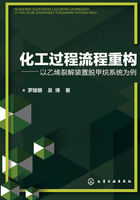
第1章 绪论
在化工生产过程中,为了实现不同产品组分的分离,往往需要多种不同操作单元的协同配合。随着设备的长期运行,其中的一些操作单元会出现系统节能优化的瓶颈,直接制约着整个系统产品的分离及能量的高效利用,通过操作条件的优化已经无法达到降低系统能耗的目标。此时往往需要识别出系统的用能及分离的瓶颈,并根据瓶颈及瓶颈处操作单元的特性,采取相应的设备改造措施,在设备改造后重新进行设备操作条件的再优化,其实施的基本思路如图1.1中的路径1所示。设备改造的措施往往费用较高,且需要停工作业。相比之下,设备的流程重构(结构优化)通过实现对设备流程的调整达到去瓶颈的操作,不但能避免停工作业,而且能降低设备的操作费用。同时,对流程重构后的系统的再优化操作,能够有效解决重构后系统的操作条件最优化的问题,其实施的基本思路如图1.1中的路径2所示。实现流程重构与操作条件再优化的轮换操作,能够同时获得去瓶颈和操作条件优化的双重功效,是一种有效地降低系统能耗的措施。路径2的方法更加方便且易于在线操作和实现系统的周期循环优化。

图1.1 设备改造与流程重构实施策略
由于精馏功能的特殊性,是一项重要的分离技术,因此在整个过程工业中约占全部流体分离操作的95%[1]。精馏塔的分离效率及节能同时受到冷凝器和再沸器等外部操作参数以及塔板的分离效率等内部结构参数的影响[2~6]。传统的精馏塔分析主要集中于对精馏塔节能的研究,在相同的分离指标下使得塔顶和塔底的能量消耗最小。近年来,随着科学技术的进步,高效塔板的不断出现,已证实改造塔板的结构参数是有效改变精馏塔分离效率的措施[7~9],然而这种改造操作的成本较高并且施工不便。考虑到上述诸多因素,探索在不改变精馏塔内部结构的条件下,又能提高精馏塔的用能效率的措施显得尤为重要。精馏塔在设计之初是根据分离进料的状态(流量、组成等)来选择进料位置,其参数往往是合理的。但随着装置的运行,塔内部的结垢或者进料组成及流量的差异,在原始的进料位置保持不变的条件下,这样的进料位置就可能导致精馏塔内部的传热/传质的异常,塔板的利用效率随之下降,对于含有多股进料的精馏塔来说,这种变化会更加明显。例如本书所涉及的具有质量交换的换热网络系统——乙烯裂解过程脱甲烷塔装置,其中传热单元实现冷热交换,闪蒸单元实现粗分,而精馏塔同时完成质量交换和能量交换,进而实现轻重组分的精细分离,基本流程如图1.2所示。如何找到这些影响精馏塔内部传热/传质的进料位置,尤其是对于多股进料的精馏塔,如图1.2中的四股进料脱甲烷塔,并实施流程重构对进料位置进行调整来降低其影响,进而实现整个装置的节能和产品的分离效率的提高。

从研究对象的选择方面来说,具有质量交换的换热网络系统是同时包含换热网络和精馏塔质量交换单元的系统。换热网络的输出会直接影响到精馏塔的进料状态,两者具有很强的相关性,并且精馏塔的进料状态会严重影响其内部气相和液相的分布规律,进而影响到后续操作单元中最终产品的分离。为了较为准确地分析组合系统内部各个单元之间的相关性及相互的影响,在对象的选择时应该同时包含精馏塔和换热网络,并将同时具有质量交换和能量交换的精馏塔以及有能量交换的换热网络系统作为研究对象。换热网络系统决定了精馏塔的进料条件,然而本书的侧重点并不在于换热网络的结构优化改造方面,而是讨论在其提供的进料条件下精馏塔进料位置流程重构的识别及设计问题,从精馏塔的角度去探索精馏塔系统的能量使用、瓶颈的识别及去瓶颈的方法,为进料位置的在线流程重构的实施提供理论依据。
从改造策略方面来说,与常规改造精馏塔的措施相比,在不改变精馏塔塔板结构的前提下,研究精馏塔内部的传热/传质机制,分析制约精馏塔能量利用的瓶颈,研究进料位置对于内部传热/传质的影响规律,进而在分离负荷发生变化时,能够为进料位置调整的流程重构的设计提供合理的依据。对进料位置调整的流程重构策略完全可以在非停车的情况下进行,能实现根据需求及进料的变化在线对系统内部的流程进行重构操作,使得在动态调整过程中塔板的使用效率最大化,这不但有助于降低操作成本,而且能够获巨大的经济效益。在精馏塔的设计之初,设计人员往往对于同一股进料设置了多个备用的进料位置,进而在进料状态变化时,操作工可以根据需要对其实现进料位置的切换。与单股进料的精馏塔相比,多股进料的精馏塔的进料位置切换更加复杂。因此,在不对生产过程产生较大扰动的条件下,根据进料的差异去实现进料位置的在线流程重构是一个需要重点研究的问题。
从最优操作条件方面来说,经过设备改造的系统,设备的稳态工作点往往会发生改变,原始的条件不一定适合当前新系统,设计人员进而会对其再进行操作条件的优化,得到新系统的最优操作条件,这就是常见的设备改造与操作条件再优化的结合问题。类似地还有进料位置调整的流程重构问题。流程重构是从结构优化的角度去除系统中存在的瓶颈,但这种重构并不能够保证整个系统的操作条件最优。重构后系统仍需要进一步的操作优化,以获取结构参数变化后新系统的最优操作条件。在仿真装置上的优化策略的实现对于在实际装置上的再优化操作是一种有效的尝试,并且能够消除其对正常的生产指标和生产进度的影响,这是一个重要的研究课题。本书将在模拟实际脱甲烷塔装置的仿真模型上,根据流程重构后的装置,研究操作条件再优化的具体实施方法及优化问题的现场求解策略,为实际装置的在线优化及在线流程重构的实施提供一种可行的经验方法。
从控制策略方面来说,根据生产过程的要求,生产过程往往包含多个生产指标,其中包含参数要求较为苛刻的指标(浓度和温度)和符合一定的范围即可满足生产需要的宽泛指标(液位)。对于苛刻指标,通过控制手段即可满足要求。对于除此之外的指标,通过控制当然可以满足条件,但控制器的设定值不同导致了输出变量的不同,进而会导致能量的浪费,达不到能量使用的最优化,因此在控制苛刻变量的同时需要考虑系统内部其他变量的优化,使得整个系统的能量利用最优,即采用控制与协同优化相结合的控制方法。同时,随着现代化工厂对于自控率水平要求的不断提高,实现进料位置的自动在线流程重构中对关键指标的控制也是应该着重考虑的问题。若能够直接进行进料位置的在线流程重构,将在很大程度上解决进料条件变化的问题,既能在保障产品质量的同时降低系统的操作成本,又能减轻操作人员的工作负担。
因此,本书主要研究具有质量交换的换热网络的流程重构设计、识别及操作条件再优化的相关方法,并以乙烯裂解过程脱甲烷塔装置为例,根据图1.1实现流程重构的基本思路,给出解决脱甲烷塔系统节能优化方法实施的基本框架,如图1.3所示。

图1.3 流程重构实施的基本框架
为了实现对所提方法的研究,首先应对脱甲烷塔装置进行建模及仿真,并有效解决缺少工业装置数据来源的限制以及对所提方法有效性的验证问题。其次,针对脱甲烷塔装置,对于给定的装置进行进料的瓶颈识别,找到影响内部传热/传质的进料瓶颈,再采用进料位置流程重构的方法来尽可能地去除进料瓶颈对脱甲烷塔的物料分离及能量利用的影响。重构后的系统随着设备的长期运行会存在结垢等情况,导致进料条件的改变,需要对其进行操作条件的再优化。
本书基于乙烯裂解过程脱甲烷塔装置,在流程重构的设计、识别及操作条件的再优化研究方面主要有以下研究内容。
①考虑到应用实际装置开展相关课题研究较为困难,在对脱甲烷塔装置内部各部分模型的特点及难点分析的基础上,实现对整个脱甲烷塔装置平台的建模,并对其进行仿真验证。针对精馏塔内部传热/传质的规律,提出一种精馏塔内部传热/传质组合曲线的构建方法,以图示法来呈现精馏塔内部异常的传热/传质的瓶颈,并将其与进料位置进行关联,给出进料瓶颈的识别方法。以乙烯裂解过程中的关键过程多股进料脱甲烷塔为例,采用上述方法对其进行了进料瓶颈分析,探索系统的进料瓶颈。根据调整瓶颈进料位置后塔内部的传热/传质分布的变化,给出脱甲烷塔装置调整进料位置的流程重构方法。脱甲烷塔装置的仿真对比验证了装置平台模型的准确性。通过对脱甲烷塔装置进料瓶颈的识别及进料位置的流程重构方法的应用,无论是对产品质量的改变,还是对处理量的调整,所提方法均能有效降低多股进料脱甲烷塔系统的能耗。
②针对流程重构后多股进料脱甲烷塔装置操作条件的设置问题,新旧操作条件之间可能存在差异,并且新系统操作条件并非最优操作条件而导致系统能量的损耗过大,因而流程重构后需要对设备重新进行操作条件再优化。提出脱甲烷塔装置的核心流程的单塔优化和考虑进料条件的复合塔优化的具体实施方法。分别从单塔优化和复合塔优化的角度出发,采用单变量分析法寻找关于系统能耗的操作变量,根据系统的能量利用指标分别选择脱甲烷塔的冷量消耗及甲烷压缩机功率作为单塔与复合塔优化的目标函数,采用正交试验的方法寻找系统的最优操作变量。通过两种方案的对比,复合塔优化所带来的系统的节能效率要比单塔优化高,因而对系统进行操作优化应该将复合塔系统作为对象进行研究。
③多股进料脱甲烷塔是整个装置中的核心操作单元,其控制策略对于产品的分离和能耗具有重要的影响,引入过程控制与协同优化相结合的策略来实现系统能量的合理利用。同时,针对流程重构中的进料位置切换的问题,又讨论了进料位置切换与控制指标切换的控制问题。以双入双出系统为例,探讨了主被控变量通过控制器实现目标指标控制,并且次要被控变量采取优化的方法,得到在系统能耗最低条件下最优的控制策略。另外,通过对进料位置切换进行了动态分析,并且在常规的控制策略下分析塔顶塔底的控制效果,提出了塔顶控制指标与进料位置切换的分步与同步控制,并对控制效果及系统的能耗进行了对比分析。