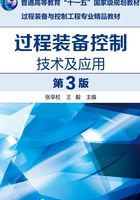
2.4 单回路控制系统
单回路控制系统又称简单控制系统,是指由一个被控对象、一个检测元件及变送器、一个控制器和一个执行器所构成的闭合系统,其方框图如图1-3所示。单回路控制系统结构简单、易于分析设计,投资少、便于施工,并能满足一般生产过程的控制要求,因此,在生产过程中得到了广泛的应用。
2.4.1 单回路控制系统的设计
设计一个单回路控制系统的主要步骤概括如下。
ⅰ.对被控对象做全面的了解,除被控对象的动静态特性外,对于工艺过程、设备等也需要做比较深入的了解。
ⅱ.综合考虑位置、技术和噪声等因素,选择测量传感器类型和数目。
ⅲ.综合考虑位置、技术、噪声和功率等因素,选择执行机构的类型和数目。
ⅳ.对被控对象、执行器和测量变送器建立线性模型。
ⅴ.制定一个基于超前-滞后校正补偿或者比例积分微分控制的初步设计,如果满足要求,直接跳至步骤ⅷ。
ⅵ.考虑通过改变过程本身来改进闭环控制性能。
ⅶ.基于最优控制或其他标准尝试极点配置设计。
ⅷ.对系统进行模拟,包括非线性、噪声、和参数变化的效果。如果性能不满意,回到步骤ⅰ并重复上述步骤。
ⅸ.进行样机测试。如果不满意,回到步骤ⅰ并重复上述步骤。
概括而言,首先要确定控制目标。在此基础上,确定正确的控制方案,包括合理地选择被控变量与操纵变量;选择配套的一次仪表,包括合适的检测变送元件及检测位置;选用恰当的执行器、控制器以及控制器控制规律等;还要设计报警和连锁保护系统。最后是控制系统的调试和投运,最重要的是将控制器的参数整定到最佳值。
(1)被控变量的选择
被控变量是生产过程中希望保持在定值或按一定规律变化的过程参数。影响一个生产过程正常操作的因素很多,但并非所有的影响因素都要进行控制,而且也不可能都加以控制。作为被控变量,它应是对提高产品质量和产量、促进安全生产、提高劳动生产率、节能等具有决定作用的工艺变量。这就需要在了解工艺过程、控制要求的基础上,分析各变量间的关系,合理选择被控变量。以苯-甲苯二元精馏塔为例,来说明被控变量选择时应注意的问题。当气、液两相共存时,塔顶产品易挥发组分浓度XD、温度TD和压力p之间是二元函数的关系,XD=f(TD,p),其中的XD是直接反映塔顶产品质量的指标,控制目标是要控制XD。但由于难以找到合适的成分分析仪表或成分分析测量滞后太大,不能及时反映浓度变化,考虑以另一参数作为被控变量,间接控制XD,但选择的这一参数必须与XD是单值函数关系。当温度TD或压力p为定值时,另一个物理量p或TD与XD是单值函数关系,所以,以温度TD或压力p为被控变量。实际精馏过程中,要保持塔压p一定,如果p发生波动,则塔内的气、液两相平衡关系就会遭到破坏,使精馏塔不能工作在最佳工况,影响整个塔的效率和经济性,因此,选择塔顶温度TD为被控变量是较为合理的。这里提出几个选择的基本原则。
ⅰ.作为被控变量,其信号最好是能够直接测量获得,并且测量和变送环节的滞后也要比较小。
ⅱ.若被控变量信号无法直接获取,可选择与之有单值函数关系的间接参数作为被控变量。
ⅲ.作为被控变量,必须是独立变量。变量的数目一般可以用物理化学中的相律关系来确定。
ⅳ.作为被控变量,必须考虑工艺合理性,以及目前仪表的现状能否满足要求。
综上所述,合理选择被控变量是单回路控制系统设计的第一步,同时也是关系到控制方案成败的关键。如果被控变量选择不当,则不管组成什么形式的控制系统,也不管配备多么精良的自动化设备,都不能达到预期的控制效果。
(2)操纵变量的选择
在控制系统中,用来克服干扰对被控变量的影响,实现控制作用的变量就是操纵变量。在化工和炼油生产过程中,最常见的操纵变量是流量,也有电压、转速等。如图2-37所示的换热器,已知被控变量是被加热介质的温度,那么,是选择载热体流量作为操纵变量,还是选择被加热介质的流量作为操纵变量呢?这主要应从工艺合理性以及被控对象的特性方面考虑。
①考虑工艺合理性 对于图2-37所示的换热器,无论哪一个流量发生变化,都会使被控变量(温度)发生变化。从工艺合理性考虑,应选择载热体流量作为操纵变量。因为,被加热介质一般为生产过程中需要使用的物料,用它的变化来克服干扰因素的影响,达到温度控制的目的,势必会影响生产工艺过程中的负荷,甚至影响正常的生产。而载热体是用来加热介质的,它不直接影响生产所需物料量。因此,选择载热体流量作为操纵变量能满足工艺上的合理性。

图2-37 换热器示意图
再看图2-38所示的某物料浓度的控制系统,应选择稀释水流量作为操纵变量,尽量避免选用主物料流量作为操纵变量。

图2-38 浓度控制系统
②考虑被控对象特性 操纵变量与被控变量之间的关系构成了被控对象的控制通道特性;干扰与被控变量之间的关系构成了被控对象的干扰通道特性。在本章第2节被控对象动态特性的内容中曾讲述了不同通道特性参数对控制质量的影响,根据其结论,可以归纳出操纵变量选择的一般原则为:
ⅰ.使被控对象控制通道的放大系数较大,时间常数较小,纯滞后时间越小越好;
ⅱ.使被控对象干扰通道的放大系数尽可能小,时间常数越大越好。
图2-39为炼油和化工生产中最常见的精馏设备。根据工艺需要,选择提馏段某板(一般为温度变化最灵敏的板——灵敏板)的温度作为被控变量,那么,控制系统的任务就是维持灵敏板温度的恒定,使塔底产品的成分满足工艺要求。在这个过程中,影响提馏段灵敏板温度的因素有:进料流量、进料成分、进料温度、回流流量、回流温度、加热蒸汽流量、冷凝器冷却温度以及塔压等。从工艺角度分析可以知道,除回流量和加热蒸汽量外,其他参数都不允许作为操纵变量。根据对象特性对控制质量的影响,在回流量与加热蒸汽量两者之间,选择加热蒸汽量作为操纵变量更为恰当。因为回流量与提馏段温度之间的控制通道时间常数太大,而加热蒸汽量与提馏段温度之间的控制通道时间常数小,滞后小,这样构成的控制系统克服干扰能力强,可以获得良好的控制质量。

图2-39 精馏过程示意图
1—精馏塔;2—蒸汽加热器
(3)检测变送环节的影响
检测变送环节在控制系统中起着获取信息和传送信息的作用。一个控制系统如果不能正确及时地获取被控变量变化的信息,并把这一信息及时地传送给控制器,就不可能及时有效地克服干扰对被控变量的影响,甚至会产生误调、失调等危及生产安全的问题。
①纯滞后 在过程控制中,由于检测元件安装位置的原因会产生纯滞后。如图2-40所示为一pH值控制系统,由于检测电极不能放置在流速较大的主管道,只能安装在流速较小的支管道上,使得pH值的测量引入纯滞后τ0。
(2-91)

图2-40 pH值控制系统
式中 l1,l2——主管道、支管道的长度;
u1,u2——主管道、支管道内流体的速度。
图2-41所示是一个用蒸汽来控制水温的系统,蒸汽量的变化一定要经过长度为L的路程以后才能反映出来。

图2-41 蒸汽直接加热系统
这是由于蒸汽作用点与被控变量的测量点间相隔一定距离所致。如果水的流速为v,则蒸汽量变化引起的温度变化需经过一段时间τ=L/v才表现出来,τ0就是纯滞后时间。
纯滞后使测量信号不能及时地反映被控变量的实际值,从而降低了控制系统的控制质量。由检测元件安装位置所引入的纯滞后是不可避免的,因此,在设计控制系统时,只能尽可能地减小纯滞后时间,唯一的方法就是正确选择安装检测点位置,使检测元件不要安装在死角或容易结焦的地方。当纯滞后时间太长时,就必须考虑采用复杂控制方案。
②测量滞后 是指由测量元件本身特性所引起的动态误差。当测量元件感受被控变量的变化时,要经过一个变化过程,才能反映被控变量的实际值,这时测量元件本身就构成了一个具有一定时间常数的惯性环节。例如,测温元件测量温度时,由于存在传热阻力和热容,元件本身具有一定的时间常数Tm,因而测温元件的输出总是滞后于被控变量的变化。如果把这种测量元件用于控制系统,控制器接收的是一个失真的信号,不能发挥正确的作用,因而影响控制质量。
克服测量滞后的方法通常有两种:一是尽量选用快速测量元件,以测量元件的时间常数为被控对象的时间常数的十分之一以下为宜;二是在测量元件之后引入微分作用。在控制器中加入微分控制作用,使控制器在偏差产生的初期,根据偏差的变化趋势发出相应的控制信号。采用这种超前补偿作用来克服测量滞后,如果应用适当,可以大大改善控制质量。需要指出的是,微分作用对克服纯滞后是无能为力的,因为在纯滞后时间里,参数没有发生变化,控制器中以参数变化速度为输入的微分控制器,其输出也等于零,起不到超前补偿作用。
③传递滞后 即信号传输滞后,主要是由于气压信号在管路传送过程中引起的滞后(电信号的传递滞后可以忽略不计)。
在采用气动仪表实现集中控制的场合,控制器和显示器均集中安装在中心控制室,而检测变送器和执行器安装在现场。在由测量变送器至控制器和由控制器至执行器的信号传递中,由于管线过长就形成了传递滞后。由于传递滞后的存在,控制器不能及时地接受测量信号,也不能将控制信号及时地送到执行器上,因而降低了控制系统的控制质量。
传递滞后总是存在的,克服或减小信号传递滞后的方法有:尽量缩短气压信号管线的长度,一般不超过300m;改用电信号传递,即先用气电转换器把控制器输出的气压信号变成电信号,送到现场后,再用电气转换器变换成气压信号送到执行器上;在气压管线上加气动继动器(气动放大器),或在执行器上加气动阀门定位器,以增大输出功率,减少传递滞后的影响;如果变送器和控制器都是电动的,而执行器采用的是气动执行器,则可将电气转换器靠近执行器或采用电气阀门定位器;按实际情况采用基地式仪表,以消除信号传递上的滞后。
测量滞后和传递滞后对控制系统的控制质量影响很大,特别是当被控对象本身的时间常数和滞后很小时,影响就更为突出,在设计控制系统时必须注意这个问题。
(4)执行器的影响
执行器是过程控制系统中的一个重要环节,其作用是接受控制器送来的控制信号,控制管道中介质的流量(改变操纵变量),从而实现生产过程的自动控制。执行器通常为控制阀,包括执行机构和阀两个部分。由于控制阀直接与介质接触,当在高温、高压、深冷、强腐蚀、高黏度、易结晶、闪蒸、气蚀等各种恶劣条件下工作时,其重要性就更为突出。如果执行器选择不当或维护不善,常常会使整个系统不能可靠工作,或严重影响控制系统的质量。在设计控制系统时,按照生产过程的特点、安全运行和推动力等来选用气动、电动或液动执行器(化工过程控制中用得最多的是气动薄膜控制阀);根据被控变量的大小选择控制阀的流通能力;从生产安全的角度选取控制阀的气开或气关形式;从被控对象的特性、负荷的变化情况等选择控制阀的流量特性等(详见本书第4章中的有关内容)。
从广义对象的角度考虑,执行器可以看作是被控对象的一部分,其动态特性相当于在被控对象中增加了一个容量滞后环节。当执行器的时间常数TV与被控对象的时间常数接近时,将会使广义对象的容量滞后显著增大,这对于控制是非常不利的。
2.4.2 控制器参数的工程整定
当一个控制系统设计安装完成后,系统各个环节以及被控对象各通道的特性就不能再改变了,而唯一能改变的就是控制器的参数,即控制器的比例度δ、积分时间TI和微分时间TD。通过改变这三个参数的大小就可以改变整个系统的性能,获得较好的过渡过程和控制质量。控制器参数整定的目的就是按照已定的控制系统,求取使控制系统质量最好的控制器参数值。
控制器参数的整定方法有很多种,通常可分为两大类:理论计算整定法和工程整定法。根轨迹法、频率响应法、偏差积分准则(ISE、IAE或ITAE)等方法都属于理论计算整定法。这些方法的共同特点是:必须知道被控对象的特性,然后通过理论计算来求取控制器的最佳参数。但是,在缺乏足够的被控对象特性资料的情况下,使用理论计算整定法很难得到准确可靠的控制器参数;而且对复杂过程来讲,它的计算方法烦琐、工作量大,比较费时。因此,理论计算整定法一般适用于科研工作中做方案比较。工程上常常从实际出发,使用另一种方法即工程整定法。所谓工程整定法,就是避开被控对象的特性和数学描述,在被控对象运行时,直接在控制系统中,通过改变控制器参数,观察被控变量的过渡过程,来获取控制器参数的最佳数值。工程整定法是一种近似的方法,所得到的控制器参数不一定是最佳数值,但却很实用。工程整定法实质上也有一定的理论依据,因此在工程实践中得到了广泛的应用。下面介绍几种简单控制系统控制器参数的工程整定方法,包括经验试凑法、临界比例度法和衰减曲线法。
(1)经验试凑法
若将控制系统按液位、流量、温度和压力等参数来分类,属于同一类别的系统,其对象特性比较接近,所以无论是控制规律的形式还是所整定的参数均可相互参考。经验试凑法就是根据被控变量的性质,在已知合适的参数(经验参数)范围内选择一组适当的值作为控制器当前的参数值,然后直接在运行的系统中,人为地加上阶跃干扰,通过观察记录仪表上的过渡过程曲线,并以比例度、积分时间、微分时间对过渡过程的影响为指导,按照某种顺序反复试凑比例度、积分时间、微分时间的大小,直到获得满意的过渡过程曲线为止。
①温度系统 其对象容量滞后较大,被控变量受干扰作用后变化迟缓,一般选用较小的比例度,较大的积分时间,同时要加入微分作用,微分时间是积分时间的四分之一。
②流量系统 是典型的快速系统,对象的容量滞后小,被控变量有波动。对于这种过程,不用微分作用,宜用PI控制规律,且比例度要大,积分时间可小。
③压力系统 通常为快速系统,对象的容量滞后一般较小,其参数的整定原则与流量系统的整定原则相同。但在某些情况下,压力系统也会成为慢速系统,图2-42所示即为一慢速压力系统。在该系统中,通过控制换热器的冷剂量来影响压力,因此热交换的动态滞后和流量滞后都会包含在压力系统中,从而构成一个由多容对象组成的慢速过程,这类系统的参数整定原则应参照典型的温度系统。

图2-42 慢速压力系统
④液位系统 其对象时间常数范围较大,对只需要实现平均液位控制的地方,宜用纯比例控制,比例度要大,一般不用微分作用,要求较高时应加入积分作用。
各种不同控制系统的经验参数见表2-3。
表2-3 控制器参数经验数据

经验试凑法简单可靠,容易掌握,适用于各种系统。特别是对于外界干扰作用较频繁的系统,采用这种方法更为适合。但这种方法对于控制器参数较多的情况,不易找到最好的整定参数。
(2)临界比例度法
临界比例度法又称Ziegler-Nichols方法,早在1942年已提出。它首先求取在纯比例作用下的闭环系统达到等幅振荡过程时的比例度δK和振荡周期TK,然后根据经验公式计算出相应的控制器参数。通常将等幅振荡下的比例度和振荡周期分别称为临界比例度和临界周期。临界比例度法便于使用,而且在大多数控制回路中能得到较好的控制品质。
临界比例度法整定参数的具体步骤是:首先将控制器的积分作用和微分作用全部除去,在纯比例的情况下,按比例度δ从大到小的变化规律,对应于某一δ值做小幅度的设定值阶跃干扰,直到获得等幅振荡过渡过程曲线,如图2-43所示。这时的比例度为临界比例度δK,振荡周期即为临界周期TK,临界周期TK可在图2-43中过渡过程曲线上求取。最后根据表2-4所给出的经验公式计算出控制器各参数的整定数值。

图2-43 临界振荡曲线
表2-4 临界比例度法经验算式

表2-4列出的PID参数整定算式是以闭环系统得到4∶1衰减比,并且有合适的超调量(或最大偏差)为目标的。
最后要指出的是,使用临界比例度法整定控制器参数有两个条件:一是工艺允许被控变量做等幅振荡;二是在获取等幅振荡曲线时,应特别注意,不能使控制阀出现全关、全开的极限状态。否则由此获得的等幅振荡实际上是“极限循环”,从线性系统概念上说系统早已发散了。
例2-5 对简单控制系统中的PI控制器采用临界比例度法进行参数整定,当比例度为10%时系统恰好产生等幅振荡,这时的等幅振荡周期为30s,问该控制器的比例度和积分时间应选用表2-5所列何组数值整定为最好?
表2-5 控制器的比例度和积分时间

解 临界比例度法考虑的实质是通过现场试验找到等幅振荡的过渡过程,得到临界比例度和等幅振荡周期。其具体整定方法,首先用纯比例作用将系统投入控制,然后逐步减小比例度,使系统恰好达到振荡和衰减的临界状态,即等幅振荡状态,记下这时的比例度δK和振荡周期TK,则控制器的比例度和积分时间可按表2-4求出
δ=2.2δK=2.2×10%=22%
TI=0.85TK=0.85×30=25.5(s)
所以,控制器参数应选表2-5中D组数值。
(3)衰减曲线法
在一些不允许或不能得到等幅振荡的情况下,可考虑采用修正方法——衰减曲线法。它与临界比例度法的唯一差异仅在于临界比例度法是以在纯比例下获得4∶1衰减振荡曲线为参数整定的依据,而衰减曲线法只需在比例作用下获得4∶1衰减振荡过渡过程曲线即可,记下此时的比例度δs,并在4∶1曲线上求得振荡周期Ts。然后根据表2-6给出的经验公式,求出相应的比例度、积分时间和微分时间。
表2-6 衰减曲线法经验公式

表2-6给出的经验公式适用于多数系统。当控制器参数调整到计算值后,如果过渡过程仍不够理想,则可根据曲线振荡的情况,对控制器参数再做适当调整。
衰减曲线法的整定方法简单、可靠,而且整定的质量较高,目前得到了广泛的应用。但这种方法要求在工艺稳定的条件下通过改变设定值信号加入阶跃干扰,工艺上的其他干扰要设法免除,否则,记录曲线将是几种外界干扰作用同时影响的结果,不可能得到正确的4∶1衰减曲线上的比例度和振荡周期。因此,衰减曲线法适用于干扰较小的系统。另外,设定值信号的干扰幅度不应超出工艺允许的范围。
以上介绍了控制器参数的三种工程整定方法。它们都不需要预先知道被控对象的特性,而是直接在闭合的系统中进行整定。如果预先知道被控对象特性,就可以根据理论分析计算的方法求出控制器参数的数值,再在闭合系统投运中进行适当调整,将会更方便、迅速和准确。另外需要指出的是,对控制器参数的整定是在某一工作状态下进行的,即在一定的工艺操作条件和一定的负荷下进行的。那么一组控制器参数在一种工作状态下是最佳的,而在另一种工作状态下就不一定是最佳的。所以,当工艺操作条件或负荷发生较大变化时,控制器参数往往需要重新整定。
总之,上述所提到的方法一般都可以工作得较好,特别是以人工智能为基础的专家系统自整定的PID控制系统在过程工业控制的应用中取得了明显的实效,而且必将得到更广泛的应用。