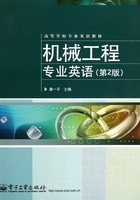
3.5 Centrifugal Casting
As its name implies, the centrifugal-casting process utilizes the inertial forces caused by rotation to distribute the molten metal into the mold cavities. This method was first suggested in the early 1800s. Hollow cylindrical parts, such as pipes, gun barrels, and street lamp posts, are produced by the technique shown in Fig.3.4, in which molten metal is poured into a rotating mold. The axis of rotation is usually horizontal. Molds are made of steel, iron, or graphite, and may be coated with a refractory lining to increase mold life.

Fig.3.4 Schematic illustration of the centrifugal casting process
The mold surfaces can be shaped so that pipes with various outer shapes, including square or polygonal, can be cast. The inner surface of the casting remains cylindrical because the molten metal is uniformly distributed by centrifugal forces. However, because of density differences, lighter elements such as dross, impurities, and pieces of the refractory lining tend to collect on the inner surface of the casting. Cylindrical parts ranging from 13 mm (0.5 in.) to 3 m (10 ft) in diameter and 16 m (50 ft) long can be cast centrifugally, with wall thicknesses ranging from 6 mm to 125 mm (0.25 in. to 5 in.). The pressure generated by the centrifugal force is high, and such high pressure is necessary for casting thick-walled parts. Castings of good quality, dimensional accuracy, and external surface detail are obtained by this process. In addition to pipes, typical parts made are bushings, engine cylinder liners, and bearing rings with or without flanges.