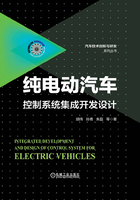
3.1.4 高压配电电气架构
1.整车布置方式
高压电气系统中的高压电气件,根据整车的驱动方式,其布置方案一般包含以下九种,下面引用某款车型的布置方案对其优缺点进行简单阐述。
(1)后驱方案
1)方案一(图3-18)。

图3-18 整车布置方案一
①电动压缩机(EAC)、电加热器(PTC)、直流变换器(DC/DC)及车载充电器(OBC)、高压分配单元(PDU)布置在前舱。
②交流插座(AC)、直流插座(DC)布置在前翼子板。
③动力蓄电池系统(Pack)布置在下车体。
④电机控制器(MCU)布置在后驱动桥。
优点:动力蓄电池系统(Pack)前后两端出线,省去由高压分配单元(PDU)到电机控制器(MCU)的高压线束,且合理规避了对下车体布置高压线束空间的要求。
缺点:直流插座(DC)布置在前翼子板,无形地增加了对L5线束线径的要求,因为直流充电电流远大于其他高压负载工作电流。
2)方案二(图3-19)。

图3-19 整车布置方案二
①电动压缩机(EAC)、电加热器(PTC)、直流变换器(DC/DC)及车载充电器(OBC)、高压分配单元(PDU)布置在前舱。
②交流插座(AC)布置在前翼子板。
③直流插座(DC)布置在后侧围。
④动力蓄电池系统(Pack)布置在下车体。
⑤电机控制器(MCU)布置在后驱动桥。
优点:动力蓄电池系统(Pack)前后两端出线,省去由高压分配单元(PDU)到电机控制器(MCU)的高压线束,且合理规避了对下车体布置高压线束空间的要求。直流插座(DC)布置在后侧围,降低了对L5线束线径的要求,从而节省了成本。
缺点:直流插座(DC)布置在后侧围,布置直流快充高压线束时容易与电机控制器高压线束干涉,整体空间比较紧凑,不易装配。
3)方案三(图3-20)。
①电动压缩机(EAC)、电加热器(PTC)、直流变换器(DC/DC)及车载充电器(OBC)、高压分配单元(PDU)布置在前舱。
②交流插座(AC)、直流插座(DC)布置在后侧围。
③动力蓄电池系统(Pack)布置在下车体。
④电机控制器(MCU)布置在后驱动桥。
优点:动力蓄电池系统(Pack)前后两端出线,省去由高压分配单元(PDU)到电机控制器(MCU)的高压线束,且合理规避了对下车体布置高压线束空间的要求。

图3-20 整车布置方案三
缺点:交流插座(AC)、直流插座(DC)布置在后侧围,且是由前舱高压分配单元(PDU)引出,增加了对下车体两侧空间的要求,从而使动力蓄电池系统的尺寸减小,同时还会压缩整车制动管路和冷却管道的空间。另外,与方案二相比,方案三的高压线束更长,导致成本增加。
4)方案四(图3-21)。

图3-21 整车布置方案四
①电动压缩机(EAC)、电加热器(PTC)、直流变换器(DC/DC)及车载充电器(OBC)、高压分配单元(PDU)布置在前舱。
②交流插座(AC)、直流插座(DC)布置在后侧围。
③动力蓄电池系统(Pack)布置在下车体。
④电机控制器(MCU)布置在后驱动桥。
优点:动力蓄电池系统(Pack)前后两端出线,省去由高压分配单元(PDU)到电机控制器(MCU)的高压线束,且合理规避了对下车体布置高压线束空间的要求。
缺点:与方案二、方案三有相同的缺点。
(2)前驱方案
1)方案五(图3-22)。
①电动压缩机(EAC)、电加热器(PTC)、直流变换器(DC/DC)及车载充电器(OBC)、高压分配单元(PDU)、电机控制器(MCU)布置在前舱。
②交流插座(AC)、直流插座(DC)布置在前翼子板。
③动力蓄电池系统(Pack)布置在下车体。
优点:整体结构紧凑。
缺点:无明显缺点。

图3-22 整车布置方案五
2)方案六(图3-23)。
①电动压缩机(EAC)、电加热器(PTC)、直流变换器(DC/DC)及车载充电器(OBC)、高压分配单元(PDU)、电机控制器(MCU)布置在前舱。
②交流插座(AC)布置在前翼子板。
③直流插座(DC)布置在后侧围。
④动力蓄电池系统(Pack)布置在下车体。
优点:无明显优点。
缺点:与方案五相比,增加了L6高压线束,导致增加了成本。

图3-23 整车布置方案六
3)方案七(图3-24)。

图3-24 整车布置方案七
①电动压缩机(EAC)、电加热器(PTC)、直流变换器(DC/DC)及车载充电器(OBC)、高压分配单元(PDU)、电机控制器(MCU)布置在前机舱。
②交流插座(AC)、直流插座(DC)布置在后侧围。
③动力蓄电池系统(Pack)布置在下车体。
优点:无明显优点。
缺点:与方案三有相同的缺点。
4)方案八(图3-25)。

图3-25 整车布置方案八
①电动压缩机(EAC)、电加热器(PTC)、直流变换器(DC/DC)及车载充电器(OBC)、高压分配单元(PDU)、电机控制器(MCU)布置在前舱。
②交流插座(AC)、直流插座(DC)布置在后侧围。
③动力蓄电池系统(Pack)布置在下车体。
优点:无明显优点。
缺点:与方案四有相同的缺点。
5)方案九(图3-26),这是特斯拉Model3的一个后驱车型的布置方案。
①电动压缩机(EAC)、电加热器(PTC)布置在前舱。
②交流插座(AC)、直流插座(DC)布置在后侧围。
③动力蓄电池系统(Pack)、直流变换器(DC/DC)及车载充电器(OBC)、高压分配单元(PDU)布置在下车体。
④电机控制器(MCU)布置在后驱动桥。
优点:将直流变换器(DC/DC)及车载充电器(OBC)、高压分配单元(PDU)高度集成在了动力蓄电池系统(Pack)内部。
缺点:正是因为高度集成化,所以如果其中一个器件损坏,那么需要将整个电池包拆卸更换,售后维修费用高。

图3-26 整车布置方案九
评判一个方案的好坏,最终无非体现在价格和质量上,各方案相关数据见表3-3。
表3-3 各方案相关数据

注:1.2.5mm2:11.5元/m,0.07kg/m。
2.6mm2:18.7元/m,0.15kg/m。
3.35mm2:34元/m,0.5kg/m。
图3-27和图3-28所示分别为价格对比和质量对比。
综述:
1)如果采用后驱方案,那么采用方案二最为合适。
2)如果采用前驱方案,那么采用方案五最为合适。
3)不管采取何种方案,最后都需要和整车造型相匹配。

图3-27 价格对比

图3-28 质量对比
2.几种典型高压电气原理图
每个车企都有各自的高压电气架构,这里只列出典型的几种高压电气原理图。
(1)高压电气原理图一(图3-29)在电动汽车发展初期,此种高压电气架构基本应用于所有车企,用于每一路负载的过电流保护。

图3-29 整车高压电气原理图一
(2)高压电气原理图二(图3-30)随着电动汽车的发展,每个车企开始对整车成本有了要求,随之就过渡到了第二种架构,将电机控制器(MCU)和直流快充的熔断器取消以降低成本。

图3-30 整车高压电气原理图二
(3)高压电气原理图三(图3-31)近年来,高能量密度电池和整车能耗低的补贴越来越大,随之就过渡到了第三种架构,将直流变换器(DC/DC)及车载充电器(OBC)进行“板集成”以降低成本和减小质量,同时也降低了对整车布置空间的要求。

图3-31 整车高压电气原理图三
(4)高压电气原理图四(图3-32)此种电气架构与前几种电气架构有很大的不同,由电池包前后两端引出线,一个接PDU、一个接MCU,主要应用于后驱车型。后驱车型采取电池包一端出线方案,会产生高压线束布置上的问题,从而引起整车其他零部件布置的问题。

图3-32 整车高压电气原理图四