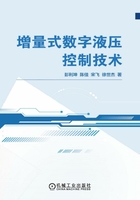
3.2 数字液压缸建模
传递函数模型不仅能够表征系统的动态特性,还可以清晰地体现系统的结构组成,便于从物理本质上对系统响应作出解释。对数字液压缸进行频域建模,能够有效判断系统的稳定性,准确揭示系统的控制结构及各结构参数的作用,对数字液压控制系统整体性能的提高和结构参数的优化设计具有重要意义。
本节将以图3-1所示机械反馈式数字液压缸为主要研究对象,首先针对目前阀控缸建模过程中存在的问题试图建立统一的数字液压控制系统传递函数模型,便于后续进行理论解析。
3.2.1 传递函数模型
为简化分析,将步进电动机-减速机-滑阀阀芯、滚珠丝杠-减速机-反馈螺母之间的连接均视为刚性连接,并将数字液压控制系统分为步进电动机及滑阀(简称数字滑阀)、阀芯及反馈机构和阀控缸三个部分分别进行建模,最终整合得到系统总的传递函数模型。
1.阀芯及反馈机构模型
由数字液压控制系统的工作原理可知,滑阀阀口开度是由阀芯、螺母、滚珠丝杠和减速机反馈机构的旋转运动复合而成的,参照图3-2,可用式(3-1)所示方程简述其运动过程。
式中,xv为阀芯实际轴向位移;xm为数字滑阀旋转产生的阀芯轴向输入位移;xf为液压缸运动产生的阀芯轴向反馈位移;xp为活塞位移;t1为阀芯轴端螺杆螺母导程;t2为滚珠丝杠导程;ir为滚珠丝杠轴端减速机传动比;θ为步进电动机旋转角度;is为步进电动机轴端减速机传动比。
图3-8 典型的阀控非对称缸结构
2.阀控缸模型
数字液压控制系统特殊的结构形式决定了其一般采用阀控非对称缸结构,图3-8所示为典型的阀控非对称缸结构。图3-8中各阀口面积梯度分别为w1=w3,w2=w4,定义阀口面积梯度比为m=w2/w1,则m=1时为对称阀,m≠1时为非对称阀;A1、A2分别为液压缸无杆腔和有杆腔有效作用面积,定义液压缸两工作腔面积比为n=A2/A1,则n∈(0,1),而就对称缸而言,n=1;V1、V2分别为无杆腔和有杆腔等效容积;p1、p2分别为无杆腔和有杆腔工作腔压力;ps为供油压力;p0为回油压力;Ci为液压缸内泄漏系数;Ce为外泄漏系数;M为折算到活塞杆上的总质量;FL为负载力;Bp为负载及活塞运动黏性阻尼系数;KL为负载等效弹簧刚度。图3-8中箭头方向均为正向。
与电液伺服和比例伺服等阀控液压伺服系统类似,阀控缸模型也是数字液压控制系统建模中的重要环节。建立阀控缸的传递函数模型存在较大困难,需要进行大量简化和合理假设,尤其是非对称缸的建模不能简单套用对称缸建模的方法,对系统工作点的设定和负载压力、负载流量的定义必须考虑系统不对称特性引起的变化。虽然已有大量文献对此进行研究,但仍需阐明以下几个重点:
1)传递函数模型是对系统在稳态工作点附近进行线性化处理得到的,仅能近似表征稳态工作点附近的系统特征,工作点变化较大时将使系统动态特性产生较大误差。
2)系统工作原点的选取必须具有代表性,一般应选取系统固有频率最低的位置作为工作原点,从而保证整个系统的稳定性。
3)传递函数模型建立的关键是通过负载压力pL与负载流量qL的定义将液压缸两腔的流量连续性方程整合,pL和qL可以有多种定义形式,但必须符合液压缸输出功率与输入功率匹配的原则。
遵循上述原则,本节旨在建立一种通用的阀控缸传递函数模型。
(1)确定系统工作原点和初始容积
在液压系统中,液压弹簧刚度最小的位置,固有频率最低,阻尼比最小,系统稳定性最差,故以液压弹簧刚度最小的位置作为稳态工作点,进行系统特性的研究具有代表性。
定义液压弹簧刚度为
由于液压缸两工作腔中油液始终处于压缩状态,可以看作两液压弹簧并联,故系统的总液压弹簧刚度为
式中,βe为油液体积弹性模量;L为活塞行程。此时,xp代表活塞位置。
由式(3-2)可知,时,液压弹簧刚度最小,即有Khmin=
。以此位置为稳态工作点,取液压缸总压缩体积Vt=A1L,则两工作腔的初始容积分别为
液压缸运动过程中,无杆腔和有杆腔瞬时等效容积分别为V1=V10+A1xp,V2=V10-A2xp。
由上述分析可知,当n=1时,有V10=V20=Vt/2,这与阀控对称缸系统建模时将工作原点设定在活塞中位处相符。而对于阀控非对称缸系统,n≠1,系统固有频率最低的位置既不是行程中点,也非两工作腔容积相等的位置。
(2)定义负载压力和负载流量
设q1为流入无杆腔流量,q2为流出有杆腔流量,则液压缸稳态运行时,存在,进而可得
故液压缸输出功率为Wc=p1q1-p2q2=(p1-np2)q1。液压缸输入功率即滑阀输出功率为Wv=pLqL,因此负载压力pL与负载流量qL的定义必须满足条件Wc≤Wv,即输出功率不大于输入功率。
假设系统功率完全匹配,即Wc=Wv始终成立,则pLqL=(p1-np2)q1,故可定义
为建立统一的数学模型,综合考虑两工作腔流量,可在稳态时对式(3-6)进行等价变换,得到负载流量的另一种定义形式
当n=1时,由式(3-5)和式(3-7)可得,pL=p1-p2,qL=(q1+q2)/2,这与阀控对称缸系统建模时常用的负载压力和负载流量的定义相同,故该定义形式具有通用性。
(3)阀口流量方程线性化
不考虑超压和气穴现象等非常规情况,即恒有p1,p2∈(p0,ps),则当xv≥0时,阀口流量方程为
式中,Cd为阀口流量系数。忽略回油背压,令p0≈0,并结合式(3-4)和式(3-5)、式(3-7),可得
xv<0时,阀口流量方程为
与xv≥0同理,可得
在设定工作点处对负载流量qL进行线性化,可得
式中,Kq为流量增益系数;Kc为流量-压力系数。Kq、Kc取值分别为
(4)液压缸流量连续性方程
假设:控制阀至液压缸的连接管路粗且短,不计管路内的压力损失和动态损失;液压缸两工作腔内油液温度和体积模量为常数,压力相对均衡;液压缸内外泄漏均为层流状态。可得液压缸两工作腔内流量连续性方程为
则
假设液压缸在初始位置附近作微小移动,式(3-16)可忽略最后一项,联合式(3-3)和式(3-7),得到
将式(3-9)和式(3-12)代入式(3-17),整合后得到
式中,Kt为比例系数;Ctc为等效泄漏系数;Cta为附加泄漏系数。其取值分别为
(5)液压缸力平衡方程
液压缸输出力与负载力平衡方程为
液压缸稳态运行时,忽略弹性负载及黏性阻尼,则有
故此时A1也为系统的负载面积。
对式(3-14)、式(3-18)和式(3-19)进行拉式变换,得到以活塞位移为输出的阀控缸传递函数:
式中,Ktc=Kc+Ctc为总流量-压力系数。
3.系统结构框图及总传递函数模型
图3-9所示为数字液压控制系统结构框图。
忽略弹性负载,即令KL=0,同时由于,忽略此项,式(3-21)简化为
图3-9 数字液压控制系统结构框图
此时,结合式(2-6),可进一步化简整理得到如图3-10所示简化的系统结构框图。
图3-10 简化后数字液压控制系统结构框图
图3-9中,为步进电动机细分步距角;
为数字滑阀角度-位移转换系数;
为活塞位移反馈系数;
为数字滑阀固有频率;ξs=
为数字滑阀的阻尼比;
为液压固有频率;
为液压阻尼比。
不考虑阀芯旋转阻力矩的影响,则数字滑阀的传递函数为
不考虑负载和附加泄漏的干扰作用,数字液压控制系统内反馈回路开环传递函数为
式中,为开环放大系数;
为阀控缸传递函数;H(s)=kf为反馈通道传递函数。故内反馈回路闭环传递函数为
此时,图3-10可进一步整理得到整合的系统结构框图如图3-11所示。
以脉冲数N为输入,活塞位移xp为输出的数字液压控制系统总传递函数为
式(3-26)综合考虑了正向运动(xv≥0)和反向运动(xv<0)两种工况。在不同的工况下分别取相应阀系数Kq、Kc,即可得到相应的数学模型。同时该传递函数取m=1和m≠1分别对应对称阀控数字液压控制系统和非对称阀控数字液压控制系统两种类型,因而模型具有统一性和通用性。此外,由于建模过程兼顾了n=1时的情况,因此该模型同样适用于数字阀控对称液压缸系统。
图3-11 整合后数字液压控制系统结构框图
由于包含小孔节流的流量-压力二次关系,数字液压控制系统属于本质非线性系统。此外,还存在液压伺服系统中常见的控制阀饱和、死区和滞环,传动机构间隙以及运动部件的摩擦等因素,系统非线性严重。由前文分析可知,数字液压控制系统由于反馈机构内置,多采用单出杆结构,系统同时具备阀控非对称动力机构固有的非对称性,动态特性复杂,跟踪精度及运行平稳性易受较大影响。因此建立相对准确的数学模型,研究系统的非线性动态特性及非线性因素对系统性能的影响,对数字液压控制系统的性能优化及拓展应用具有重要意义。
这里采用传统的线性化方法建立了传递函数模型,由于对系统进行了大量的简化和近似处理,该传递函数模型只适用于分析数字液压控制系统稳态及工作原点附近的情况,不能准确描述系统的非线性和时变特性。文献[30]、[31]建立了阀控非对称缸的非线性模型,并采用微分几何方法通过状态反馈实现了系统模型的精确线性化。文献[32]建立了比例阀控非对称缸系统的非线性状态方程模型,并分析了流量死区对系统动态跟踪性能的影响。文献[33]根据非线性动力学理论,通过理论分析和试验验证,研究了非线性弹簧力和非线性摩擦力对液压缸动态特性的作用。文献[34]则通过解析方法分析了时滞及死区等非线性因素对简化的液压位置调节系统动力学特性的影响。现有的液压伺服系统非线性建模及动态特性研究多以通用或简化的阀控缸系统为研究对象,缺少对数字液压控制系统结构特殊性的关注。文献[35]专门针对数字伺服步进液压缸,初步建立了系统的非线性状态方程模型,分析了摩擦非线性对系统的影响。在此基础上,本章进一步考虑数字液压控制系统结构的特殊性,对数字滑阀螺旋运动及反馈机构动态进行详细建模,同时对系统的非线性描述进行补充和修正,以得到更为合理完善的数学模型,从而为数字液压控制系统的性能预测和补偿控制提供理论基础。
3.2.2 状态方程模型
3.2.1节在建立数字滑阀传递函数模型的过程中,将阀芯的旋转动态折算到步进电动机转子轴上,以简化数字滑阀阀芯螺旋运动的数学模型,但所用步进电动机模型为简化模型,且并未给出数字滑阀旋转阻力矩的具体形式;在建立阀芯及反馈机构模型时,仅对滑阀阀芯、反馈螺母、滚珠丝杠及减速机等反馈机构的运动位移传动关系进行描述,而忽略了阀芯和反馈机构的动态。事实上,阀芯及反馈机构的动力学模型,对于研究数字滑阀的驱动能力和卡滞特性以优化阀结构设计和选型,研究反馈机构对系统非线性动态特性的影响,揭示数字液压控制系统的特殊性等,都具有重要意义。因此,本节首先建立数字滑阀旋转动态模型和阀芯平动及反馈机构动态模型,其次修正并完善阀控非对称缸部分的非线性模型,最终得到完整的数字液压控制系统非线性状态空间模型。
1.数字滑阀旋转动态模型
由式(2-3)数字滑阀旋转的动力学方程可得
为建模方便,步进电动机的输出转矩简化为
式(3-28)能从一定程度上反映步进电动机的矩角特性,但缺乏对绕组自感、互感以及磁路饱和等非线性的描述。为充分考虑步进电动机的非线性,同时兼顾建模难度,本节在Leenhouts模型基础上进行一定简化,得到基本参数可测的二相混合式步进电动机非线性模型。Leenhouts模型于1991年提出,是近代较为通用的步进电动机非线性模型。它在早期的Singh-Kuo模型和Pickup-Russell模型的基础上进一步研究了绕组自感的变化过程,将绕组自感由基波分量和恒定分量的和来表达,并在转矩中考虑了三次谐波的影响,用饱和系数ktc来表示旋转电压、绕组电感和转矩中与绕组电流有关的项。对于二相混合式步进电动机,应用Leenhouts模型可得到其转矩方程为
式中,TA、TB、Td分别为A、B相绕组电磁转矩及定位转矩;iA、iB分别为A、B相电流;kt0、ktc分别为转矩系数及磁路饱和系数;h3为电磁转矩三次谐波相对幅值;θe=Zrθ为电角度;D为定位转矩幅值。
由于数字液压控制系统通常采用较为成熟的电流矢量恒幅均匀旋转细分驱动技术,可近似认为步进电动机相电流与预置电流相等,则
式中,Imax为最大相电流;θte=Zrθm=ZrθNN为指令电度角。
2.阀芯平动及反馈机构动态模型
阀芯平动的动力学方程为
式中,mv为阀芯质量;xv为阀芯轴向位移;Bv为阀芯在阀套内滑动阻尼系数;Ffv为滑动库仑摩擦力;Fs、Ft分别为作用在阀芯上的稳态液动力和瞬态液动力;Fv为轴向驱动力。
(1)稳态液动力
对于单个节流口,考虑径向间隙时,稳态液动力计算式为
式中,速度系数为Cv=0.98;w为节流口面积梯度;Δpsv为节流口压降;射流角α与节流口开口量和径向间隙rc的比值有关,即
,当rc=0时,α≈69°,Kf=0.43。
图3-12所示为考虑节流口差异的阀控非对称缸结构,各节流口初始遮盖量为Δi,则输入阀芯位移为xv时,各节流口的开口量和压降分别为
数字滑阀工作时,同时有两个可控节流口起作用。忽略正遮盖节流口上因泄漏引起的稳态液动力,同时,考虑稳态液动力的作用总是使节流口关闭,方向与阀芯位移方向相反,故数字滑阀总稳态液动力为
图3-12 考虑节流口差异的阀控非对称缸结构
(2)瞬态液动力
单个节流口工作时的瞬态液动力为
式中,L为阻尼长度。
在图3-12中,液流运动在节流口1和2处产生的瞬态液动力始终指向节流口关闭的方向,为正阻尼,阻尼长度以L1表示,而液流运动在节流口3和4处产生的瞬态液动力始终指向节流口打开的方向,为负阻尼,阻尼长度以L2表示。忽略负开口量节流口上的瞬态液动力,则总瞬态液动力为
(3)轴向驱动力
图3-13所示为滑动螺旋传动机构受力分析,N为滑动螺旋面法向,T为滑动螺旋面切向,A为阀芯轴向,C为阀芯周向;ψ=arctan[t1/(πd2)]为螺旋面升角,t1为螺纹导程,d2为螺纹中径;θr为阀芯螺杆与反馈螺母的相对转角,可表示为
式中,θb为滚珠丝杠轴角位移。假设反馈螺母不动,则在周向力Fa的作用下,阀芯旋转,沿螺旋面滑动产生周向相对位移θrd2/2和轴向位移xv。此时,螺旋面上反馈螺母对阀芯的支持力为FN,摩擦力为FT,则阀芯的轴向驱动力为
由图3-13可知,阀芯与反馈螺母在螺旋面法线方向N上的相对位移可表示为
图3-13 滑动螺旋传动机构受力分析
由于机械传动机构中不可避免地会存在间隙,使得力和位移的传递呈现非线性。建模时可将螺旋传动结构、反馈机构及减速机传动间隙,统一等效为螺纹间隙以简化模型。设传动间隙宽度为2xc,则螺旋面上正压力为
式中,KN为材料的接触刚度;BN为材料的结构阻尼。
由图3-13可知,阀芯相对于反馈螺母沿螺旋面切线方向T滑动的速度为
图3-13中阀芯周向相对转角θr及轴向位移xv均为正方向,则螺旋面上滑动摩擦力为
式中,ρv=f/cosβ为摩擦当量角,f为螺纹面动摩擦系数,β为螺纹牙型侧角。
由图3-13可知,驱动阀芯旋转所需周向力为
故阀芯旋转的负载转矩为
实际中,由于反馈螺母仅轴向固定,阀芯旋转的负载转矩同时也通过减速机反向传动至滚珠丝杠轴充当驱动力矩,则滚珠丝杠轴的力矩平衡方程为
式中,Jb为滚珠丝杠轴等效转动惯量;Bb为等效阻尼比;Tfb为等效动摩擦转矩;作用在丝杠轴上的反馈力矩为
式中,KT为滚珠丝杠传动机构的综合等效扭转刚度。
图3-14所示为滚珠丝杠传动机构偏差分析。K1=2π/(ηt2)为滚珠丝杠的力矩-力转换系数,η为传动效率,一般可取η=0.98;K2=2π/t2为位移-角度转换系数;Kl为滚珠丝杠传动机构综合轴向刚度;Kθ为滚珠丝杠传动机构综合扭转刚度。分析可得
图3-14 滚珠丝杠传动机构偏差分析
滚珠丝杠传动机构综合轴向刚度是指包括滚珠丝杠螺母副和支撑轴承在内的整个传动机构的综合拉压刚度,体现了滚珠丝杠传动机构抵抗轴向变形的能力。计算时,将滚珠丝杠传动机构的各组成部件视为一系列弹簧组件串联,由胡克定律可得
式中,Ks、Kn、Kb分别为丝杠轴、螺母组件和支撑轴承的轴向刚度。
滚珠丝杠轴的轴向刚度与丝杠轴的安装方式有关。在数字液压控制系统中,滚珠丝杠轴内置于活塞杆中,采用一端止推,另一端简支的安装方式。故丝杠轴的轴向刚度为
式中,E为材料弹性模量;ds为丝杠轴径;ls为支撑轴承到螺母的安装距离,与活塞位移xp有关。
为消除滚珠丝杠的轴向间隙,滚珠丝杠螺母组件一般采用预压型。当预压力为Fa0时,由赫兹弹性接触理论可得螺母组件轴向刚度为
式中,Ca为螺母组件基本动额定载荷;Kn0为预压基本动额定负荷10%的轴向负荷时,螺母组件的理论轴向刚度;0.8Kn0为综合考虑螺母座和轴承座等安装零部件的刚度,式中取刚度修正系数为0.8。
Kn0和Kb均可根据所用产品型号,从样本尺寸表中查得。
同理由胡克定律可得,滚珠丝杠传动机构综合扭转刚度为
式中,Kcθ为联轴器及减速机等效扭转刚度,可从产品样本尺寸表中查得;Ksθ为滚珠丝杠扭转刚度,计算公式为
式中,G为材料切变模量;Ls为丝杠总长,与活塞有效行程L有关。
综上所述,将式(3-29)、式(3-30)和式(3-43)代入式(2-3),可得数字滑阀旋转动力学模型为
将式(3-34)~式(3-37)代入式(3-31),可得阀芯平动动力学模型为
将式(3-43)、式(3-45)代入式(3-44),可得反馈机构动力学模型为
3.阀控缸动态模型
由于数字滑阀在实际使用过程中不可避免地会出现磨损,即使是新阀也存在加工及装配造成的阀芯与阀套间径向间隙,由此导致滑阀泄漏,影响滑阀性能。尤其是当数字液压控制系统内位置反馈增益较大时,数字滑阀的实际阀芯位移较小,此时阀的径向泄漏不可忽略,如仍采用式(3-8)和式(3-11)阀口流量方程,将导致较大仿真误差。
图3-15所示为典型滑阀泄漏流量曲线,可以看出阀芯与阀套间径向间隙引起的泄漏流量有如下特性:①阀芯处于中位时泄漏量最大;②泄漏量随阀芯移动迅速减小。虽然通过新阀径向间隙泄漏的液流为层流,但在使用过程中阀口节流边受液流冲蚀磨损,径向泄漏增大,且变为紊流。
采用紊流模型描述开口量时各阀口泄漏流量。同时,修正开口量
时通过锐边节流孔流量公式,可得新的阀口流量方程为
图3-15 典型滑阀泄漏流量曲线
式中,kli为各阀口泄漏系数;x0i为各阀口开度修正量,相当于最大泄漏量对应的无泄漏阀口开度。若不考虑各节流口间的差异,wi、Δi、kli、x0i可用w、Δ、kl、x0统一表示。当缺少数字滑阀中位泄漏流量曲线时,设径向间隙为rc,可近似取
式中,μ为油液动力黏度。
由此可知,流入无杆腔流量q1和流出有杆腔流量q2分别为
将式(3-56)和式(3-57)代入式(3-15)液压缸工作腔内流量连续性方程,可得
式(3-19)液压缸力平衡方程可进一步写作
式中,FL为液压负载力,即液压输出力;Fe为外载荷;Fb为反馈机构所需驱动力;Ffc为活塞、活塞杆与缸筒之间的摩擦力。
由式(3-45)可知,反馈机构所需驱动力为
Canudas de Wit提出的LuGre模型是在Dahl模型的基础上,将微观下的摩擦接触面看作大量具有随机行为的弹性bristle,并基于bristle的平均变形建立的动态摩擦模型。LuGre模型采用一阶微分方程,较全面、精确地描述了预滑动、摩擦滞环、变静摩擦及Stribeck效应等各种摩擦现象,反映了摩擦运动的机理,因而广泛用于机械液压等伺服系统的设计与研究。以LuGre模型考察摩擦力Ffc,则有
式中,z为bristle平均变形量,Fc为库仑摩擦力,Fsc为最大静摩擦力,σ0为bristle刚度系数,σ1为bristle阻尼系数,σ2为黏性摩擦系数,vsk为Stribeck速度。
将式(3-61)和式(3-62)代入式(3-60),可得液压缸的动力学模型为
4.完整的系统非线性状态空间模型
定义系统状态量为
输出量为y=x1=xp,输入量为u=N,联立式(3-52)~式(3-54)、式(3-58)、式(3-59)、式(3-63),得到考虑阀芯螺旋运动及反馈机构动态、阀口正遮盖误差和径向泄漏、机构传动间隙以及动摩擦力等因素的完整的数字液压控制系统非线性状态方程模型,见式(3-64)。
式中,各函数关系式为