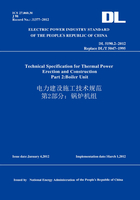
8.3 Flue Gas Denitrification
8.3.1 The erection of metal structures shall meet the following requirements:
1 The erection of reactor steel structure,platforms and staircase shall comply with the related requirements of Chapter 4 in this Part.
2 The erection of flue gas ducts,the reactor shell and expansion joints shall comply with the related requirements of Chapter 7 in this Part.
3 The erection of the guide plates shall meet the design requirements.The plane curvature deviation for the plane guide plates shall not exceed 5mm.The deviation for the spacing from the wall plate shall not exceed 5mm.The radius deviation for the arc guide plates shall not exceed 3mm and the center location deviation shall not exceed 5mm.
4 The elevation deviation for the internal support beams inside the reactor shall not exceed±3mm.The levelness deviation shall not exceed 3mm.The axial line deviation shall not exceed 10mm.The allowable deviations of the relative distance between the support beams in the vertical direction and in the horizontal direction shall be 2mm and 5mm,respectively.
5 During erection,the positions of the fixed support devices and sliding support devices inside the reactor shall be checked to ensure the free expansion of the reactor.
6 The welds and arrises in the wall plates of the reactor,which may influence the erection of the sealing devices,shall be burnished smoothly.The sealing plate local flatness deviation shall not exceed 5mm.The top sealing plate unloading ash slope shall not be less than 45°.
7 The reactor shell shall be involved in the boiler flue gas and air system whole pressure decay test.The supports or pipe connecting seats for the measuring points shall be completed before pressure decay test.
8.3.2 The erection of the internal devices of the reactor shall meet the following requirements:
1 The catalyst modules shall not be unpacked and the moistureproof measures shall be taken during transportation and storage.If there is any damage in the package,it shall be repaired in time.
2 Before the erection of catalyst modules,all the welding work in the shell,the internal devices and the upper shell internal cavity shall be completed,and the region between the furnace and the reactor shall be cleaned completely.
3 The erection of the catalyst modules shall be carried out before the start-up of the boiler complete unit is implemented.The period of the catalyst being exposed to the uncontrolled atmosphere shall meet the manufacturer's requirements.
4 No squeezing or collision shall occur for the catalyst modules during transportation.Moreover,the direction of the modules shall be noticed during transportation and hoisting.
5 Before the erection of catalyst modules,the damage situations for the modules shall be checked.If there is any damage in the module,the module shall be replaced or repaired by the manufacturer.
6 The arrangement of the catalyst modules shall be orderly.The deviation for the clearance between the modules shall not exceed 5mm,and the seals shall be tight.
7 The erection of the catalyst testing bars shall be clean.
8 The spray ammonia device and the support beam shall be connected tightly.The wear-resistant sleeve shall be fixed firmly,with the correct direction.
9 The nozzle angle shall meet the design requirements.And the spray pipes shall be fixed reliably.
8.3.3 The erection of the ammonia system shall meet the following requirements:
1 The installation of the compressor for unloading liquid ammonia shall comply with the related requirements of GB 50275 Code for Construction and Acceptance of Compressor,Fan and Pump Erection Engineering.
2 The erection of storage tanks and grooves shall meet the related requirements of DL 5190.3 Technical Specification for Thermal Power Erection and Construction-Part 3:Steam Turbine Set,and the following requirements shall apply:
1)Hydrostatic test and leak test under the design pressure for the liquid ammonia tanks shall be carried out according to the design requirements.Leak test may be carried out together with the pipes in the liquid ammonia system.
2)Hydrostatic test,blowing and the leak test for the ammonia evaporation tank shall be carried out,and its requirements are the same as those for the pipes in liquid ammonia system.Inspection and blowing for hydrostatic test shall be carried out to the hot medium side and the heat release side,and it shall meet the related requirements of DL 5190.5 Technical Specification for Thermal Power Erection and Construction-Part 5:Piping and System.
3)Hydrostatic test and leak test under the design pressure for the vapor ammonia buffer tank shall be carried out according to the design requirements.The leak test may be carried out together with the pipes in the vapor ammonia system.
4)Hydrostatic test and the leak test for the nitrogen gas tanks shall be carried out according to the related requirements of DL 5190.5 Technical Specification for Thermal Power Erection and Construction-Part 5:Piping and System.
5)The filling water test shall be carried out to the waste ammonia absorption tanks.
3 The installation,pressure test,blowing of water,steam,gas,oil pipes and valves shall comply with the related requirements of DL 5190.5 Technical Specification for Thermal Power Erection and Construction-Part 5:Piping and System.
4 The erection,pressure test and blowing of the pipes of the ammonia system shall meet the related requirements of DL 5190.5 Technical Specification for Thermal Power Erection and Construction-Part 5:Piping and System,and the following requirements shall apply:
1)The repairing number of the leakage points in the welds in any pipe in the ammonia system shall not exceed 2 times.Otherwise,the pipe shall be cut and replaced and the welding shall be carried out again,and any flange or weld in the pipes shall not be located inside the wall or inconvenient for the maintenance.
2)The vapor and liquid ammonia pipes shall be equipped with the air or nitrogen blowing pipes according to the design requirements.
3)The nondestructive testing shall be carried out to all craters in the liquid ammonia pipes.
4)The pipes in the ammonia system shall be equipped with the special valves and accessories,and there shall be no spare parts with copper,zinc coating,tin coating.
5)For all valves(such as the check valves,the throttle valves,the stop valves,safety valves,the float valves,the electromagnetic valves,the electric valves and the float type liquid level indication device and so on)in the ammonia system,the sensitivity and the seal tightness shall be tested before the erection,respectively.
6)After the erection of the pipes in the ammonia system and hydrostatic test has been qualified,the blowing shall be carried out with the dry and clean compressed air until there is no black spot from the outlet,and the flow direction of pipe blowing air shall be consistent with the flow direction of the medium.
7)Before the blowing to the system is carried out,the connection equipment joints shall be disassembled temporarily.They may be recovered after the blowing is finished.Those valves in the system,for which the blowing has been carried out,shall be disassembled and cleaned,and then they shall be reassembled.
5 After the blowing of the pipes in the ammonia system has been carried out,the leak test shall be carried out,and the leak test shall meet the following requirements:
1)The leak test shall be carried out with the dry and clean compressed air,and the test pressure shall meet the design requirements.
2)The pressure shall rise gradually.When the pressure reaches 10% of the regulated test pressure and it is not more than 0.05MPa,the first leakage inspection shall be carried out to all welding joints and connection locations after keeping up the pressure for five minutes.If there is any leakage position,the repair and retesting shall be done after the system has been connected to the atmosphere.
3)If it passed the first leakage inspection,the pressure shall be increased slowly to 50% of the regulated test pressure and then inspection shall be carried out.If there is no leakage and abnormal phenomenon,the pressure shall gradually rise in stage with 10% of the regulated test pressure and be kept up for 3minutes at each stage until the pressure reaches the regulated test pressure and is kept up for 10minutes,the inspection shall be carried out with the soap water or other foaming agents to confirm whether it leaks or not.
4)Those equipment,instruments and pipe fittings which are not involved in pressure test according to the requirements of the manufacturers'technical documents shall be isolated firstly before pressure test.
5)The valves at the both ends of the liquid level indicator shall be closed when starting the system pressure test,and they shall be opened gradually after the system pressure is stable.
6)After the system is filled with gas to the test pressure and the pressure is stable for 6 hours,the pressure parameters shall be recorded.If the pressure drop is not more than 1% of the test pressure after keeping up the pressure for 24 hours,it shall be qualified.The pressure drop can be calculated by the following equation.When the pressure drop exceeds the regulated value,the causes shall be found and the leakage shall be eliminated,and the test shall be carried out again until it is qualified.
Δp=p1-p2(273+t1)/(273+t2)
Where:Δp—The pressure drop,MPa.
p1—The gas pressure in the system at the test starting time,MPa,absolute pressure.
p2—The gas pressure in the system at the test ending time,MPa,absolute pressure.
t1—The gas temperature in the system at the test starting time,℃.
t2—The gas temperature in the system at the test ending time,℃.
6 After the leak test of pipes in ammonia system,the connections between the system and the equipment shall be recovered in time,and the nitrogen filling replacement shall be carried out together with the compressor.
7 The following conditions shall be met for filling ammonia into the system:
1)The acceptance of fire fighting facilities and antistatic facilities shall be qualified,and the operation condition shall be ready.
2)The system leak test and the insulation project for the equipment and pipes shall be completed and the acceptance shall be qualified.
8 Nitrogen replacement shall be carried out to the liquid ammonia pipes and storage tanks before the first ammonia unloading.During the later ammonia unloading operation,nitrogen replacement shall still be carried out to the open sections of the liquid ammonia pipes,and oxygen content in the system shall meet the requirements of the manufacturer's technical documents.
9 During the ammonia unloading,the liquid level in the liquid ammonia tank shall be monitored so that it can meet the requirements of the manufacturer's technical documents.And there shall be enough evaporation space in the upper part of the tank.