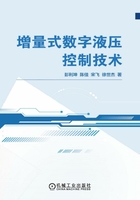
3.1 典型的内驱式数字液压缸结构形式
3.1.1 机械反馈式数字液压缸
典型的机械反馈式数字液压缸结构如图3-1所示,主要由步进电动机、减速机、三位四通滑阀、螺杆螺母副、液压缸以及滚珠丝杠反馈机构等组成,多为阀控非对称缸结构,采用阀缸一体化集成设计,并将反馈机构内置于活塞杆中,属于内驱式刚性间接反馈数字液压缸。由于采用螺旋传动副,使得阀芯与反馈机构分离,容易形成双级或多级间接反馈,增强了系统结构配置的灵活性,从而使得数字液压缸具有结构紧凑,阀芯移动范围大,活塞运动速度快等优点。图3-1中所示减速机增大了步进电动机和滚珠丝杠的适用范围,为非标配组件,目的是为了方便在数字液压缸设计成型后进一步对系统性能进行微调,可根据数字液压缸的实际应用需求合理取舍。
图3-1 机械反馈式数字液压缸结构
1—活塞杆 2—滚珠丝杠 3、6—减速机 4—螺杆螺母副 5—阀芯 7—步进电动机
数字液压缸是一种具有局部内反馈的复合系统,如图3-2所示,其基本工作原理为:输入的脉冲信号经过细分电路调制后,驱动步进电动机及减速机传动机构带动滑阀阀芯旋转;阀芯的旋转运动在其端部螺杆螺母副的作用下转化为直线运动(反馈螺母轴向固定),形成阀口开度;通过改变阀口开度,调节液压油的流向和流量,以控制液压缸的运动方向和速度;液压缸的移动通过内置于活塞杆中的滚珠丝杠转化为旋转运动,并经减速机减速后传动至螺杆螺母副,形成负反馈,使阀芯复位,阀口关闭,液压缸停止运动。当有连续脉冲信号输入时,液压缸以相应速度朝相应方向直线运动,直至阀芯反馈位移与输入位移相等,阀口完全关闭,由此实现了以数字脉冲的频率和数量对液压缸速度和位置的精确控制。因此控制器只需根据期望位移和速度输出规划好的脉冲序列,即能实现开环控制,使数字液压缸按照预定的轨迹运动。由于控制方式简单,以数字脉冲信号直接控制,阀缸一体,采用常见的滑阀结构实现液流控制,具有结构紧凑,控制方便,定位精度高,抗干扰、抗污染能力强等优点,能够更好地适应有一定精度要求的复杂、恶劣工作环境。但受步进电动机矩频特性限制以及结构参数无法在线调整等因素影响,机械反馈式数字液压缸的响应频率、控制精度及自适应能力不太可能达到很高的要求。
图3-2 机械反馈式数字液压缸工作原理
3.1.2 磁力耦合式数字液压缸
图3-3所示为重庆大学机械工程学院的研究团队设计研制的磁耦合式数字液压缸,属于采用复合反馈形式的闭环控制数字液压缸,主要是在机械反馈式数字液压缸的基础上通过采用磁耦合机构作为反馈并增加了旋转编码器改进而成,因此其工作原理及特性与机械反馈式数字液压缸基本一致,主要区别在于液压缸内滚珠丝杠将活塞的直线运动转化为旋转运动后并不直接通过机械传动机构反馈至数字阀芯,而是通过缸内与滚珠丝杠直接相连的磁铁和缸外与阀芯直接相连的转盘以磁力耦合传递的方式将滚珠丝杠的旋转运动反馈至滑阀阀芯,形成控制闭环。由于磁耦合组件内外隔离,回避了机械传动所需的旋转密封,加工难度及要求极大降低。同时,由于在缸外采用旋转编码器产生数字反馈信号形成复合反馈方式,可用于进一步构建数字阀的闭环控制以补偿系统温度、压力负载、内泄及死区等因素对控制精度产生的不利影响。但受磁力耦合方式传动能力与可靠性的限制,以及采用将旋转运动直接反馈至旋转编码器和阀芯螺杆的单级反馈方式,使得其传递的速度、转矩及阀口开度不可能很大,只适用于负载力较小、低速和精度要求不高的场合。
图3-3 磁耦合传动数字液压缸结构
1—步进电动机 2—花键 3—万向联轴器 4—阀芯 5—外螺纹 6—编码器 7—缸外转轴 8—缸外转盘 9—后缸盖 10—磁铁 11—缸内转盘 12—缸体 13—滚珠丝杠 14—丝杠螺母 15—空心活塞杆
3.1.3 螺旋伺服式数字液压缸
螺旋伺服式数字液压缸最大的特点在于直接通过改变液压缸活塞两端的液力平衡状态,利用差动液压力来推动液压缸活塞运动。螺旋伺服式数字液压缸最早出现于1970年,为德国Rexroth公司研制的一种基于螺纹伺服机构的液压脉冲缸,其结构如图3-4所示。由于采用液压缸活塞内置控制阀芯的结构,利用三通阀来控制差动缸,零部件少,结构紧凑,但加工难度较高。
浙江工业大学研究团队利用液压螺旋伺服机构研制出的螺旋伺服式数字液压缸如图3-5所示,其工作原理为高压油(压力为ps)经可调节流阀(或调速阀)至控制活塞杆底部的活塞下腔(即工作腔,压力为pc)。活塞下腔与活塞杆内的回油孔6相通,并通过活塞杆上开设的轴对称小孔10及液压缸内壁上开设的三角螺旋槽,最终与低压回油腔(压力pa=0)相通。三角螺旋槽与弓形回油口构成可变节流口,利用活塞杆旋转即可改变可变节流口面积,从而控制工作腔的压力。工作腔始终与高压油液相通,高压油流量调节方便,可适应实际需要。当控制信号输入,步进电动机通过齿轮传动使活塞杆转动,此时可变节流口面积变小,则油液流向工作腔,腔内压力增大,打破了原来的平衡关系,活塞向上移动,这样又逐渐使可变节流口面积增大,直到恢复为原来的值,工作腔内的压力也减小至原平衡值,与高压腔和工作负荷FL的向下推力相等,活塞重新达到一种平衡关系。反之亦然。这样步进电动机输入一定转角,活塞就产生相应的位移,从而实现通过步进电动机带动液压缸活塞旋转,控制螺旋槽与回油孔的通流面积以改变高低压腔的液力平衡,来推动活塞产生一定位移直至重新恢复液力平衡状态。螺旋伺服式数字液压缸属于内驱式柔性直接内反馈式数字液压缸,具有结构简单、成本低、抗污染能力强等优点,但只适用于小行程运动场合。
图3-4 早期德国力士乐数字液压缸
a)整体结构 b)阀芯结构局部放大
图3-5 螺旋伺服式数字液压缸
a)原理图 b)结构图
1—缸盖 2—上盖 3—活塞杆 4—弓形回油口 5—三角螺旋槽 6—回油孔 7—缸筒 8—活塞 9—缸底 10—小孔
3.1.4 内循环式数字液压缸
西南科技大学研究团队设计了一种内循环数字液压缸,如图3-6所示。它能接收脉冲信号,并在内部通过电磁线圈控制柱塞组的定量吸排油过程将脉冲信号转换为液压推力,控制液压缸的位移和速度。这种液压缸不需要外部系统供油,是一种完全一体化的结构,克服了传统液压系统能量损失多、效率低和外泄漏的问题,具有一定的新意,是一种新型的数字液压缸。
图3-6 内循环式数字液压缸
a)整体结构 b)阀芯结构局部放大
3.1.5 多闭环控制数字液压缸
日本IHI(石川岛播磨重工)公司生产的ALMX-3003TC型闭环控制电液步进液压缸,如图3-7所示,采用了步进电动机、滚珠丝杠螺母副、内置式机液随动伺服阀的整体结构。由于能够通过编码器进一步形成外闭环反馈控制,因此能够补偿温度、压力负载、内泄及死区等因素对系统产生的影响,提高控制精度。这种数字缸与磁力耦合式数字液压缸一样,采用了复合反馈形式,属于多闭环控制数字液压缸。
图3-7 日本IHI公司闭环控制电液步进液压缸
1—活塞 2—丝杠螺母 3—阀套 4—阀芯 5—滚珠丝杠 6—编码器齿轮 7—滚珠丝杠齿轮 8—编码器 9—步进电动机齿轮 10—步进电动机
可以看到,仅仅是内驱式数字液压缸就有多种不同形式,不可能一一进行深入的理论研究,因此本章的后续理论研究内容将对象限定为课题组研究应用较多、较为熟悉的机械反馈式数字液压缸,其研究方法和分析结论对其他内驱式数字液压缸的分析研究具有一定的参考意义。
机械反馈式数字液压缸本质是利用步进电动机作为电-机转换元件,以数字脉冲信号直接控制液压缸位移和速度的机液伺服机构,具有结构紧凑、控制简单、定位精度高、抗污染能力强等优点,能够更好地适应有精度要求的复杂、恶劣的工作环境。但特殊的内部结构使得数字液压缸的系统特性主要取决于固有的结构参数,而无法在线调整,因此,初始的结构设计对提高数字液压缸本身的响应特性以及构建综合性能优良的数字液压控制系统至关重要。而目前,针对数字液压缸响应的本质及结构参数作用的研究还相对较少,这将是本章后续研究分析的重点。