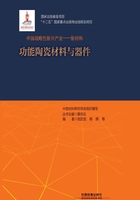
2.4 微波介质陶瓷器件
目前微波介质陶瓷已广泛用于制作各种微波器件,如介质基片、介质波导线路、介质天线、超小型片式电容器、介质谐振器、滤波器,能够满足现代微波通信、移动通信、卫星通信、广播电视、雷达、电子对抗、制导等技术对微波电路集成化、微型化、高可靠性和低成本的要求。近几年,微波介质陶瓷和器件的研究十分活跃,已成为目前功能陶瓷领域研究的热点之一。
2.4.1 微波谐振器件
在低频电路中,谐振回路是一种基本元件,它是由电感和电容串联或并联而成的,在振荡器中作为振荡电路,用以控制振荡器的频率;在放大器中用作谐振回路;在带通或带阻滤波器中作为选频元件等。在微波频率上,也有上述功能的器件,这就是微波谐振器件。它的结构是根据微波频率的特点从LC回路演变而成的。微波谐振器一般有传输线谐振器和非传输线谐振器两大类,传输线谐振器是一段由两端短路或开路的微波导行系统构成的,如金属空腔谐振器,同轴线空腔谐振器和微带谐振器等。
低频电路中的LC回路是由平行板电容C和电感L并联构成的,如图2-14所示。它的谐振频率为


图2-14 从谐振回路到谐振腔
当要求谐振频率越来越高时,必须减小L和C。减小电容就要增大平行板距离,而减小电感就要减少电感线圈的匝数,直到仅有一匝,如图2-14(b)所示;如果频率进一步提高,可以将多个单匝线圈并联,以减少电感L,如图2-14(c)所示;进一步增加线圈数目,以致相连成片,形成一个封闭的中间凹进去的导体空腔,如图2-14(d)所示;这就成了重入式空腔谐振器;继续把构成电容的两极拉开,则谐振频率进一步提高,这样就形成了一个圆盘子和方盒子,如图2-14(e)所示,这就是微波空腔谐振器的常用形式。虽然它们与最初的谐振回路在形式上已完全不同,但两者之间的作用完全一样,只是适用于不同频率而已。对于谐振腔而言,已经无法分出哪些是电感、电容,腔体内充满电磁场,因此只能用场的方法进行分析。
无论是LC型或空腔型谐振器,其基本原理都是将一定频率的电磁波封闭在有限空间(LC回路或金属空腔)中,并尽可能不让电磁波能量通过发热、辐射或其他形式消耗掉。LC回路是通过电磁能在L和C之间相互转换而使电磁波封闭于LC回路中;微波空腔谐振器是通过微波在金属腔壁之间来回反射形成振荡而使微波封闭在空腔内。后来人们发现,将某些高ε的陶瓷加工成一定形状和尺寸,一定功率的微波也可以借助于陶瓷与自由空间的边界反射而被封闭于陶瓷体内。这样,人们就用陶瓷介质制成了微波介质谐振器。介质谐振器与空腔谐振器相比,具有体积小、重量轻、加工制作简单、成本低、品质因数Q值高和温度系数小等优点。它们正以很大的优势越来越广泛地应用于微波系统的各个领域。
介质谐振器可以有多种形式,当前在微波系统中广泛实用的形式主要有如表2-8所示的三种形式。其中:①是使用TE01δ模的圆柱形陶瓷构成的最有代表性的微波介质谐振器,它不需要电极;②是使用TEM模的同轴型陶瓷介质谐振器,大多数情况下使用于λ/4型谐振器;③是微带形,底面是接地电极,以λ/2型应用得最好,由于其为平面形状,故有利于小型化、集成化,在微波集成电路中应用很广。
表2-8 介质谐振器的主要形式

2.4.2 微波介质滤波器
滤波器是无线电技术中许多设计问题的核心,可以利用它们来分开或组合不同的频率。随着通信技术的不断发展,作为通信系统中的一种不可缺少的器件,滤波器在近年来发展很快。由于电磁波频谱是有限的,且必须按应用加以分配,而滤波器是用来分离不同频率微波信号的一种器件,它的主要作用是抑制不需要的信号,使其不能通过滤波器,而只让需要的信号通过,因而既可用来限定大功率发射机在规定频带内辐射,反过来又可用来防止接收机受到工作频带以外的干扰。
图2-15是对滤波器作用的说明。由0.7kHz和1.7kHz两个正弦波所合成的信号,经过只允许频率低于1kHz的信号通过的滤波器后,输出端只剩下0.7kHz一个正弦波了。如果采用不同的滤波器,就可以取出各种不同的信号。

图2-15 滤波器的作用
对于微波滤波器,可按其作用、频率效应、结构特点等来分类。若按作用分类,则可划分为低通、高通、带通和带阻等四种类型的滤波器。理想低通滤波器的特性如图2-16所示,它能让零频到截止频率fc之间的所有信号都没有任何损失地通过,而阻止频率高于fc的所有信号;理想高通滤波器的特性如图2-17所示,它正好与理想低通滤波器相反,是让高于fc的所有信号通过,而阻止频率低于fc的所有信号;理想带通滤波器的特性如图2-18所示,它是让中心频率fc附近某一频率范围内的所有信号都毫无损失地通过,而阻止频率范围以外的任何信号;理想带阻滤波器的特性如图2-19所示,它正好与理想带通滤波器相反,带阻滤波器有时也称为带陷器。四种滤波器等效电路及衰减特性如图2-20所示。

图2-16 理想低通滤波器的特性

图2-17 理想高通滤波器的特性

图2-18 理想带通滤波器的特性

图2-19 理想带阻滤波器的特性

图2-20 四种滤波器等效电路及衰减特性
图2-21是一种基本的微波介质陶瓷滤波器结构,它是一块长方体的微波介质陶瓷体。沿长度方向上有三个通孔,中间孔为耦合孔,其余两个孔为谐振孔,除三个通孔所在面以及端口电极周围区域外,介质块其余表面全部进行金属化。该介质滤波器由两个谐振器构成,每个谐振孔的长度大约为谐振频率处的1/4波长,即构成一个1/4波长谐振器。在介质滤波器中,未金属化的端面为开路面,此处电场强度最大。与开路面相对的另一个端面为短路面,此处磁场强度最大。两个1/4波长同轴谐振器间通过耦合孔相互耦合。当信号经金属电极后由电容耦合到一个近似于终端短路的同轴谐振器中时,在谐振频率点产生谐振,能量由两谐振器间的耦合孔耦合到输出端的同轴谐振器,然后再经输出端电极与陶瓷块周围电极的耦合输出。输入输出的耦合强弱可以通过调节输入输出电容大小(即调节电极大小)来控制;而级间耦合强弱则可通过调整耦合孔的直径来确定。
根据微波理论,1/4波长同轴谐振器的谐振频率

式中,c为光速;L为沿电磁波传播方向的长度。
谐振器的谐振频率主要倚赖它沿波传播方向的长度L,而与其宽度W和厚度H无关。等效电路图如图2-22所示。

图2-21 微波介质陶瓷滤波器结构

图2-22 等效电路图
2.4.3 微带天线
2.4.3.1 微带天线的结构及特点
微带天线是由一块厚度远小于波长的介质板(称为介质基片)和印制电路板或微波集成技术覆盖在它的两面上的金属片构成的,其中完全覆盖介质板的一片称为接地板,而尺寸可以和波长相比拟的另一片称为辐射元,如图2-23所示。辐射元的形状可以是方形、矩形、圆形和椭圆形等。
微带天线的馈电方式分为两种,如图2-24所示。一种是侧面馈电,也就是馈电网络与辐射元刻制在同一表面;另一种是底馈,就是以同轴线的外导体直接与接地板相接,内导体穿过接地板和介质基片与辐射元相接。

图2-23 微带天线结构

图2-24 微带天线的馈电
微带天线的主要特点有:体积小、重量轻、低剖面,因此容易做到与高速飞行器共形,且电性能多样化(如双频带微带天线、圆极化天线等),尤其是容易与有源器件、微波电路集成为统一组件,因而适合于大规模生产。在现代通信中,微带天线广泛应用于100MHz~50GHz的频率范围。
2.4.3.2 微带天线的辐射原理
由于分析微带天线的方法不同,对它的辐射原理有不同说法。为了简单起见,我们以矩形微带天线为例,用传输线模分析法介绍它的原理。
设辐射元的长为l,宽为w,介质基片的厚度为h,现将辐射元、介质基片和接地板视为一段长为l的微带传输线,在传输线的两端断开形成开路,如图2-25所示。
根据微带传输线理论,由于基片厚度h≪λ,场沿h方向均匀分布。在最简单的情况下,场沿宽度w方向也没有变化,而在长度方向(l≈λ/2)有变化,其场分布如图2-26所示。

图2-25 矩形微带天线开路端电场结构

图2-26 场分布侧视图
由图2-26可见,在两开路端电场均可以分解为相对于接地板的垂直分量和水平分量,两垂直分量方向相反,水平分量方向相同,因而垂直于接地板的方向,两水平分量电场所产生的远电场同相叠加,而两垂直分量所产生的场反相相消。因此,两开路端的水平分量可以等效为无限大平面上同相激励的两个缝隙,如图2-27所示,缝的电场方向与长边w垂直,并沿长边w均匀分布。缝的宽度为Δl≈h,长度为w,两缝间距l≈λ/2。这就是说,微带天线的辐射可以等效为由两个缝隙所组成的二元阵列。

图2-27 等效辐射缝隙
2.4.4 微波介质陶瓷器件制备工艺
微波介质陶瓷器件(以谐振器为例)制备工艺流程如图2-28所示。下面对关键工艺进行介绍和说明。

图2-28 谐振器制备工艺流程
2.4.4.1 混料和球磨技术
因为粉料的颗粒大小、粒度分布及各组成的均匀程度直接影响烧成温度、质量和最终微波介质陶瓷材料及器件的各项性能。目前生产用的球磨机主要有滚动球磨机、行星球磨和搅拌球磨机。为了更好地控制颗粒的形貌和尺寸,大多厂家采用多种球磨技术混合使用。
1.滚动球磨机
滚动球磨是粉体生产中使用面较广的一种粉碎工艺。球磨是在钢制或瓷制的回转圆筒中加入粉碎物质和钢球、钢煅、瓷球或刚玉球等研磨介质,然后利用圆筒旋转产生研磨和冲击作用,从而使物料粉碎。当球磨机以不同转速回转时,筒体内的研磨体可能出现三种情况,如图2-29所示。转速太快,研磨体与物料贴附在筒体上一起运转,称为“转速状态”,研磨体对物料起不到冲击和研磨作用;转速太慢,研磨体和物料因摩擦力被筒体带到等于摩擦角的高度时,研磨体和物料就下滑,称为“倾泻状态”,对物料有研磨作用,但对物料没有冲击作用,因而粉磨效率不佳;转速适中,研磨体提升到一定高度后抛落下来,称为“抛落状态”,研磨体对物料有较大冲击和研磨作用,粉碎效果较好。因此,磨机转速控制至关重要。磨机的理论适宜转速,D0为球磨罐直径,实际转速应该根据球磨罐的直径和长度进行调节。

图2-29 筒体转速与研磨体运动的关系
影响粉碎和混合效率的因素主要有:
(1)功能陶瓷磨球一般采用ZrO2圆柱体与球体,一般不采用金属球,避免金属对陶瓷性能的恶化,材质尽可能与原材料组分相同,尺寸根据所需的粒度决定;
(2)装球量一般为磨罐容积的一半,磨球加入量正好盖没磨球,一般理想条件是对应蒸发空间50%,磨球占有空间30%,磨料20%;
(3)料∶球∶介质比控制为1∶(1~1.4)∶(0.8~1.2),粉料比较硬,磨球也略多,粉料黏度大,可适当增加分散介质量;
(4)延长球磨时间,球磨效率降低,细度降低也趋于缓慢,长时间的球磨会引入大量杂质,因此,球磨时间应在满足适当细度的条件下尽量缩短,一般混料时间较短,细磨时间相对长一点,20~40h;
(5)球磨分为干法和湿法,干法不加分散介质,主要靠球的冲击力破碎,湿法需加水或酒精等作为分散介质,靠球的相互作用进行粉碎,湿磨效率比干磨高,通常用水作为分散介质,若原料中有水溶性物质,可采用酒精等其他液体;
(6)当物料磨至一定细度后,研磨效率显著降低,这是因为已粉碎的细粉对大颗粒的粉碎起缓冲作用,较大颗粒难以进一步粉碎,为了提高研磨效率,使物料达到预期的细度,需加入助磨剂,常用的有油酸和醇类,例如,干磨时加油酸、乙二醇、三乙醇胺和乙醇等,湿磨时加乙醇和乙二醇等。
2.行星球磨机
行星球磨机是借助一种特殊装置,使球磨筒体既产生公转又产生自转,带动磨腔内的球磨介质产生强烈的冲击、研磨作用,使介质之间的物料被粉碎和超细化。它可看成是普通球磨机与离心式球磨机结合而发展出的一种机型。该机工作时,传动轴由电动机带动旋转,连接杆和筒体绕传动轴旋转;与此同时,固定齿轮带动传动齿轮转动,由此使装有磨介的筒体绕各自的轴心自转。这种公转与自转的运动使介质产生冲击、摩擦力,使物料粉碎。行星球磨机粉碎效率高、能耗低,而且兼具表面改性与表面处理的功能,同时对由多种成分构成的物料具有良好的均质作用。行星球磨机是目前制备高质量陶瓷粉体较先进的设备。
3.搅拌球磨机
搅拌球磨机主要是通过搅拌细小磨介来实现对颗粒物料的有效粉碎。搅拌球磨机由研磨筒、搅拌器和循环卸料装置等三部分组成。研磨筒轴中心部装有搅拌器,并填充有磨介。搅拌器的棒或叶片末端线速度一般为3~25m/s。磨介的线速度在搅拌器轴中心位置较低,但随着离轴中心距离的增加而增大,在棒或叶片末端处,其线速度达到最大值。由于搅拌器难以施加磨介所需的动能,所以磨介的线速度急剧降低,有利于降低磨介与筒壁的相互磨损。在搅拌器的搅动下,磨介与被研磨物料做多维循环运动和自转运动,从而在磨机内上下、左右不断地产生激烈的碰撞、剪切运动。由磨介重力和高速螺旋回转所产生的挤压力对物料进行摩擦、冲击、剪切作用而有效地进行超细粉碎,产品粒度可达亚微米级,并达到均匀分散的效果。
与普通球磨机相比,搅拌球磨具有以下特点:高转速与高磨介填充率使搅拌球磨机获得很高的功率密度,大大缩短研磨时间,能量利用率高,较普通球磨机节能50%以上;可以获得平均粒径小于1mm的粉料;结构简单、操作方便。经搅拌球磨研磨所得的粉料,粒径小、粒形圆润,特别有利于多层片式微波器件、多层片式电容器、多层ZnO压敏电阻、多层基片载体等器件的流延成型。
2.4.4.2 造粒技术
从有利于烧结和固相反应进行的角度考虑,希望获得超细的原料,但粉料越细比表面积越大,干压成型时不容易均匀地充满模具,经常出现成型件有空洞、边角不致密、层裂等问题。常通过造粒工艺解决这一问题。
造粒工艺是将磨细的粉料经过干燥、加胶黏剂,制成流动性好、粒径约为0.1mm的颗粒。一般使用的胶黏剂应满足以下要求:要有足够的黏性,以保证良好的成型性和坯体的机械强度;经高温煅烧能全部挥发,坯体中不留或少留胶黏剂残余杂质;工艺简单,没有腐蚀性,对瓷料性能无不良影响。干压成型造粒常用聚乙烯醇水溶液,使用这种胶黏剂进行生产的工艺简单,瓷料的气孔率小,加入量为3%~5%。此外,PVB、石蜡、酚醛清漆等胶黏剂也常用于造粒工艺中。造粒工艺常用的有加压造粒法、手工造粒法和喷雾造粒法。其中加压造粒法是将混合了胶黏剂的粉料经15~25MPa预压成块,然后将压块粗粉碎后过筛,筛余后的物料返回破碎,再过筛,筛余物料仍应压碎,使全部物料过筛,混合均匀。该工艺制出的颗粒体积密度大、机械强度高,能满足各种大型、异型制品干压成型的要求。手工造粒是将配料与5%~8%聚乙烯醇溶液混合均匀,然后在研钵中手工将该物料研制成小球,再将其过筛,多次重复上述操作,完成手工造粒。手工造粒法主要适于实验室对物料进行造粒。喷雾干燥造粒法简称喷雾造粒法,该工艺把混合好的胶黏剂的粉料做成浆料,用喷雾器喷入造粒塔中雾化,雾滴与塔中的热空气混合,进行热交换,使雾滴被干燥到一定程度,形成流动性好的球状团粒,由旋风分离器吸入料斗。该方法产量大,适合于连续化生产和自动化成型工艺。目前,企业生产中大多选用喷雾造粒法进行造粒。
2.4.4.3 成型技术
将造粒好的陶瓷粉体通过成型设备及工艺加工成一定形状坯体的过程称为成型。功能陶瓷的成型技术对其制品的性能有很大的影响。功能陶瓷元器件的形状、尺寸、材质、烧成温度不一,对各种元器件性能和质量的要求也不相同。块体微波介质陶瓷及器件的主要成型有干压成型、等静压成型、热压铸成型。片式多层微波介质陶瓷器件主要采用流延成型,将在第6章进行介绍。
1.干压成型
将造粒、流动性好、颗粒级配合适的粉料倒入一定形状的钢模内,借助于模塞,通过外加压力将粉料压制成一定的坯体。干压成型是利用模具在油压机上进行的。干压成型产品的质量主要受粉料本征特征、加压方式、压力大小、加压速度和保压时间的影响。
粉料自身堆集密度也会直接影响成型后坯体的密度。堆集密度是指加压前粉料在模具中自然堆集或适当振动时所形成的填充密度。它与堆集方式、粒径配比以及粉料的各种质量关系很大。其他条件相同时,堆集密度越大,可望获得质量更高的坯体。从等径球粉粒简单的几何排列可知,最大填充率为面心立方密堆或六方密堆,相对密度可达74.05%。如果是简立方堆集的话,则相对密度只为52.36%。通常粉料的堆积密度介于两者之间。如在填充时只在纵向加以振动,相对密度可达60%左右;如在三维方向加以振动,则其填充密度可接近立方密堆。在干压成型时,振动加料,特别是多维振动加料,能有效地提高坯体密度。此外,粗粒与细粒相互搭配,也可使坯体密度有一定改善。
加压方式主要有单向加压、双向加压和双向先后加压三种。单向加压通常是模具下端之承压板或模塞固定不动,压力只通过模塞上方加压,这时由于粉料之间以及粉料与模壁之间的摩擦阻力,会出现压力梯度分布,直接受压端密度大,远离受压端密度小。双向加压和单向加压的不同之处在于上下压头,同时朝模套内加压,其间存在压力梯度的有效传递距离却只为原来的一半,实际压力差变小,仅坯体的中间部分密度较低。在这种情况下,坯体的密度相对均匀多了。双向先后加压是先由上方加压,使模塞伸入模套,再改由下方加压,使下模塞压入。由于先后两次分别加压,压力传递比较彻底,有利于气体排出,密度比前两种方法都要均匀。单向加压和双向加压如图2-30所示。
成型压力的大小直接影响坯体和瓷体的密度。陶瓷坯体的压实过程可大致分为两步:第一步为加压前期,主要是粉粒在压力作用下的重排,以及对与粉粒大小相当或更大的空隙的填充。其时孔隙大量被压掉,密度增加较快。第二步为加压后期,此时刚性粉粒之间已基本相切。压力进一步加大,由于陶瓷粉料的脆性与不可压缩性,将在压应力集中的触点处压出碎片并填充在小孔隙之间,密度增加较慢。
升压速度与保压时间主要应从压力的传递和气体的排除两方面来考虑。升压速度过快,保压时间过短,使本来能够排出的气体来不及排出体外。同时,压力尚未传递到应有的深度,外力已卸除。升压速度过慢、保温时间过长,将影响工效。对于大型、厚、体高、形状较为复杂的产品,加压初期速度可以快些,后期宜慢些。对于小型、薄片等简单坯体,对加压速度无严格要求,可以采用快速冲压方式提高工效。为了提高压力的均匀性,通常采用多次加压。
干压成型的优点是生产效率高、工艺和设备简单、容易实现机械化自动化生产,干压成型粉体中水和黏合剂等成分少,烧成收缩率小,瓷体的强度和抗击穿强度高。缺点是模具成本高,每个规格产品需特定模具,且磨损大,产品具有明显的各向异性,上、下或上下同时加压,缺乏侧向加压。目前主要用于圆片、薄片状电子元件。

图2-30 单向和双向加压时压坯密度沿高度的分布
2.等静压成型
干压成型的产品结构和强度存在各向异性,为解决这个问题,必须使产品能受到均匀的各向加压。等静压成型就是满足这一要求而发展起来的,它是利用液体介质的不可压缩性和均匀传递压力的一种成型方法。即处于高压容器中的试样所受到的压力如同处于同一深度的静水中所受到的压力,所以称为静水压或等静压,根据这种原理而得到的成型工艺称为静水压成型或叫等静压成型。
等静压成型方法有冷等静压和热等静压两种类型。冷等静压又分为湿式等静压和干式等静压两种。
湿式等静压成型是将预压好的粉粒坯体,包封于弹性的塑料或橡胶做成的弹性模具内,置于高压容器内,密封后,注入高压液体介质,压力传递至弹性模具对坯料加压。然后释放压力取出模具,并从模具取出成型好的坯件。传压液体可用水、甘油或重油等,弹性模具材料应选用弹性好、抗油性好的橡胶或类似的塑料。视粉料特性及产品需要,容器内压力可予以调整,通常在35~300MPa,实际生产中常用100~150MPa。
干式等静压成型是对湿式等静压成型的改进。采用这种方法时,待压粉料的加添和压好工件的取出,都采用干法操作,而弹性模具并不都是处于液体之中,是半固定式的,可多次使用,经此改进后,工效及自动化水平大为提高。干式等静压成型模具,两头(垂直方向)并不加压,适于压制长形、薄壁、管状产品。
等静压成型方法对模具无特殊要求,适于压制形状复杂、大件且细长的功能陶瓷制品;湿式等静压容器可同时放入几个模具,还可压制不同形状的坯体。优点是坯体密度高、均匀性好、烧成收缩小,不易变形和开裂、不分层;成型时压力大小容易控制;粉料可以不用黏合剂或少用黏合剂。缺点是设备比较复杂、操作烦琐、生产效率不高。
3.热压铸成型
热压铸成型是目前块体微波介质陶瓷器件的主要成型方法。它是将煅烧过的熟瓷粉和石蜡等制成蜡块熔化,然后在压缩空气的作用下,使之迅速充满模具的各个部位,保压冷凝,便可脱模获得蜡坯。在惰性粉料的保护下,将蜡坯进行高温排蜡,然后清除保护粉粒,得到半熟的坯体。
1)蜡浆制备
热压铸成型必须用煅烧的熟瓷料,使用熟料的目的,除使反应充分均匀之外,还可减少石蜡的用量,降低烧结收缩和变形。瓷粉在拌蜡前应充分干燥,其含水率必须<0.5%。拌蜡前瓷粉应加热至60~80℃,再与熔化的石蜡混合搅拌,瓷粉过冷易凝结成团块,难以搅拌均匀。蜡浆制备过程如图2-31所示。

图2-31 蜡浆制备过程
以石蜡作为增塑剂,优点是它具有很好的热流动性、润滑性和冷凝性。石蜡是石油类产品,它是亲油而憎水的;而瓷粉是离子性或强极性的物质,与油之间缺乏强亲和力,所以,为了使瓷粉与石蜡更好地结合,必须采用硬脂酸或油酸一类的两性物质,作为粉料的表面活性剂或润湿剂。油酸分子式CH3(CH2)7CHCH(CH2)7COOH,硬脂酸的分子式CH3(CH2)16COOH,其中—COOH是极性的,能与粉料很好地结合,其他烷基部分是典型油性,和石蜡没有多大差别,能和它很好地结合在一起,即使粉粒为石蜡所润湿。
蜡浆中石蜡的用量,取决于粉料的粒度、粒形和粒度的配比。通常石蜡用量为瓷粉用量的12%~16%,油酸用量为瓷粉用量的0.4%~0.7%,硬脂酸用量为石蜡用量的5%左右或蜂蜡用量为石蜡用量的3%左右。
2)热压铸机及工艺参数
图2-32为热压铸机示意图。蜡浆置于热油浴锅2包围的蜡浆桶3之内,模具7置于工作台1的中心,压缩空气经阀门9、活塞6将模具顶紧,再经阀门5使蜡浆上升至模具7中,由于钢模本身是冷的,视工件大小和钢模温度,稍许保压冷却,即可卸压出模。如果室温较高时,必须将钢模冷却至一定低的温度后,才能再一次使用。热压铸工艺参数主要包括蜡浆温度、模具温度和铸浆压力。蜡浆温度直接决定着蜡浆的黏度和可浇注性。在一定范围内,浆温升高,则浆料的黏度降低,可使坯体颗粒排列致密,减少坯内的缩孔。浆温若过高,坯体体积收缩加大,表面容易出现凹坑。浆温和坯体大小、形状和厚度有关。形状复杂、薄壁的坯体要用热些的浆料压铸。一般浆温为65~75℃。模具温度决定坯体冷却凝固的质量和速度。模具温度也和坯体形状、厚度有关。压铸形状简单和厚壁的坯体时,模温要稍低;压铸形状复杂和薄壁坯体时,模温要稍高。一般模具温度为15~25℃。此外,铸浆压力和加压持续时间也同样与坯体的形状有关。小型坯体在0.3~0.4MPa维持5~15s;大型坯体在0.4~0.5MPa维持1min左右。

图2-32 热压铸机示意图
1—工作台;2—热油浴锅;3—蜡浆桶;4—加热装置;5,9—阀门;6—活塞;7—模具;8—温度计;10—脚控踏板;11—压缩空气进口。
3)高温脱蜡
如果将蜡坯直接进入窑炉烧结,随烧结温度的升高,会出现蜡浆流失、挥发、燃烧,瓷料将失去支持黏结而解体,不能保持原有形状。所以,在升温之前,必须先将蜡坯埋入疏松、惰性的保护粉粒之中。这种保护粉粒又称吸附剂,它是通过高温煅烧,活性极低、不易与瓷体黏结的粗大粉粒,在升温过程中,石蜡虽已向吸附剂中流渗、扩散,但吸附剂却始终支持着坯体。常用的吸附剂有煅烧过的氧化铝粉、煅烧过的氧化镁粉、煅烧过的滑石粉和石英粉等。一般排蜡温度为900~1100℃,使坯体初步发生化学反应,具有一定强度。排蜡的加热制度一般要根据瓷粉的性质、产品形状、大小及窑炉结构来决定。也可将低温阶段升温速度减慢,不必单独排蜡,直接烧成产品。
热压铸工艺具有操作简易、劳动强度不大,生产效率高等优点,适于外形复杂、精密度高的中小型、新型陶瓷制品的成型;其缺点是工序复杂、耗能较大、工期较长,不宜制作壁薄、大而长的产品。目前大多厂家采用热压铸成型微波介质陶瓷器件。
2.4.4.4 烧结技术
烧结是功能陶瓷及器件的一个关键工艺。烧结是通过一定的高温处理过程,使成型的坯体发生预期的物理化学反应和充分致密化,形成需要的化学组成、晶体和微观结构,得到具有要求的物理化学性能的陶瓷的全过程。目前,微波介质陶瓷及器件发展起来的烧结技术主要有常压烧结、微波烧结、放电等离子烧结、反应烧结。
1.常压烧结
常压烧结法是在大气条件下将坯体烧结的过程,是制备微波介质陶瓷最常使用的一种方法。材料在无外加压力下烧结,温度一般达到材料熔点的50%~80%即可引起足够的原子扩散。
在常压下进行烧结时,烧结温度、保温时间是最重要的工艺参数。Yoshida等研究Y2BaZnO5陶瓷时发现,保温时间对该材料的品质因数有很大影响。在1300℃烧结,当保温时间由2h延长至50h时,由于陶瓷致密度得到提升,介电常数εr从14.1增为15.3,Qf值从50000GHz显著提高到189000GHz。当保温时间进一步延长至100h时,由于Zn2+的挥发造成材料成分偏离化学计量,导致Qf值下降。Chen等研究了烧结时间对(Ca0.8Sr0.2)ZrO3陶瓷晶相结构和介电性能的影响。在1480℃烧结,当保温时间由2h增加到12h,晶胞体积逐渐下降,这是由于长时间烧结导致失氧所致,介电常数增大,Qf值先增加后减少,在10h达到最大值。
升温制度对材料性能的影响也很显著,合理的升温制度可减少制品开裂与结构缺陷现象。Li等研究了升温速率、保温时间和冷却速率对Ba(Zn1/3Nb2/3)O3-ZnNb2O6微波性能的影响。烧结参数对介电性能的影响程度从大到小依次为冷却速度、升温速率和保温时间,缓慢的升温速率、长保温时间和快的冷却速率对介电性能有明显的改善作用。最优的烧结制度为:升温速率为2℃/min,保温时间8h,在空气中冷却,此时最佳的介电性能:εr=32.75,Qf=34100GHz,τf=-10.2×10-6/℃。Lei等详细研究了升温速率对(1-x)ZnAl2O4-xTiO2(x=0.21)微波性能的影响。当以1℃/min升温至1500℃烧结时,由于烧结过程的延长,易使Zn2+挥发造成孔洞,同时Ti4+变价为Ti3+,导致烧结体内部出现“黑心”。随升温速率的提高,这一现象逐渐改善,当升温速率为5℃/min时,“黑心”现象完全消失,此时获得最致密的陶瓷且微波介电性能最佳:εr=11.6,Qf=74000GHz,τf=-0.4×10-6/℃。当升温速率大于5℃/min时,原子扩散不均匀,导致烧结体微孔增多,致密度降低。
烧结气氛对材料的相组成、显微组织、致密度、晶体缺陷等也有明显的影响。Shin等详细研究了氧分压对0.9MgTiO3-0.1CaTiO3微波介电性能的影响,发现第二相的量对氧分压相当敏感,弱还原气氛可提高烧结体的致密度,改善材料的介电性能。但过低的氧分压
容易使材料产生氧空位、Ti3+等晶格缺陷,导致其介电损耗增加。Zhou等研究了Bi2O3-ZnO-Nb2O5陶瓷在空气和氮气中的烧结行为和介电性能。结果表明:氮气有利于陶瓷的烧结,但不同气氛对不同组分介电性能的影响有所不同。Bi2(Zn1/3Nb2/3)2O7在900℃氮气中烧结获得最佳介电性能;而Bi2(Zn1/3Nb2/3-xVx)2O7(x=0.001)在空气中930℃烧结获得最优性能。
2.微波烧结
微波烧结是一种材料烧结工艺的新方法,其原理是物质在微波作用下发生电子极化、原子极化、界面极化、偶极转向极化等,将微波的电磁能转换为热能。它具有升温速度快、能源利用率高、加热效率高和安全卫生无污染等特点,并能提高产品的均匀性和成品率,改善被烧结材料的微观结构和性能,已经成为材料烧结领域里新的研究热点。
采用微波烧结技术制备功能陶瓷得到迅速发展,已用于Mg2iO4、BaTiO3、(Ba,Sr)TiO3、BiFeO3、BaTiO3/K0.5Bi0.5TiO3等介电、铁电与压电陶瓷的制备。微波介质陶瓷的应用主要在近几年。杨雪蛟等采用微波烧结技术,可使(Zr0.8Sn0.2)TiO4烧结温度较传统固相烧结降低70℃,保温时间缩短5/6,介电常数和品质因数分别提高17%和14%。这是因为微波烧结相对均匀的温度场使陶瓷中残余气体更易排出,促进了材料的致密化;同时降低了烧结活化能,促进离子扩散,提高陶瓷中阳离子排列有序度。谭颖等研究了Ba6-3xSm8+2xTi18O54(x=0.67,BST)陶瓷材料的微波烧结情况,将陶瓷片放入微波高温炉内1350℃烧结20min,升温速率为20℃/min。结果表明,与固相烧结工艺相比,微波烧结BST陶瓷缩短了烧结周期,晶粒细小分布均匀。微波烧结后,BST陶瓷的微波介电性能优良:εr=82.89,Qf=8450GHz(4.75GHz)。
由于微波介质陶瓷通常是微波透明材料,难以吸收微波,导致初期加热困难;此外,加热炉腔内不均匀的电磁场分布可能会使材料出现局部热失控,导致其开裂。因此,仍需深入地研究微波场的特性与分布,弄清微波与材料间的相互作用、传热等机制,进一步改进和完善其工艺。
3.放电等离子烧结
放电等离子烧结(spark plasma sintering,SPS)是近年来发展起来的一种新型快速烧结技术,如图2-33所示。由于等离子烧结技术融等离子活化、热压、电阻加热为一体,因而具有烧结温度低(比热压烧结和热等静压烧结低200~300℃)、烧结时间短(只需3~10min,热压烧结和热等静压一般为120~300min)、晶粒均匀、有利于控制烧结体的细微结构、获得的材料致密度高、性能好等特点。SPS消耗的电能仅为传统烧结工艺的1/5~1/3。

图2-33 SPS烧结示意图
SPS烧结机理目前还没有达成较为统一的认识,其烧结的中间过程还有待进一步研究。目前一般认为,SPS过程除具有热压烧结的焦耳热和加压造成的塑性变形促进烧结过程外,还在粉末颗粒间产生直流脉冲电压,并有效利用了粉体颗粒间放电产生的自发热作用,因而产生了一些SPS过程特有的现象。
SPS技术为磁性材料、功能梯度材料、纳米陶瓷、纤维增强陶瓷等一系列新型材料的制备提供了可能。诸如,可以在晶粒无显著长大的状态下烧结出纳米材料,制备难以烧结的功能陶瓷或新型化合物。Noh等以纳米TiO2粉末为原料,采用SPS法在760℃烧结10min,制得致密度为99.1%的纳米晶体TiO2。而相同初始粉末通过传统方法需在1300℃烧结2h才获得99.2%的致密度。与传统方法相比,SPS法制备的TiO2陶瓷介电常数εr变化不大,但由于粒径由6.5mm减小为300~400nm,单位体积晶界数量增加,导致Qf下降40%。Li等采用SPS法在1475℃烧结制备出致密度96%的La3Ti2TaO11钙钛矿层状结构微波陶瓷,而固相法烧结温度为1560℃。Shim等采用SPS法在1150℃烧结10min获得了具有优良微波介电性能的0.93MgTiO3-0.07CaTiO3陶瓷:εr=23,Qf=70000GHz。ZnAl2O4基陶瓷的烧结性通常很差,需要在很高的温度烧结(约1500℃)。Lorite等采用SPS法制备ZnAl2O4和0.79ZnAl2O4-0.21Mn2TiO4陶瓷,发现只需在1300℃烧结5min即可获得致密度不低于98%的烧结体。SPS法制备的陶瓷纤维组织都很均匀,且晶粒十分细小,ZnAl2O4和Mn2TiO4陶瓷单相结构性能与传统方法相当或略高于传统方法,这是因为超短的加热时间抑制了第二相的产生。
相比传统方法,SPS技术在降低烧结温度和缩短烧结时间上效果十分显著,能有效抑制晶粒异常长大。但超快速的烧结过程容易导致材料的晶粒过于细小,这些都可能对材料的微波介电性能造成不良的影响。
4.反应烧结
反应烧结是指初始粉末间的化学反应和材料的致密化在同一加热过程中完成的一种烧结方法。该法无须常规方法中的预烧阶段,是获得高致密陶瓷的一种简单有效的方法。
Chang等通过将纳米BaTiO3和TiO2粉末直接反应烧结制备Ba2Ti9O20发现,采用高能球磨可显著提高粉末的烧结性能,获得相对密度大于96%的陶瓷所需的烧结温度(1200℃)较采用普通球磨低150℃,然而,无论采用哪种球磨方式的反应烧结,Qf值与传统固相烧结(Qf=32000GHz)相比都有不同程度的下降。但由于晶粒发育不完全,高能球磨烧结体的Qf值(Qf=10000GHz)较普通球磨(Qf=26000GHz)降低更明显。Lin等在Chang的研究基础上发现,增加预反应步骤(即反应烧结过程中在1000℃设置一个保温台阶)可促进主晶相的合成,且随着预反应时间的延长,烧结体异常长大的晶粒所占比例和尺寸都在减小,Ba2Ti9O20陶瓷的显微组织较没有预反应步骤烧结的陶瓷更加均匀,当预反应时间为6h时材料的Qf为29000GHz。由于BaTiO3和TiO2间复杂的反应过程容易导致化学组成不均匀,Lin等采用BaTi4O9和BaTi5O11为原料进行反应烧结,将Ba2Ti9O20的Qf值提高到36000GHz。
与常规方法相比,反应烧结具有两个明显的优点:无须预烧工艺;利用化学反应的自由能作为附加的烧结驱动力。但反应烧结过程不易控制,反应机制十分复杂,难以保证材料化学组成的均匀性,从而影响材料的微波介电性能。
2.4.5 微波介质陶瓷器件研究现状
微波介质陶瓷可以做成高Q值谐振器,若按设计要求将若干谐振器耦合在一起,即可制成一系列微波器件,如振荡器、滤波器、双工器、天线等。这类器件的特点是体积小、损耗低、稳定好、承受功率高、可在恶劣条件下工作,最高应用频率可达90GHz,不仅民用广泛,而且在军用通信中受到重视。这类陶瓷介质微波器件有分体和联体两种结构,前者是由几个谐振器耦合而成;后者是在一个陶瓷块体上制作几个谐振器及其间的耦合结构,使器件体积大大减小。Murata开发的用于CDMA的陶瓷介质双工器的体积为12.6mm×5.3mm×2.0mm,发射到天线的插损小于1.5dB,发射/接收间的隔离大于50dB,频带为1.8~2GHz。西门子研制的三级单块联体型微波介质陶瓷的尺寸为5.75mm×4.0mm×2.95mm,适用于个人手持系统(personal handyphone system,PHS)1900等移动通信产品。吴坚强设计了一种低损耗贴片式独块状的八级介质滤波器,该滤波器采用切比雪夫响应的方法设计,利用介电常数为45的高Q值独块状微波陶瓷制作,谐振器之间使用电容和电容加载耦合,制备出中心频率897.5MHz,插入损耗小于2.5dB的介质滤波器,可满足800~1500MHz频率范围内通信基站要求。风华高科推出针对4G基站滤波器用介质谐振器,具有损耗小、温度特性更优等特点,所制作的滤波器具有体积小、重量轻、数据传输速率高等优势,是目前解决LTE中文网络建设频谱资源瓶颈的关键器件。
20世纪90年代初,汽车用全球卫星定位系统(global position system,GPS)天线开始用相对介电常数为10~20的微波介质取代低介电常数的聚四氟乙烯材料。这种具有辐射电极和接地电极的平面型微带天线,通过同轴线与接收机相连接,安装在汽车车身外壳,外形尺寸为70mm×70mm×20mm。随着微波介质陶瓷、天线设计与制作技术的改进,GPS天线的尺寸已缩减为25mm×25mm×4mm、15mm×15mm×4mm,甚至缩减为9mm×9mm×4mm、12mm×6mm×4mm。由于GPS天线直接接收的卫星信号极其微弱,早期高介天线必须后置GaAs低噪声放大器(low noise amplifier,LNA)以及类似移动电话用的带通滤波器,改进型的低介天线增益系数提高,可省去LNA直接接入接收机,而使之从有源天线变成无源天线。
鞭状天线和螺旋状天线在移动电话中广泛使用,但由于体积较大,不能满足移动电话小型化的要求,已逐步被内置天线(片式介质天线和平面倒F天线)取代。片式介质天线具有宽带、低损耗、高辐射率、内置且易于集成等特点,成为研究的热点。Asgar和Moon等研究了用于个人通信服务(personal communication system,PCS),国际移动通信2000(international moblie telecom 2000,IMT2000)系统的片式介质天线。Murata已经研制出基于不同介质类型和不同Q值的多种片式介质天线,典型片式介质天线尺寸为10mm×4mm×2mm,频率为2GHz,带宽100~150MHz;改进后的超薄型天线尺寸缩小到6.0mm×4.6mm×1.8mm,可内置于个人计算机内存国际标准(personal computer memory card international assocition,PCMCIA)卡上。Toko公司新研制的DAC2450CT1型微波介质天线,适用于2.4GHz的W-LAN,外形尺寸ф16mm×9.7mm。片式介质蓝牙天线是专门为蓝牙技术配套的片式天线,尺寸为15mm×7mm×6mm,频率范围为2400~2500MHz,电压驻波比小于2,天线增益在水平面内很高,在垂直面较差,目前Murata公司达到100万只/月的产量规模。
Eeatern Wireless Telecomn开发了带阻滤波器,其中心频率为14250MHz,3dB带宽为2000MHz(最大值),从14000MHz到14250MHz的抑制度为50dB(最小值),插入损耗小于1dB,DC(直流)~12750MHz和15750~22000MHz时的驻波比是1.5dB。Integrated Microwave公司研制的陶瓷天线分离滤波器的工作频率为2.4GHz,通带带宽为10GHz,插入损耗为2.5dB,其10dB时的带宽为75MHz,TX/RX隔离度为22dB,该分离滤波器的每个通道均有两个极,可用来处理5W的载波。
国外厂商在微波介质器件市场占主导地位。微波介质陶瓷材料和器件生产水平以日本Murata、德国EPCOS公司、美国Trans-Tech公司、Narda Microwave-West公司、英国Morgan Electro Ceramics等公司最高。其产品的应用范围已在300MHz~40GHz系列化,年产值均达10亿美元以上。我国上海大学、天津大学、同济大学、浙江大学、厦门大学、电子科技大学、清华大学、中国电子科技集团公司第十三所和中国科学院上海硅酸盐研究所等也对微波介质陶瓷材料及元器件进行了研究。国内微波介质陶瓷及器件生产厂家主要有嘉兴佳利电子股份有限公司、潮州三环(集团)股份有限公司、景华电子有限责任公司、张家港璨勤电子元件有限公司、苏州捷嘉电子有限公司等,并实现了一定的生产规模。如嘉兴佳利电子的微波介质滤波器频率覆盖350~6000MHz共1500多个型号规格,可提供低插损小于1dB或带宽500MHz的高性能特殊要求介质滤波器,主要应用于基站、直放站、无线通信、Wimax、RFID、导航监控、雷达、航空航天等领域;微波介质双工器产品应用领域覆盖DCS、PCS、GSM、CDMA、W-CDMA、CDMA2000、GPS导航、北斗导航定位、军事雷达、航空航天等领域。但与国外厂商相比,在技术水平、产品种类和生产规模上差距比较大。