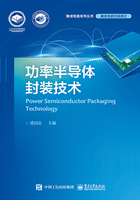
2.2 电学设计
微电子封装是指对微电子芯片或部件进行保护,并且将微电子部分和外部环境进行电气、热学和机械的连接。为了减小电力电子装置的体积和质量、提高功率密度、提高控制精度和改善动态响应,需要提高电力电子装置的工作频率。功率半导体器件开关频率不断提高导致器件寄生参数的影响增大、开关损耗增大、EMI增加。在器件开和关的瞬间寄生电感和寄生电容将会产生较大的反馈电压或者电流,与器件本身的电压或电流叠加,从而影响器件的正常工作状态,同时导致EMI增加。器件长时间工作在这样的状态下会加速其老化,甚至引起器件失效,寄生电阻的存在也加大了器件的功耗。封装的电学设计就是在封装工艺可行的前提下,结合成本估算,选择合适的封装外形和材料,设计合理的封装布局来降低封装寄生参数对器件工作性能的影响。
2.2.1 寄生参数简介
目前,功率半导体材料仍以硅为主,传统硅基的MOSFET的工作频率最高为几百千赫兹。以SiC和GaN为代表的新型功率半导体材料的工作频率可高达数十兆赫兹,封装内寄生参数的影响比第一代硅基材料更为突出。
封装内的寄生参数一般用R、L和C表示。寄生电阻R可用公式来估算:

式中,R为寄生电阻,单位为Ω;ρ为导体电阻率,单位为Ω·cm;S为导体横截面积,单位为cm2;l为电阻的长度,单位为cm。在直流情况下,封装中键合线、基板内的走线、倒装芯片上的铜柱等形状规则的导体均可用该公式估算寄生电阻。
在高频情况下,导体受趋肤效应的影响,电流趋向于在导体的外表面上流动,把电流层厚度δ近似视为固定的,并称该等效厚度为集肤深度,横截面积 S 随着频率的升高而逐渐减小,导致寄生电阻随频率的升高越来越大,所以在高频情况下,要防止寄生电阻过大,以免影响器件性能。
在高频电路中,互连线中寄生电感是一个很重要的参数。很多情况下需要减小寄生电感,如通过减小信号路径间的互感来减小开关噪声,通过减小电源分布系统的回路电感来减小封装系统的 EMI。此外,可以优化路径电感以获得所需阻抗。
为了分清磁力线的源头,电感分为自感和互感。自感表示导线中流过单位安培电流时在其周围所产生的磁力线数;同理,互感表示一根导线中流过单位安培电流时产生的环绕在另一根导线周围的磁力线数。两根导线距离越近,互感就越大,反之则越小。事实上,导线外部和导线内部都有磁力线,所以自感可分为外部自感和内部自感。在一个回路中,为了估算一段导体的电感而优化设计,提出了局部电感的概念。局部电感即假设回路中的其他部分不存在,除研究的那段导体外,其他部分没有电流。封装中键合线的局部电感可用圆杆的几何结构近似,近似公式为

式中,L为键合线的局部电感,单位为nH;r为键合线半径,单位为in(1in=25.4mm);d为键合线的长度,单位为in。根据该公式可知,键合线的局部电感约为1nH/mm。
在交流情况下,外部自感由于不通过导体,所以不会随着频率的变化而变化;而导线内部的电流分布随着频率变化而变化,所以内部自感会发生变化。与寄生电阻类似,寄生电感在交流情况下也受到趋肤效应的影响。随着频率的升高,外部自感不变,导体内部电流向表面移动,内部自感越来越小。当达到一个频率时,集肤深度仅占几何厚度的很小一部分,内部自感趋于零,从而自感就约等于外部自感。即电感随着频率升高而减小,直至趋于收敛。
电容器实际由两个导体构成,任意两个导体都存在一定的电容量。寄生电容的大小取决于导体的几何结构和导体周围材料的属性,与频率没有关系。估算寄生电容的模型有同轴模型、双圆杆模型、圆杆平面模型、微带线模型和带状线模型。在封装中,圆杆平面模型可描述键合线与参考平面的寄生电容;双圆杆模型可描述铜柱或者基板内过孔的寄生电容;微带线模型与带状线模型可描述封装基板内走线的寄生电容。模型具有一定的局限性,需在严格的条件下才能使用。如果需要得到精确的寄生电容值,则需要借助专业的场求解器。寄生电容可引起电路响应延时,电容耦合产生脉冲电压或电流,从而影响传输质量,因此在一般情况下需尽量降低寄生电容。在多层印制电路板(PCB)或封装基板中,许多电源和地层可以近似为平面板电容。平面板电容的电容量可表示为

式中,C表示电容量,单位为pF;ε0表示自由空间的介电常数,为0.225pF/in;rε表示两平面间的相对介电常数;A表示平面的面积,单位为in2;h表示平面间的距离,单位为in[6]。
根据电阻、电感、电容的近似公式可快速估算出封装体中的寄生参数,在设计初期可快速评估封装体的电学性能,在封装材料性能、价格等方面制定出大致合理的封装设计方案,从而缩短产品开发周期,节约开发费用。
封装寄生参数模型本质上是RLC集总参数模型,代表封装的无源效应。器件的 SPICE模型和 IBIS模型与封装模型不同的是,器件的 IBIS模型用来描述该器件的输入/输出行为;器件的SPICE模型记录了该器件的内部电路图,内部电路图属于机密,一般IC设计公司不会与其他公司共享。封装的SPICE模型和IBIS模型可以被器件模型调用,成为器件模型的一部分。封装的IBIS模型包含版本、文件名等信息,端口的定义,以及信号间电导、电阻、电感和电容的具体值的矩阵。封装常用的模型为HSPICE模型和IBIS模型。HSPICE模型为T模型,如图2-3(a)所示,开头也为节点的定义,然后是后缀为_half和_parlel的两个子电路。电阻R和电感L分布在T模型的两端,所以电阻值和电感值分别为IBIS模型的一半。值得注意的是,HSPICE模型内的电容为SPICE电容矩阵,矩阵的对角线为信号对参考地的自容,矩阵中的其他电容为信号间的互容。IBIS模型如图2-3(b)所示。IBIS 模型的电容为麦克斯韦电容矩阵,麦克斯韦电容矩阵的对角线为对参考地的自容和其他信号互容的总和,也可称为负载电容。

图2-3 封装RLCG模型
2.2.2 功率半导体封装寄生参数
封装寄生参数的获得一般有三种途径:①根据现有的经验公式对寄生参数进行估算,结果不精确,而且不适用于形状不规则导体的寄生参数估算。②通过专业的软件对封装模型进行精确建模,并通过算法来提取封装体内的寄生参数,常见的仿真软件如ANSYS公司的Q3D和Cadence公司的Xtract IM。③通过具体的仪器设备,如阻抗分析仪和时域反射计(TDR)来测量封装内的寄生参数。测量可以验证设计、建模、仿真的准确性,并对仿真结果进行校准。文献[7]给出TDR的测量原理和方法,并结合专业的软件测量IGBT模块的寄生参数。文献[8]采用Q3D软件对一个集成电力电子模块(IPEM)进行建模仿真,结果与阻抗分析仪测量出的寄生参数基本吻合。
在设计之初通过经验公式估算封装体内寄生参数,结合封装尺寸、材料、成本等因素初步制定较为合理的电气设计方案。然后通过专业的仿真软件对功率器件或模块进行三维精确建模,提取封装体寄生参数,模拟器件在大功率下的电流分布,结合设计要求对原设计提出改进方案。最后通过对封装成品进行电气性能测试,在验证设计、建模、仿真过程的准确性的同时验证电学设计是否达到产品性能指标。以上是功率半导体器件电学设计的三个主要步骤。
随着功率半导体器件工艺技术的不断发展,新型SiC或者GaN功率芯片内部的寄生参数已经达到可比拟或者远远小于封装的寄生参数的程度,为了不让封装成为制约芯片工作性能的瓶颈,需要对封装结构进行电性能设计和优化。
目前,功率半导体器件和功率半导体模块普遍采用平面封装结构和引线键合互连工艺。MOSFET是常见的开关器件。导通电阻RDS(on),即漏源极间的电阻是功率MOSFET主要的特征参数之一。常见的功率MOSFET封装结构模型如图2-4所示。MOSFET 封装成品的等效导通电阻等于芯片的导通电阻与封装的寄生电阻之和。RDS(on)由4部分组成:引线框架电阻RL、漏极装片电阻RD、芯片内部电阻Rds(on)、键合线电阻RW,即RDS(on)=RL+RD+RW+Rds(on)。为了降低封装体的寄生电阻,可采用低电阻率引线框架,还可通过采用高电导率的以烧结银为代表的低温连接技术焊料取代普通焊料来降低芯片漏极与框架之间电阻RD,在减小RD的同时获得更高的耐热能力。根据式(2-1)可知,寄生电阻与电阻率和长度成正比,与横截面积成反比。选择电阻率低的键合线,并且尽可能增大键合线横截面积和缩短传输路径,或者采用并联多根键合线的方式来减小寄生电阻,在减小寄生电阻的同时降低了寄生电感。

图2-4 常见的功率MOSFET封装结构模型
在开关模型中,封装体内的寄生电感阻碍着输入电流的转换速度,从而影响开关转换速度。以传统的引线键合互连工艺为例,寄生电感与寄生电阻的模型类似,源端的寄生电感来源于器件封装体内的键合线及源极引脚,漏极电感来源于引线框架和芯片与漏极的装片材料,栅极电感来源于键合线及栅极引脚。寄生电感阻止电流的迅速升高,寄生电感越大,电流上升的速度越慢,晶体管栅极充电速度越慢。当器件关断时,寄生电感也会延缓电流的迅速减小,不利于晶体管快速转换,从而影响开关速度。对于开关速度要求较高的功率半导体器件或功率半导体模块,在设计时应尽量减小封装体的寄生电感,防止在开关瞬间产生较高的电压尖峰。文献[9]和[10]指出MOSFET共源极电感对器件的开关速度、损耗有一定的影响。漏极、源极、栅极电感过大在器件开关过程中会产生振荡,所以需尽量减小布局中的电感。
IGBT结合了MOSFET开关频率高和GTR载流大的优点,相较于MOSFET而言,源、漏极需要承受更大的电流,所以需要打多根键合线。路径短并且靠近源端和终端的键合线承受的电流比其他键合线更大。这样,在工作多个周期后,承受电流越大的键合线发热量就越大,从而导致电流分布不均而引起封装体的热失效。为了增大载流能力而并联多个 IGBT 芯片的功率半导体模组中也会遇到类似的问题,靠近正极的芯片承载的功率相比于远端芯片更高,从而影响整个模组的工作状态。并且更快的开关速度使得栅极寄生电感在模块上的布局变得更加敏感,电感值的不一致将导致各个器件的开关速度差异。在多个功率芯片并联布局时采用对称结构,即每个器件源端(或漏端)到正极(或负极)的路径长度尽量相等,减小寄生参数对功率半导体器件或模块的电流分布、热效应及开关差异具有积极的影响。所以,在多条键合线或者芯片并联设计时尽量保持并联回路的一致性。文献[11]对并联IGBT模组布局做对称处理,相比原布局电流分布及功耗均得到有效改善。由此可见,未来电热混合仿真分析将得到越来越多的应用。
当功率器件闭合与断开时,驱动电路对栅极输入电容进行充放电,寄生电容的充放电延缓了器件的开关。寄生电容的单位一般为pF,虽然其数值在三个寄生参数中最小,但寄生电容是引起EMI的重要参数,尤其是输出端和栅极寄生电容。文献[12]对IPEM做了布局优化,均衡直流总线的寄生电感和电容,同时使输出端寄生电容及栅极寄生电容尽量减小。与原功率半导体模块电气设计相比较,改进后的功率半导体模块的EMI问题得到很大的改善。
为了消除引线键合带来的寄生参数大、载流量有限、由热应力等产生的器件失效等问题,提出了铜片键合技术、倒装芯片技术以及压接封装技术三种新型互连技术。铜片键合相比于传统引线键合接触面积大,从而使寄生参数减小,利于封装产品散热,不同的产品造就了铜片设计的多样化[13]。倒装芯片技术在整个芯片平面上实现多引脚,相比于传统键合互连工艺,互连线路长度短,载流量大,寄生参数小,由于尺寸小,可实现更高的集成度。前两种技术仍属于焊接型技术,而压接封装技术利用压力实现电气连接,器件内部较为对称,使得寄生电感分布更均匀,适合多芯片并联的模组封装,保证了双面散热且可靠性高,但成本较高。中车株洲时代电气在2017年年底完成世界上功率等级最高的压接型 IGBT 的研发,实现了国内压接型 IGBT 技术“从无到有”的突破,打破了国外大功率压接型 IGBT 的技术和市场垄断。文献[14]分析压接型 IGBT 模块的封装寄生参数对芯片工作过程中的均流特性的影响。三种互连技术相比于传统引线键合互连技术均对寄生电感和电阻有较大改善。表2-1给出三种新型互连技术的比较,新型互连技术的出现为电力电子模块化提供了强有力的技术支持。
表2-1 三种新型互连技术的比较

封装器件的电气性能、热性能、可靠性之间是相互关联、不可分割的。提高器件布局密度有助于提高功率密度,减小互连线路长度,从而缓解寄生参数带来的EMI和开关噪声等一系列问题。布局过度集中会使模块热量集中,从而导致模块难以散热,引起可靠性问题。温度过高又会引起材料参数的变化,导致功率半导体器件和模块的电气性能下降。所以在考虑功率半导体器件电气设计时要兼顾封装的热性能和可靠性。由于功率半导体器件大多工作在大电流或者大电压的环境下,在考虑封装电气连接的同时,为保证产品绝缘性能,在选用材料时尽量选用介电常数低,在不同温度和湿度下介电常数较为稳定的介质。
2.2.3 功率器件封装电学建模及仿真
目前,Cadence公司的Xtract IM软件和ANSYS公司的Q3D Extractor软件均可提取封装寄生参数并导出封装IBIS模型或SPICE模型。仿真案例采用ANSYS公司的Q3D软件来提取封装的寄生参数。Q3D是一款三维准静态电磁仿真工具,可以提取任意封装形式的导体结构电阻、电感、电容和电导参数矩阵,并导出SPICE、IBIS 模型。准静态即不考虑电场和磁场的相互耦合,采用三维边界元求解技术提取电容、电导和交流电阻、电感,采用有限元法提取直流电阻、电感。如果功率半导体器件产品尺寸较大,建议采用全波三维仿真器(如 HFSS)来仿真。Q3D软件采用自动自适应剖分技术,网格形状为三角形。表2-2列出了Q3D中电阻、电感、电容、电导参数求解方法及网格策略。
表2-2 Q3D软件参数求解方法及网格策略

封装体由芯片、黏结层、铜框架、引脚及塑封体组成,芯片通过黏结层与铜框架相连,芯片通过键合线与引脚连接。根据实物的实际尺寸建立3D封装模型,如图2-5所示。模型可以在专业的三维模型软件如ANSYS公司的Workbench平台或者SolidWorks、UG等中建立,也可在Q3D中直接建立。然后在Q3D中设置导体的电阻率/电导率,设置介质在不同频率下的介电常数与耗散系数,以及在需要仿真的网络指定源端和漏端,芯片一般设置为源端,封装输出端一般设置为漏端。在Q3D中网格是自动划分的,最后设置好仿真频点,即可进行仿真,待Q3D计算完成后输出仿真结果。

图2-5 封装实物与模型
仿真案例采用常见的 TO-252封装形式,框架引脚长度约为5mm,厚度为0.51mm,宽度为0.76mm,框架的电阻率为1.9μΩ·cm。栅极和源端键合线分别采用5mil(1mil=0.0254mm)和10mil线径,长度分别为2.6mm和2.8mm,电阻率为2.8μΩ·cm。塑封料的相对介电常数为3.8。仿真结果在频率为1MHz下提取。电阻、电感、电容的估算值是在直流情况下计算得到的,估算值和仿真值对比如表2-3所示。由于趋肤效应的影响,电阻仿真值比估算值略大,电感仿真值与估算值相比较大。若装片焊料层出现空洞或分层,漏极寄生电阻将会增大。由于键合线有一定的弧度,所以源端与栅极的电容只能通过仿真计算得到。由于趋肤效应的影响,交流情况下的电阻、电感需要借助专业的软件提取。
表2-3 寄生参数估算值与仿真值对比

仿真的目的不仅是提取封装的寄生参数,还要通过仿真结果进一步优化设计和布局,从而减小寄生参数对性能的影响。随着电力电子模块布局的集中化以及开关频率的高频化,势必会采用越来越先进的封装互连技术,封装形式的定制化在未来将占很大比重。电力电子模块的电学设计将会受到越来越多的重视,研究集成电力电子模块封装技术具有重要意义。