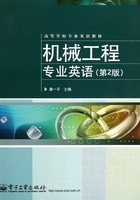
3.6 Inspection of Casting
Several methods can be used to inspect castings to determine their quality and the presence of any defects. Castings can be inspected visually or optically for surface defects. Subsurface and internal defects are investigated using various nondestructive techniques. In destructive testing, test specimens are removed from various sections of a casting to test for strength, ductility, and other mechanical properties, and to determine the presence and location of porosity and any other defects.[4]
Pressure tightness of cast components (valves, pumps, and pipes) is usually determined by sealing the openings in the casting and pressurizing it with water, oil, or air. (Because air is compressible, its use is dangerous in such tests because of the possibility of a sudden explosion due to a major flaw in the casting.) For extreme leak tightness requirements, pressurized helium or specially scented gases with detectors (sniffers) are used. The casting is then inspected for leaks while the pressure is maintained. Unacceptable or defective castings are re-melted for reprocessing.
Because of the major economic impact, the types of defects present in castings and their causes must be investigated. Control of all stages during casting, from mold preparation to the removal of castings from molds or dies, is important in maintaining good quality.