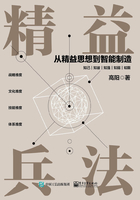
1.5 必然的选择
随着我国开放程度的进一步扩大,制造业逐渐面临更为严峻的国际化竞争和更为充分的市场化挑战,这些都对制造业产业提出了更高的要求。
1950年,当丰田英二走进美国底特律福特公司的汽车工厂后,他被眼前的景象震惊了:一条条巨大的汽车装配流水线,一堆堆充足的装配用零件摆在流水线旁,工人如机器一般有条不紊地进行着装配活动,不需要大量移动,不需要零件配合的打磨。当时这个厂每天的产量是7000辆轿车,比日本丰田公司一年的产量还多。但他并没有盲目复制美国模式,他在自己的本子上慎重地写下“这里还有改进的可能”。
“二战”后的日本,资金缺乏,技术缺乏,人才同样缺乏。但就是在这样一种逆境中,丰田走出了自己的道路:利用丰田生产制造方式,秉持着绝不浪费的精神,将有限的资源加以充分利用。通过这种生产管理方式的熏陶,丰田培养了大批具有改善精神和专业素质的人才队伍,创造了后来属于丰田公司的传奇。相较美国的大批量生产模式,精益生产有以下几个特点:
(1)对待上下游企业的态度不同。大批量生产方式源于美国,基于美国的企业间关系,强调市场导向,每个企业以财务关系为界限,优化自身的内部管理。而关联企业,无论是供应商还是经销商,则以对手相对待。
精益生产方式以整个大生产系统为优化目标,一方面,降低协作供应链企业的交易成本;另一方面,保证稳定需求与及时供应。丰田精益思想视供应链中所有企业的浪费为整个系统的浪费,强调如果浪费不是被消除而是被转移到供应商端,并不是真正消灭了浪费,“浪费”本身还会以不同的形式(如质量缺陷、交期延后、成本提升等)反馈到企业自身。这种强调协作和共赢的理念,对于现阶段内耗严重的我国制造业产业来说具有很大的启发。
(2)对待库存的态度不同。大批量生产方式的库存管理强调“库存是必要的恶物”。在批量生产中,材料的“富余”是保证连续生产的基础,虽然认识到库存属于资金的占用,但生产方式决定了其对库存的依赖。
精益生产方式的库存管理强调“库存是万恶之源”。精益生产方式将生产中的一切库存视为“浪费”,同时认为库存掩盖了生产系统中的缺陷与问题。所以,通过不断降低库存以消灭库存本身产生的“浪费”,且不断暴露生产中各个环节的矛盾并加以改进。基于此,精益生产提出了“消灭一切浪费”的口号,追求零浪费的目标。这种追求零库存的管理方式如果能够施行,将会大大提升企业的流动资金总量,保证企业在技术革新、扩大市场占有率上获得先机。
(3)对待人的态度不同。传统的大批量生产方式的用人制度基于双方的“雇佣”关系,在业务管理中强调个人工作高效的分工,强调严格的层次关系。对员工的要求在于严格完成上级下达的任务,人被看作附属于岗位的“设备”,越是无条件服从越好。
精益生产源于日本,深受东方文化的影响,在专业分工的同时强调相互协作,尽量发挥人的能动性。这种方法将员工视为企业团体的成员而非机器,强调管理流程精简,充分发挥基层员工的主观能动性。
例如,在传统大批量生产方式中,一旦工人导致了生产线停止,就毫无例外地要被责罚,因为工人没有被授予可以停止生产线的权力,所以,大家都害怕停止生产线的运转。但是在丰田,公司希望尽可能地将问题暴露出来,再加以解决。例如,安灯系统(ANDON)就鼓励大家在发现生产线上的质量问题或设备问题后立即停止产线并拉动安灯报警,将问题及时暴露出来。丰田汽车的创始人丰田喜一郎曾说过一句话:“人员是我社最大的财产。”
随着精益改善项目的推行,企业内部相关人员可借此机会与企业一同成长,真正由“人材”变成“人才”,乃至变成企业的“人财”。精益生产这种强调人才培养、将企业发展与人员能力提升深度绑定的模式,对于传统制造业中外部人才引进有困难的行业来说无疑是对症良药。相比1950年的丰田,我国制造业的环境还没有那么恶劣,但居安思危是每个企业家必备的素质。随着市场竞争的逐渐激烈,面对人力成本的逐年提升等种种问题,制造业企业如何快速应对变化,如何在未来多变的市场环境下培养富有战斗力的人才群体,正变得迫在眉睫。
丰田的成功,给我们指明了一条道路。中国制造业企业需要通过精益生产变革,利用精益生产的指导思想,运用其包含的技术手段和工具,加速企业的敏捷创新,提升利润率,提升人才培养效率,使我们能够与外国同行充分竞争。因此,精益生产逐渐成为我们必然的选择。