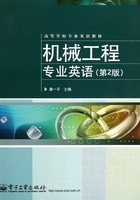
3.4 Expandable-pattern Casting
The expandable-pattern casting process uses a polystyrene pattern, which evaporates upon contact with molten metal to form a cavity for the casting. The process is also known as evaporative-pattern or lost-pattern casting, and under the trade name Full-Mold process.[3] It was formerly known as the “expanded polystyrene process, ” and has become one of the more important casting processes for ferrous and nonferrous metals, particularly for the automotive industry.
In this process, raw expendable polystyrene (EPS) beads, containing 5% to 8% pentane (a volatile hydrocarbon), are placed in a preheated die which is usually made of aluminum. The polystyrene expands and takes the shape of the die cavity; additional heat is applied to fuse and bond the beads together. The die is then cooled and opened, and the polystyrene pattern is removed. Complex patterns may also be made by bonding various individual pattern sections using hot-melt adhesive.
The pattern is coated with a water-based refractory slurry, dried, and placed in a flask. The flask is then filled with loose fine sand, which surrounds and supports the pattern (Fig.3.3) and may be dried or mixed with bonding agents to give it additional strength. The sand is compacted around the pattern by various means. Then, without removing the polystyrene pattern, the molten metal is poured into the mold, immediately vaporizes the pattern (an ablation process) and fills the mold cavity, completely replacing the space previously occupied by the polystyrene pattern. The heat degrades (depolymerizes) the polystyrene and the degradation products are vented into the surrounding sand.

Fig.3.3 Schematic illustration of the expendable-pattern casting process