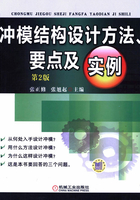
2.5 用典型组合标准设计连续式复合模
直接由板、条、带、卷料用多工位连续式复合模,一模成形冲制出形状复杂、尺寸与几何精度高、一致性好且互换性强、用其他加工办法根本无法加工的轻型结构零件,是目前大力推广应用的冲压技术。
与传统板料冲压技术相比,用多工位连续模及连续式复合模一模成形冲制的冲压零件,不仅使用冲模数量大幅减少,生产率成倍增长,更主要的是比传统的分序多模冲制的冲压零件质量好,工艺流程短,耗用人力物力少,占用机床及生产面积少,操作安全又便于实现冲压过程的机械化与自动化,且生产成本大幅下降,故各种连续模的应用日趋广泛。
2.5.1 连续模及其结构特点
通常按冲模冲压工序(步)的组合程度和方式,将普通全钢冲模分为:单工序冲模(亦称单冲模)、连续模、复合模三大类。随着模具市场的开放,这种简单的冲模分类法,已不适应冲模及其零部件作为商品参与市场流通的需要;难以准确计算制模工时,无法确定准确制模周期;不能确定各方认同的冲模造价,无法对冲模进行造价概算、预算及最终决算,给冲模供销合同签约及实施造成困难。冲模分类的细化已势在必行。在生产现场,冲模的分类多数是在上述简单分类法的基础上,结合冲模完成冲压工艺作业性质给予分类和命名的。单工序冲模可分为冲孔模、落料模、弯曲模、拉深模、翻边模等;在连续模中,用于冲孔—落料的连续模称连续冲裁模,进行冲孔多次拉深—落料的冲模称连续拉深模等;对于复合模,如果只是冲孔、落料复合冲裁则称为复合冲裁模,而对落料拉深又冲孔的复合模,才称为拉深复合模。这种分类法虽进了一步,但未能表明冲模结构形式、工位数目以及主要工艺技术功能。
众所周知,在机械压力机滑块的一次冲压行程中,在多个工位上完成多个不同而连续冲压工步的连续模,具有与单工序冲模和单工位复合模完全不同的工艺技术功能与结构特点。
1)绝大部分连续模都采用有搭边排样,进行有废料冲裁,而且搭边宽度比相当单工序冲模和复合模的冲压零件排样搭边要稍大一些。
2)无论使用条、带、卷材等哪一种原材料冲压,也不管采用手工送料还是自动送料,操作者都只能在模具工作区之外操作,故连续模操作安全性好。
3)连续模要不间断冲压,便于实现冲压过程的机械化与自动化。
4)连续模均设有良好的送料定位系统,能保证各工位对送进材料或半成品准确定位,确保冲压零件质量高,互换性强。连续模的定位系统通常采用以下几种方式:
①固定挡料定位系统。由固定挡料销(定位板)加始用挡料装置构成定位系统,多用于料厚t>1mm零件,五工位以下的连续模,定位精度较低,送进误差≥±0.3mm。
②侧刃切边定位系统。由数量不等、不同截面形状与结构的定距侧刃,配或不配侧压装置构成的侧刃切边定位系统,多用于料厚t≤1mm的薄料多工位连续冲压,定位精度较高,送进误差≤±0.15mm。
③导正校准定位系统。由导正销、导正凸模、专设工艺定位孔配导正销等装置,对送料进距进行校准精确定位,通常与固定挡料系统或侧刃切边定位系统配合,构成成套精准定位系统,可使送进误差≤±0.04mm。
5)连续模工位间送料方式,即模内各工位送进方式是结构设计的重要组成部分,通常采用如下几种方式:
①直送法。原材料入模,自动或手动直接送到各工位。这种方法适用于具有群孔的冲裁件,采用分工位冲裁,最后组合在一个工位上落料为成品冲压零件。各工位无直接关系,如冲孔、冲槽孔……落料。连续冲裁模多属于工位少、形状简单的冲压零件用连续模。
②携带法。形状复杂、具有细小长悬臂的冲压零件采用连续模冲压,多采用分次冲去结构废料或搭边的方法,将工件留在条料上,用送进原材料携带工件至各工位连续冲压,最后工位切断或落料出件;另一种方法是冲孔、整体落料,将落料工件从凹模中顶回,嵌入到原材料搭边框内,用送进原材料携带至下一工位成形。上述分切式与嵌入式携带法,只适用于连续模诸工位都在同一平面且沿送料方向直线排列,否则便不能实施。
③传递法。需要长弯边、多向弯曲及拉深、翻边成形的冲压零件,当采用连续模冲制时,冲压零件弯曲或拉深成形,需要有较大冲压工作空间,需要整体落料的展开毛坯,从冲孔后落料的凹模洞口下推出,由专用楔传动推送机构,推送毛坯到下一工位成形。如果展开毛坯由专用落料模提供,则可用楔—料斗—滑板的送料装置,用料推料的方法,将料斗下漏出的毛坯,逐件推送至各工位,进行连续冲压。上述推送与料推料两种传递法,都需要专用送料系统。特别是推送传递法,其冲模的各工位布局不仅不在一个平面上,而且总体呈L形。这类冲模均属自动或半自动冲模。
6)连续模要连续不间断冲压,所用冲压设备都比计算的和间断冲压需要的公称压力大1倍左右,为的是防止在连续不间断冲压中,冲压设备输出压力与功因其飞轮转速下降而减小,从而影响正常冲压工作。冲模为适应连续冲压,也应该采用加强型模架(导柱加粗、上下模座加厚),以防其承载后产生过大弹性变形,长期工作而出现疲劳变形与裂纹等损坏。
2.5.2 连续模与连续式复合模的结构类型
冲制板料立体形冲压零件的连续模,不仅有冲孔、切断、落料等冲裁工位,而且还有各种不同的成形工位,如弯曲、翻边、扳边、拉深、压波、压印等;有一些连续模还具有复合冲裁或综合式复合冲压作业,如冲孔翻边、落料拉深或切断弯曲等复合冲压工位。对于在不同工位上进行分离与变形作业的连续模和具有复合冲裁、复合冲压工位的连续模,按照德国工程师协会(VDI)编辑出版的《技术准则手册》中的定义、说明及举例,都应称之为连续式复合模。
连续模在我国的相关标准与资料中,命名都不统一,有的称跳步模、级进模,也有的称顺序模、程序模等,称连续模较为科学也贴近实际。近年来,连续模、连续式复合模这种名称已逐步为有关方面认同。
常用的连续模按其导向与卸料方式、工艺技术功能不同,有以下几种结构类型:
1)无导向固定卸料结构连续冲裁模。
2)无导向固定卸料结构连续式复合模。
上述两种连续模,用于冲制简单形状的平板冲裁件、圆形与方形拉深件、预冲孔翻边件等,一般不超过三个工位,结构也简单。这类冲模在现场生产中采用较多,其典型结构组合曾纳入机械行业标准,即原JB/T 8065.1、2—1995。
3)滑动导向导柱模架固定卸料结构连续冲裁模与连续复合模。
4)滑动导向导柱模架弹压卸料结构连续冲裁模与连续复合模。
5)滑动导向导柱模架弹压卸料导板式连续冲裁模与连续复合模。
6)固定卸料导板式连续冲裁模与连续复合模。
上述3)~6)四种连续模是现场生产中使用广泛的连续模。其典型结构组合曾纳入机械行业标准,即原JB/T 8065.3、4—1995,原JB/T 8066.1、2—1995及原JB/T 8068.1~4—1995。上述3)~5)采用各种结构形式的滑动导向导柱模架,均可换用滚动导向滚珠导柱模架,再派生出三种高精度连续模结构形式。
上述3)~4)连续模的结构形式,在生产现场使用较多。其中,滑动导向导柱模架固定卸料结构连续冲裁模与连续复合模使用尤为广泛。前面已列举了图2-13~图2-16等多套应用实例,可供参考。
滑动导向导柱模架弹压卸料导板式连续冲裁模与连续复合模,是用于冲制薄料与超薄料,即冲压材料厚度t为0.05~1mm的高精度、复杂形状冲压零件用冲模的主要结构类型。
固定卸料导板式连续冲裁模与连续复合模,主要用于料厚t>0.2~6mm的小型金属板冲压零件,特别是一些小尺寸、复杂形状的冲压零件,见图2-11、图2-12。
2.5.3 用典型组合标准设计连续式复合模
1.滑动导向导柱模架弹压卸料导板式结构连续式复合模
多数连续式复合模比连续冲裁模工位数多,结构也复杂。一模成形冲制各种立体成形件的多工位连续式复合模,除必须拥有冲裁工件展开毛坯的各种冲裁工位外,还必须依成形冲制的工艺需要,设置多个成形工位,往往一个不太复杂的立体成形件,也要三个以上工位才能实现一模成形。而连续冲裁模多数用二或三工位即可完成,超过五工位的连续冲裁模较少。
实例1
图2-17所示卡环冲压零件七工位连续复合模,是小型仪表零件冲压常用的滑动导向后侧导柱模架弹压卸料导板式连续复合模。其主要结构特点如下:
1)直接用带料一模成形冲出立体形卡环零件,配备通用送料装置,可以全自动连续冲压,不仅生产率高,而且操作安全性好,操作者劳动强度小。
2)冲压工步安排为:冲矩形孔、切口、弯U形、空挡、有芯弯圆、折弯、切断七个工位。第Ⅳ工位空挡是为了拉开第Ⅲ、第Ⅴ工位距离;否则,因工件尺寸小而凸模、凹模尺寸大,安装到固定板上没有足够的位置,甚至要相碰,装不上去。切断前折弯30°是为了达到工件尺寸要求。七工位均在同一凹模框表面沿送料方向排布,结构紧凑。
3)除采用加强型模架提高模具整体刚度外,还使用加厚弹压导板,以利于对细长小凸模的横向大面积支承,冲压过程中凸模不会发生纵弯折断。
4)采用高精度Ⅰ级导柱模架,模具工作零件按IT7制造。
5)采用典型结构组合标准设计(原JB/T 8066.1、2—1995)。由于该冲压零件尺寸小,选用横向送料结构形式为宜。
6)第Ⅴ工位有芯弯圆的弯芯横向动作机构属非标准部件,要专门设计。
2.滑动导向导柱模架固定卸料横向送进连续式复合模
这类结构的连续式复合模在用条、带、卷料一模成形连续冲制一般精度的小型复杂形状冲压零件中,应用十分广泛。图2-18~图2-21所示为由原材料通过冲裁,切去废料获得展开毛坯后,用不同变形作业,包括:扳边、多向弯曲及拉深等,冲出形状复杂的立体成形零件。
图2-17 卡环零件弹压卸料导板式七工位连续复合模
1—固定板 2—凹模板 3—卸料板 4—导套 5—导柱 6—冲矩形孔凸模 7—凸模固定板 8—垫板 9—上模座 10—模柄 11—弯曲芯子 12—角形摆杆 13—压簧 14—切断凸模 15—压形凸模 16—弯圆凸模 17—弯曲凸模 18—切槽口凹模孔
实例2
图2-18中所示仪表底盘形状复杂,需要对35mm×24mm的矩形框的三边一次扳出,拐角R=3mm,相当于矩形盒浅拉深成形。两个35mm矩形长边上各有两个R2mm(即Φ4mm)的半圆凸耳。绘出其展开平毛坯图形状,与冲压零件形状近似,见排样图Ⅱ工位所示。
该冲压零件排样图设计为三个工位。第Ⅰ工位仅冲出两个斜槽孔,确定扳边与尾部平板连接部位,限制扳边长度35mm,并依靠对称布置的两个凹形切边侧刃,在第Ⅰ工位切除原材料一定宽度的料边,精确定位。第Ⅱ工位用切开而不分离的冲裁方法,切出冲压零件要扳边的展开毛坯轮廓,与Ⅰ工位冲出的两上斜槽孔连通。同时,还冲出冲压零件平板尾部的两个1.5mm×5mm的矩形孔。第Ⅲ工位是个综合式复合冲压工位:无扳边尾部外廓落料与原材料分离、扳边成形、冲26mm×19mm矩形孔等,三工步在一个工位上完成。
在结构设计上,要充分考虑到冲模必备的专用技术功能和连续冲压的需要。
1)设置双边成对侧刃切边定位,确保各工位送进误差≤±0.15mm。
2)各工位在同一凹模表面,沿送料方向呈直线布置,用送进原材料携带工件至各工位简单方便。
图2-18 底板滑动导向对角导柱钢模架固定卸料横向送进三工位连续式复合模
1—垫板 2—销钉 3—顶件器 4—冲孔凸模 5—卸料器 6—弹簧 7—落料凸模 8—冲口凸模 9—切开凸模 10—冲矩形孔凸模 11—侧刃 12—凹模
3)第Ⅲ工位用压边拉深的方法实施外缘扳边。压边靠下弹顶器(顶件器)加压,扳边后冲26mm×19mm矩形孔,是在行程末尾,用装在下模该工位中心的冲孔凸模,向上反向冲孔。依靠装在冲孔凹模洞口中的弹性卸料器,将冲孔废料顶出并落在工位表面,可与同时由下模顶件器顶出的成品冲压零件一并由送进材料携带出模。
4)第Ⅱ工位切开冲压零件扳边部位展开毛坯后,需要反顶回原搭边框中,故在Ⅱ工位切开凹模洞口中装有顶件器。
5)冲压零件扳边后的最大高度为10mm。为使压边拉深向上扳边,具有更大作业空间,使Ⅲ工位下模顶出工件,不碰撞卸料板下表面,并利于顺畅出件,除加厚导料板之外,还在Ⅲ工位卸料板下表面开挖一个凹口,以增大作业高度;改用紧固卸料板的埋入式圆柱头内六角螺钉,为外露的六角螺钉,使局部减薄的卸料板仍可安全夹紧固定。
6)按典型组合标准给定的尺寸规格,选配滑动导向对角导柱钢模架。
实例3
图2-19所示为仪表壳底滑动导向钢模架固定卸料横向送进四工位连续式复合模。该冲模的连续冲压工艺工步及冲模结构虽与图2-18颇为相似,但有一些值得汲取的独到之处。
图2-19 仪表壳底滑动导向钢模架固定卸料横向送进四工位连续式复合模
1—销钉 2—六角螺钉 3、8—卸料板 4—下模座 5—弹簧 6、17—内孔弯边凸模 7—顶件器 9—切断凸模 10—弯边凸模 11—固定板 12—成形侧刃 13—压筋凸模 14—冲矩形孔凸模 15—导料板(加厚的) 16—凹模
1)采用了非标准的成形侧刃。该侧刃切除条料的长度L等于送料进距S,而侧刃内侧冲裁出冲压零件展开毛坯的部分外廓。这种侧刃除具有普通常规侧刃节制送料控制进距的作用外,还具有切除沿边与结构废料的冲裁凸模作用,是一模成形多工位连续模经常采用的一种非标准、双重作用的侧边凸模。其设计方法同单边剪切的冲裁凸模,但仍须保证与匹配凹模在冲裁刃口上具有合理间隙。
2)最后工位配备切断刀,将经冲孔、空挡工位、压筋并弯曲成形复合冲压的工件从条料上切断分离开。成形工件顺切断凹模旁的落件坡,滑落入零件箱。
3)卸料板的结构形式与紧固件的选用与图2-18完全相同。
实例4
图2-20所示芯夹四工位连续式复合模,是一模成形冲制小型复杂形状立体成形零件较为典型的冲模结构。
图2-20 芯夹滑动导向导柱模架固定卸料、横向送料四工位连续式复合模
1—卸料板 2—弯曲成形凸模 3—凸模 4—成形侧刃 5—凹模 6—顶杆 7—预弯曲凹模 8—预弯凹模弹顶垫 9—弹簧
(1)冲压加工难点 对该冲压零件进行工艺分析可知,其冲压加工难点在于以下几点:
1)其展开毛坯具有对称的细长悬臂,长近15mm、宽3mm,而料厚t=0.6mm,很容易弯扭变形,尤其在将展开毛坯送入最后成形工位之前,故平稳送进非常重要。
2)直接冲裁展开毛坯的一对细长悬臂,不仅凸模极易损坏,寿命低,而且毛坯因料薄难免扭曲而推不出凹模。
3)冲裁间隙很小,单边间隙为0.012~0.024mm,要保证冲裁刃口都具有均匀一致的冲裁间隙,有一定制模难度。尤其在宽度仅2~3mm、长达15mm的矩形断面悬臂凸模上,两边刃口如此小的间隙都要同样均匀,制模要求过高,制造难度大。
4)如何在一对悬臂部位弯曲成形为封闭的空心方环形,弯成形后又如何从凸模上完好卸下,是该冲模结构设计的关键问题之一。
5)对这种多向弯曲成形的复杂形状立体形冲压零件,若要实现连续冲压一模成形,就必须设计出合理的冲压工艺工序,并用合理的冲模结构作保障。
(2)排样图设计采取的技术措施
1)按冲压零件展开平毛坯图,见图2-20排样图Ⅱ工位图形,采用单列直排,用裁搭边法获取展开毛坯。冲压零件展开毛坯有一对悬臂细长落料,结构废料很宽大,用裁搭边法切除结构废料,留下工件与条料连接,便于用送料携带送进。冲切去结构废料,面积大、形状简单,凸、凹模刃口均易制造。
2)用成形侧刃冲切去展开毛坯两悬臂头部,使冲模结构进一步简化。
3)切断分离与最终成形在一个工位完成,使成形不受相连工位及条料拉扯的影响。
(3)冲模结构设计的主要特点
1)按选定典型组合的标准规格,配备滑动导向对角导柱Ⅰ级高精度钢模架。
2)在Ⅳ工位切断弯曲成形之前的第Ⅲ工位,进行预弯成形,见图2-20中B—B剖视图。
3)将导料板加厚以增大模具工作区高度,满足弯形需要。
4)减薄卸料板,改用六角螺钉紧固。
5)弯曲成形凹模洞口做一个台阶止口,冲压零件弯曲成形并包在凸模上,穿过台阶止口后,因脱离模腔,会产生回弹而使冲压零件口部稍稍张开,待凸模回程后会被台阶止口卸下而掉入模下零件箱。
实例5
图2-21所示为扣盖滑动导向对角导柱钢模架固定卸料横向送进三工位连续式复合模。其冲压工艺与冲模结构都具有典型性与实用性。这种小型浅拉深成形件虽精度要求不高,但其成形,尤其连续冲压一模成形,容易出现拉深时底角部裂口、断裂或口部起皱,以及凸腰成形过浅、过深使裂口以及整体形状歪扭等疵病,造成次品或废品。其冲压工艺及冲模结构设计采取了如下技术措施:
1)采用大搭边、有工艺切口拉深,使拉深凸腰成形复合冲压(第Ⅱ工位)过程中的材料流动不受相连原材料牵扯带来的阻力影响,确保成形达到要求。
2)在拉深凹模弹顶垫内装可伸缩导正销。在拉深之前,导正销先插入到第Ⅰ工位冲制的两个圆孔中,对送入第Ⅱ工位的材料进距进行微调校准,以确保冲压零件成形外廓与孔的同轴度。
3)为保证压凸腰与拉深成形的相对高度,拉深与压凸腰用凸模采用分体镶嵌结构,保持恒定的高度差。
4)为使成形工位和第Ⅲ工位有足够的成形与送料携带工件的工作空间,可加厚导料板,适当减薄卸料板,并采用外露六角螺钉紧固。
图2-21 扣盖滑动导向对角导柱钢模架固定卸料横向送进三工位连续式复合模
1—六角螺钉 2—卸料板 3—下模座 4—导柱 5—导套 6—上模座 7—凸模镶套 8—固定销 9—拉深压腰凸模 10—冲孔凸模 11—工艺切口凸模 12—凹模 13—侧刃 14—销钉 15—弹簧 16—橡胶体 17—弹顶垫
5)采用单边矩形侧刃对送进条料切边定位,以保证各工位送料进距精度。
3.采用典型组合标准设计连续复合模的注意事项
从图2-17~图2-21的冲模结构设计实例中,可以得出以下结论:
1)选用典型组合标准设计法进行冲模结构设计,只限于曾纳入机械行业标准的四大类14种结构形式。
2)典型组合标准仅对模芯以外的零部件,如配用模架,按规格成套的螺钉、销钉这类的紧固件,垫板及限位柱等,给定了类型、材料、尺寸规格等,给予标准化;对支承与安装及主要工作零件,如卸料板、固定板、导料板、凹模等按标准规格配备成套,给定了外廓尺寸,与凸、凹模刃口,模腔等匹配模孔与相关尺寸,应另绘出加工图,故仅进行半标准化。
3)模芯即模具工作部分(凸模、凹模、凸凹模及相关零件),包括凸模固定板、导板、卸料板的模孔、顶件器、卸料(件)器及整套机构等都必须依照冲压零件图、冲压零件展开平毛坯图、冲压工艺排样图等进行设计。
4)典型组合标准中没涉及冲模的送料定位系统,必须按冲压工艺排样图与选定的典型结构类型进行设计。
5)典型组合标准中大都没有考虑冲模的安全防护机构及装置,设计中按需要和使用习惯,在模具工作区之外安装防护栅、防护屏或光、声、电感应防护系统,确保操作安全。
6)对于冲模的主要工作零件加固结构、镶拼结构、快换组合结构等,典型组合标准中均不涉及,都应由设计者按需要设计。
7)选用典型组合标准设计冲模,必须进行以下必要的计算:①多工位连续模和复杂形状大、中型单工序冲模的压力中心;②细长小孔凸模、冲深孔凸模的抗压强度、抗纵弯刚度验算;③冲压力计算及合理冲压设备类型及公称压力的确定;④查阅GB/T 16743—2010《冲裁间隙》,计算合理间隙值;⑤计算冲模刃口、模腔尺寸,并选定制造精度等级;⑥核定冲模的主要技术规格及匹配设备安装尺寸。
8)冲模的矩形凹模周界一般为L×B=315mm×250mm。对于固定卸料导板式冲模许用最大凹模周界还要小一些,为L×B=280mm×160mm,连续模与连续式复合模的凹模多为矩形。当凹模周界超越上述许用范围时可设计非标准冲模结构。
9)有一些形状复杂、尺寸较大,以及需要横向冲压、诸工位不能在同一凹模平面沿送料方向呈直线布置的连续式复合模,附带有送料与卸(出)件机构的自动或半自动连续式复合模,均不能采用或不能完全采用典型结构组合标准。