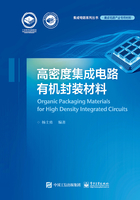
3.1.2 挠性覆铜板
挠性封装基板的制造过程主要包括挠性覆铜板和挠性封装基板的制造两个阶段。挠性覆铜板是将导电铜(Cu)箔与聚酰亚胺(PI)薄膜黏结复合在一起形成的Cu/PI复合结构,主要分为有胶型(三层结构)和无胶型(两层结构)两种类型,包括单面覆铜板和双面覆铜板两种结构(见图3.31)。

图3.31 单面和双面挠性覆铜板的剖面结构
1.有胶型挠性覆铜板
有胶型挠性覆铜板是采用改性环氧树脂或丙烯酸树脂黏合剂(Adhesive,Ad),将导电铜箔和聚酰亚胺薄膜经加热辊压或层压黏结复合在一起形成的Cu/Ad/PI复合结构。首先将黏合剂胶液涂敷在聚酰亚胺薄膜表面上,然后加热处理使溶剂等小分子挥发份完全除去,进一步加热使铜箔与带黏结层的聚酰亚胺薄膜黏结复合形成挠性覆铜板。黏合剂涂敷加工的质量将直接影响挠性覆铜板的质量稳定性,要求黏合剂涂敷的单点厚度偏差低于0.5%。压合黏结是在一定温度和压力条件下将已经涂敷黏合剂的聚酰亚胺薄膜与铜箔连续地(或片状模压)黏结复合在一起。图3.32和图3.33分别是挠性覆铜板连续生产装置及生产现场。
目前,挠性覆铜板的生产技术已经相当成熟,所生产挠性覆铜板的黏结强度、尺寸稳定性、挠曲寿命、电绝缘性能和长期可靠性等都有保证。但是,有胶型挠性覆铜板中环氧树脂或丙烯酸酯胶黏层的存在会导致其耐热性、耐化学药品性及电绝缘性较差,导致所制备的挠性封装基板无法满足高密度电子封装的使用要求。表3.6总结了典型有胶型挠性覆铜板的主要性能。

图3.32 有胶型挠性覆铜板连续生产装置

图3.33 有胶型挠性覆铜板连续生产现场
表3.6 典型有胶型挠性覆铜板的主要性能(薄膜厚度:25μm;铜箔厚度:压延铜箔35μm)

2.无胶型挠性覆铜板
无胶型挠性覆铜板是在聚酰亚胺(PI)薄膜的两个表面涂敷一层厚度为热塑性聚酰亚胺(TPI)黏结层形成的TPI/PI/TPI三层复合薄膜。其中,TPI黏结层厚度通常为5~7μm,PI薄膜厚度为12.5~50μm。由于TPI为可熔性聚酰亚胺树脂,当加热至熔点温度时形成可流动的熔体,可以充分浸润被黏结物(如铜箔等)的表面,形成Cu/TPI/PI/TPI/Cu覆铜板。由于TPI黏结层也属于PI薄膜的一部分,故成为无胶型挠性覆铜板。无胶型挠性覆铜板具有比有胶型覆铜板更好的耐热性、耐化学药品性及介电性能,具有无卤阻燃特性。近年来,随着无胶型挠性覆铜板性能的不断提高,挠性封装基板已经成为非常重要的高密度封装基板。
无胶型挠性覆铜板的制造方法主要包括涂敷法、层压法和电镀法等3种。涂敷法需要先在铜箔表面上涂敷聚酰亚胺树脂,经干燥、亚胺化后形成绝缘薄膜层,从而形成挠性覆铜板。该方法的优点是可以获得高铜箔剥离强度,聚酰亚胺薄膜层厚度可以控制得很薄,但难以制造较厚的绝缘薄膜层。在制作两面铜箔的挠性覆铜板时,首先在铜箔表面上涂敷一层黏结性高的热塑性聚酰亚胺黏结树脂,再涂敷一层高尺寸稳定的聚酰亚胺薄膜专用树脂;然后涂敷一层热塑性聚酰亚胺黏结树脂。在其表面覆盖铜箔后,加热、加压形成双面挠性覆铜板。所涂敷的热塑性聚酰亚胺黏结树脂的熔点高于300℃,真空压制温度约为350℃。该工艺的难点是,如何克服聚酰亚胺树脂在高温亚胺化过程中产生的少量水分和残留溶剂导致的气泡问题。另外,采用该工艺方法生产双面覆铜板的技术难度较大,投资高。
表3.7比较了涂敷法制造的两种无胶型挠性覆铜板的主要性能。可以看出,压延铜箔制造的覆铜板在耐折性、弯曲性等方面优于电解铜箔覆铜板。
表3.7 典型无胶型双面挠性PI覆铜板的主要性能

层压法需要在聚酰亚胺薄膜(12.5~50μm)的两个表面涂敷热熔性聚酰亚胺黏结层膜,在两面覆盖铜箔(通常厚度为18~70μm)后,在真空压机上加热、加压形成无胶型双面挠性覆铜板(见图3.34)。热熔性聚酰亚胺树脂必须同时具有可溶性和可熔性。聚酰亚胺树脂必须能够溶解在有机溶剂中形成均相树脂溶液,当涂敷在聚酰亚胺薄膜表面后形成黏结层膜,经加热处理后,所有的有机小分子和水分等挥发物必须排出,以免在高温压制覆铜板过程中由于小分子挥发物溢出受阻而形成气泡或内部缺陷。聚酰亚胺树脂在高温加热条件下能够熔融,在热辊压加工过程中,树脂熔融后形成具有一定流动性的熔体,在压力作用下与铜箔和聚酰亚胺基膜两个表面充分浸润,排出所有的有机小分子和水分等挥发物,形成黏结界面。通常,热熔性聚酰亚胺树脂的熔点超过300℃,因此覆铜板的热辊加工往往需要在350℃左右的温度和真空条件下进行。由于热熔性聚酰亚胺树脂的分子结构密度较大,难以进行化学刻蚀成孔,通常采用激光或等离子体刻蚀工艺。层压法制造的覆铜板在耐折性上明显优于涂敷法制造的覆铜板。层压法适合在真空压机上制备片状双面覆铜板,而在连续生产设备上制造卷状覆铜板产品则比较困难。

图3.34 无胶型双面挠性覆铜板的制备方法
层压法用的TPI复合胶膜也可在聚酰亚胺薄膜连续化生产线上生产(见图3.35),首先将聚酰亚胺薄膜专用树脂(PI)和热熔性聚酰亚胺树脂(TPI)通过三层共挤模具(Multi Manifold Dies)一次性涂布在环状不锈钢带上,经烘干成膜后,再进行高温处理、亚胺化,得到连续的TPI/PI/TPI聚酰亚胺复合薄膜,即PI芯膜的上下表面同时具有一层热熔性TPI胶膜,其中TPI胶膜的厚度为5~7μm;然后将TPI/PI/TPI三层复合薄膜的两面与铜箔贴合后,在高温辊压机(或高温真空压机)上加热至350~400℃,通过模压形成双面挠性覆铜板(2L-FCCL)。

图3.35 无胶型挠性覆铜板的连续生产过程
溅射/电镀法(或化学镀/电镀法)首先需要在聚酰亚胺薄膜上,采用磁控溅射的方式形成铜的晶种层,或采用化学镀的方式制作出较薄的导体“底基层”;然后采用电镀法制得所要求厚度的导电层,制成FCCL。此方法可以制造出9μm以下的超薄铜层FCCL,相较于前面两种技术而言,目前溅射/电镀法主要用于生产铜箔厚度为2~4μm的FCCL产品,主要用于生产高端FPC——COF(Chip On Film,是将FPC作为封装载体)的覆铜板。由于这种方法可制造出其他两种方法很难制造的薄导电金属层,因此更利于高密度布线。目前,COF覆铜板用2L-FCCL的50%以上都是采用溅射法/电镀法制造的。
采用该方法制造2L-FCCL时需要注意PI薄膜的高吸水性、针孔、剥离强度与离子迁移性等问题。另外,所制造的2L-FCCL的铜箔剥离强度较低,在溅射加工前需要对PI薄膜进行表面预处理(如等离子体处理等),目前主要应用于对黏结力要求不高的场合。
表3.8比较了3种FCCL制造的工艺方法。日本住友金属矿业公司、美国3M公司、美国Rogers公司、韩国LS电线集团、韩国ILGIN铜箔有限公司、韩国东丽世韩公司、韩国DMS电线有限公司、韩国SK化学,以及我国台湾律胜科技公司、山东天诺光电材料有限公司等,都采用溅射/电镀法制造二层型FCCL。在美国,80%的2L-FCCL采用此法生产。表3.9比较了层压法和电镀法制造的无胶型挠性覆铜板的主要性能。
表3.8 3种FCCL制造工艺方法的比较

续表

表3.9 层压法和电镀法制造的无胶型挠性覆铜板的主要性能

在磁控溅射/电镀法基础上,珠海创元公司成功开发了离子注入/电镀技术,在真空环境和高电压下,将铜电离成带有能量(最高达上百万电子伏特)的等离子体,轰击PI膜表面,使铜离子嵌入PI表层以下,与PI膜形成新的化学键,在薄膜表面形成纳米级厚度的掺杂过渡层后,通过等离子体沉积技术在掺杂结构层表面沉积铜,形成一层致密的、具有高导电性能的表面铜层,最终在基材表面形成结合力良好、表面方阻小的导电籽晶层后,再通过多级连续电镀增厚至需要的铜层厚度,经过表面防氧化处理后,制作为FCCL产品(见图3.36)。

图3.36 离子注入/电镀技术制造FCCL的工艺过程
该方法具有下述优点:①无胶,铜层与PI直接结合,无任何有机过渡层,是纯正的两层结构;②薄铜,铜层逐步加厚,提供铜厚2~9μm的双面产品;③低粗糙度,铜层与PI表面结合面的粗糙度取决于PI膜表面的光洁度,创元FCCL的Rz比全球最好的日矿铜箔低一个数量级(见图3.37);④纳米级铜晶粒,铜层为均匀的100nm晶体。

图3.37 离子注入/电镀技术生产的FCCL的超低轮廓铜箔
表3.10是该技术生产的FCCL的主要性能,具有下述性能特点:①薄铜+高结合力,注入离子与PI膜形成的纳米级厚度掺杂过渡层如同“锚”,保证了结合力大于0.7N/mm(铜箔厚度:12μm);②高可靠性,无胶(精确控制的注入深度和剂量,确保线路刻蚀干净、彻底),耐离子迁移性能卓越;③高频性能,Rz低,高频信号传输损耗低;④物理性能的耐弯折性能优异。图3.38是离子注入/电镀技术生产的FCCL产品照片。
表3.10 离子注入/电镀技术生产的FCCL的主要性能


图3.38 离子注入/电镀技术生产的FCCL产品照片