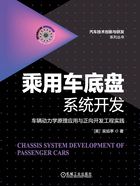
2.2.1 承载式车身结构和副车架
车身可分为承载式和非承载式两类。非承载式车身都有单独的车架,车架是连接前后轴的桥梁式结构,类似梯形。底盘和动力总成直接安装在车架上,主要承担来自地面的载荷。车身通过多个弹性件安装在车架上,弹性件可以吸收振动和噪声,提高了车身寿命和行驶平顺性。车架是整车的核心,便于各总成部件以及车身的安装。另外,撞车时,车架可以对车身提供保护作用(图2.6)。但由于这种结构在车身和底盘之间装有车架,从而会增加整车高度,而且为了保证有足够的强度和刚度,车架变成车上最重的部件,增加了整车重量,需要大型制造设备,成本也比较高。因此,非承载式车身结构主要应用于大中型货车、大客车、高级轿车和越野型SUV。近年来,随着电动车的兴起,将电池模组直接集成到底盘结构的CTC架构(Cell to Chassis)因其提供的诸多优势重新引起关注。实际上可以看成非承载式车身的进一步发展。
承载式车身结构试图取消车架,将车架的承载功能融入车身结构中,直接将发动机和底盘与车身连接,但这势必将发动机和路面的振动、噪声直接传递到车身(图2.7)。为此,在下车体与底盘之间引入了前后独立的副车架。为了增加强度并降低重量,副车架通常做成封闭断面结构。副车架可在承载最集中的前后轴部位分担一部分载荷,使车身纵梁变形减小,因此,带有副车架的车身结构又称为“半承载式车身”。车身中间部位仍然直接承受各种外力引起的弯曲和扭转变形。副车架和车身纵梁之间可以通过橡胶衬套连接或者螺栓硬连接。采用橡胶衬套连接可以降低发动机和路面的振动对车身的影响,但衬套的变形会降低承载式结构的整体刚度,影响操纵性能。硬连接可以有效增加整体刚度,有助于改善操纵响应,当然平顺性和NVH性能会受到负面影响。副车架可以将动力总成、悬架、转向系形成一个组装部件,这种模块化结构给生产带来方便。承载式车身是空间框架结构,充分利用了车身结构承担载荷,因此其整体刚度大、重量轻、整车高度低、生产效率高,是乘用车上最常用的结构。承载式与非承载式结构相比,减轻了重量,易于充分利用车内空间,成本低。当然,发生事故导致车身损坏时,承载式结构的修复更为困难。

图2.6 非承载式车身和车架

图2.7 承载式车身
乘用车车身结构相当复杂,图2.8试图简要描述与发动机和底盘承载直接相关的车身骨架部分。车身骨架主要由纵梁、横梁和立柱焊接成一个空间框架结构,起主要承载作用,因此必须满足一定的强度和刚度要求。车身覆盖件是覆盖在车身骨架上,体现汽车外形的板型件,对车身的强度和刚度有一定贡献。
车身结构件或车身骨架是车身的核心结构,其中车身纵梁一般是车身最主要的骨架部件。带有副车架结构的汽车,因副车架需承受悬架杆件传递来的所有轮胎侧向力、纵向力、部分垂向力和回正力矩、侧翻力矩等,所以必须安装在前纵梁较为坚固的部位(图2.9)。

图2.8 乘用车承载式车身结构与车身骨架的关系

图2.9 车身纵梁和副车架
悬架的阻尼力、弹簧力和缓冲限位块力通常直接作用到车身上,最大弹簧和减振器动态力一般在千牛级,而限位块最大的动态力通常在万牛级。图2.10为承受减振器力的车身塔座部位结构图。有些动力总成悬置的抗扭衬套也直接连接到下车体上,因此,车身必须有足够的局部强度和刚度。车身上通常采用加强梁以提高车身的局部强度和刚度,加强梁是下车体的一部分,不可拆卸。

图2.10 车身塔座部位结构
车身的强度决定了发生碰撞时是否容易损坏,而车身的刚度一般与驾驶操作时车身受力后的弹性变形有关。理论上,刚性车身结构可以达到最佳的操纵稳定性和行驶平顺性。可以想见,用一整块金属挖出所需的乘坐空间得到的车身结构应该是最理想的情况。车身刚度高的车辆,在转向操作时其优势可以充分发挥出来。车身刚度太低,容易产生各种噪声和振动问题,甚至会影响底盘调校的有效性。除了运用有限元分析技术在设计阶段降低车身重量的同时优化刚度之外,还可以通过在悬架的关键安装部位增加支承杆的方式加强局部刚度。