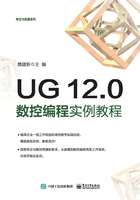
3.数控编程过程
1)进入UG加工环境
(1)在横向菜单中单击“应用模块”选项卡,再单击“加工”命令。
(2)在【加工环境】对话框中选择“cam_general”选项和“mill_contour”选项,单击“确定”按钮,进入UG加工环境。此时,实体上出现两个坐标系:基准坐标系和工件坐标系,这两个坐标系重合在一起。
(3)按键盘上的W键,还会出现1个坐标系(动态坐标系),这个坐标系与上述两个坐标系重合。
(4)单击“菜单|编辑|移动对象”命令,在【移动对象】对话框中,对“运动”选择“距离”选项,对“指定矢量”选择“ZC↑”选项,把“距离”值设为-20mm,对“结果”选择“
移动原先的”单选框。
(5)单击“确定”按钮,实体往下移动20mm。此时,工件坐标系位于实体上表面的中心,基准坐标系位于实体底面,如图4-12所示。
(6)在屏幕左上方的工具条中单击“几何视图”按钮。
(7)在“工序导航器”中展开的下级目录,再双击“
WORKPIECE”选项。
(8)在【工件】对话框中单击“指定部件”按钮,在绘图区选择整个实体,单击“确定”按钮。然后,单击“指定毛坯”按钮
,在【毛坯几何体】对话框中,对“类型”选择“包容块”选项,把“XM-”、“YM-”、“XM+”、“YM+”、“ZM+”值都设为1mm。

图4-11 创建圆锥特征

图4-12 工件坐标系位于实体上表面的中心
2)创建ϕ12mm立铣刀与ϕ6mm立铣刀
(1)单击“创建刀具”按钮,在【创建刀具】对话框中,对“刀具子类型”选择“MILL”图标
,把“名称”设为“D12R0(铣刀-5参数)”。设置完毕,单击“确定”按钮。
(2)在【铣刀-5参数】对话框中,把“直径”值设为12mm、“下半径”值设为0mm。
(3)按照上述方法,创建D6R0立铣刀,把“直径”值设为6mm、“下半径”值设为0mm。
3)创建ϕ12mm立铣刀刀路(粗加工程序)
(1)单击“创建工序”按钮,在【创建工序】对话框中,对“类型”选择“mill_planar”选项。在“工序子类型”列表中单击“带边界面铣”按钮
,对“程序”选择“NC_PROGRAM”选项、“刀具”选择“D12R0(铣刀-5参数)”选项、“几何体”选择“WORKPIECE”选项、“方法”选择“MILL_ROUGH”选项,如图4-13所示。设置完毕,单击“确定”按钮。
(2)在【面铣】对话框中单击“指定面边界”按钮,在【毛坯边界】对话框中,对“选择方法”选择“曲线”选项、“刀具侧”选择“内侧”选项,对“平面”选择“指定”选项,如图4-14所示。

图4-13 设置【创建工序】对话框参数

图4-14 设置【毛坯边界】对话框参数
(3)在工作区上方的工具条中选择“相切曲线”选项,如图4-15所示。

图4-15 选择“相切曲线”选项
(4)在实体上选择方形凹坑口部的内边线作为边界曲线,选择方形凹坑的底面作为指定平面(加工的最低深度),如图4-16所示。
(5)在【面铣】对话框中,对“刀轴”选择“+ZM轴”选项、“切削模式”选择“往复”选项、“步距”选择“刀具平直百分比”选项,把“平面直径百分比”值设为75.0000(%)、“毛坯距离”值设为15.0000(单位:mm)、“每刀切削深度”值设为0.5000(单位:mm)、“最终底面余量”值设为0.1000(单位:mm),如图4-17所示。

图4-16 选择边界曲线和指定平面

图4-17 设置刀轨参数
(6)单击“切削参数”按钮,在弹出的【切削参数】对话框中,单击“策略”选项卡,对“切削方向”选择“顺铣”选项、“剖切角”选择“指定”选项,把“与XC的夹角”值设为0°;勾选“
添加精加工刀路”复选框,把“刀路数”值设为1、“精加工步距”值设为1.0000mm,如图4-18所示。单击“余量”选项卡,把“部件余量”值设为0.2mm、“壁余量”值设为0.2mm、“最终底面余量”值设为0.1mm。单击“拐角”选项卡,对“光顺”选择“所有刀路”选项,把“半径”值设为2.0000mm,如图4-19所示。

图4-18 设置“策略”选项卡参数

图4-19 设置“拐角”选项卡参数
(7)单击“非切削移动”按钮,在弹出的【非切削移动】对话框中单击“进刀”选项卡,在“封闭区域”列表中,对“进刀类型”选择“螺旋”选项,把“直径”值设为10.0000mm、“斜坡角”值设为1.0000(单位:°)、“高度”值设为1.0000mm;对“高度起点”选择“当前层”选项,把“最小安全距离”值设为0.0000mm,如图4-20所示。单击“转移/快速”选项卡,在“区域内”列表中,对“转移方式”选择“进刀/退刀”选项、“转移类型”选择“前一平面”选项,把“安全距离”值设为2.0000mm,如图4-21所示。

图4-20 设置“进刀”参数

图4-21 设置“转移/快速”参数
(8)单击“进给率和速度”按钮,在弹出的【进给率和速度】对话框中,把主轴速度值设为1000r/min、切削速度值设为1200mm/min。
(9)单击“生成”按钮,生成的面铣刀路如图4-22所示,仿真模拟的刀路如图4-23所示。

图4-22 生成的面铣刀路

图4-23 仿真模拟的刀路
如果在图4-18中取消“添加精加工刀路”复选框中的,那么重新生成的刀路——非精加工刀路如图4-24所示,仿真模拟的非精加工刀路四周有凸起,如图4-25所示。

图4-24 非精加工刀路

图4-25 仿真模拟的非精加工刀路
读者可以自行在图4-19中对“光顺”选择“无”选项,此时,拐角处的刀路变成直角。在实际加工时,若选择这种刀路,则容易损伤刀具。
提示:运用“带边界面铣”命令编写加工程序时,应注意以下几点:
● 通过设置毛坯距离的方法设置加工的高度。
● 在【毛坯边界】对话框中,对“边界”列表中的“选择方法”选择“曲线”选项,而不选择“面”选项;对“刀轴”应选“+Z轴”选项。
4)创建清理拐角刀路
(1)在辅助工具条中单击“程序顺序视图”按钮。在“工序导航器”中把“PROGRAM”名称改为A1,并把前面创建的刀路程序移到A1程序组中。
(2)单击“菜单|插入|程序”命令,在【创建程序】对话框中对“类型”选择“mill_contour”选项,对“程序”选择“NC_PROGRAM”选项,把“名称”设为A2。
(3)单击“确定”按钮,创建A2程序组。此时,A1与A2都在NC_PROGRAM下级目录中,如图4-26所示。
(4)单击“创建工序”按钮,在弹出的【创建工序】对话框中对“类型”选择“mill_contour”选项,在“工序子类型”列表中单击“剩余铣”按钮
,对“程序”选择A2选项、“刀具”选择“D6R0(铣刀-5参数)”选项、“几何体”选择“WORKPIECE”选项、“方法”选择“METHOD”选项,如图4-27所示。设置完毕,单击“确定”按钮。
(5)在【剩余铣】对话框中单击“指定切削区域”按钮,选择实体内部的曲面。
(6)在【剩余铣】对话框中设置“刀轨设置”选项卡参数,对“切削模式”选择“轮廓”选项,把“附加刀路”值设为0,对“公共每刀切削深度”选择“恒定”选项,把“最大距离”值设为1.0000mm,如图4-28所示。
(7)单击“切削参数”按钮,在弹出的【切削参数】对话框中,单击“策略”选项卡,对“切削方向”选择“顺铣”选项、“切削顺序”选择“深度优先”选项。单击“余量”选项卡,把“部件侧面余量”值设为0.3mm、“部件底面余量”值设为0.1mm。

图4-26 创建A2程序组

图4-27 设置【创建工序】对话框参数
(8)单击“非切削移动”按钮,在弹出的【非切削移动】对话框中单击“进刀”选项卡。在“封闭区域”列表中,对“进刀类型”选择“与开放区域相同”选项;在“开放区域”列表中,对“进刀类型”选择“圆弧”选项,把“半径”值设为2mm、“圆弧角度”值设为90°、“高度”值设为1mm、“最小安全距离”值设为5mm。单击“转移/快速”选项卡,在“区域内”列表中,对“转移方式”选择“进刀/退刀”选项、“转移类型”选择“直接”选项。
提示:为了能更好地理解这些参数的含义,读者可以夸张地改变这些参数的大小,观察重新生成的刀路有什么变化。
(9)单击“进给率和速度”按钮,在弹出的【进给率和速度】对话框中,把主轴速度值设为1000r/min、切削速度值设为1200mm/min。
(10)单击“生成”按钮,生成的剩余铣刀路如图4-29所示。

图4-28 设置“刀轨设置”选项卡参数

图4-29 生成的剩余铣刀路
(11)在“工序导航器”中双击选项,在【剩余铣】对话框中把“最大距离”值设为0.5mm,生成的刀路如图4-30所示。图4-30中的刀路与图4-29中的刀路相比,在加工四周的斜面时每隔一层,多了一层刀路,也多了加工中间圆台斜面的刀路。这是因为刀路程序
的“每刀切削深度”值被设为1mm,上一层刀路与下一层刀路之间有1个台阶(见图4-31),图4-30比图4-29多出来的刀路正好用来切削台阶。而实体的下半部分没有斜度,也就不会产生台阶,因此实体的下半部分的刀路只用于切削角位。

图4-30 重新生成剩余铣刀路

图4-31 铣削斜面留下的台阶
(12)修剪图4-30所示的刀路。在“工序导航器”中双击选项,在【剩余铣】对话框中单击“指定修剪边界”按钮
。在【修剪边界】对话框中,对“选择方法”选择“点”选项、“修剪侧”选择“外侧”选项,如图4-32所示。
(13)单击“俯视图”按钮,把实体切换成俯视图,然后在实体左上角选择4个点,绘制1条封闭的线路(封闭的线路范围比刀路程序
在拐角的残留余量略大),如图4-33中的左上角所示。
(14)在【修剪边界】对话框中单击“添加新集”按钮,在实体右上角选择4个点,绘制1条封闭的线路,如图4-33中的右上角所示。
(15)采用相同的方法,绘制左下角与右下角的封闭线路,如图4-33所示。

图4-32 设置【修剪边界】对话框参数

图4-33 绘制4条封闭的线路
(16)单击“生成”按钮,修剪后的刀路如图4-34所示。
5)创建精加工刀路
(1)单击“菜单|插入|程序”命令,在【创建程序】对话框中对“类型”选择“mill_contour”选项,对“程序”选择“NC_PROGRAM”选项,把“名称”设为A3。
(2)单击“确定”按钮,创建A3程序组。此时,A1、A2和A3并列,并且A1、A2和A3都在NC_PROGRAM的下级目录中。
(3)在“工序导航器”中选择选项,单击鼠标右键,在快捷菜单中单击“复制”命令。再选择A3,单击鼠标右键,在快捷菜单中单击“内部粘贴”命令,把刀路程序
粘贴到A3程序组下。
(4)在“工序导航器”中双击选项,在【面铣】对话框中单击“指定面边界”按钮
,在【毛坯边界】对话框中,对“平面”选择“指定”选项,在实体上选择台阶面作为指定平面(此平面为加工的最低深度)。
(5)在【面铣】对话框中,对“刀具”选择“D6R0(铣刀-5参数)”选项,如图4-35所示。

图4-34 修剪后的刀路

图4-35 选择“D6R0(铣刀-5参数)”选项
(6)在【面铣】对话框中设置“刀轨设置”选项卡参数,对“切削模式”选择“轮廓”选项,把“毛坯距离”值设为5.0000(单位:mm)、“每刀切削深度”值设为0.2000(单位:mm)、“最终底面余量”值设为0.000、“附加刀路”值设为0,如图4-36所示。
(7)单击“切削参数”按钮,在弹出的【切削参数】对话框中,单击“余量”选项卡,把“部件余量”值、“壁余量”值、“最终底面余量”值都设为0。
(8)单击“非切削移动”按钮,在弹出的【非切削移动】对话框中单击“进刀”选项卡,在“封闭区域”列表中,对“进刀类型”选择“与开放区域相同”,在“开放区域”列表中,对“进刀类型”选择“圆弧”、“半径”值设为2mm、“圆弧角度”值设为90°、“高度”值设为0、“最小安全距离”值设为5mm。单击“转移/快速”选项卡,在“区域内”列表中,对“转移方式”选择“进刀/退刀”选项、“转移类型”选择“直接”选项。
(9)单击“进给率和速度”按钮,在弹出的【进给率和速度】对话框中,把主轴速度值设为1200 r/min、切削速度值设为500 mm/min。
(10)单击“生成”按钮,生成的面铣刀路如图4-37所示。

图4-36 设置“刀轨设置”选项卡

图4-37 生成的面铣刀路
(11)单击“前视图”按钮,切换视图方向。可以看出刀路有斜度,如图4-38所示。

图4-38 刀路有斜度
(12)在“工序导航器”中选择选项,单击鼠标右键,在快捷菜单中单击“复制”命令。选择A3,单击鼠标右键,在快捷菜单中单击“内部粘贴”命令,把刀路程序
粘贴到A3程序组。
(13)在“工序导航器”中双击选项,在【面铣】对话框中选择D6R0的刀具。把“每刀切削深度”值设为0、“最终底面余量”值设为0。单击“进给率和速度”按钮
,在弹出的【进给率和速度】对话框中,把主轴速度值设为1200 r/min、切削速度值设为500 mm/min。
(14)单击“生成”按钮,生成精加工底面的刀路,如图4-39所示。
(15)在“工序导航器”中选择选项,单击鼠标右键,在快捷菜单中单击“复制”命令。选择A3,单击鼠标右键,在快捷菜单中单击“内部粘贴”命令,把刀路程序
粘贴到A3程序组。
(16)在“工序导航器”中双击选项,在【面铣】对话框中对“切削模式”选择“
轮廓”选项、“步距”选择“恒定”选项,把“最大距离”值设为0.2mm、“每刀切削深度”值设为0、“最终底面余量”值设为0、“附加刀路”值设为3。单击“切削参数”按钮
,在弹出的【切削参数】对话框中,单击“余量”选项卡,把“部件余量”值、“壁余量”值、“最终底面余量”值都设为0。
(17)单击“进给率和速度”按钮,在弹出的【进给率和速度】对话框中,把主轴速度值设为1200 r/min、切削速度值设为500 mm/min。
(18)单击“生成”按钮,生成精加工侧壁的刀路,如图4-40所示。

图4-39 精加工底面的刀路

图4-40 精加工侧壁的刀路
(19)单击“创建工序”按钮,在弹出的【创建工序】对话框中,对“类型”选择“mill_planar”选项。在“工序子类型”列表中单击“底壁铣”按钮
,对“程序”选择A3选项、“刀具”选择“D6R0(铣刀-5参数)”选项、“几何体”选择“WORKPIECE”选项、“方法”选择“MILL_ROUGH”选项。设置完毕,单击“确定”按钮。
(20)在【底壁铣】对话框中单击“指定切削区底面”按钮,在实体中选择圆台上表面,如图4-41所示。
(21)在【底壁铣】对话框中设置“刀轨设置”选项卡参数,对“切削区域空间范围”选择“底面”选项,对“切削模式”选择“往复”选项、“步距”选择“刀具平直百分比”选项,把“平面直径百分比”值设为75.0000(%)、“底面毛坯厚度”值设为3.0000(单位:mm),把“每刀切削深度”值和“Z向深度偏置”值都设为0.0000,如图4-42所示。

图4-41 选择圆台上表面

图4-42 刀轨参数
(22)单击“切削参数”按钮,在弹出的【切削参数】对话框中,单击“余量”选项卡,把“部件余量”值、“壁余量”值、“最终底面余量”值都设为0。
(23)单击“非切削移动”按钮,在弹出的【非切削移动】对话框中单击“进刀”选项卡。在“封闭区域”列表中,对“进刀类型”选择“与开放区域相同”选项;在“开放区域”列表中,对“进刀类型”选择“线性”选项,把“长度”值设为3mm、“高度”值设为2mm、“最小安全距离”值设为5mm。
(24)单击“进给率和速度”按钮,把主轴速度值设为1200 r/min、切削速度值设为500 mm/min。
(25)单击“生成”按钮,生成的底壁铣刀路如图4-43所示。
(26)单击“菜单|插入|工序”命令,在【创建工序】对话框中,对“类型”选择“mill_planar”选项。在“工序子类型”列表中单击“平面铣”按钮,对“程序”选择A3选项,对“刀具”选择“D6R0(铣刀-5参数)”选项(铣刀-5参数)、“几何体”选择“WORKPIECE”选项、“方法”选择“METHOD”选项。设置完毕,单击“确定”按钮。
(27)在【平面铣】对话框中单击“指定部件边界”按钮,在【部件边界】对话框中,对“选择方法”选择“面”选项、“刀具侧”选择“外侧”选项,选择圆台的上表面,单击“确定”按钮。然后,单击“指定底面”按钮
,选择圆台的下底面。
(28)在【平面铣】对话框中对“切削模式”选择“轮廓”选项,把“附加刀路”值设为0。
(29)单击“切削层”按钮,在弹出的【切削层】对话框中,对“类型”选择“恒定”选项,把“每刀切削深度”值设为0.1000(单位:mm)、“增量侧面余量”值设为0.1*tan(10),如图4-44所示。

图4-43 生成的底壁铣刀路

图4-44 设置【切削层】对话框参数
(30)单击“切削参数”按钮,在弹出的【切削参数】对话框中,单击“余量”选项卡,把“部件余量”值和“最终底面余量”值都设为0。
(31)单击“非切削移动”按钮,在弹出的【非切削移动】对话框中单击“进刀”选项卡。在“开放区域”列表中,对“进刀类型”选择“圆弧”选项,把“半径”值设为2mm、“圆弧角度”值设为90°、“高度”值设为0、“最小安全距离”值设为5mm。单击“快速/转移”选项卡,在“区域内”列表中,对“转移类型”选择“直接”选项。
(32)单击“进给率和速度”按钮,把主轴速度值设为1200 r/min、切削速度值设为500 mm/min。
(33)单击“生成”按钮,生成平面铣加工斜面的刀路,如图4-45所示。
(34)仿真模拟平面铣加工斜面的刀路如图4-46所示。

图4-45 平面铣加工斜面的刀路

图4-46 仿真模拟平面铣加工斜面的刀路