K),与有限元分析结果一致,证实了有限元建模仿真方法的有效性。
3.优化后热性能结果分析
与传统采用热沉散热的IGBT模块最高温度85.2℃相比,预置微通道底板的优势相当明显。底板预置微通道的IGBT模块温度分布如图2-20所示。采用新型液冷方案时,模块最高温度仅为80.43℃,比原来降低了不止4℃。由此可见,预置微通道底板IGBT模块的散热效果满足大功率密度器件的散热需求,并且去除了外部热沉,无需风扇,在保证散热能力的同时大大减小了系统的整体体积和质量。
进一步分析底板预置微通道的 IGBT 模块中每一层结构的材料及厚度对温度分布的影响。
在模块温度最高点(二极管芯片的中心位置)作纵向剖面,取底板底面为 Z轴零点,依次往上分别为铜底板、焊料层、DBC基板下铜层、Al2O3陶瓷层、DBC基板上铜层、焊料层和硅芯片。图2-21给出了IGBT模块沿Z轴方向的温度变化曲线,从中可以发现同一层材料内温度与其沿Z轴方向的距离几乎呈线性关系:不同层之间的温度变化速率与材料的热导率密切相关,其中采用水冷的预置微通道底板,温度变化很小,3mm 厚的底板温度仅升高2.7℃,在铜底板上表面达到最高温度58℃;而温度变化最剧烈的是Al2O3陶瓷层,0.38mm厚的Al2O3陶瓷层存在14℃的温度变化,这是因为Al2O3陶瓷的热导率较低。

图2-20 底板预置微通道的IGBT模块温度分布
针对上述分析,通过选用高热导率的材料来降低各层的温度升高速率。例如,在DBC基板中采用氮化铝陶瓷[热导率为319W/(m·K)]替代原有的氧化铝陶瓷[热导率为25W/(m·K)],或者用纳米银焊膏[热导率为240W/(m·K)]替代原有的无铅焊料SAC305[热导率为57W/(m·K)]。然而,高热导率材料的成本较高,在工业应用中需要根据实际需求对热性能和生产成本进行权衡。

图2-21 IGBT模块沿Z轴方向的温度变化曲线