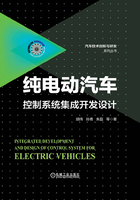
3.1.2 高压电气系统设计通用要求
1.警示标识
根据GB 18384—2020《电动汽车安全要求》的要求,B级电压的电能存储系统或产生装置,应标记图3-1所示符号。当移开遮拦或外壳可以漏出B级电压带电部分时,遮拦或外壳上也应有同样的符号且清晰可见。此标识的底色为黄色,边框和箭头为黑色如图3-1所示。
同时为了能提示用户和维修人员,要求B级电压电路中的电缆和线束的外皮应使用橙色加以区别,如图3-2所示。

图3-1 高压警告标记

图3-2 高压线束(见彩插)
2.绝缘
在最大工作电压下,直流电路绝缘电阻的最小值为100Ω/V,交流电路的绝缘电阻至少应为500Ω/V。
整个高压电路,其实是由直流电路和交流电路连接在一起的(如电机控制器和电机),这种组合电路的绝缘电阻至少为500Ω/V。为了保证整车的绝缘阻值能够满足此要求,每个高压部件应该有更高的绝缘电阻,典型的有动力蓄电池的绝缘电阻至少为10MΩ,电机控制器的绝缘电阻至少为20MΩ,高压线束的绝缘电阻至少为100MΩ。
整车绝缘是由交给电池管理系统(BMS)检测的,BMS会根据整车绝缘电阻的大小进行整车高压控制。绝缘故障保护是以保证人的安全为前提而设置的。在绝缘故障处理上,不能检测到有绝缘故障就下高压,这种“一刀切”的处理方式不但会引起用户的抱怨,甚者会加深对人的伤害。如在高速行驶下,由于绝缘问题突然下高压,容易发生追尾事故。
各整车厂针对绝缘故障有不同的处理方式,但方法基本相同,一般控制方式是:
1)在高压上电前,会禁止高压上电。
2)如果已经高压上电但未行驶,会立即下高压。
3)如果已经高压上电且已行驶,整车会进行降功率处理,并通过声/光报警方式告知驾驶人,严重时会在极短的时间内断开高压。
3.耐压
采用基本绝缘装置的高压部件,施加(2U+1000)V(U为组件锁连接电路的最大工作电压,通常指的是动力蓄电池系统的最高电压,单位为V)的交流电压进行测试,漏电流小于0.1mA/min,且测试结束后不能发生介质击穿或电弧现象。
用直流电试验时,此电压是交流电压的1.41倍。
4.防护等级
大部分车辆都在露天环境下使用,粉尘、雨水环境甚至泡水情况非常多,很容易使电动汽车发生严重的安全事故,影响人身财产安全。所以,高压部件都需要考虑防水防尘设计,并且需要达到非常高的防护等级。
一般要求所有高压部件至少应达到IP67标准,只有达到这样的标准才可能满足整车的防水要求,防护等级表见表3-1。
确定了防护等级为IP67后,可以从以下几个方面入手:弹性元设计、限位设计、子零件选型。
(1)弹性元设计 比较成熟的IP67密封设计可以归纳为两种:压力密封和粘接密封。
表3-1 防护等级表

压力密封是通过上下安装界面的作用力压缩弹性元,利用弹性元的反弹力使得上下安装界面充分接触,以达到防尘防水要求。常见的弹性元主要有发泡类或注塑类的硅胶和橡胶,具体选用何种材料还与要求的压缩率有关,压缩率的计算公式为
μ=[h1-h2)/h1]×100%
式中,h1为弹性元自由状态下的原始高度(mm);h2为弹性元压缩后的高度(mm);μ为压缩率。
h2与上下盖固定螺栓的大小有关,不同大小的螺栓有不同的力矩。
粘接密封是通过粘接力代替压缩的反弹力,使得上下安装界面充分接触,以达到防尘防水要求。当然也需要一定的压缩,使得粘接力达到更优状态。使用粘接密封需要一定的工艺水准,对设备的要求会高一些。粘接密封通常会配合压力密封,使产品达到更高的防尘防水要求。
图3-3所示为密封压条,图3-4所示为密封胶。

图3-3 密封压条

图3-4 密封胶
防护方面,在满足成本要求的情况下应尽量提高要求,部分车企已经达到了IP68甚至更高的标准。
(2)限位设计 由于弹性元的存在,在通过紧固件螺栓锁紧上下盖时,如果没有刚性支撑,弹性元的压缩率很难控制且有可能会将弹性元压挤出来(如果采用粘接密封方式),使得密封失效,所以限位设计必不可少。图3-5所示为限位设计示例。

图3-5 限位设计示例
(3)子零件选型 在壳体上看到的零部件,都会涉及IP67密封设计,这些零部件基本是高低压插接器、手动维修开关(MSD)和防爆阀等。在选取以上零部件时,本身就必须要求达到IP67级别。
高压插接器基本上都是选取“快插”型(图3-6)的,但也有选用“IPT”插接器(图3-7)的。在A级车及以上基本采用“快插”型插接器,其优点是在整车装配时,工艺简单且省工时,缺点是成本偏高。A0级及以下车型需要考虑成本,往往采用“IPT”插接器。其优点是技术含量较低且成本也低,只需要具有模具即可,其缺点是整车装配工艺复杂且耗时,同时在安装高压线束时需要打开上盖,这可能导致已经达到IP67等级的性能失效。

图3-6“快插”型插接器

图3-7 “IPT”插接器
手动维修开关(图3-8)在早期的电动汽车上基本上是安装在高压配电盒或电池包上的,其目的是在维修时断开此开关,保证车辆处于无高压电状态。但是近年来在车辆上已经取消了此装置,原因有两个方面,一是成本过高,二是需要占用空间。
防爆阀(图3-9),其实是从动力蓄电池系统延伸出来的一个装置。因为动力蓄电池系统是一个高能量的储能系统,在某些特定的条件下(电池包内部短路),可能存在能量在短时间内集中爆发的情况。如果没有防爆阀,那么集中的能量就会在壳体最薄弱的位置释放,所以防爆阀应运而生。防爆阀的工作原理是相同的,都是当内部能量集中爆发时,能够快速将其能量释放出去。

图3-8 手动维修开关

图3-9 防爆阀
5.电位均衡
电位均衡又称为等电位连接,是为了减小电位差而采用的接地方法,与整车的连接阻抗值越小越好,一般要求≤0.1Ω。对于等电位连接用的导体,要求颜色是黑色,方便维修时辨认。
6.预充保护
高压电气系统中,带容性负载的高压器件很多,如电机控制器、电动压缩机、直流变换器(DC/DC)等。其中电机控制器的母线电容最大,一般在500~1000μF左右,直接接通高压回路会产生高压电冲击,为了避免高压上电时瞬间产生大电流烧坏继电器,需要设计预充回路对容性负载进行预充电。
如图3-10所示,把高压电气系统简化成一个由电阻和电容组成的模型。上高压前,首先闭合预充继电器Kp,再闭合主负继电器K-,此时与电阻R构成预充电回路。当容性负载端电压Uc=(0.9~0.95)Ub时,接通主正继电器K+,再切断预充继电器Kp,整个预充电过程结束。图3-11所示为预充电压及电流变化。

图3-10 预充模型

图3-11 预充电压及电流变化
7.高压互锁保护
整车高压部件需要高压线束与高压分配单元(CDU)进行连接。当所有高压插接器对插以后,高压分配单元(CDU)内部通过低压线进行串联,然后引出到整车控制器(VCU)或电池管理系统(BMS)。
高压互锁的检测方式一般分为两种,分别是直流源方案、脉宽调制(PWM)方案。
直流源方案就是检测单元在硬件的某一接口发出高电平/低电平,同时在另一接口实时检测电位情况,从而来判断高压互锁是否断开。
PWM方案就是检测单元在硬件的某一接口发出PWM波,同时在另一接口实时检测PWM的占空比进行比较,从而来判断高压互锁是否断开。
高压互锁的检测回路数一般分为三种,即一路、两路、三路,应根据具体的电气架构定义。
一路是将所有负载的高压插接器进行串联,只要检测到高压互锁故障,就只有一种处理方式,这种处理方式简单但不便于用户使用。如实际只是电动压缩机的高压插接件断开,但是整车却不能“ready”。
两路是一路将负责动力输出的高压插接器进行串联,另一路是其余的高压插接器串联。这种处理方式便于用户使用,但会有高压风险。如雨天行驶过程中,检测到另外一路存在高压互锁故障,虽然关闭了这一路的所有高压负载输出,但仍会出现绝缘故障。
三路是一路将负责动力输出的高压插接器进行串联,另一路是电动压缩机(EAC)、电加热器(PTC)高压插接器串联,最后一路是车载充电器、快充高压插接器串联。这种处理方式也会便于用户使用,但也会有高压风险,与两路方式相似。
以上三种方式在各种车型上均有应用,但推荐采用一路检测方式。原因是,如果不是人为或车辆撞到某一装置时,这种高压互锁故障发生的概率是极低的。不应仅认为会出现这样的故障,就做太多种不切实际的保护,否则反而可能会增加故障发生率。
检测出有高压互锁故障后,一定要对整车进行故障保护处理,各整车厂针对高压互锁故障,有不同的处理方式,但基本相似,一般控制方式如下:
1)在高压上电前,会禁止高压上电。
2)如果已经高压上电但未行驶,会立即下高压。
3)如果已经高压上电且已行驶,整车会进行降功率处理,并通过声/光报警方式告知驾驶人,直至功率降至0为止。
8.过载/短路保护
整车一般有28种工况,高压电气系统中的所有高压零部件必须满足其中部分典型及极端工况的负载要求,并且能满足一定的过流能力,不允许在规定的行驶工况中过热导致高压部件出现绝缘层融化、烧蚀或者冒烟情况。同时应合理控制过流时间,防止过载时间长而过热导致起火事件。
当高压电气系统发生瞬时大电流或短路时,可以设置熔断器(图3-12),它能自动切断高压回路,确保高压部件不被损坏,避免发生热失控,从而保证驾乘人员的安全。

图3-12 熔断器
9.余能释放保护
由于整车存在大量电容负载的原因,断开高压回路后,整车并不能在第一时间内将电压下降到0,仍有较高的电压和残余电能存储在电容上。
为了避免可能带来的伤害,电机控制器(MCU)被动放电时间应不超过5min、主动放电时间应不超过3s,将其高压降低到DC 60V以下,实际情况可以做到被动放电时间不超过3min、主动放电时间不超过1s。
具体做法是,在电池管理系统断开主回路后,整车控制器通过硬线或CAN方式命令电机控制器主动放电(Discharge),电机控制器收到命令后,通过电机绕组以最快的方式将余能释放。在此过程中,如果电机控制器损坏或断开低压电,也可以串联电阻方式被动地将余能释放。图3-13所示为余能释放时间分析。

图3-13 余能释放时间分析
10.电磁兼容
电磁兼容性(EMC)是指设备或系统在其电磁环境中能正常工作且不影响其他设备或系统正常工作的能力。包括电磁干扰(EMI)和电磁敏感度(EMS)。
EMI是指设备在正常运行过程中对所在环境产生的电磁干扰,是主动性的。
EMS是指设备对所在环境中存在的电磁干扰所具有的避免性能降低的能力,是被动性的。
具有电磁骚扰源的动力蓄电池系统(Pack)、电机控制器(MCU)、电机(Motor)、电动压缩机(EAC)、电加热器(PTC)、直流变换器(DC/DC)及车载充电器(OBC),可将外壳形成一个良好的密封体实现屏蔽,再通过多点接地方式将外壳与整车可靠接地,降低电磁辐射的强度。
对于整车而言,执行的EMC标准主要有GB/T 18387—2017《电动车辆的电磁场发射强度的限值和测量方法》、GB 34660—2017《道路车辆 电磁兼容性要求和试验方法》。