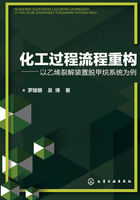
第2章 背景分析
在满足工艺和操作约束的条件下,为了实现设备的产量和能耗的最优配比,化工过程的系统应处于最优操作条件和最佳设计状态。同时,为了实现设备在整个生命周期内的节能高效运行,希望在全周期内都能够实现设备的最佳设计与最佳操作。由于实际过程中存在着各种不确定的因素,经常导致系统的操作条件或者设备的结构参数偏离最优值,甚至出现设备的停车。因此,需要在工业设备的运行过程中对其进行改造设计,识别出制约系统产品分离及用能的薄弱环节并加以改造,实现设备运行状态的最佳化。无论是否对设备进行改造,长期的运行会致使设备的稳态工作点发生变化,过程操作偏离稳态最优点,需要实施运行中操作条件的再优化。
传统工业设备的改造设计和操作条件的再优化往往是分开、分步进行的,且设备改造多采用离线分析的方法实现设备的分析。首先由化工工程师基于稳态模型和稳态设计方法,利用化工模拟软件建立稳态计算模型,并求解出设备的结构参数,得到最佳的设备改造设计方案。在工艺改造完成后由控制工程师以此为被控对象,设计配套的控制系统,使过程在设计的最优点保持稳定的操作。
传统的设备改造操作往往是离线进行的,且应用的最优改造设计数据主要是通过离线得到的,改造后的设备也会与所期望的改造结果存在偏差。对于设备的实际运行来说,传统的改造主要是在几年一次的检修期进行的,施工周期较长。同时,考虑到可能涉及更换操作元件,设备改造的成本也会增加,操作费用较高。改造措施的离线操作特性也不能满足实施在线调整的要求,不能保证生产周期内装置流程设计的实时最优化。因此,应研究流程重构的设计方法,根据工艺操作条件的变化实现装置流程在线调整,进而实现在线流程重构改造。
此外,工程设计人员在过程设计阶段并未考虑到后续过程最优操作的问题,以及工程设备改造设计对于控制回路和最优操作条件的影响,以至于改造后的设备仍处于低效率的运行状态。同时对于较为严格的产品质量,设备的改造能够实现质的改变,然而能量如何最优配比还需要对整个装置的操作条件进行再优化,以实现设备的高效运行。基于以上的原因,研究工业设备流程重构的设计、识别及操作条件的再优化在工业设计及优化中的重要性日渐凸显,它能够同时实现设备的在线调整和操作条件优化的双目标。
针对进料条件对精馏塔内部的传热/传质及全塔用能的影响,本书旨在提出一种识别精馏塔进料瓶颈的方法,并采取进料位置调整的流程重构方法来消除进料瓶颈。针对类似于实际工业设备的仿真模型装置,探究如何对其进行操作条件的优化,并给出对其优化的具体方法。针对一种复杂的、传热传质的分离设备——脱甲烷塔,如何实现对其进行指标及进料位置的切换控制和节能控制。
根据研究对象复杂程度的不同,分为实现单个功能的简单操作单元对象和由单个功能的简单操作单元按照一定流程组合而成的复杂系统。根据操作对象实现的功能不同,可以分为各种不同类型的操作单元。其中精馏塔和换热器的研究较为普遍,分别用来实现产品的分离和能量的交换。一些学者选择对精馏塔操作单元进行研究,讨论其设计与改造方法,研究控制策略及操作条件优化的方法等[10~13];另一些学者则对由多组换热器构成的换热网络进行研究,研究换热网络的设计、控制及节能改造措施[14~22]。倘若仅对单个操作单元组成的简单对象进行研究,往往需要假定其外部输入的条件保持不变,研究结果仍具有一定的理论价值,并且对于复杂系统操作具有指导意义,但是这并不能完全反映出整体系统的特性。因此,在对于研究对象,应该根据所需要实现的功能进行选择。
为了从结构改造方面实现精馏塔的节能增效,具体的实施方法主要包含两个方面:①识别出系统的瓶颈,根据瓶颈识别准则对系统的瓶颈进行调整并实现节能增效;②直接设定系统设定改造的目标,采用结构优化的方法找到系统改造的措施并实现系统的节能。从实施方法上来说,前者往往采用较为直观的图示法,后者则往往采用数学优化的方法。
为了直观形象地表示分离系统内部的热力学特性,Dhole和Linnhoff[23]提出分馏塔总组合曲线(column grand composite curve,CGCC)的分析方法对精馏塔进行节能改造。吴升元等[24]受此启发,提出基于CGCC曲线确定分馏塔进料位置的方法,通过构造出与CGCC部分重合的两条相交的全塔精馏和提馏线,分析CGCC进料位置与两条曲线之间的关系来确定最佳进料位置。但所采用的全塔精馏和提馏线主要依据塔顶或塔底进料求出,也就限制了该方法仅适用于单一进料的情况,因此不适用于多股进料脱甲烷塔的进料位置分析及瓶颈识别。
相比之下,分析方法同时包含了热力学的第一定律和第二定律,能帮助识别出系统的无效操作单元。Khoa等[25]提出用三维
分析曲线来识别影响精馏塔正常运行的设计和操作参数。Bandyopadhyay[26]应用“
-焓图”中“精馏-提馏曲线”的恒定特性分析识别了精馏过程中的
损失。Liu等[27]利用复合曲线和面积利用率(fractional utilization of area,FUA)曲线来识别最优的改造策略。Wei等[28]对文献[27]的方法进行了拓展,能直观显示出系统内部的瓶颈位置。Long等[29]采用FUA方法来判断气相的通过面积,来辨识精馏塔内部的液泛问题,进而采取热泵和热耦合精馏相混合的措施实现解瓶颈与改造操作。他们所提的
分析方法虽能够直观指示出系统的瓶颈位置,但只是针对单一进料或者二元精馏塔的情况,对于多股进料和多组分分离显得乏力。Shin等[30]采用
分析作为热力学工具来研究在天然气液体回收过程中不可逆的能量损失,探寻系统中的无效操作与设计。这些是制约精馏塔系统用能的瓶颈,也从计算上给出相应的判断准则。与用来进行瓶颈分析或者设备改造相比,
分析方法更主要是用来判断设备改造或者操作过程中无效能的量,是一个重要的能量效率的衡量指标[30~32]。
考虑到脱甲烷塔的多股进料及多组分的复杂性,且计算过程极为复杂,
分析相关的节能研究方法并不太适用于复杂进料的情况,需要结合内部传热/传质的机理找到针对多股进料精馏塔的瓶颈识别方法。
近年来,随着计算机辅助求解技术的进步,流程模拟或数学优化法因其考虑多因素的方便性,并且能直接实现系统重构或改造方案的便捷实施而得到广泛的关注。根据文献记载,自20世纪80年代以来,工业过程中的设备改造投入不断加大,占总投入的70%~80%[27]。在精馏过程中,随着市场对于新产品及产量需求的不断提高,能源紧缺,原始设备很大程度上造成能量的浪费或者不能满足需求,需要对精馏过程进行有效的改造。精馏装置改造技术应运而生,主要包含热泵系统的应用[29,33~43]、自热再生技术[44~48]、进料状态调整的研究[11,49~51]、再沸器和冷凝器的利用及改造[52~55]、精馏塔塔板结构的改造[27]等方面。
(1)热泵系统的应用 若精馏塔具有相对较低的热力学效率,则可以通过再沸器输入一个较高品级的能量来完成分离任务。同时,需要由塔顶的冷凝器提供同样数量的冷量来抵消塔底的热量,热泵的概念便应运而生,目的是提高精馏塔的能量利用效率。对于蒸汽压缩式热泵,选用一种合适的工作流体,该流体在冷凝器被蒸发后,通过压缩机重新压缩到一个较高的温度,并在再沸器中被冷凝,然后通过一个节流阀达到低于冷凝器的温度。在此过程中,热泵系统中合适的工作流体是设计中的一个重要的参数。考虑到一些馏分气的不可压缩性,蒸汽压缩式仅适用于一些特殊的热泵系统。蒸汽压缩式技术对于处理具有腐蚀作用和容易结垢的化合物相当有效[33]。相比之下,机械式蒸汽再压缩热泵则广泛应用于具有相似沸点的混合物的分离过程。塔顶的气相馏出物经压缩机压缩到达一个即使在较高温度下也能冷凝的压力,进而能为再沸器提供有效的热能,使得再沸器和冷凝器需求的额外能量下降[34~37]。机械式蒸汽再压缩热泵技术对挥发性相对较低的混合物是较经济有效的。由于塔顶和塔底的温差较小,它需要较小的压缩比,压缩机的功率也就较低[38]。机械式蒸汽再压缩热泵技术比蒸汽压缩热泵所需要的冷凝器更小,并且仅进行一次热交换,精馏塔的热效率较高[39]。热蒸汽再压缩热泵是对机械蒸汽再压缩式热泵的改进,用一个蒸汽喷射器来代替原来的压缩机进行工作。由于蒸汽喷射技术的优点,热蒸汽再压缩技术得到了广泛的应用[40]。蒸汽喷射器通过文丘里效应,从进入变径管道的射流流体中获得机械能,进而使得热蒸汽再压缩技术具有较强的鲁棒性,同时设备中不含有旋转部分,也就降低了设备投资和维护费用[41,42]。输入流体与塔顶馏分的混合可以达到需要的温度,这种技术比较适合塔顶产物中含水蒸气的精馏过程[43]。底部闪蒸热泵是一项重要的改造技术,来自精馏塔的底部流股在闪蒸罐内分成两部分:一部分作为最终的产品;另一部分先通过减压阀降低自身温度,再与塔顶出料流股进行热交换,随后被压缩到与塔相同的压力[37]。
(2)自热再生技术 热泵的技术仅考虑到了精馏塔再沸器的热量回收,并未对进料预热所需的热量进行考虑,而自热再生技术则是通过压缩机充分利用系统的潜热和显热[44~46]。Kansha等[47]在自热再生技术的基础上,提出一种有效的、促进精馏塔能量利用的集成过程模型。将精馏塔分为两个模型,两个模型之间通过压缩机和换热器实现潜热及显热的再生利用,从而降低了整个过程对外部能量的需求。这种技术既可以应用于精馏塔的原始设计问题,也可以应用于对精馏塔系统的改造,且已经广泛应用于流程工业[48]。当塔板的数目及直径等结构参数固定时,增加压缩机及换热器的数目能有效降低精馏系统对外部能量的需求,与精馏塔的重新设计相比,改造过程也较容易实现。
(3)进料状态调整 将进料流股分成两股,并对其中一股流股进行预热,能够将预热效率提高[49,50]。根据组合曲线的特点,进料的预热或者预冷能分别有效地改变塔底再沸器或者塔顶冷凝器的热负荷和冷负荷的用量。Soave和Feliu[51]通过回收塔底部产品中的有效热能并对进料进行预热,能够降低底部再沸器对外界热能的消耗,从而使精馏塔达到节能的效果。他们应用稳态流程模拟的方法,通过迭代计算来确定能使工业精馏塔节能达到50%的进料分流比,并且得出在冷凝器的温度低于环境温度的精馏塔中,最小化冷量的消耗对于节能是至关重要的。Soave等[11]对深冷分离塔进行了分析,结合进料分流的应用,研究了利用塔顶产品对进料进行预冷操作来降低塔顶冷凝器的冷量消耗。精馏塔进料的热状态对精馏塔的处理能力具有强烈的影响[9],且对于组分较难分离的过程尤为明显。而改变进料的热状态的研究主要集中在单一进料或者二元精馏塔方面,也可以用来分析更加复杂的精馏塔。
(4)再沸器和冷凝器的利用及改造 为了最小化能量的消耗,通常通过回收塔底液相产品的热量来为精馏塔的底部提供能量[52,53]。Manley[52]应用中间再沸的技术提高天然气的回收率,这主要应用于脱乙烷塔和脱丙烷塔的节能研究中。当塔底的产品中含有较多的重组分时,中间再沸器的热效应会更为明显。且在中间再沸器的应用中,抽出的流股与返回的流股一般在同一块塔板上。通过对比,含有中间再沸器的精馏塔能够大幅度地降低热公用工程。Bandyopadhyay[54]通过对精馏塔的热集成研究,发现使用侧线换热器也能有效提高精馏塔的效率。对于低温精馏塔,通过中间冷凝器和中间再沸器的联合使用,能够有效降低能量的消耗[55]。对于精馏塔来说,相关研究也表明中间再沸器和冷凝器的使用能够允许精馏塔产量的增加[9]。同时,两者的使用也能改变精馏塔内部的气液相流股的分布,使塔内部气液相相对塔面积的使用更加一致。由于中间再沸器的存在,精馏塔底部的气液相拥堵的现象得到了有效缓解。因此,增加中间再沸器的过程改造增加了整个塔的使用面积。中间再沸器能够有效减少下部塔板的液相流量,并且增加上部塔板的气相流量。相似地,中间冷凝器能够减少上层各塔板的气相流量,增加下层各塔板的液相流量。
(5)精馏塔内部结构的改造方面 随着精馏塔塔板结构的迅速发展,产生了一系列高效的塔板结构。对精馏塔的内部结构参数进行分析,用高效的塔内部结构替换原始内部结构能有效提高精馏塔的分离效率和能量利用率。因而,内部结构的改造是一种快速有效的精馏塔的改造措施。用新的内部结构元件代替现存设备元件的方法,能够使精馏塔的处理量明显提升,但这并非是唯一的选项,也并不是最经济的改造方式。这种更换元件的方式是最直接且有效的方法,但是设备改造的费用较高,停工期较长[27]。
在众多的精馏装置改造方法中,核心应用技术是根据要求建立相关系统的数学优化模型,选取目标函数,采用合适的数学优化算法,通过求解得出最终的流程重构策略或者改造方案。代表性的研究主要包括Diaz等[56]和Luo等[57]建立混合整形非线性规划的(mixed integer nonlinear programming,MINLP)数学模型,并采用相应的求解方法实现对精馏塔结构的优化,从结构上实现对精馏系统进行去瓶颈操作。这种方法可被看作是一类“黑箱”的研究方法,不必事先识别瓶颈的位置,也就降低了识别系统瓶颈的难度。但去瓶颈的改造方法实施的过程往往极其复杂,且最优解也并不一定存在。在此基础上,引入图示化的分析方法能够有效降低“黑箱”分析方法的难度。尹洪超等[58]做了相关研究工作,提出基于超结构模型的数学规划方法与全局夹点分析相结合的设备改造方法对老旧设备进行改造。该研究方法较类似于常说的“灰箱”研究法,在部分夹点法分析结果的基础上进行优化计算,能够从很大程度上降低优化求解的难度。无论是哪种操作方法,都需要建立设备改造的结构化优化模型,并且需要实现优化问题的求解。这些在实际的过程中都是不易求解且不易操作的,且所建立的结构优化模型的可靠性也需要不断验证。
为确保能够方便得到识别出的系统的瓶颈位置并得到相应的调整方案,通过对比瓶颈识别方法和设备改造方法的优缺点,裂解装置多组分、多股进料的脱甲烷塔的瓶颈识别方法可以从图示法的角度出发,研究出新的通过表达塔内部传热/传质特性的可视化方法来识别多组分、多股进料精馏系统瓶颈的方法。
在设备的生产过程中无论是即将投入生产的新设备还是经过改造的老旧设备,在运行一段时期后都会存在操作点改变的问题,导致设备在运行过程中系统的能耗和物耗较高,重新进行设备改造成本较高且不易实施。与之相比,操作条件的优化是降低系统成本、提高经济效益的绝佳手段[58~62]。
精馏过程中的操作变量对产品产量和能耗具有重要的影响,在精馏系统生产过程中应对其进行优化操作,根据研究的侧重点的不同,可以进行不同的划分。从对象的复杂程度上说,主要可以分为单一精馏操作的单塔优化和核心精馏系统与外围设备的协同优化。从操作优化实现的对象形式上,文献的研究主要采用建模及模型仿真的方式对精馏塔装置进行仿真,根据对象的特性的不同,一方面可以建立优化问题后采取各种类型的求解方法,得到最优的操作参数;另一方面可以通过变量分析得到参数之间的相互影响规律,并对其调整实现最优化的操作。从操作优化问题的求解优化算法上来说,主要分为普通优化算法和智能优化算法。从操作优化的实效性上来说,分为在线优化和离线优化两种。
为获取精馏塔系统的最优操作条件,学者们往往从建立研究对象的仿真模型开始,在此基础上采用不同的优化方法实现所建立对象的操作条件优化问题的求解。刘兴高等[63]提出理想物系内部热耦合精馏塔的操作费用的估计方法,即通过建立的过程操作费用的优化数学模型来进行操作费用节省的优化。这种优化问题的求解既能够揭示出操作费用的节省潜力,同时又能得到最大操作费用节省目标下过程的最优操作条件。邵之江等[64]根据开放式方程建立了精馏塔的严格机理优化模型,考虑优化操作的实时性要求,提出基于简约空间序列二次规划算法的精馏塔智能操作优化方法。此方法综合考虑了优化效益、优化求解时间和质量约束等因素,其计算效率高于基于Snopt软件包和一般简约空间二次规划算法的精馏塔操作优化方法。针对精馏塔操作优化问题自由度低、模型结构稀疏且导数难以得到解析解的问题,江爱朋等[65]对文献[64]所提出的方法进行了拓展,将简约空间序列二次规划算法与混合求导方法相结合,建立精馏塔操作优化的问题,并采用自动微分技术进行优化问题的求解。席永胜等[66]通过从历史数据中挖掘模糊规则,结合专家经验建立模糊规则库,描述进料量、回流比与塔顶产品浓度之间的映射关系。提出了一类含模糊规则约束的数学规划模型,并将采用合成推理方法得到的模糊系统作为数学规划问题的等式约束,最后采用融合模糊推理的遗传算法进行求解来获得精馏塔的最优操作条件。文献[63~66]的研究主要包含优化模型的建立,实现优化问题的求解,最终得到最优的操作条件。其计算求解的过程往往复杂,一般较难得到操作优化问题的最优解。
考虑到通过模型计算来求解最优操作问题的难点,基于仿真软件的模型仿真操作条件分析易于操作且结果准确性较高,不用求解大量的数学优化问题。Nakaiwa等[67]通过模拟仿真的方式对理想热集成精馏塔进行了参数分析,分析过程设计和操作变量的影响关系,并为过程配置提供相应的指导,这种方式得到的过程结构具有较高的能量利用效率和灵活性。Gadalla等[68]考虑到炼油厂蒸馏系统的能量密集性,以及与相关联的换热网络之间关系的复杂性,采用蒸馏塔模拟开发的快捷模型与用于换热网络研究的改进快捷模型相结合的方式,通过改变关键操作参数来优化现有的蒸馏过程,同时考虑内部的水力限制以及现有热交换器网络的设计和性能,取得了不错的经济效益。同样,根据对仿真模型中的操作参数的分析,罗雄麟等[69]提出均衡操作优化的观点,认为乙烯精馏塔系统总能耗应该同时包含精馏塔自身能耗与塔底乙烷循环裂解的能耗,且两者之间此消彼长。仿真及数据分析能够得出两者之间的相关性并且证实总能耗存在最优点。对于操作的调整,只要将两者控制在相应的可行域内,即可实现两者之间的均衡操作优化,得到较高的回收率和较低的能耗,方便且易于实现。Liau等[70]使用由一组经验丰富的工程师所提供的专业知识建立原油蒸馏的专家系统,用具有人工神经网络(ANN)方法的输入-输出数据来构建原油蒸馏操作模型的知识数据库,并利用定义的目标函数找到最佳操作条件。Inamdar等[71]建立了精馏塔的稳态模型并通过工业数据进行校正,采用非支配排序遗传算法实现对上述模型进行操作优化问题的求解,并且在可接受的限制下获得系统的最佳操作条件。仿真的分析能够有效识别最优的操作变量,但要得到最优操作变量的值还要采取相应的求解方法,对于数学模型以及实时优化问题的建立难度大且计算量较大;相反,根据过程操作数据能快速得到神经网络模型,并且评估计算时间短。Osuolale等[32]在HYSYS仿真的基础上建立考虑有效能效率和产品组成的神经网络模型,实现了在满足产品质量约束的同时有效能效率最大化的操作优化。
工厂内实际的操作对象往往流程极其复杂,为实现复杂问题的简单化,Tahouni等[72]考虑到低温分离系统内部的核心过程分离塔与外部换热网络及制冷循环系统之间的复杂关系,首先对单个系统分别进行操作参数的优化,而后采用遗传或者模拟退火算法实现对整个系统的协同优化,进而证明协同优化能够获得更高的经济效益。Luo等[73]分析了蒸馏过程的操作变量对产品产量和能耗的影响。最低能量消耗和最大产品产出值的目标不协调,会阻碍炼厂的经济利益,因而提出了一种系统优化方法,在Aspen Plus对蒸馏塔模拟的基础上,采用夹点分析来确定能量回收的目标,并建立非线性规划问题,再通过粒子温敏随机算法进行解决,适用于同时考虑产品产量和能耗来实现原油蒸馏系统年经济效益最大化。无论是由单系统到整个系统的协同优化,还是整个系统的系统优化方法,都需要解决最终优化问题的求解,而求解方法往往较烦琐,常规数学求解方法又较为乏力。上述的优化方法一般是离线操作优化方法,也不适用于在线操作优化或者较为实际的优化操作。
目前对于操作优化方法的研究文献多集中在根据建模或者仿真的方式去实现离线的优化,且操作的对象往往不是实际对象本身,这样优化出的结果往往并不能直接应用到实际的装置上,因而能够直接应用于实际对象的操作优化方法显得更具有市场应用前景。本书将从关键操作单元的操作优化和整个系统的操作优化的角度,探讨多股进料脱甲烷塔装置操作条件优化的问题,并为实际装置操作优化问题的解决提供直接应用的范例。
针对本书中所涉及的研究对象——脱甲烷塔装置,王松汉等[74]认为脱甲烷部分的冷量消耗约占总负荷的12%,甲烷-氢的分离效果直接影响产品的纯度和后续的分离工序,是裂解气分离的关键。研究关键流程脱甲烷塔的操作条件直接关系到乙烯的产量、质量及成本的高低[75]。学者们对于脱甲烷塔装置的研究主要集中在对脱甲烷塔的改造优化方面和对塔的控制方法的研究方面。
对于优化问题的考虑,王弘轼等[76]在对低压脱甲烷系统进行计算机模拟的基础上,建立了以系统乙烯损失与能耗之和为目标函数的最优化数学模型,采用可行路径序贯模块法为最优化计算策略,结合广义既约梯度法对该系统实施优化计算,找出了对系统目标函数影响较大的可调决策变量及其最优化条件。他们对优化决策变量的选择及中等规模化工系统的优化策略进行了有益的探索。张元生[77]从操作条件出发分析了影响乙烯装置脱甲烷塔运行的主要因素,并针对乙烯装置改造后脱甲烷塔存在的问题进行了探讨。采用提高塔压、节流膨胀等方法改善脱甲烷塔的操作,减少了塔顶乙烯损失,提高了乙烯产品收率。Yang和Xu[78]在严格仿真模型的基础上,应用灵敏度分析的方法确定系统的最优操作变量,针对冷箱和脱甲烷塔的集成系统,建立了塔顶乙烯损失和能量消耗最低的目标函数,求解得到了最优的操作变量。赵晶莹等[79]在实际工厂数据的基础上,建立系统的仿真模型,根据优化系统中通过压缩机的循环量,进而实现对整个系统的节能优化。
对于改造问题的考虑,蒲通等[80]针对脱甲烷塔通过能力差、乙烯损失大等问题,应用流程模拟软件进行模拟计算,得出CH4/H2摩尔比塔顶操作压力、塔顶温度等影响乙烯回收的因素,并给出了相应地降低乙烯损失的操作措施。冯利等[81]通过模拟计算,认为将脱甲烷塔经过填料改造代替原来的浮法塔板,可带来系统的稳定操作和能耗的降低。陆恩锡等[82]在原始的脱甲烷系统的基础上,应用流程模拟开发出一套新系统,虽然新系统能达到节能的目的,但新流程的改造实施过程复杂,成本较高。张海涛[83]采用水力学计算的方法,从脱甲烷塔内部改造的角度出发,降低脱甲烷塔的乙烯损失率。Nawaz等[12]建立利润的经济目标函数,应用模拟退火算法寻求系统最优的设备尺寸和操作条件。
综上所述,对于乙烯裂解装置脱甲烷塔的研究,目前文献的研究限制在应用流程模拟或者操作条件优化对脱甲烷塔本身的改造和操作条件修改的范畴,未从脱甲烷塔的进料位置分布对内部传热/传质特性的影响以及瓶颈分析、进料位置的流程重构的设计方面进行研究。
与脱甲烷塔的控制策略相关问题的研究也是一个重要的课题,金冶[75]主要从传统的控制器控制方法进行研究,探讨塔的控制方法,以保证产品的质量指标,未考虑其他的因素。方红飞等[84]通过流程模拟,在脱甲烷系统内部引入质量控制回路,并通过控制系统的闭环动态模拟为脱甲烷塔的操作优化和控制系统设计提供决策依据。针对脱甲烷塔的进料状态随进料位置的差异,Luyben[85,86]对脱甲烷塔系统的动态控制进行了研究,提出脱甲烷塔的进料中甲烷和乙烷的相对数量对深冷高压精馏塔塔底产品有重要影响,同时分析了进料组成对脱甲烷塔设计的影响,提出随着进料组分数量的变化,应该对设备进行有效的改造。但同时考虑脱甲烷塔关键指标控制与系统能量优化的控制策略并未提及,针对多组合进料位置的切换问题也未涉及。
综合分析以脱甲烷塔为主要研究对象的文献,主要限制在应用流程模拟或者操作优化对脱甲烷塔的内部结构、外围设备的改造以及操作条件的优化方面,而对多股进料脱甲烷塔内部传热/传质的分析、进料位置调整的控制方法及控制与能量优化相结合的控制策略的研究较少。本书从脱甲烷塔内部的传热/传质的分析研究出发,研究进料位置对内部的传热/传质的影响规律,进而实现系统的瓶颈分析及流程重构的设计,在进料位置切换的流程重构过程中同时解决关键指标的控制与系统能量的协同优化等问题。