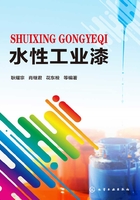
2.2 乳液聚合物的合成
1909年德国Bayer公司的Hofmann公布了烯类单体在水乳液中进行聚合的专利[14],尽管聚合的方法类似于悬浮聚合,这份专利被认为是最早乳液聚合相关的文献。乳液聚合从第一份专利已到现在经发展100多年,传统的乳液聚合过程采用间歇式反应器,甚至现今大量的产品仍然采用间歇式反应设备,连续法的设备和工艺条件会相对复杂,只在部分的产品中使用。在1961年,Gershberg和Longfield首次提出连续搅拌釜式反应器的模型(CSTR),该模型基于Simth-Ewart Case2理论模型[15]。
乳液聚合过程的影响因素可以从两个方面去考虑,聚合机理和工艺过程;聚合机理是从高分子化学、胶体化学、物理化学等方面的研究乳液聚合过程,这些机理决定了乳液配方的基本设计和工艺过程参数的设定;工艺过程影响是指实际生产过程的影响因素,原料、设备和工艺控制这三个方面的影响。在乳液聚合配方和工艺参数确定以后,工艺过程就成为对于产品的影响的主要因素,并且在乳液聚合过程中实现工艺过程的稳定性是比较困难得,这是由于乳液聚合不是单纯的高分子聚合物过程,是在胶体粒子内部进行的聚合过程,影响乳液聚合的因素不仅仅是高分子聚合方面的因素,还涉及胶体形成和界面的影响,乳液聚合中粒子形成、自由基进入粒子的过程受到自由基聚合和界面化学两个方面机理的影响。
保证乳液聚合物不同批次之间的均一性会比较困难,黏度、粒径等存在一定范围的差异,聚合物性能的参数上也会有不同,例如,润湿性、聚合物分子量分布、吸水率等。一些使用领域对于乳液聚合物性能的要求范围较宽,较小的差异是可以被接受;但是在工业防护涂料、纸张涂料、高速涂布或粘接等领域,聚合物乳液批次之间的波动有时会导致最终的涂料等在使用时会出现缺陷或问题。
乳液聚合的工艺过程控制始终让工程师和生产管理人员感到困惑,产品性能会被许多因素影响,出现次品或性能波动的情况很难避免,例如,原料中阻聚剂的浓度微小的变化都会影响到乳液聚合过程的成核,从而导致产品最终的黏度和粒径发生变化,影响产品的性能。
尽管乳液聚合理论发展了近100多年,有了诸多的理论和书籍,但是开发一个新的产品或遇到产品质量波动时,还是需要有足够的经验,可以说乳液聚合是一种“艺术”。尽管实验室产品的乳液聚合过程具有良好的稳定性和重复性,但是小试产品在放大时性能出现偏差是一个常见的问题,甚至有时使用性能变得很差,例如,放大过程中出现大量的凝胶或在反应釜中凝聚,有的产品的外观、粒径、黏度都没有偏差,但是使用性能却比小试的样品差了很多。在实际的生产中,有的产品配方只有在特定的反应釜才能完成,更换反应釜就会有差异。这些现象往往被看作乳液聚合过程经验的部分,很难准确分析原因并加以预防、控制。聚合物乳液的制备对于设备的依赖性很强,这是由于聚合物乳液胶体特性的影响,设备的不同会极大地影响聚合物粒子的形成与合并融合的过程,从而导致聚合物乳液产品的波动与差异。从技术的角度来看,这些问题的原因最终都能够准确找到。这些研究需要花费大量的人力、财力和时间,是乳液聚合物制造商的发展战略来决定是否投入。
聚合物乳液对于减少VOC的排放有着积极的意义,深入的研究乳液聚合的机理,有利于新的产品的开发,提高水性产品的性能,加快溶剂型涂料、黏合剂水性化的进程。乳液聚合的研究需要从乳液聚合过程和聚合物乳液应用的两个方面着手,聚合物过程的研究能够提高乳液聚合物胶体粒子形态设计、聚合物性能调整、生产工艺控制水平,聚合物乳液应用研究有利于掌握聚合物乳液胶体粒子的应用机理、优化使用性能、扩展使用领域;应用的研究对于聚合物乳液的设计也有积极的指导作用,同时应用研究对于其他聚合物胶体使用也具有参考意义。
乳液聚合属于高分子化学或材料专业,乳液聚合作为高分子合成方式的一个分支,一般在研究生阶段才能全面学,乳液聚合通常分类在高分子专业,早期的乳液聚合书籍是从高分子的角度,在聚合物的特点、乳液聚合数学模型、聚合物的使用等方面篇幅较多,在聚合物乳液胶体化学的部分篇幅一般较少;在乳化剂的选择主要从亲水和亲油的HLB和聚合物的极性来考虑,没有将乳化剂的选择与乳液聚合的粒子形成、增长的机理相结合。1997年有Lovell 和EL-Aasser合编《Emulsion polymerization and emulsion polymers》[16]的内容相对全面,尤其在成核、成膜机理等的章节。
要全面地了解乳液聚合以及聚合物乳液,需要从胶体化学和高分子化学两个领域来理解,才能知道乳液聚合过程存在着怎样的复杂性,从胶体角度比较系统阐述乳液聚合是Fitch的《colloid polymer》[17]。在乳液聚合过程中,粒子稳定性是一个动态的过程,粒子的形成、增长、碰撞和融合的过程中,粒子的界面面积、界面能(界面张力)始终在变化,是一能量不断变化的胶体体系。粒子的增长和单体的扩散速率相关,因此在聚合物乳液生产过程中,从制备乳化液开始就会影响最后聚合物的性能,乳化液滴的大小会影响单体的扩散速度,进而影响粒子的增长速度,影响粒子的表面大小和界面张力的变化。
乳液聚合工艺过程中的每一个因素都会带来不同效果的“蝴蝶效应”,要研究清楚其中的关联,需要制造商持续不断的投入资金深入研究问题原因和寻找解决方案,一些国际公司研究从20世纪70年代左右开始,至今未停止,而且更加细致和深入。乳液聚合机理在高分子化学和胶体化学的交叉区域,因此分析问题的原因往往很烦琐,这就需要在聚合物乳液合成和应用领域的工程师,更深入的了解胶体化学和高分子化学的理论。
工业乳液聚合过程的粒子增长过程符合以下基本原则:①乳液聚合过程不断有新的粒子形成;②聚合物乳液的粒子增长方式是单体进入聚合物粒子持续发生聚合反应,和粒子的碰撞融合同时存在;③如果粒子的稳定性很好,包括新生粒子的稳定性很好,粒子的数目就会不断得增加,粒子的总表面积就不断增加,所需要的表面活性剂就非常大,才能保证粒子的稳定。粒子的表面能增加,必然会导致粒子的碰撞融合开始增多,无论表面活性剂用量多少,粒子的融合一定会发生,因为粒子与水相的界面的变化,需要乳化剂快速的吸附来降低界面张力,乳化剂的扩散和吸附需要时间,尽管这个时间很短,但是粒子的表面能仍然会快速增加,从而导致粒子的融合,粒径增加,剧烈的碰撞融合过程就会产生凝胶颗粒。因此在乳液聚合生产配方中,仅仅增加乳化剂的用量并不意味着能提高粒子的稳定性。从热力学角度看,由于粒子的融合碰撞减少了表面积,减少了总的表面能,从而保证了胶体的稳定性,因此合理控制粒子的凝聚可以获得稳定的聚合过程。
控制粒子的形成和碰撞融合过程的平衡,才能获得最终的胶体稳定性,了解乳液聚合的机理,有助于提高粒子稳定性的控制,图2-2描述了聚合开始以后,新粒子形成以后的碰撞融合的过程。

图2-2 粒子形成过程与凝聚过程
乳液许多的性能从表面看与表面活性剂有关,调整表面活性的种类和用量,从而获得需要的乳液聚合物性能。但是微观的情况是,引发剂水相反应阶段的水相低聚物(water oligomer, 缩写WO)是具有表面活性结构,WO与表面活性剂的相互作用和竞争吸附会影响乳液粒子的形成、稳定、增长,形成稳定的新粒子与粒子碰撞融合之间的平衡是保证成熟粒子数目与粒子稳定性的基本原则。碰撞融合也是提高成熟粒子稳定性的一种方法,曹同玉[18]等研究ST和MMA无皂乳液聚合,张茂根[19]等研究了BA与MMA无皂乳液聚合,解释了初始粒子碰撞融合的增长过程。在乳液聚合的配方设计时,采用极性相似和HLB原则选择乳化剂的种类和用量,没有考虑粒子的动态过程—粒子的形成、增长、凝聚,因此不总是能的实现预期的目标。
本章对于乳液聚合机理的介绍会偏重于胶体的角度,从水相自由基的形成起点,将聚合机理和实际的应用结合,对于胶体的成膜过程也做了基础的介绍。