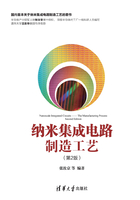
4.4 半导体绝缘介质的填充
随着半导体技术的飞速发展,半导体器件的特征尺寸显著减小,相应地也对芯片制造工艺提出了更高的要求,其中一个具有挑战性的难题就是绝缘介质在各个薄膜层之间均匀无孔的填充,以提供充分有效的隔离保护,包括浅槽隔离(shallow-trench-isolation)、金属前绝缘层(pre-metal-dielectric)、金属层间绝缘层(inter-metal-dielectric)等。
高密度等离子体化学气相沉积(HDP-CVD)工艺自20世纪90年代中期开始被先进的芯片工厂采用以来,以其卓越的填孔能力、稳定的沉积质量、可靠的电学特性等诸多优点而迅速成为0.25μm以下先进工艺的主流。
4.4.1 高密度等离子体化学气相沉积工艺
在HDP-CVD工艺问世之前,大多数芯片厂普遍采用等离子体增强化学气相沉积(PE-CVD)进行绝缘介质的填充。这种工艺对于大于0.8μm的间隔具有良好的填孔效果,然而对于小于0.8μm的间隔,用PE-CVD工艺一步填充这么高的深宽比(定义为间隙的深度和宽度的比值)的间隔时会在间隔中部产生夹断(pinch-off)和空穴(见图4.12)。

图4.12 PE-CVD填充产生pinch-off
其他一些传统CVD工艺,如常压CVD(APCVD)和亚常压CVD(SACVD)虽然可以提供对小至0.25μm的间隔的无孔填充,但这些缺乏等离子体辅助沉积产生的膜会有低密度和吸潮性等缺点,需要增加PE-CVD薄膜对其进行保护,或者进行后沉积处理(如退火回流等)。这些工序的加入同样提高了生产成本,增加了整个工艺流程的步骤和复杂性。
为了同时满足高深宽比间隙的填充和控制生产成本,诞生了HDP-CVD工艺,它的特点在于,可以在同一个反应腔中同步地进行沉积和物理轰击(见图4.13),从而实现绝缘介质在沟槽中的bottom-up生长。

图4.13 HDP-CVD工艺沉积同时进行原位物理轰击
1.HDP-CVD作用机理
为了形成高密度等离子体,需要有激发混合气体的射频(RF)源,并直接使高密度等离子体到达硅片表面。在HDP-CVD反应腔中(见图4.14)[1],主要是由电感耦合等离子体反应器(ICP)来产生并维持高密度的等离子体。当射频电流通过线圈(coil)时会产生一个交流磁场,这个交流磁场经由感应耦合即产生随时间变化的电场,如图4.15所示。电感耦合型电场能加速电子并能形成离子化碰撞。由于感应电场的方向是回旋型的,因此电子也就往回旋方向加速,使得电子因回旋而能够运动很长的距离而不会碰到反应腔内壁或电极,这样就能在低压状态(几个mT)下制造出高密度的等离子体。

图4.14 应用材料HDP-CVD反应腔

图4.15 电感耦合等离子体反应器(ICP)工作原理示意图
为了实现HDP-CVD的bottom up生长,首先要给反应腔中的高能离子定方向,所以沉积过程中在硅片上施加RF偏压,推动高能离子脱离等离子体而直接接触到硅片表面,同时偏压也用来控制离子的轰击能量,即通过控制物理轰击控制CVD沉积中沟槽开口的大小。在HDP-CVD反应腔中,等离子体离子密度可达1011~1012/cm3(2~10mT)。由于如此高的等离子体密度加上硅片偏压产生的方向,使HDP-CVD可以填充深宽比为4∶1甚至更高的间隙。
2.HDP-CVD常见反应
HDP-CVD可用于金属形成前或形成后。某些金属如NiSix或Al会对形成后的工艺温度有一定限制,而在HDP-CVD反应腔中高密度等离子体轰击硅片表面会导致很高的硅片温度,另外,高的热负荷会引起硅片的热应力。对硅片温度的限制要求对硅片进行降温,在HDP-CVD反应腔中是由背面氦气冷却系统和静电卡盘(electrostatic chuck)共同在硅片和卡盘之间形成一个热传导通路,从而来降低硅片和卡盘的温度。
HDP-CVD的反应包含两种或多种气体参与的化学反应。根据沉积的绝缘介质掺杂与否及掺杂的种类,常见的有以下几种:
(1)非掺杂硅(酸盐)玻璃(un-doped silicate glass, USG)
SiH4+O2-→USG+挥发物
(2)氟硅(酸盐)玻璃(fluorosilicate glass, FSG)
SiH4+SiF4+O2-→FSG+挥发物
(3)磷硅(酸盐)玻璃(phosphosilicate glass, PSG)
SiH4+PH3+O2-→PSG+挥发物
3.HDP-CVD工艺重要参数-沉积刻蚀比
如前所述,HDP-CVD工艺最主要的应用也是其最显著的优势就是间隙填充,如何选择合适的工艺参数来实现可靠无孔的间隙填充就成为至关重要的因素。在半导体业界,普遍采用沉积刻蚀比(DS ratio)作为衡量HDP-CVD工艺填孔能力的指标。沉积刻蚀比的定义是
沉积刻蚀比=总沉积速率/刻蚀速率=(净沉积速率+刻蚀速率)/刻蚀速率
实现对间隙的无孔填充的理想条件是在整个沉积过程中始终保持间隙的顶部开放,以使反应物能进入间隙从底部开始填充,也就是说,我们希望在间隙的拐角处沉积刻蚀比为1,即净沉积速率为零。对于给定的间隙来说,由于HDP-CVD工艺通常以SiH4作为绝缘介质中Si的来源,而SiH4解离产生的等离子体对硅片表面具有很强的化学吸附性,导致总沉积速率在间隙的各个部位各向异性,在间隙拐角处的总沉积速率总是大于在间隙底部和顶部的总沉积速率;另外,刻蚀速率随着溅射离子对于间隙表面入射角的不同而改变,最大的刻蚀速率产生于45~70之间,正好也是处于间隙拐角处,因此需要优化沉积刻蚀比来得到最好的填充效果。图4.16即是HDP-CVD工艺在不同沉积刻蚀比下对间隙填充情况的示意图。要得到优化的沉积刻蚀比,最主要的影响因素包括反应气体流量、射频(包括电感耦合和偏压)的功率、硅片温度、反应腔压力等。

图4.16 不同沉积刻蚀比的填充
4.HDP-CVD中的再沉积问题
另外,在HDP-CVD中的物理轰击遵循碰撞中的动量守恒原理,因此被溅射出的物质存在一定角度。随着沟槽开口尺寸变小,当轰击离子质量较大时,被轰击掉的部分会有足够的能量重新沉积到沟槽侧壁另一侧某一角度处,使得这些地方薄膜堆积,过多的堆积将会造成沟槽顶部在没有完全填充前过快封口(见图4.17)。随着器件尺寸减小,填充能力的挑战越来越大。为了减少物理轰击造成的再沉积,HDP中的轰击气体主要经历了Ar→O2→He→H2的变化,通过降低轰击原子的质量来改善再沉积引起的填充问题。但是仅仅通过轰击物质的改变,沟槽填充能力的改善是有限的。

图4.17 HDP-CVD中的再沉积
所以在90nm以后,为改善物理轰击所造成的问题,引入同位化学刻蚀对填充结构轮廓进行调整,即在沟槽顶部封口前将其重新打开而不造成再沉积,使得薄膜可以bottom-up填满整个沟槽。其中NF3的干法刻蚀被认为是一种非常有效的方法。NF3在等离子体中离解形成含氟的活性基团,它可以打断已沉积薄膜中的Si-O键,形成挥发性的SiF4随着多余的O2一起被抽走,从而打开沟槽顶部。但是这种单步沉积-刻蚀-沉积对填充能力的改善是有限的。

通过多步循环沉积-刻蚀-沉积来实现对所填充结构轮廓的调整,来降低沟槽填充的难度。这样可以在保持HDP本身填充能力的同时,通过NF3的刻蚀来重新调整沟槽的形状,使得更多的材料可以填充进去,保证沟槽不封口形成孔洞。
5.轮廓修正(多步沉积-刻蚀)的HDP-CVD工艺[2]
图4.18是一个典型的多步沉积-刻蚀HDP-CVD的工艺。与一般的HDP相似,主要通过SiH4和O2反应来形成SiO2薄膜。但是沉积过程的要求与传统的HDP不同,传统的HDP-CVD要求侧壁沉积尽可能薄以提供足够的开口使反应粒子可以到达沟槽底部,最大限度实现从底部到顶部的填充。但是多步DEP-ETCH的HDP-CVD主要是以SiO2的刻蚀为主导的,因此轮廓结构的控制更重要,最优化的沉积应该有足够厚的侧壁保护,对称的沉积轮廓。应用材料的研究表明(见图4.19),较低的沉积温度(230~600℃)能够很大地改善侧壁的保护但又不损伤填充能力,同时可以通过调节沉积温度将薄膜的应力从180MPa调到100MPa。一旦沉积条件确定后,填充能力可以通过每个循环中沉积和刻蚀的量来优化。降低每个沉积过程的沉积厚度可以实现更多次的轮廓调整,但是这样会增加沉积时间也引入更多的F,有可能会对器件可靠性造成影响。而沉积过程中的物理轰击气体分子量越大,可以在沟槽顶部形成Cusping来以保护沟槽顶部在刻蚀过程中不被损伤。目前主要采用He为主的He/H2混合,主要想通过保证填充能力的同时为沟槽顶部提供足够的保护。

图4.18 多步沉积-刻蚀HDP-CVD的工艺

图4.19 侧壁厚度与沉积温度关系
刻蚀过程是多步dep-etch的关键步骤,刻蚀过程通过与NF3的反应去除掉SiO2,由于NF3在沟槽不同部位的入射角不同,可以实现顶部刻蚀较多从而可以修整部分填充后的沟槽的形状得到更容易填充的沟槽结构。刻蚀过程所采用的载气为H2,载气的分子量越小,可以尽量减少物理轰击的效果。另外刻蚀的对称性对最后的完全填充非常重要,尤其在晶片边缘,由于F radical的方向性,这种不对称性就更加严重,可以通过调节压力、NF3气体流量、衬底偏压大小以及刻蚀化学物质来对对称性进行优化。刻蚀的量必须进行非常好的控制。对于特定的沟槽结构,要进行沉积和刻蚀量的优化,尽可能达到填充、沉积速率以及刻蚀Window的平衡。
另外为了尽可能降低薄膜中由于NF3刻蚀而引入的F。刻蚀结束后,引入Ar/O2/He/H2等离子体处理可以去除薄膜中所残留的F,通过调整等离子体处理的时间和功率大小可以优化等离子体处理工艺,将薄膜中的F含量降低到0.07at.%[2]。
多步沉积-刻蚀填满沟槽后,进一步沉积一层高温的SiO2薄膜,作用有二,进一步去除薄膜中残留的F以及提高薄膜的质量。
4.4.2 O3-TEOS的亚常压化学气相沉积工艺
1.为什么SACVD被再次使用
对于技术节点为亚65nm、器件深宽比大于8的结构来说,人们发现用这种多步的沉积刻蚀虽然能够改善HDP的填充能力,但是会使工艺变得非常复杂,沉积速度变慢,而且随着循环次数的增加,刻蚀对衬底的损伤会变得更加严重。因此O3-TEOS基的亚常压化学汽相沉积(SACVD)工艺再次提出被用于沟槽填充,由于它可以实现保形生长,所以具有很强的填充能力(深宽比>10)。但是由于SACVD是一种热反应过程,所以传统的SACVD生长速度都比较慢,美国应用材料公司AMAT的HARP(High Aspect Ratio Process)采用TEOS ramp-up技术,可以在保证填充能力的条件下,获得较快的生长速度,这使得SACVD代替HDP成为可能。而且随着器件尺寸的减小,器件对等离子造成的损伤越来越敏感,SACVD由于是一种纯热过程,所以在45nm以后它比HDP有更多的优势。
目前主要用于STI与PMD绝缘介质的填充。STI过程因为没有温度限制,所以可以通过高温540℃获得高质量高填充能力的薄膜,而PMD由于有使用温度限制,一般采用400℃沉积温度。
由于SACVD是一种热反应过程,一般来讲,低的沉积速度和高的O3/TEOS比值将获得较高的填充能力。AMAT的HARP采用三步沉积法,通过调节O3/TEOS比例获得较好的填充效果同时提高沉积速率(见图4.20):第一步是TEOS ramp up的过程,在沉积的起始阶段,保持非常高的O3/TEOS比例,以较慢的速度得到非常薄的成核层;第二步在较低的速度下保证填满整个STI沟槽间隙。因此,把第一步与第二步中的O3/TEOS比值设计得很高,到第三步时,继续提高反应中TEOS的流量,从而得到更高的沉积速率。

图4.20 HARP沉积中TEOS, spacing随时间的变化
2.SACVD填充对沟槽轮廓的要求
然而,HARP工艺的填充能力不仅受沉积中O3/TEOS比值的影响,更受到沟槽轮廓的强烈影响。以STI为例,SACVD沉积的保形性很高,所以HARP工艺主要采用坡度≤86°的V形沟槽形貌,保证STI沟槽的上端处于开口状态,以完成自底向上的填充(见图4.21)。V形STI可以很容易获得良好的HARP填充效果。而U形的或凹角沟槽形貌会导致在STI被HARP薄膜填满之前,STI沟槽的上端边角早就被堵塞了,结果就会在沟槽内部形成锁眼或裂缝。在处理U形或凹角STI形貌时,不存在一种能够克服填充问题的简便方法。很难通过HARP工艺的一些改进来减轻U形或凹角沟槽形貌中的锁眼(keyhole)。

图4.21 用于HARP填充的理想沟槽形貌
3.SACVD沉积后的高温退火[3]
由于SACVD形成的SiO2薄膜质量较差,所以在用于浅沟槽隔离时,在薄膜沉积完成后需要进行高温的退火以提高薄膜的密度和吸潮性。目前退火主要包括:水蒸气退火+N2干法退火或N2干法退火。在高温退火的过程中,由于薄膜中存在氧(薄膜中残存的或吸潮形成的O-H键),沟槽间的有源区会被进一步氧化而使得有源区面积损失;而水蒸气退火更会使得活性Si面积损耗得更加严重。可以通过降低蒸气退火的温度或/和减少退火时间来减轻这个问题(见图4.22)。通过在STI沟槽侧壁上插入SiN衬垫也可以预防损失,同时退火条件对HARP填充能力也有一些影响。由于在干法退火后HARP薄膜大量收缩,所以有时在沟槽内部可以发现裂缝。与此相反,蒸气退火可使HARP收缩减少,从而获得更好的填充效果。

图4.22 高温退火造成的活性硅的损耗
4.SACVD的应力
与具有压缩薄膜应力的HDP不同,空白片沉积的HARP薄膜具有拉伸应力,经过高温退火后,应力由拉伸转为压缩(见图4.23)。但是对于图形化的硅片,AMAT[3]通过测定图形化后硅片的弯曲程度,分别得到薄膜沉积后,退火后以及化学机械抛光后的硅片所受应力状态,如图4.24所示。沉积后与退火后结果与空白片结果类似,但是机械抛光后HDP会产生一个非常高的压应力,但是HARP会对有源区产生拉应力,而且退火温度也会对拉应力大小产生影响。

图4.23 540℃ HARP空白片的薄膜应力-温度曲线

图4.24 图形化硅片在不同条件下的应力
由HARP STI引起的拉伸应变可能是由两方面的原因造成的。对该应力的回滞研究(见图4.23)表明当退火温度上升时,HARP薄膜应力将变得更加抗延伸,这将给活性Si带来拉伸应变。即使冷却后HARP薄膜压缩在一起时,这种张力应变仍然被记忆并保留在Si中。其次,HARP薄膜将在退火后收缩,但HDP薄膜不会。退火后HARP薄膜被限制在沟槽中进行收缩,为Si提供了另一种强大的拉伸应变,这也进一步增强了NFET和PFET的载流子移动性,尤其是窄宽度晶体管器件[3]。这也是采用HARP代替HDP的另一优势。
5.SACVD薄膜生长的选择性
像所有其他SACVD O3-TEOS工艺一样[4~6], HARP沉积工艺也对衬底材料表现出了很高的敏感性。如表4.7所示,HARP在SiO2上比在SiN上的沉积速率慢。这种敏感性与温度、O3/TEOS比例以及压力有非常强的关系,所以当评价HARP在CMP的沟槽中的loading时,HARP的表面敏感性也需要被考虑在内。
表4.7 HARP对不同衬底的表面敏感性[7]

Qimonda等公司[8]报道了利用SATEOS对衬底的敏感性,实现了薄膜在沟槽中选择性生长,从而得到从下到上的填充效果。但是具体通过什么处理以及采用什么样的条件,并没有详细的报道。
随着器件尺寸的继续减小,seam对填充的影响会越来越大,应用材料公司在HARP系统中引入H2O将是32nm或22nm的发展方向,另外通过刻蚀对HARP沉积中的轮廓进行修正也变得越来越重要。