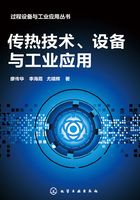
2.5 换热器
换热设备是实现物料之间热量传递的设备。换热器是过程工业中重要的设备之一。一个好的换热设备设计一般应满足如下要求:
①在给定的工艺参数条件(流体的流量、温度等)下,达到要求的传热量和流体出口温度(即符合工艺要求),即合理地实现所规定的工艺条件;
②采用传热速率大、流体流动压力降小、传热面积小的换热设备,以取得最佳经济效益;
③设备安全可靠;
④便于制造、安装、操作和维护。
换热器的类型很多,特点不一,可根据生产工艺要求进行选择。
2.5.1 换热器的类型
依据换热原理和实现热交换的方法,换热器可分为间壁式、混合式及蓄热式三类,其中以间壁式换热器应用最为普遍。
2.5.1.1 间壁式换热器
其特点是冷热两流体间用固体壁隔开,以使两种流体不相混合而通过固体壁面进行热量传递,这种换热器在工业上应用最为广泛。间壁式换热器按传热面的形状及结构特点又可分为管式换热器(如套管式、喷淋蛇管式、管壳式等)、板面式换热器(如板式、螺旋板式等)和扩展表面式(如板翅式、管翅式等),其中以管式换热器中的管壳式换热器最为普遍。
(1)管壳式换热器
也称列管式换热器,如图2-19所示,是间壁式换热器中应用最为广泛的一种。管壳式换热器(或称列管式换热器)在圆筒形壳体中放置了由许多管子组成的管束,管子的两端固定在管板上,壳体内安装了折流板以增加壳程流速,提高传热效率,是目前应用最广泛的一种换热设备。图2-20为管束在管板上固定的局部图示,一般采用胀接。根据需要,管壳式换热器可以采用水平或立式安装。

图2-19 管壳式换热器
1—封头;2—管板;3—壳体;4—管束;5—折流板;6—耳架;7—接管

图2-20 管子与管板连接的放大图
1—管子;2—管板
图2-19所示的管壳式换热器,因为管内流体自管束的一端进入,一次穿过管束并从另一端流出,而称为单程管壳换热器。许多情况下,由于管内流体的流速太低,影响了总传热系数的提高,此时可在两端的封头内添置适当的隔板,使流体先后流经各部分管束。图2-21中管内流体先通过管束的一半管子,又从左封头改变流向通过另一半管子,流体质点在管内所走的路程是管束长的两倍,称这个管壳换热器的管程为双程。

图2-21 双程管壳换热器
1—壳体;2—管束;3—挡板;4—隔板;5—鞍座
当增加隔板的数量和布置后,管程数还可增加,如表2-12所列的四程、六程、八程等。换热器中每个管程的管子数应大致相等。
表2-12 管程隔板的设置与管程数

壳内一般不设横向隔板而成为多壳程,一般多壳程是指多个相同的管壳换热器的串联使用。为了增加壳程流速、增强流体的湍动,提高壳程对流传热系数,在壳程内设置挡板(折流板),其形式为图2-22所示的三种:圆缺形、弓形和环盘形。图2-23表示设置圆缺形挡板(缺口在水平方向排列时)及环盘挡板后的壳体内流体流向。

图2-22 折流板的形式

图2-23 挡板间的流动情况
由于换热器内两种流体有明显的温度差异,因此管束和外壳的热膨胀程度显著的不同,产生管束、外壳、管板间的热应力。当热应力达到一定值时,可使管子发生弯曲变形,甚至从管板上拉脱,使换热器损坏。为此,当管子与壳体的温度相差50℃以上时,应采用热补偿措施,以减少热应力。一般采用在换热器的外壳中间部位加装波纹膨胀节来调整热膨胀量,减少热应力,如图2-24所示。由于这种结构简单,在管子与外壳温差低于60~70℃和壳程压力不高的操作条件下得到了广泛的应用。

图2-24 波纹膨胀节
管壳式换热器的突出优点是:单位体积设备所能提供的传热面积大,结构坚固,尤其适合在高温、高压、大型装置中应用。常用的管壳式换热器有固定管板式、浮头式、U形管式等结构形式。固定管板式换热器结构简单,造价低,但只适合于冷热两种流体温差不大的场合,且壳程不易清洗或检修;浮头式换热器管子受热或冷却时可以自由伸缩,适合于冷热两种流体温差较大的场合,且便于清洗和检修,但结构较复杂,造价较高;U形管式换热器的每根管子都弯成U形,所以只有一块管板,管程至少为两程。这种结构较浮头式简单,同样可用于温差较大的场合,但管程不易清洗。
各种类型的管壳式换热器以及其他类型的换热器,我国已有系列化标准,设计时参数的选定应参照有关标准。
(2)夹套式换热器
这种换热器构造简单,如图2-25所示。换热器的夹套安装在容器的外部,夹套与器壁之间形成密封的空间,为载热体(加热介质)或载冷体(冷却介质)的通路。夹套通常用钢或铸铁制成,可焊在容器上或者用螺钉固定在容器的法兰或器盖上。

图2-25 夹套换热器
1—内筒体;2—夹套;3—叶轮;4—接管;5—轴
夹套式换热器常用作反应器、物料贮罐、蒸发器、结晶器等,主要应用于过程的加热或冷却。根据需要,夹套内可以在不同的时间分别通入热水、蒸汽、冷却水、冷冻盐水,以满足槽内不同时期的加热、冷却的需要。在用蒸汽进行加热时,热汽由上部接管进入夹套,冷凝水则由下部接管流出。作为冷却器时,冷却介质(如冷却水)由夹套下部的接管进入,而由上部接管流出。
这种换热器的传热系数较小,传热面又受容器的限制,因此适用于传热量不大的场合。反应釜的内筒常用不锈钢或碳钢,夹套材料主要是价格低的碳钢。为了提高其传热性能,可在容器内安装搅拌器,使器内液体作强制对流;为了弥补传热面的不足,还可在器内安装蛇管等。
夹套换热器的总传热系数K的经验值如表2-13所列。
表2-13 夹套换热器的K值

(3)蛇管式换热器
当传热速率较大,需要大的传热面积时,夹套换热不能满足要求,可考虑浸入式蛇管换热。如图2-26所示,盘管安装在壳体内,形成蛇管内、外两种流体的流动空间。槽式容器内部也可设置适当的蛇管换热装置,有时还可将夹套、蛇管同时使用。

图2-26 蛇管式换热器
蛇管的形状是将直管加工成各种曲线形状的连续叠加状态,如螺旋状或盘管状态,其圈数多少可根据需要而定。制作蛇管的材料有碳钢、不锈钢、铝材、铅材、玻璃、塑料等。为防止蛇管在使用中变形,均把蛇管固定在各种支架上,并把伸出壳体外的管端固定在壳体上。蛇管的形状如图2-27所示,根据需要也可制作成其他形状。

图2-27 蛇管的形状
蛇管式换热器可分为两类,即沉浸式蛇管换热器和喷淋式换热器。
①沉浸式蛇管换热器 蛇管多以金属管子弯制成,或制成适应容器要求的形状,沉浸在容器中。两种流体分别在蛇管内、外流动而进行热量交换。
这种蛇管换热器的优点是结构简单、价格低廉、便于防腐蚀、能承受高压,主要缺点是由于容器的体积较蛇管的体积大得多,故管外的总传热系数值较小。如在容器内加搅拌器或减少管外空间,则可提高传热系数。
②喷淋式换热器 喷淋式换热器如图2-27(e)所示,多用作冷却器。单排或多排固定在支架上的蛇管排列在同一垂直面上,热流体在管内流动,自最下管进入,由最上管流出。操作运行状态如图2-28所示。冷水由最上面的多孔分布管(淋水管)流下,分布在蛇管上,并沿其两侧下降至下面的管子表面,最后流入水槽而排出。冷水在各管表面流过时,与管内流体进行热交换。这种设备常放置在室外空气流通处,冷却水在空气中汽化时,可带走部分热量,以提高冷却效果。它和沉浸式蛇管换热器相比,还具有结构简单,安装方便,便于工作与检修和清洗、传热效果较好等优点,其缺点是体积较大,常安装在室外操作,喷淋不易均匀。管外对流传热系数比沉浸式大,这是由于部分冷却水被汽化的结果。

图2-28 喷淋式换热器
1—冷却水泵;2—淋水管;3—支架;4—蛇管;5—排水
蛇管换热器的K值范围如表2-14所示。
表2-14 蛇管换热器的K值范围

应指出,在夹套式或沉浸式换热器的容器内,流体常处于不流动的状态,因此在某瞬间容器内各处的温度基本相同,而经过一段时间后,流体的温度由初温变为终温,故属于不稳定传热过程。这些换热器仍为一些中小型工厂所广泛采用。
③套管式换热器 套管式换热器系用管件将两种尺寸不同的标准管连接成为同心圆的套管,然后用180°的回弯管将多段套管串联而成,如图2-1所示。每一段套管称为一程,程数可根据传热要求而增减。每程的有效长度为4~6m,若管子太长,管中间会向下弯曲,使环形中的流体分布不均匀。
套管换热器的优点为:构造较简单;能耐高压;传热面积可根据需要而增减;适当地选择管内、外径,可使流体的流速较大,且双方的流体作严格控制的逆流,有利于传热。
缺点为:管间接头较多,易发生泄漏;单位换热器长度具有的传热面积较小。故在需要传热面积不太大而要求压强较高或传热效果较好时,宜采用套管式换热器。
2.5.1.2 混合式换热器
这种类型的换热器主要用于气体的冷却(有时兼作除尘、增湿或减湿等用)及蒸气的冷凝,故又称为混合式冷却器或冷凝器。其特点是被冷凝(或冷却)的蒸气直接与水(或冷流体)接触进行换热,因此传热效果较好。此外设备结构简单,易于防腐蚀。必须指出,仅在允许冷、热流体互相混合时,才能应用混合式换热器。
2.5.1.3 蓄热式换热器
蓄热式换热器又称蓄热器,器内装有固体填充物(如耐火砖等)。冷、热流体交替地流过蓄热器,利用固体填充物来积蓄和释放热量而达到换热的目的。通常由两个并联的蓄热器交替使用。
蓄热器结构简单,且可耐高温,因此多用于高温气体的加热。其缺点是设备体积庞大,且不能完全避免两种流体的混合,所以这类设备在过程工业生产中使用得不太多。
2.5.1.4 翅片式换热器
翅片式换热器的构造特点是在管子表面上装有径向或轴向翅片。当两种流体的对流传热系数相差很大时,例如用水蒸气加热空气,此传热过程的热阻主要在气体和壁面间的对流传热方面。若气体在管外流动,则在管外装置翅片,既可扩大传热面积,又可以增剧流体的湍动,从而提高换热器的传热效果。一般来说,当两种流体的对流传热系数之比为3∶1或更大时,宜采用翅片式换热器。
翅片的种类很多,按翅片的高度不同,可分为高翅片和低翅片两种,其中低翅片一般为螺纹管。高翅片适用于管内、外对流传热系数相差较大的场合,现已广泛应用于空气冷却器上。低翅片适用于两流体的对流传热系数相差不太大的场合,如黏度较大的液体的加热或冷却等。
2.5.1.5 螺旋板式换热器
如图2-29所示,螺旋板式换热器是由两块薄金属板焊接在一块分隔挡板(图中心的短板)上并卷成螺旋形而构成的。两块薄金属板在器内形成两条螺旋形通道,在顶、底部上分别焊有盖板或封头。进行换热时,冷、热流体分别进入两条通道,在器内作严格的逆流流动。

图2-29 螺旋板换热器的螺旋形流道
1—隔板;2—传热板
因用途不同,螺旋板式换热器的流道布置和封盖有下面几种型式。
(1)Ⅰ型结构
两个螺旋流道的两侧完全为焊接密封的Ⅰ型结构,称为不可拆结构,如图2-30(a)所示。两流体均作螺旋流动,通常冷流体由外周流向中心,热流体从中心流向外周,即完全逆流流动。这种型式主要用于液体与液体间的传热。

图2-30 各种型式的螺旋板换热器
(2)Ⅱ型结构
Ⅱ型结构如图2-30(b)所示。一个螺旋流道的两侧为焊接密封,另一流道的两侧是敞开的,因而一流体在螺旋流道中作螺旋流动,另一流体则在另一流道中作轴向流动。这种型式适用于两流体的流量差别很大的场合,常用作冷凝器、气体冷却器等。
(3)Ⅲ型结构
Ⅲ型结构如图2-30(c)所示。一种流体作螺旋流动,另一种流体是轴向流动和螺旋流动的组合,适用于蒸气的冷凝冷却。
螺旋板换热器的直径一般在1.6m以内,板宽200~1200mm,板厚2~4m,两板间的距离为5~25mm。常用材料为碳钢和不锈钢。
螺旋板换热器的优点如下。
①总传热系数高 由于流体在螺旋通道中流动,在较低的雷诺数下即可达到湍流(一般Re=1400~1800,有时低到500),并且选用较高的流速(对液体为2m/s,气体为20m/s),故总传热系数较大。螺旋板换热器总传热系数经验值如表2-15所示。
表2-15 螺旋板换热器的K值

②不易堵塞 由于流体的流速较高,流体中悬浮物不易沉积下来,并且任何沉积物将减小单流道的横断面,因而速度增大,对堵塞区域又起冲刷作用,故螺旋板换热器不易被堵塞。
③能利用低温热源,能精密控制温度 这是由于流体流动的流道长及两流体完全逆流的缘故。
④结构紧凑 单位体积的传热面积约为列管式换热器的3倍。
螺旋板式换热器的缺点如下。
①操作压强和温度不宜太高 目前最高操作压强为2MPa,温度约为400℃以下。
②不易检修 因整个换热器为卷制而成,一旦发生泄漏,修理内部很困难。
2.5.1.6 板式换热器
板式换热器主要由一组长方形的薄金属板平行排列、夹紧组装于支架上而构成。两相邻板片的边缘衬有垫片,压紧后可以达到密封的目的,且可用垫片调节两板间流体通道的大小。每块板的四个角上,各开一个圆孔,其中有两个圆孔和板面上的流道相通,另外两个圆孔则不相通,它们的位置在相邻的板上是错开的,以分别形成两流体的通道。冷、热流体交替地在板片两侧流过,通过金属板片进行换热。每块金属板面冲压成凹凸规则的波纹,以使流体均匀流过板面,增加传热面积,并促使流体湍动,有利于传热。
板式换热器的优点:结构紧凑、单位体积设备提供的传热面积大;总传热系数高,如对低黏度液体的传热,K值可高达7000W/(m2·K);可根据需要增减板数以调节传热面积;检修和清洗都较方便等。
板式换热器的缺点:处理量不大;操作压强比较低,一般低于1500kPa,最高不超过2000kPa;因受垫片耐热性能的限制,操作温度不能太高,一般对于合成橡胶垫圈的温度不超过130℃,压缩石棉垫圈不超过250℃。
2.5.1.7 板翅式换热器
板翅式换热器的结构形式很多,但其基本结构元件相同,即在两块平行的薄金属板(称平隔板)间,夹入波纹状的金属翅片,两边经侧条密封,组成一个单元体。将各单元体进行不同的叠积和适当地排列,再用钎焊给予固定,即可得到常用的逆、并流和错流的板翅式换热器的组装件,称为芯部或板束,然后将带有流体进、出口的集流箱焊到板束上,就成为板翅式换热器。目前常用的翅片形式有光直型翅片、锯齿型翅片和多孔型翅片等。
板翅式换热器的主要优点:
①总传热系数高,传热效果好 由于翅片在不同程度上促进了湍流并破坏了传热边界层的发展,故总传热系数高。同时冷、热流体间换热不仅以平隔板为传热面,而且大部分热量通过翅片传递,因此提高了传热效果。
②结构紧凑 单位体积设备提供的传热面积一般能达到2500m2,最高可达4300m2,而列管式换热器只有160m2。
③轻巧牢固 因结构紧凑,一般用铝合金制造,故重量轻。在相同的传热面积下,其重量约为列管式换热器的十分之一。波纹翅片不单是传热面,又是两板间的支撑,故其强度很高。
④适应性强、操作范围广 由于铝合金的热导率高,且在零度以下操作时,其延性和抗拉强度都可提高,故操作范围广,可在220℃至绝对零度范围内使用,适用于低温和超低温的场合。适应性也较强,既可用于各种情况下的热交换,也可用于蒸发或冷凝。操作方式上可用于逆流、并流、错流或错逆流同时并存等。此外,还可用于多种不同介质在同一设备内进行换热。
板翅式换热器的缺点:
①由于设备流道很小,故易堵塞而增大压强降;且换热器内一旦结垢,清洗和检修很困难,所以处理的物料应较洁净或预先进行净制。
②由于隔板和材料都由薄铝片制成,故要求介质对铝不发生腐蚀。
2.5.2 换热器内流体流程和流速的选择
(1)流程的选择
在换热器中,选择哪一种流体走管程,哪一种流体走壳程,这对设备的合理使用非常重要。选择流程时要考虑:不洁或易结垢的物料应走易于清洗的一侧,对于直管管束,一般走管程;需要提高流速以增大传热系数的流体应走管程;腐蚀性或压力高的流体应走管程;深冷低温流体应走管程;被冷却流体和饱和蒸汽一般走壳程;黏度大或流量小的流体,以走壳程为宜,因壳程中一般设有折流板,易于达到湍流。
以上各点常常不可能同时满足,应首先抓住主要方面,如压力、腐蚀性、清洗要求等,再兼顾其他要求。
(2)流速的选择
流速直接影响传热系数,但流速增大,又将使流体阻力增大,因此,换热器内适宜的流速应通过经济核算选择。表2-16列出的常用流速范围,可供参考。
表2-16 管壳式换热器内常用流速范围

2.5.3 各种间壁式换热器的比较
在过程工业生产中,经常要求在各种不同的条件下进行热量交换,例如操作压强高达200MPa,温度在-250~1500℃的范围内变化,某些流体的腐蚀性又特别严重等,因此,对换热器的要求也必然是多种多样的。每种类型的换热器都有其优点。选择换热器类型时,要考虑的因素很多,例如材料、压强、温度、温度差、压强降、结垢腐蚀情况、流动状态、传热效果、检修和操作等。对同一种换热器而言,在某种情况下使用是好的,而在另外的情况下,却不能令人满意,甚至根本不能使用。现在虽然新型换热器不断出现和使用日趋广泛,但是老式的换热器(如蛇管式和夹套式换热器)仍有其适用的场合,如在釜式反应器中的换热,而其他类型的换热器就难以完成此种传热任务。列管式换热器在传热效果、紧凑性及金属耗量方面不如新型换热器(如板式、螺旋板式换热器),但它具有结构坚固,可在高温、高压下操作及材料范围广等优点,因此列管式换热器仍然是使用最普遍的。当操作温度和压强都不是很高,处理量又不太大,或处理腐蚀性流体而要求用贵金属材料时,就宜采用新型的换热器。总之,采用什么类型的换热器,要视具体情况,综合考虑择优选定。
2.5.4 传热的强化途径
所谓强化传热过程,就是指提高冷、热流体间的传热速率。从传热速率方程不难看出,增大传热系数K、传热面积S或平均温度差都可提高传热速率。在换热器的设计和生产操作中,或换热器的改进中,大多从这三方面来考虑强化传热过程。
(1)增大传热面积S
增大传热面积可以提高传热速率。但应指出,增大传热面积不应靠加大设备的尺寸来实现,而应从设备的结构来考虑,提高其紧凑性,即单位体积内提供较大的传热面积。改进传热面的结构,如用螺纹管、波纹管代替光滑管,或采用翅片管换热器、板翅式换热器及板式换热器等,都可增加单位体积设备的传热面积。例如板式换热器,每立方米体积可提供的传热面积为250~1500m2,而管壳式换热器单位体积的传热面积为40~160m2。
(2)增大平均温度差Δt
增大平均温度差,可以提高传热速率,但是平均温度差的大小主要取决于两流体的温度条件。一般来说,流体的温度为生产工艺条件所规定,可变动的范围是有限的。当换热器中两侧流体均变温时,采用逆流操作可得到较大的平均温度差。螺旋板式换热器和套管式换热器可使两流体作严格的逆流流动。
(3)增大总传热系数K
增大总传热系数也可以提高传热速率。已知总传热系数的计算公式为
(2-77)
由上式可见,要提高K值,就必须减小各项热阻。但因各项热阻所占的比重不同,因此应设法减小对K值影响较大的热阻。减小热阻的方法有。
①加大流速,增强流体湍动程度,减小传热边界层中滞流内层的厚度,以提高对流传热系数,即减小对流传热的热阻。例如增加列管换热器的管程数和壳程中的挡板数,均可提高流速;板式换热器的板面压制成凹凸不平的波纹,流体在螺旋板式换热器中受惯性离心力的作用,均可增加湍动程度;在管内装入麻花铁、螺旋圈或金属丝片等添加物,亦可增强湍动,且有破坏湍流底层的作用。与此同时,应考虑由于流速加大而引起流体阻力的增加及设备结构复杂、清洗和检修困难等问题,即不能片面地要求提高对流传热系数,而不顾及其他。
②防止结垢和及时地清除垢层,以减小垢层热阻。例如增加流速可减弱垢层的形成和增厚;易结垢的流体在管内流动,以便于清洗;采用机械或化学的方法或采用可拆卸换热器的结构,以便于清除垢层。
从以上分析可知,强化传热的途径是多方面的,但对某实际的传热过程,应作具体分析,即抓住影响强化传热的主要矛盾,并结合设备结构、动力消耗、检修操作等予以全面考虑,采取经济而合理的强化传热的方法。