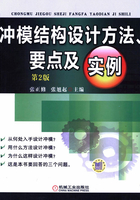
2.4 选用典型组合标准设计法
2.4.1 相关标准中的典型结构组合
1)原JB/T 8065.1—1995《冷冲模固定卸料典型组合 无导柱纵向送料典型组合》。
2)原JB/T 8065.2—1995《冷冲模固定卸料典型组合 无导柱横向送料典型组合》。
3)原JB/T 8065.3—1995《冷冲模固定卸料典型组合 纵向送料典型组合》。
4)原JB/T 8065.4—1995《冷冲模固定卸料典型组合 横向送料典型组合》。
5)原JB/T 8066.1—1995《冷冲模弹压卸料典型组合 纵向送料典型组合》。
6)原JB/T 8066.2—1995《冷冲模弹压卸料典型组合 横向送料典型组合》。
7)原JB/T 8067.1—1995《冷冲模复合模典型组合 矩形厚凹模典型组合》。
8)原JB/T 8067.2—1995《冷冲模复合模典型组合 矩形薄凹模典型组合》。
9)原JB/T 8067.3—1995《冷冲模复合模典型组合 圆形厚凹模典型组合》。
10)原JB/T 8067.4—1995《冷冲模复合模典型组合 圆形薄凹模典型组合》。
11)原JB/T 8068.1—1995《冷冲模导板模典型组合 纵向送料典型组合》。
12)原JB/T 8068.2—1995《冷冲模导板模典型组合 横向送料典型组合》。
13)原JB/T 8068.3—1995《冷冲模导板模典型组合 弹压纵向送料典型组合》。
14)原JB/T 8068.4—1995《冷冲模导板模典型组合 弹压横向送料典型组合》。
上述原机械行业标准的四大类14种冲模典型结构组合,每种均由多组规格可供设计选用。每种规格的成组配套零部件,均为标准件和半标准件,可以随时在就近模具市场按要求购买。
2.4.2 设计步骤
1.确定冲模结构类型
冲模结构选型的主要依据如下所述:
(1)冲压零件加工图样 其中,主要参数是:材料种类及料厚、尺寸及其精度、技术要求,以及经工艺分析后的冲压加工难点。
(2)冲压零件的工艺文件 包括:工艺流程图、工艺过程卡、工艺设计与计算书及说明、冲模设计任务书等。
(3)初步选择冲模的类型与结构 根据上述图样、工艺文件,针对冲压工艺需要,按冲模设计任务书要求,在前述的14种冲模典型结构组合标准中,初步选择冲模的类型与结构。
(4)对比确定。在初步选定冲模类型的过程中,应经过以下几方面的对比后确定。
1)冲模要不要导向装置及使用何种导向装置。如果不要导向装置,根据冲压零件工艺要求、生产批量以及尺寸精度,可以用无导向冲模冲制,则只有两种典型组合标准供选用,即原JB/T 8065.1—1995《冷冲模固定卸料典型组合 无导柱纵向送料典型组合》、原JB/T 8065.2—1995《冷冲模固定卸料典型组合 无导柱横向送料典型组合》,两种各33个规格可供设计选用。
如果必须具有导向装置,有导板导向、导柱导套导向及导板与导柱导套组合导向三种结构形式供选择。
使用导板导向的冲模是指固定卸料导板式冲模,通常推荐可冲裁料厚t为0.6~6mm,最大冲裁件尺寸不大于200mm,冲压精度低于IT10。冲模体积小,结构紧凑,操作安全,冲压噪声小。
使用导柱导套导向的冲模,通常指用滑动导向导柱模架,有固定卸料或弹压卸料的各种结构形式的冲模,冲裁料厚t为0.05~16mm,最大冲裁件尺寸一般不大于250mm,最高冲压精度为IT10~IT14,使用广泛。
所谓导板与导柱模架组合导向的冲模,是指滑动导向导柱模架弹压卸料导板式结构高精度冲模。这种结构的冲模可冲制薄料、超薄料高精度冲压零件,如料厚t为0.05~<0.5mm的超薄料高精度冲压零件的冲制,也可以对厚料冲裁及光洁冲孔加工,包括冲孔直径d≤t及d≥0.4mm的深孔与小孔冲制。
2)冲模的导向装置与结构类型。用导板导向的固定卸料导板式冲模,可选用典型组合标准是:原JB/T8068.1—1995《冷冲模导板模典型组合 纵向送料典型组合》、原JB/T8068.2—1995《冷冲模导板模典型组合 横向送料典型组合》,两种各17个规格,共34个规格可供选用。
用滑动导向导柱模架的冲模,有以下8种结构形式的典型组合标准可供选用:①原JB/T 8065.3—1995《冷冲模固定卸料典型组合 纵向送料典型组合》、原JB/T 8065.4—1995《冷冲模固定卸料典型组合 横向送料典型组合》,两种各33个规格,共66个规格可供选用;②原JB/T 8066.1—1995《冷冲模弹压卸料典型组合 纵向送料典型组合》、原JB/T 8066.2—1995《冷冲模弹压卸料典型组合 横向送料典型组合》,两种各33个规格,共66个规格可供选用;③原JB/T 8067.1—1995《冷冲模复合模典型结构 矩形厚凹模典型组合》、原JB/T 8067.2—1995《冷冲模复合模典型结构 矩形薄凹模典型组合》,两种各33个规格,共66个规格可供选用;④原JB/T 8067.3—1995《冷冲模复合模典型结构 圆形厚凹模典型组合》、原JB/T 8067.4—1995《冷冲模复合模典型结构 圆形薄凹模典型组合》,两种各33个规格,共66个规格可供选用。
用导板与导柱模架组合导向的滑动导向导柱模架、弹压卸料导板式冲模,有两种结构形式可供选择,即原JB/T 8068.3—1995《冷冲模导板模典型结构 弹压纵向送料典型组合》、原JB/T 8068.4—1995《冷冲模导板模典型结构 弹压横向送料典型组合》,两种各18个规格,共36个规格可供设计选用。
3)确定使用卸料方式。典型组合标准中,有弹压卸料、固定卸料两种方式,都使卸料板强制从凸模上卸下板料。弹压卸料板是校平板料后冲裁,工件不会拱弯而较平整,而且卸料是用弹性元件逐渐施压柔性卸料,不产生冲击噪声,一般用于t≤1mm的薄料,以及弹性大、原本有轧制圆弧及需要校平后冲裁而获取较高尺寸精度的冲裁件。
固定卸料属于刚性冲击卸料,大多数用固定卸料板,而且固定卸料块、卸料钩等是大尺寸、厚料冲裁中经常采用的卸料装置。固定卸料的冲压零件,会产生拱弯并伴随有较大的弹性变形和冲击噪声。t>1mm料厚的平板冲裁件,尤其是t>3mm的中厚板冲裁件,以及精度不高的、1mm以上料厚的薄板冲裁件也常采用固定卸料。卸料板结构简单,造价也低,使用可靠。
4)确定使用模架的结构形式及精度等级。需要配用模架的所有典型组合标准中,没有规定配用模架类型及其结构形式,只规定了每个规格配用模架的最小闭合高度与最大闭合高度。通常情况下,所有需配模架的典型组合均为普通全钢冲模,除另有注明和特殊需要外,都配用不同精度等级的滑动导向导柱模架。至于何种冲模结构典型组合,配何种结构形式的模架,均由冲模设计人员根据需要确定。冲压零件的工艺尺寸及精度,以及由其冲压工艺确定的排样图设定的凹模周界,是确定选用模架规格及精度的主要因素。对于料厚t≤0.5mm的薄料与超薄料冲裁件,为确保上模芯对下模芯,尤其是小孔、深孔凸模对准其匹配凹模的导向,一般都选用I级精度,甚至超过I级精度,选O级高精度模架。
模架结构形式的选择,主要与工艺排样及其确定的送料方式、送料方向有关,模具附带送料机构的安装位置、横向冲压机构所需楔传动系统的安装位置与空间等,不得与模架导向零部件碰撞。此外,要考虑冲模能平稳运作。
2.确定已选定典型结构的标准规格
选择合适规格,就是确定冲模的整体尺寸及其主要零部件尺寸及规格。
选定典型组合标准规格的依据如下:
1)冲裁零件的最大外廓尺寸:长×宽(L件×B件)、直径(D件)。
2)考虑搭边、沿边、凹模壁厚、导料板及侧刃等零件安装尺寸,计算出所需的凹模周界:长×宽(L×B)、直径(D)。
3)冲压零件的冲压工艺过程及排样图。根据冲压零件图、排样图,以及选定的冲模典型组合标准规定的标准模具图,便可方便地计算出冲模的凹模周界,即凹模在下模座上许用安装的平面外廓尺寸L×B或D。有时,考虑在凹模表面安装挡料销、始用挡料装置、挡料板、防护栅(屏)等,会对计算的L×B或D值稍加调整后确定。
按照最终确定的凹模周界尺寸,查相应典型组合标准,即获得其标准规格及成套标准零部件的编号、名称、数量、选用标准号及其具体尺寸。
3.绘制非标准及半标准零部件加工图
通常非标准零件主要是凸模、凹模、凸凹模、非标准成形侧刃;半标准件指待加工模孔的凸模固定板、固定卸料板、凹模板、导板、顶件器、卸料块,以待加工漏件(废料)孔的下模座和待加工安装孔的上模座打料推卸系统等。
冲压零件不同,冲压工艺各异,选用的冲模典型结构组合标准也不同,故需要绘制的非标准及半标准零部件加工图也完全不同。
(1)设计单工序冲模
1)非标准零部件图:非圆断面冲孔与落料凸模,弯曲、拉深、翻边、压波、打凸、压印、压花、冲挤及体积冲压等成形作业单工序冲模的凸模与凹模,顶件器、防护栅(屏)、附设的自动或半自动送料、出件机构成套零部件。
2)半标准零部件:与凸模匹配的凹模板、凸模固定板、卸料板、导板的模孔、限位柱、定距套、弹性元件(弹簧、橡胶块)。
(2)设计多工位连续模 除与上述单工序冲模相同的非标准零部件、半标准零部件外,视所设计冲模需要配套,绘制加工图。所不同的是,连续模所需单工位冲裁、各种成形凸、凹模,顶(卸)件器,都是按工位成套设计。同时,连续冲裁模的凸模固定板、卸料板(导板)、凹模板大多为整体式结构,如需镶拼也多采用整体或组合镶块嵌装在凹模框内,故均可依一个整体考虑上述“三板”,即凸模固定板、卸料板(导板)、凹模板的统一基准的尺寸标注、与凸模配合精度等级,甚至可三板叠齐,一次由电火花线切割加工出凹模孔后,再分别按配合要求、间隙大小进行精加工。
有成形工位的连续式复合模,尤其需进行横向冲压的连续式复合模,成形工位如落料后弯曲、冲孔与落料后拉深等,这些工位均需按非标准设计。
(3)设计复合模。原JB/T 8067.1~4—1995给出了四种复合模典型结构;均为倒装式结构形式。在选定冷冲模复合模典型结构组合标准及指定规格之后,还需要绘制如下零部件加工图:
1)非标准零部件:异形凸模、凹模、凸凹模、顶(卸)件器、推卸顶杆与推板。
2)半标准零部件:与凸模、凸凹模匹配的凹模板、卸料板、固定板等。
绘制非标准与半标准零部件加工图,必须按冲压零件材料种类及力学性能、料厚等要素,查GB/T 16743—2010《冲裁间隙》,结合冲压零件使用功能要求,合理确定冲裁间隙,再计算出冲模刃口与模腔制造尺寸与公差。根据冲模主要工作零件尺寸,按冲模结构与功能需要,确定其他结构零部件、定位系统零部件、推卸系统零部件,以及附设的送料、出件机构零部件尺寸与公差。
4.绘制冲模总装配图
根据选定典型组合标准示图和已计算出的工艺数据,已绘出的非标准、半标准零部件图,结合排样图,确定冲模的压力中心、凹模的定位及检测基准面,复核并纠正冲压工艺计算中的遗漏与失误,再着手绘制冲模的总装配图。
在冲模总装图绘制好后,在该图显著位置写明冲模的主要技术规格与制造技术要求。
5.提高设计质量的措施
为了更好地应用典型组合标准设计法并提高设计质量,应采取如下措施:
1)事先编制《冲模设计与制造守则》,规定设计与制模流程,设计应完成的工作及达到的要求,规定采用标准及冲模结构形式、可预制的标准与半标准零部件,规定制模、总装、试模、验收、投产的工艺流程与验收标准。该手册发放至设计与制模工艺人员手中,并集中培训、学习、宣贯,并认真执行。
2)强化设计程序及各程序交接方式,确保设计、校对、标准检查、审核、批准各程序,并有纠正记录和书面意见。
3)冲模主要零部件、辅助机构及横向冲压系统等应有设计说明书与设计计算书。
2.4.3 无导向固定卸料冲模结构设计
这类冲模的典型结构组合标准,按送料方向分两种:无导柱纵向送料与横向送料,两种典型组合的构成完全相同,详见原JB/T 8065.1—1995、原JB/T 8065.2—1995。
实例1
图2-6所示为一套小型平板冲压零件无导向固定卸料落料模。冲压零件的基本形状及其排样图均在其冲模总装图的俯视图上表示清楚。排样图设计考虑冲压零件细长而尺寸又小,采用交错单列反身冲裁有搭边排样,设间隔两个模位,一次落料两件。既将两模孔间距拉大,提高了凹模强度,也减少了结构废料,提高了板材利用率。
该冲模采用纵向送料形式,用矩形侧刃节制送进原材料的进距。侧刃的切边长度等于送料进距。送料时可以将条料(带料)贴着凹模表面连续送入,进行不间断冲压,生产率较高。
实例2
图2-7所示为孔板无导向固定卸料二工位连续冲裁模。该冲模采用横向送料形式。与图2-6冲模不同,它采用由始用挡料装置与固定挡料销、导正销配套,构成其送料定位系统,送进原材料至各工位定位。不仅保证每个工位送料进距准确,还要保证冲孔与落料具有良好的同轴度。始用挡料装置亦称临时挡料销,控制每根条料首件先冲孔而后落料,使每根条料首件不会出现不冲孔就落料而产生废品。因为冲压零件的长度L=100mm,使用条料宽度达103mm,为使送进条料不产生偏斜,故采用两个固定挡料销。送料时,条料必须抬起越过固定挡料销,用待落料的搭边,挡在固定挡料销右边挡料圆柱面上,限距定位。落料凸模上的导正销在上模下行时,先插入在第一工位冲出两圆孔中,对送进条料精确校准定位,消除两个工位可能出现的同轴度误差后,进行落料。
这类冲模大多采用板裁条料冲压,条料长度大多在500~2000mm之间,每换一条新料都必须使用一次,由手压推出的始用挡料装置,为其首件第一工位送料进距定位。此后每冲裁一件,都必须抬起条料送进,并使送进条料挡在固定挡料销一侧,才能开始冲压。因此,使用这类冲模多用手动送料。当安装专用钩式送料装置后,也可实现连续自动冲压,而条料首件仍要使用手动的始用挡料装置。
图2-6 小型平板冲压零件无导向固定卸料落料模
1—导料板 2、4、15、18—螺钉 3、12、14、20—销钉 5—下模座 6—凹模 7—承料板 8—卸料板 9—固定板 10—垫板 11—模柄 13—上模座 16、22—侧刃 17—凸模 19—导料板 21—侧刃挡块
选用典型组合标准设计无导向固定卸料纵向送料或横向送料结构的冲模时,其关键步骤及应注意的事项如下:
1)设计前应对冲压零件进行充分的工艺分析,要着重于加工图样要求的尺寸精度、几何精度及允许的塌角与毛刺大小等要求,给予特别关注。
2)由于这类无导向冲模,其冲压精度较低,一般为1T12~IT14。如果使用冲压设备动态精度高,其冲压零件精度会稍高一些,但不会高于1T11。料厚t<1mm的薄料不适于采用这类冲模冲制。
3)由于这类冲模冲压时,上模对准下模,主要依靠使用压力机的滑块导轨对滑块的导向精度,以及滑块行程对压力机工作台表面的垂直度等,使凸、凹模对准度误差一般为0.10~0.15mm,老式及超期服役的C形机架开式压力机,动态精度更低,使凸模对准凹模的误差更大。因此,这类冲模的刃磨寿命及使用(总)寿命都偏低。
图2-7 孔板无导向固定卸料二工位连续冲裁模
1—导正销 2—螺钉 3—落料凸模 4—模柄 5—上模座 6—销钉 7—垫板 8—固定板 9—卸料板 10—导料板 11—承料板 12—凹模 13—下模座 14—导料板 15—始用挡料装置
4)这类冲模无安全防护装置及相关机构,是全钢冲模中操作安全性较差的,操作中必须多加小心。如果在模具上加设防护栅(屏)就好多了。
设计时应特别注意的几个关键环节:
(1)确定搭边与沿边宽度 按照冲压零件图或其展开毛坯图设计排样图,确定其冲压工艺工步,并按其材料种类、供应状态,校核和查对其搭边、沿边宽度;结合采用的送料方式,节制进料系统设置,确定挡料搭边强度、搭边框在挡料送进过程中的刚度。注意不要因搭边过小而在冲压过程中产生变形,甚至拉入凹模洞口,影响生产。
(2)确定凹模周界 对冲裁模而言,按排样图给定的搭边与沿边宽度及落料凹模洞口、冲孔凹模洞口的工位与边距,再依冲压零件图或展开毛坯图的尺寸,确定凹模上表面如下几个关键尺寸:
1)冲裁模孔的设计壁厚tm及允许最小壁厚tmin。通常情况下,主要通过查阅手册资料或用常规强度计算法,确定冲裁模孔间壁厚tm值,只要tm>tmin即可。如果tm≤tmin,必须采取强化措施或增加空挡工位,加大tm值。
2)冲裁模孔距凹模边缘的最小厚度tmin。一般取经验数据,不用计算。因为在多数情况下,在套用标准规格之后,这个数值总要放大许多,最后选定的凹模尺寸,其模孔刃口的边距值tn,总是比允许的tn值大得多。因为凹模周界的标准规格是按一定而且是较大的间隔设定的,选择时还可依需要放大tn值,故可不考虑。
3)紧固孔与模孔刃口间允许最小壁厚Gmin。典型组合标准中,已充分考虑了各种规格的紧固螺钉孔、销钉孔的合适间距,以及这些紧固孔与凹模板边缘的合适边距。只要选用规格的凹模周界,配备的成套导料板构成的导料槽,适合冲压零件排样图的料宽或稍宽一些,均可保证其紧固孔与模孔刃间的壁厚G>Gmin值而不必多虑。
根据上述方法确凹模板的尺寸:长×宽,再查阅标准规格系列,就高弃低,确定凹模周界Lm×Bm值。
(3)冲模的送料定位系统的构成及设计 典型组合标准件没有给定冲模送料定位系统,必须在选定典型组合的规格之后,按冲压工艺及其排样图的实际需要,设计送料定位系统。
无导向固定卸料结构冲模的送料定位系统构成如下:
1)无导向固定卸料结构单工序冲模的送料定位系统。这类冲模无论是分离还是成形作业,只有一个工位,大多采用固定的定位板、挡料板、挡料销,对送进材料、半成品进行限位或挡料定位。
除定位板、成形挡料板,需依冲压零件或半成品定位部位外形进行设计外,其他定位装置,如各种形状的固定挡料销、不同安装位置及不同结构类型的活动挡料销等,均为标准零部件,可按冲压零件料厚、尺寸大小及需要选用。
2)无导向固定卸料多工位连续模的送料定位系统。这类冲模一般为2~3个工位,很少有超过5个工位的。其定位系统构成有如下几种:
①固定挡料销。条料入模的首件第一工位,用目测定位。第二工位及以后连续送进,均用固定挡料销,多为手工送料。
②固定挡料销配始用挡料装置。这种定位系统构成使用较广。超过两工位,每增一个工位再加一组始用挡料装置,多用板裁条料,手工送进。
③固定挡料销加始用挡料装置配导正销。这种定位系统在这类连续模中使用最广。导正销一般装在落料凸模端面,以提高冲压零件内孔与外廓的同轴度。
④侧刃配或不配侧压装置。对料厚t≤1mm的薄料、超薄料冲压零件,进距小而送料精度要求较高,又要连续不间断冲压的、小尺寸冲压零件用的连续模,多采用这种送料定位系统。侧刃可按需要选用带导头或不带导头的不同断面形状的各种规格。对于t≤1mm的冲压零件,推荐用带导向头侧刃的连续模。
(4)成形工位的设计。这类连续模也有各种成形作业工位,如浅拉深、弯角不大的弯形、翻边及压印、打凸等。通常均按单工序成形模结构设计,但其推卸系统都尽量简单,而且靠反顶实现模上送料携带出件,要求加厚导料板,以增大模具变形与出件需要空间。
(5)技术参数的选择、计算 首先核定冲压工艺确定的冲压力、冲压功及选定冲压设备的正确性与合理性,而后依冲压零件材料及其抗剪强度,查阅GB/T 16743—2010《冲裁间隙》,确定冲裁间隙,计算凸、凹模刃口及模腔尺寸,考虑冲模总刃磨量;计算冲模的压力中心,计算合理凸模长度并与标准规格比对,考虑加固凸模的必要性。
(6)工作零件的强度校核 选定典型组合的标准规格后,标准中就给定了模具闭合高度Hm、凸模长度L凸。按照标准规格给定的配套零件,设计确定采用的送料定位系统构成的零部件及有关工艺参数,即可绘制冲模总装图。
在按照规定标准比例绘图,通常为1∶1、1∶2等。绘图过程中,可进一步核实配套零部件与相关技术规格的正确性。
如有必要,还可校核凸模强度、刚度及凹模板抗弯强度。
2.4.4 固定卸料导板式冲模结构设计
这类冲模的标准典型结构,与无导向固定卸料结构冲模标准典型结构大同小异。从两者整体结构及其构成对比分析,主要差别如下:
1)有和无导向的差别。固定卸料导板式冲模将固定卸料板变成导板并兼有卸料功能,使冲模的冲压精度及使用寿命都比固定卸料无导向结构冲模提高一个档次。
2)操作安全性的差别。在滑块行程可调的压力机上,选用合适的行程,用固定卸料导板式冲模冲压,确保凸模不脱离导板模孔,又有下模表面的限位柱控制上模下行位置,操作工人的手进入不到模具工作区,即便无意接触到或伸到下模表面,也压不住手指,其操作安全性是众多普通全钢冲模中最好的。而固定卸料无导向结构冲模属于敞开式冲模;工作时凸模会脱开卸料板,操作工人的手若有意无意进入冲模工作区会诱发人身伤害事故。
3)安装调校要求不同。通常情况下,固定卸料无导向结构冲模对安装调校的要求很高,一般要求经验丰富、技术水平高的专业调整工,承担其在压力机上的安装、试模、调校。直到冲出合格冲压零件,才交付操作工生产。而固定卸料导板式冲模,因为有导板和限位柱的支承,一般操作工可以方便地将其安装在压力机上工作。
4)推广应用前景大不相同。据现场调研统计分析,多数冲压过程中的压手断指事故,都是因为使用无导向敞开式冲模和手工送料入模所致,特别是使用无导向固定卸料结构冲模,在开式曲轴压力机上冲压,由于滑块行程大而又不可调,冲模开启后,凸模离开卸料板在模具工作区形成一个很大的开启无防护空间,很易诱发事故。为确保安全生产,这类冲模本身应装设防护栅(屏)或在有安全防护的压力机上使用。迄今,多数采用国产中小型机械压力机的企业,大都不在冲模上装防护装置,怕操作工不习惯、妨碍操作;在压力机上安装安全防护装置,多数工厂则还无能力或不具备条件。在这种情况下,推广应用固定卸料导板式冲模势在必行,推广前景广阔;无导向敞开式冲模则面临淘汰。
冲模固定卸料导板式冲模的典型组合标准结构见图2-8、图2-9,与冲模固定卸料无导柱的典型组合标准结构相比,仅多了一对限位柱。前者的导板即后者的卸料板,但导板模孔与匹配凸模按基孔制h5/H6~h7/H8配合制造,单边导向间隙≤0.01mm,属于无间隙或微间隙滑配合;而卸料板模孔与凸模之间的单边卸料间隙一般取冲压零件料厚t的10%~50%,即(0.1~0.5)t,甚至更大,其卸料间隙绝对值一般为>0.1mm。
固定卸料导板式冲模通常所采用的定位系统及其构成、节制送料方法,以及所有定位装置的标准零部件、标准紧固件、标准弹性元性等,都与固定卸料无导柱结构冲模完全一样。其选用典型组合标准设计法,也基本相同。
选用典型结构组合标准设计法,对于一些形状简单,需要工位数不多,尤其是各种类型平板冲裁零件,用固定卸料导板式连续模,设计与制造十分方便。对于比较复杂的连续模,要根据冲压零件的冲压工艺及其排样图的需要与要求,对其特殊的成形工位进行专门设计。
在每种典型结构组合标准中,除规定冲模结构形式外,还给定了一定适用范围的、成套系列规格,每一个规格都给定了构成该指定结构形式的、成套标准与半标准零部件及其匹配尺寸,如模板尺寸、螺钉与销钉规格,每一标准规格冲模的主要技术规格:凹模周界L×B、凸模长度L凸、模具闭合高度H等。这非常有利于计算机辅助冲模CAD系统的构建。只要将各典型结构组合标准、给定的冲模结构形式、各标准规格构成零部件尺寸系列,分别存入图形库与数据库,然后应用参数化技术,就可方便地用选用典型组合标准法,设计给定的各种典型结构组合类冲模了。
图2-8 固定卸料导板式冲模纵向送料典型组合(摘自原JB/T 8068.1—1995)
1—垫板 2—固定板 3—上模座 4—导料板 5—凹模 6—承料板 7—导板 8—下模座 9、10—销钉 11、12、13—内六角螺钉 14—圆柱头螺钉 15—限位柱
实例1
图2-10所示固定卸料导板式落料模,是标准的固定卸料导板式纵向送料冲裁模一类的通用典型结构,除凸模外,全部为标准件和半标准。如果以选用典型组合标准设计法设计,则十分简便。
(1)确定设计冲模的结构类型并选用典型组合标准
1)根据冲压零件图进行工艺分析。确认冲压零件的材料种类及其供应状态,冲压零件的形状、尺寸、料厚、要求冲压尺寸与几何精度等。经工艺分析找出冲压加工难点及其对冲压加工的适应性。
图2-9 固定卸料导板式冲模横向送料典型组合(摘自原JB/T 8068.2—1995)
1—垫板 2—固定板 3—上模座 4—导料板 5—凹模 6—承料板 7—导板 8—下模座 9、10—销钉 11、12、13—内六角螺钉 14—圆柱头螺钉 15—限位柱
2)按照冲压零件的全套工艺文件及排样图、冲模设计任务书的要求,确定所设计冲模的冲压工艺作业工序及要完成的冲压加工任务。
3)选定冲模结构类型、结构形式及其相应典型组合标准。
(2)确定冲模的凹模周界长×宽(L×B) 根据该冲压零件及其排样图,考虑凹模刃口距凹模相应部位合理边距,以及导料板的宽度,在保证凹模刃口与最近紧固孔有合理壁厚的情况下,可估算出凹模的L×B尺寸,为套用、选定标准规格提供依据。
(3)确定送料方向 选用纵向送料还是横向送料,要考虑现场操作工人的操作习惯和工作舒适度。大多数工厂的冲压工,在冲制中、小尺寸冲压零件时,喜欢靠近压力机工作台正面,以便不伸腿只需抬脚即可控制脚踏开关和操作压力机。不仅可以坐在工作椅上,轻松操作,而且可使手、脚配合准确,不易疲劳,不会发生配合失误,出现误操作。在这种情况下,采用横向送料形式的冲模结构更合适。
对于料厚较大,使用条料又宽,而且进距又大的平板冲裁件,由于整条料很重,横向单手送料吃力,时间长了易疲劳。在需要站着操作或两人合作操作压力机等情况下,应选用纵向送料的冲模结构形式。
图2-10 固定卸料导板式落料模
1—下模座 2、4—销钉 3—导板 5—固定挡料销 6—凸模 7、15、16—螺钉 8—上模座 9—模柄 10—垫板 11—固定板 12—限位柱 13—导料板 14—凹模
(4)选定标准规格 根据选用典型组合标准,按需要凹模尺寸估算凹模周界L×B,依据就高弃低的原则,选定合适标准规格。
(5)结构计算及强度校核 根据选定典型结构的标准规格及其成套零部件尺寸,进行必要的结构计算。
1)冲模的压力中心的计算。
2)凸模、凹模的刃口尺寸的计算。在计算刃口尺寸之前,先按冲压零件材料种类及其抗剪强度、料厚等参数,查GB/T16743—2010《冲裁间隙》,确定冲裁间隙C(单边)值。
如采用电加工制模工艺,并先制凹模,可仅计算凹模刃口尺寸而后配制凸模,如先制凸模则相反。通常对落料凹模,都根据冲压零件尺寸及其公差先算好凹模刃口尺寸。
3)导板、固定板模孔尺寸的计算。计算前先按冲裁件尺寸,对照选定标准,给定凸模长度L凸,设计出凸模加工图;然后选定导板模孔与凸模刃口段配合精度等级,凸模固定段与其固定板模孔配合等级,查阅有关公差配合资料,进行计算。
如有必要,可对凸模、凹模的抗压强度及抗弯刚度进行常规校核。
实例2
图2-11所示为德国一仪表厂在生产中使用的一套固定卸料导板式连续冲裁模。这种冲模在国内通称导板模,源于德国,至今在德国仍广泛使用。
图2-11 仪表底板冲裁件固定卸料导板式连续冲裁模
1—垫板 2—上模座 3—模柄 4—冲矩形孔凸模 5、13、19、20—螺钉 6—限位柱 7—凸模固定板 8—落料凸模 9、10—冲圆孔凸模 11—导板 12—固定挡料销 14—下模座 15—导料板 16—承料板 17—凹模 18—销钉
图2-11中仪表底板冲裁件(H68黄铜)的料厚t=1.5mm,有较高的尺寸精度要求。由于该平板冲裁件只有三个内孔,最小的两个孔直径为Φ3mm,其孔边距B=1.5mm=t,十分薄弱。选择固定卸料导板式连续冲裁模,分两工位冲制,先冲孔而后落料,而且三个孔,可分工步冲出,保证冲孔凹模具有更大的壁厚、更高的强度,从而使冲模达到更高的寿命。结构定型而又简单的固定卸料导板式连续模的标准化程度达80%以上,其零部件商品率不低于75%,需要按加工图样作为非标准零部件加工的,只有冲矩形孔的凸模及凹模板、导板及凸模固定板三模板上的模孔,需要叠齐后用电火花线切割一次加工出来。其他所有标准零部件,全可就近市场购得。因此,制模费用低而制模周期更短。
该工件的排样采用单列直排,取搭边a与沿边a1的宽度相等,即a=a1=2mm。由于工件为近似矩形,在两个90°斜对角内各有一个Φ3mm的孔,孔边距为1.5mm=t。工件中的宽×长为4mm×8mm的矩形孔,虽然其边距和与Φ3mm圆孔的孔间距都是2mm,但其沿矩形孔宽4mm边长均为2mm壁厚,亦显得较为薄弱。因此,连续冲裁排样图设计采用先冲4mm×8mm矩形孔,接着冲两个Φ3mm的孔,最后落料。考虑有一个冲Φ3mm的凹模孔,距落料凹模太近,计算此处的凹模壁厚≤(1.5+2)mm=2.5mm,对于t=1.5mm的工件来说,连续冲压时3.5mm厚的刃口,两面同时受到较大的冲裁压力,很易磨损和损坏。故在两工步之间即落料之前,加一个空挡工位,把凹模加长,凹模刃口壁加厚一个进距S=14mm。由于矩形孔大而且又在两圆孔中间,故先冲矩形孔,便可消除矩形孔凹模刃口距两个Φ3mm圆孔和工件外廓落料刃口过近、间距过小的缺点。同时,利用矩形孔挡料定位和对送料进距限位,省去了始用挡料装置和落料工位挡料销,简化了结构。最后排样为四工位,详见图2-11中排样图。这便是该冲模结构设计巧妙之处。
实例3
图2-12所示环夹固定卸料导板式七工位连续复合模,是一套结构较复杂的小型立体成形件连续冲压一模成形的典型实例。
当选用典型结构组合标准设计法设计这类冲模时,要在模芯部分的设计上,注意处理好以下几个关键环节:
(1)工艺分析 对冲压零件的工艺分析要细致、到位。这类小型立体形冲压零件一般尺寸精度要求不高,关键在于如何冲压成形,如何从模具上推卸出冲好的工件,而又不损伤工件,寻找出冲压加工的难点与重点,以及连续冲压的可行性与不可行性。
应该对冲压零件的冲压加工适应性进行细致分析,对上述诸问题逐个解决,工艺分析到位,为冲压工艺编制、冲压工艺过程及冲模结构设计奠定基础。
(2)排样图设计 排样图设计是重要环节。在冲压工艺过程设计中,常常要经过多个工艺方案的对比选优。一旦确定冲压工艺流程和具体方案,就用设计出的排样图表示出用连续冲压的方法及一模成形的各工步与工位。因此,排样图是连续模结构设计的重要依据。
图2-12中所示排样图明确表示出以下各点:
1)原材料宽度为48.5mm。
2)总计工位为七个,而冲压工步数为5个,有两个空挡工位。
3)冲压工步及其排列为:
第一工位冲两个Φ10.5mm圆孔,为第一冲压工步。
第二工位冲去夹环中间7mm×5mm连接带的四周废料,为第二工步。
第三工位切开夹环两个Φ20mm外圆,留着中间7mm×5mm连接带,以便用送进原材料携带工件到以下各工位冲压,为第三工步。
第四工位为空挡。
第五工位弯形,为第四工步。
第六工位为空挡。
第七工位切断分离并将其推卸出模,为第五工步。
图2-12 环夹固定卸料导板式七工位连续复合模
1、27—侧刃挡块 2、26—侧刃 3—承料板 4、42—导料板 5—弹顶垫 6、9、13、30、34、38—螺钉 7、19、24、36—垫板 8—凹模 10、31、39—防护栅 11、35—固定板 12、37—上模座 14、15、16、17—冲孔、冲裁凸模 18—模柄 20—弯曲上模 21—切断凸模 22—导板 23—凹模框 25—下模座 28—拼块 29、41—销钉 32—冲裁凹模拼块 33—切开凸模 40—限位块 43—切断凹模拼块
4)送料定位系统,由双边错开布置的两组矩形侧刃组构成。
5)侧刃切除原材料料边宽度为(48.5mm-47mm)÷2=0.75mm。
6)送料进距S=21.5mm。
7)搭边宽度a=21.5mm-20mm=1.5mm。
8)沿边宽度a1=(47mm-45mm)÷2=1mm。
9)在模具送料入口,冲模导料槽尺寸即两导料板间距B导=48.5mm+0.1mm=48.6mm。
10)冲模承料板沿送料方向长度L承≥(2~3)S=43~64.5mm。
(3)凹模的结构形式选择及设计 连续模制造多采用主凹模制造工艺技术,即先制造凹模,凸模按凹模配制。由于连续模的凹模有多工位凹模孔、模腔构成的凹模板,而众多凸模是以工步(工位)逐个与凹模匹配的。因此,凹模的设计,特别是各工位的刃口、模腔的尺寸计算与标注十分繁琐而要求严格。
该冲模的凹模采用冲裁与成形分割拼合的结构形式。第四工位以前采用整体拼合,第五至七工位采用按工位镶拼组合。前者考虑第三工位切开部位,要用下部弹顶垫将切开工件部位反向顶回原搭边框中,以便送料携带;后者则考虑弯曲及推卸成品工件需要较大空间。
(4)确定凹模周界L×B 根据排样图所示料宽、工位数、进距S及侧刃断面尺寸,估计导料板的宽度,可以初定凹模周界L×B。而后选择送料方向,便可查阅选定典型结构组合的相应标准,按估算凹模周界,就高弃低,选定标准规格。
2.4.5 导柱模架固定卸料纵向或横向送料冲模结构设计
这类冲模按原JB/T 8065.3—1995、原JB/T 8065.4—1995的规定,是配用模架的,而且绝大多数配用滑动导向导柱模架。因此,这类冲模的结构全称应为滑动导向导柱模架固定卸料纵向或横向送料结构冲模。由于连续模在这类使用甚广的冲模结构设计中,具有代表性与典型性,故选择各种有特色且经生产考验过的、滑动导向导柱模架连续冲裁应用实例,说明选用典型组合标准设计法、设计这类冲模的过程及其结构设计的关键环节和应注意的事项。
1.纵向送料结构形式的冲模设计
图2-13所示为开关接线板对角导柱模架固定卸料纵向送料连续冲裁模。该冲模依选用典型组合标准设计法设计,可以按凹模周界估算值选定标准规格、凹模周界尺寸(长×宽,L×B)的数据、图2-13俯视图中所示的两工位冲裁模排样图,考虑条料宽度,加上两导料板宽度,即可大致算出所需凹模宽度。在计算所需凹模长度时,应先计算出冲模的压力中心,这是由冲压零件形状决定的,如这样细长脚、直角形冲压零件,其重心位置必然偏移在工件外,二工步三工位冲压力合拼后的压力中心,会在两工步之间。确定压力中心后,再考虑落料凹模刃口的合理边距,保证凹模在压力中心两边长度相当,即可大致确定凹模需要最小长度Lmin。按估算凹模周界选定标准规格,只能将L×B放大,不能减小。
该冲模的结构设计在以下几方面均为典型组合标准规定以外,必须由设计人员构思、设想、设计的。
(1)冲模的送料定位系统 为节省金属材料并提高凹模强度,该冲压零件虽只需冲孔、落料两个工步,但因料头特大而搭边较小、进距S也较小、群孔与外廓要保证较好同轴度,故应保证送料进距偏差要尽量小;同时,只有拉开冲孔凹模刃口与落料凹模刃口的距离,才能加大凹模刃口壁厚增加其强度。因此,在落料与冲孔两工步间加一个空挡工位,变成三工位两工步连续冲裁。为保证送料精度,采用侧刃切边定位,控制送料进距,另配侧压装置,使送入条料不偏斜。于是,该冲模的送料定位系统由一组矩形侧刃与侧刃挡块组件、侧压装置部件构成。送料的进距S精度可达±0.15mm,甚至更小。
(2)加固细长小凸模 该冲压零件料厚t=2.5mm,要冲5个Φ3mm小孔,凸模细长,应予加固。通常是将小凸模杆部按(1.8~2)d(冲孔直径)加粗成二台阶式凸模,如需将杆部再加粗成为三台阶凸模,则固定段即第三台阶可按(3.5~4)d加粗。无论细长小凸模加固成二台阶或三台阶,其刃口工作段长度以(5~7)d为宜。如有必要,对凸模的抗压强度与抗纵弯刚度进行校核。
(3)小凸模的卸料板导向 为保护小凸模承载后不产生纵弯折断,可将加固后的凸模杆部,接近其刃口工作段,插入加厚的卸料板匹配模孔中,并采用微间隙滑配合,在凸模冲孔承载时对凸模杆部有一个可靠的横向支承。
图2-13 开关接线板对角导柱模架固定卸料纵向送料连续冲裁模
1、8—导料板 2、25—侧压装置 3、7—导柱 4、6—下模座 5、13、21—螺钉 9—卸料板 10—固定板 11—导套 12—上模座 14—凸模 15—模柄 16、20、24—销钉 17—冲孔凸模 18、23—侧刃 19—垫板 22—侧刃挡块 26—承料板
2.横向送料结构形式的冲模设计
图2-14、图2-15所示两套对角导柱模架固定卸料连续冲裁模与图2-13结构不同,为横向送料结构形式,而且送料定位系统是由固定挡料销配多个始用挡料装置构成,结构上具有一定特点与典型性。
由于典型组合标准中,依凹模周界L×B的尺寸选定标准规格,并以不同规格分别给定成套标准及半标准零部件及其类型、尺寸、材料和热处理硬度。而凹模周界L×B的尺寸系列,均来自标准模板半标准件,其紧固孔、模孔要按选用典型组合标准的具体规格,加工紧固孔;模孔则按设计的加工图另行加工。
图2-14 扣板对角导柱模架固定卸料横向送料连续冲裁模
1、25—导料板 2、4、16、27—螺钉 3、9、19、22、28—销钉 5—始用挡料装置 6—下模座 7、11—导柱 8、13、24—卸料板 10—凹模 12—固定挡料销 14—导套 15—上模座 17—凸模 18—模柄 20—冲孔凸模 21—垫板 23—固定板 26—承料板
标准模板的尺寸系列,如矩形凹模板的长度×宽度(L×B)即凹模周界,其尺寸系列都是以为基数,再乘以公比1.25获得尺寸系列。标准矩形凹模板尺寸系列见表2-1。
标准给定的凹模周界L×B使相邻两规格间有较大的尺寸间隔,有时其凹模周界在结构设计中,因加设标准以外的辅助装置后,就显得不够合适。在这种情况下,可按需要设计凹模板,而不必受标准制约。但标准给定其他配套零部件,仍可参照选用。
图2-15 垫片对角导柱模架固定卸料横向送料连续冲裁模
1、5、15、21、25—螺钉 2、23—导料板 3、26—销钉 4、10—下模座 6—始用挡料装置 7、12—导柱 8、11—固定挡料销 9、22—卸料板 13—导套 14—上模座 16—凸模 17—模柄 18—垫板 19—冲孔凸模 20—固定板 24—承料板 27—凹模
表2-1 标准矩形凹模板尺寸系列
图2-16所示为锁垫对角导柱模架固定卸料横向送料四工位连续冲裁模。该冲压零件形状复杂,尺寸精度要求较高,而且零件材料为强度大、硬度高的合金结构钢(弹簧钢)65Mn。
图2-16 锁垫对角导柱模架固定卸料横向送料四工位连续冲裁模
1—固定板 2—垫板 3—冲孔凸模 4—上模座 5—模柄 6—凸模 7—卸料板 8—导柱 9—搭边框 10—凹模 11—侧刃挡块 12—始用挡料装置 13—侧刃 14—下模座 15—侧压装置
对冲压零件进行工艺分析可知,采用分序多模冲制,不仅生产率低,关键是达不到冲压零件尺寸与几何精度要求,特别是群孔、群槽孔与外廓的同轴度,(20±0.05)mm的孔距等,较难保证。同时,冲压零件的一致性及互换性差,会给产品装配带来困难。采用复合冲裁模冲制,冲压零件的精度及互换性都可达到更高水平,满足技术要求。但由于群孔直径d为Φ5mm,长槽凹口宽仅5mm,长达25mm,两槽口间壁厚也仅5mm,而且是三个槽口并排,这给复合冲裁模结构设计与制造都会带来难以克服的困难,复合模寿命无法保证。用多工位连续冲裁模冲制,不仅生产率高,而且工件一致性好,互换性强。唯一不足是,冲压精度不易保证。为此,该冲模的结构设计采用如下措施:
1)用侧刃切口控制送料进距,控制送料进距S=41mm±0.15mm。
2)设导正销校准送料进距,S=41mm±0.04mm。
3)设侧压装置使送进带料紧靠导料板导向一侧。
4)控制入模带料宽度为600-0.6mm。