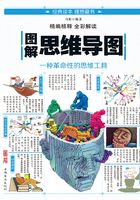
第二节 机器不转动,工厂也能赚钱
据参观丰田工厂的人说,丰田工厂和其他工厂一样,机器一行一行地排列着。但有的在运转,有的都没有启动,很显眼。
于是有的参观者疑惑不解:“丰田公司让机器这样停着也赚钱?”
不错,机器停着也能赚钱!这是由于丰田汽车公司创造了这样的工作方法:必须做的工作要在必要的时间去做,以避免生产过量的浪费,避免库存的浪费。
原来,不当的生产方式会造成各种各样的浪费,而浪费又是涉及提高效能增加利润的大事。
丰田公司对浪费做了严格区分,将浪费现象分为以下7种:
(1)生产过量的浪费;
(2)窝工造成的浪费;
(3)搬运上的浪费;
(4)加工本身的浪费;
(5)库存的浪费;
(6)操作上的浪费;
(7)制成次品的浪费。
丰田公司又是怎样避免和杜绝库存浪费的呢?许多企业的管理人员都认为,库存比以前减少一半左右就无法再减了,但丰田公司就是要将库存率降为零。为了达到这一目的,丰田公司采用了一种“防范体系”。
就以作业的再分配来说,几个人为一组干活,一定会存在有人“等活”之类的窝工现象存在。所以,有人就认为,对作业进行再分配,减少人员以杜绝浪费并不难。
但实际情况并非完全如此,多数浪费是隐藏着的,尤其是丰田人称之为“最凶恶敌人”的生产过量的浪费。丰田人意识到,在推进提高效率缩短工时以及降低库存的活动中,关键在于设法消灭这种过量生产的浪费。
为了消除这种浪费,丰田公司采取了很多措施。以自动化设备为例,该工序的“标准手头存活量”规定是5件,如果现在手头只剩3件,那么,前一道工序便自动开始加工,加到5件为止。
到了规定的5件,前一道工序便依次停止生产,制止超出需求量的加工。后一道工序的标准手头存活量是4件,如减少1件,前一道工序便开始加工,送到后一道工序。后一道工序一旦达到规定的数量,前一工序便停止加工。
像这样,为了使各道工序经常保持标准手头存活量,各道工序在联动状态下开动设备。这种体系就叫做“防范体系”。在必要的时刻,一件一件地生产所需要的东西,就可以避免生产过量的浪费。
在丰田生产方式中,不使用“运转率”一词,全部使用“开动率”,而“开动率”和“可动率”又是严格区分的。所谓开动率就是,在一天的规定作业时间内(假设为8小时),有几小时使用机器制造产品的比率。假设有台机器只使用4小时,那么这台机器的开动率就是50%。开动率这个名词是表示为了干活而转动的意思,倘若机器单是处于转动状态即空转,即使整天开动,开动率也是零。
“可动率”是指在想要开动机器和设备时,机器能按时正常转动的比率。最理想的可动率是保持在100%。为此,必须按期进行保养维修,事先排除故障。由于汽车的产量因每月销售情况不同而有所变动,开动率当然也会随之而发生变化。如果销售情况不佳,开动率就下降;反之,如果订货很多,就要长时间加班或倒班,有时开动率为100%,有时甚至会达120%或130%。丰田完全按照订货来调配机器的“开动率”,将过量生产的浪费情况减少到最低,才出现了即使机器不转动也能赚钱的局面。
讲到这里,不得不提戴尔公司的“零库存管理模式”,它与丰田的“防范体系”颇有异曲同工之妙。
戴尔公司走在物流配送时代的前列。分析家们分析戴尔成功的诀窍时说:“戴尔总支出的74%用在材料配件购买方面,2000年这方面的总开支高达210亿美元。如果我们能在物流配送方面降低0.1%,就等于我们的生产效率提高了10%。”
戴尔公司分管物流配送的副总裁迪克·亨特说:“我们只保存可供5天生产的存货,而我们的竞争对手则保存30天、45天,甚至90天的存货。这就是区别。”
戴尔是怎样做到的呢?原来,这一切的实现源于互联网生产与客户紧密相连。
工厂的多数生产过程都由互联网控制,就连几辆鸣着喇叭在厂房里穿行的叉车都是由无线电脑来控制其装卸活动的。
公司30万平方米的厂房不仅是戴尔追求效能的标志,而且是公司不断缩短从顾客订货至成品装车这段时间的标志。目前的目标是5~7小时。
由于戴尔公司按单定制,因此,这些库存一年可周转15次。相比之下,其他依靠分销商和转销商进行销售的竞争对手,其周转次数还不到戴尔公司的一半,这种快速的周转能使总利润多出1.8%~3.3%。
据此,我们可以用一幅思维导图对丰田和戴尔的成功之道进行对比分析。
