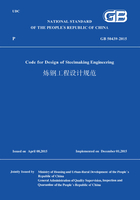
6.3 Process Equipment
6.3.1 The series of EAF volumes shall include 20t,30t,50t,60t,70t,90t,100t,120t,150t,180t,200t,220t,250t,300t,320t and 350t.A new EAF steelmaking shop shall be provided with the furnace volume specified in the series and also the volume selected shall not be less than 70t.
6.3.2 The configuration relation between furnace volume and diameter of furnace shell and between furnace volume and rated power of transformer should be in accordance with the provisions of Table 6.3.2.
Table 6.3.2 Configuration relation between furnace volume and diameter of furnace shell and between furnace volume and rated power of transformer

6.3.3 Overall platform structure should be used for the whole furnace.A horizontal locking device shall be installed below the tilting platform.When the tilting centerline position is determined in the design,the furnace shall be ensured to automatically return to the home position in case of failure of tilting mechanism.
6.3.4 The furnace shall be equipped with tubular water cooled roof and disassemble shell.The upper shell shall be composed of cage framework,which is made of steel pipes,and in-built tubular water cooled panels.The lower shell shall be composed of the cylindrical and spherical shell made of welded plates and lined with refractory to form a bath.
6.3.5 Except for EAF used for production of stainless steel,other EAF shall be provided with EBT mode.
6.3.6 Full hydraulic drive shall be provided for EAF.The titling angle of furnace to furnace door side for slag removal and that to tapping side shall meet the process requirements for slag removal and tapping.The furnace shall be provided with the ability for quick automatic returning to the home position when the target tapping is achieved.For the furnace roof,the lifting stroke shall be 400mm-500mm and the rotating angle shall meet the process requirements for charging and other relevant operations.The electrode and furnace roof should be rotated synchronously,or may be rotated individually.
6.3.7 The position adjustment in electrode lifting/lowering should be performed by proportional valve and electrode regulator.When the electrode is moved at the highest speed,the response time of electrode regulation system shall not be more than 100ms.Reliable insulation shall be provided between electrode arm and post.The total length of electrode arm and busbar shall be minimized in the condition to meet the requirement for electrode lifting/lowering and rotating movements and also the electrode arm and busbar shall be in isosceles or equilateral triangle arrangement at any dimensional position.The imbalance coefficient of impedance among three phases of busbar shall not be more than 5%.
6.3.8 The hydraulic system of furnace should be supplied with non-combustible media like water glycol.The hydraulic system shall be of reliability of operation and shall ensure that electrode can be lifted to a certain height in case of power failure and furnace tilting for tapping can be performed.
6.3.9 The furnace shall be equipped with CoJet oxygen and carbon lance at furnace wall and the oxygen supply and carbon injection capacity shall meet the requirement for melting intensity and foamed slag submerged arc melting.
6.3.10 At least 12 elevated bins should be provided for the mechanical material feeding system to furnace roof and ladle and the capacity shall meet the requirement for operation in more than 16 hours.The capacity of active lime bin shall meet the requirement for operation in more than 8 hours.The feeding system may be controlled in the master control room of EAF and in operation desk at tapping side in a centralized way.
6.3.11 The inner dimension of the doghouse shall be adaptive to the critical size for front and back tilting of furnace body and furnace roof opening,the opening of the movable charge door shall meet the requirement for furnace shell lifting and exchange operation,and the exhaust hole shall be located above taphole.The doghouse shall be provided with heat-insulation and sound-absorption material on the inner wall.
6.3.12 The size of the casting crane for EAF shall be determined based on the maximum tapping,ladle weight and slag volume.