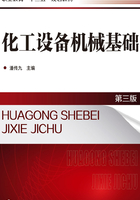
2.4 管式加热炉和废热锅炉
2.4.1 管式加热炉
随着化学工业的迅速发展,加热炉越来越受到人们的重视。现代化工生产中通常使用的加热炉是管式加热炉。管式加热炉不仅消耗着大量能量,而且在石油裂解、转化或合成氨反应中起到核心设备的作用,支配着整个工厂产品的质量、效率、能耗和操作周期等。因而,了解其结构,懂得如何选择以及如何使管式加热炉处于最佳的工作状态,对化工行业的工作者有着十分重要的意义。
管式加热炉是利用燃料在炉膛内燃烧时产生的高温火焰与烟气作为热源,加热在炉管内高速流动的物料,使其在管内进行化学反应,或达到后续工艺过程中所需的温度。管式加热炉已成为近代炼油工业和石油化学工业中必不可少的工艺设备之一。
2.4.1.1 管式加热炉的一般结构
管式加热炉一般由辐射室、对流室、余热回收系统、燃烧器及通风系统组成,如图2-57所示。其结构通常包括钢结构、炉墙(内衬)、炉管、燃烧器、孔类配件等。

图2-57 管式加热炉的一般结构
(1)辐射室
辐射室是通过火焰或高温烟气进行辐射传热的部分,也是加热炉进行热交换的主要场所。辐射室的温度高达600~1600℃,热负荷占全炉的70%~80%,是全炉的最重要部位。烃蒸气转化炉、乙烯裂解炉等,其反应和裂解过程全都由辐射室来完成。可以这样认为,一台加热炉的优劣主要以辐射室的性能好坏来判断。
在辐射室内,火焰或高温烟气通过炉管进行传热加热炉管内介质。由于以辐射热为主,故称炉管为辐射管。辐射室内的炉管直接承受火焰辐射冲刷,温度高,要求材料应具有足够的高温强度和高温化学稳定性。
(2)对流室
对流室是紧接辐射室依靠由辐射室排出的高温烟气与物料对流进行传热的部分。烟气以较高速度冲刷炉管的管壁,进行有效的对流传热,其热负荷占全炉的20%~30%。对流室一般布置在辐射室之上。有的则单独放置在地面上,如大型方炉。为了尽量提高传热效果,多数加热炉在对流室采用钉头管和翅片管。
严格地讲,在对流室中也有一部分辐射热交换存在,而且有时还占有较大的比例(但是,就其比例而言,还是对流传热起支配作用)。
(3)余热回收系统
余热回收系统指从离开对流室的烟气中进一步回收余热的部分。余热回收方法有两类:一类是靠预热燃烧用空气来回收热量,这些回收的热量被热空气再次带回炉中;另一类是采用与本炉子完全无关的另一系统的流体来回收排烟的余热。前者称为空气预热方式;后者通常采用水回收,称为废热锅炉方式。空气预热方式有直接安装在对流室上面的固定管式空气预热器和单独放在地面上的回转式空气预热器等形式。
余热回收系统中的新技术之一是将空气预热器设置为非冷凝式和冷凝式两段。在冷凝段中实现烟气中含酸水蒸气的部分冷凝,不但回收烟气低温显热,还回收冷凝时的潜热,提高加热炉热效率,节约能源。其排烟温度可降低到100℃左右。
(4)燃烧器
燃烧器的作用是完成燃料的燃烧过程,为加热炉的热交换提供热量,是加热炉的重要组成部分。管式加热炉只燃烧燃料气和燃料油,所以不需要像烧煤的加热炉那样配有复杂的辅助系统,其结构较为简单。
燃烧器由燃料喷嘴、配风器、燃烧道三部分组成。燃烧器按所用燃料不同可分为三类:燃油燃烧器、燃气燃烧器和油-气联合燃烧器。燃烧器的性能直接影响燃烧的质量和加热炉的热效率。操作时,应特别注意火焰要保持刚直有力,调整火嘴尽可能使炉膛受热均匀,避免火焰舔及炉管,并实现低氧燃烧。
为保证燃烧质量和热效率,还必须配置可靠的燃料供应系统和良好的空气预热系统。
(5)通风系统
通风系统的任务是将燃烧用的空气导入燃烧器,并将废烟气引出加热炉。它分为自然通风方式和强制通风方式两种。前者依靠烟囱本身形成的抽力,不消耗机械能;后者要使用风机,消耗机械能。
过去,大多数加热炉都采用自然通风方式,烟囱通常安装在炉顶。后来,随着加热炉结构的复杂化,炉内烟气阻力增大,加之提高热效率的需要,采用强制通风的方式日趋普遍。
(6)主要结构
①钢结构。钢结构是管式加热炉的承载骨架。其基本元件是各种型钢,通过焊接或螺栓连接构成管式加热炉的骨架。其他辅助构件则依附于钢结构。
②炉墙。管式加热炉的炉墙结构主要有三种类型:耐火砖结构、耐火混凝土结构和耐火纤维结构。其中耐火砖结构又分为砌砖炉墙、挂砖炉墙和拉砖炉墙三种。砌砖炉墙是按照一定的要求将耐火砖、保温砖、红砖等进行整体砌筑的炉墙。挂砖炉墙是利用挂砖架分段承重的结构,炉墙较薄,其高度不受限制。拉砖炉墙是将炉墙砖结构与炉墙钢结构拉接起来的一种结构形式,得到了广泛应用,尤其是温度较高的管式加热炉,如裂解炉和转化炉。
③炉管。管式加热炉的炉管是物料摄取热量的媒介。根据受热方式不同可分为辐射炉管和对流炉管,前者设置在辐射室内,后者设置在对流室内。为强化传热,对流管往往采用翅片管或钉头管,其安装方式多采用水平安装。
④其他配件。管式加热炉的配件较多,主要有看火孔、点火孔、炉用人孔、防爆门、吹灰器、烟囱挡板等。
2.4.1.2 管式加热炉的类型
各种管式加热炉通常可按外形和用途来分类。
2.4.1.2.1 按外形分类
按管式加热炉的外形大致可分为四类:箱式炉、立式炉、圆筒炉、大型方炉。这种划分方法按辐射室的外观形状区分,而与对流室无关。箱式炉的辐射室为一箱子状的六面体。立式炉的辐射室为直立状的六面体,但宽度要窄一些,通常两侧墙的间距与炉膛高度之比约为1∶2。
(1)箱式炉
①横管大型箱式炉和立管大型箱式炉。如图2-58、图2-59所示,这两种炉型结构基本一致,只是一为横管、一为立管。它们的优点是只要增加中央的隔墙数目,即可在炉膛体积强度不变的前提下,“积木组合式”地把加热炉尺寸放大。该炉型适合用于大型炉;其主要缺点是敷管率低,炉管需要用合金材料吊挂,造价高,需要独立设置烟囱。

图2-58 横管大型箱式炉

图2-59 立管大型箱式炉
②顶烧式炉。如图2-60所示,这种炉型的燃烧器和辐射炉管呈交错排列,单排炉管承受双面辐射,管子沿圆周各方向的热分布均匀。燃烧器设置在加热炉的顶部,而对流室和烟囱则设置在地面上。其缺点是加热炉体积大,造价较高,若用在单纯的加热工艺上是很不经济的。合成氨厂常用它作为大型烃蒸气转化炉的炉型,其运转情况良好。

图2-60 顶烧式炉
(2)立式炉
①底烧横管立式炉。如图2-61所示,其传热方式与条式炉相似,只是在造型上采用了立式炉的特点。其结构设计为:炉管布置在两侧壁上,而中间部分则布置一列底烧的燃烧器,烟气由辐射室经对流室和烟囱一直上行。其燃烧器的能量较小,数量较多,间距较小,从而在加热炉中央形成一道火焰膜,以增强辐射传热效果。当今使用的立式炉多数采用这一形式。

图2-61 底烧横管立式炉
②附墙火焰立式炉。如图2-62所示,这种立式炉炉膛中有一道火墙,火焰附墙而上,把墙壁烧红,从而增加了炉膛内热辐射体的辐射面积,提高炉管的受热强度。从辐射传热效果而言,它比底烧横管立式炉传热均匀。同时,中央火墙将辐射室分为两室,因此每室可各走一路油品,可以分别调节温度。

图2-62 附墙火焰立式炉
③环形管立式炉。如图2-63所示,这种加热炉的内部结构是用多根U形炉管把火焰包围起来,因而适用于炉管路数多且要求管内压力降小的场合。当加热炉的热负荷增大时,可设计成图2-64所示的由两个甚至三个U形管组成的结构。

图2-63 环形管立式炉

图2-64 多个环形管立式炉
④立管立式炉。如图2-65所示,这是我国首创的炉型。该炉型的炉管沿墙直立排列,因而与横管立式炉相比,可节省大量的高铬镍材料的管架,同时又保留了立式炉的优点,常作为大热负荷加热炉的炉型。

图2-65 立管立式炉
⑤无焰燃烧炉。如图2-66所示,这种炉型属于单排管双面辐射炉型。无焰燃烧炉的侧壁装有许多小能量的气体无焰燃烧器,使整个侧壁成为均匀的辐射墙面,因而有优越的加热均匀性,并可分区调节温度,它是乙烯裂解和烃类蒸气转化最合适的炉型之一。但是其造价昂贵,若用于纯加热工艺上非常不经济。另一缺点是该炉型只能烧气体燃料。

图2-66 无焰燃烧炉
(3)圆管炉
①螺旋管式炉、纯辐射式炉。这种炉型主要应用在加热炉热负荷很小、效率要求不高的场合,其结构最简单,造价也最便宜。
图2-67所示为螺旋管式炉,其炉管盘绕成螺旋状。它虽属于立式炉型,但由于螺旋管的开角不大,因而其管内特性更接近于水平管,管内物料能完全排空,且管内流体阻力较小。这种加热炉的主要优点是便于制造,被加热介质通常只在一连续的螺旋管内流动,即管程数为1。

图2-67 螺旋管式炉
图2-68所示为纯辐射式炉,该炉膛内没有设置对流室,燃烧器安放在炉底,炉管沿炉墙直立排成一圈。这种加热炉结构简单,重量较轻,但热效率低。

图2-68 纯辐射式炉
②辐射-对流式炉。如图2-69所示,是普遍采用的炉型。其结构特点是在辐射室的顶部增设了水平管式对流室,采用钉头管和翅片管,故热效率较高。其制造及施工简单、造价低,是管式加热炉中应用最广泛的炉型。但该炉型不适合用于大型炉的结构,其原因是放大之后的炉膛内部过于空旷,导致炉膛体积发热强度急剧下降。为了克服这一缺点,最好的方法是在炉膛内增添炉管,以提高炉膛内部空间的利用率。

图2-69 辐射-对流式炉
(4)大型方炉
图2-70所示为大型方炉,这种加热炉用两排炉管把炉膛分成若干小间,每间内设置一或两个大容量高强燃烧器。炉膛可以沿两个方向进行分隔,称为十字交叉分隔法。该炉型在结构设计时通常是把对流室单独设置在地面上,把几台加热炉的烟气用烟道汇集起来,然后送进一个公共的对流室或废热锅炉。这种加热炉结构简单,节省占地,便于回收余热,容易实现多炉集中排烟,减轻大气污染。该炉型是专为超大型加热炉而开发的。

图2-70 大型方炉
2.4.1.2.2 按用途分类
管式加热炉按用途可大致分为以下几类。
(1)炉管内进行化学反应的加热炉
这种加热炉的管内发生吸热化学反应。按复杂程度来讲,它代表了加热炉技术的最高水平。属于这种加热炉的有两种:炉管内装有催化剂,如烃类蒸气转化炉;炉管内不装催化剂,如乙烯裂解炉。无论是哪一种,它不仅要求从炉内取热,而且要满足各段管道化学反应及正常运行的各种条件,如温度、压力、流量和热输入量等。
(2)加热液体的加热炉
①管内无相变化,是单纯的液体加热炉。这种炉子只把工艺液体加热到其沸点以下(如温水加热、液相载热体加热等),它加热的终温低,管内结焦的腐蚀也小,操作容易。
②炉管入口为液相、出口为气液混相的加热炉。这种工况多数出现在炼油过程中,此时往往要求被加工的流体以气、液混相的状态进入蒸馏塔等。在全部的工艺加热炉中,它的数量最大。其关键的参数是吸热量、汽化率、压力降和温度等。
③管子进口为液相、出口全部汽化的加热炉。这种加热炉是反应器的进料加热炉,它把液体完全汽化,并加热至一定温度,然后送入后续反应器中。由于反应器的操作条件在运转期间将随催化剂活性而发生变化,故这种加热炉的操作温度和压力等也往往变化很大,必须掌握操作规律,以防止裂解和结炭发生。
(3)气体加热炉
这种加热炉主要用于水蒸气的过热和工艺气体的预热。它是纯气相,多在较高温度下操作,因而在一般情况下结焦的可能性不大。该炉型在结构设计上要注意的是当气体量很大时,炉管的路数很多,应保证各路气体流动均匀、防止偏流。
(4)加热混相流的加热炉
这种加热炉常用于加氢精制、加氢裂化等装置的反应器进料加热。由于管内流体从加热炉的入口端起就是气、液混相,故与上述纯气体加热炉相比更难保证各路流量的均匀。在使用中更要重视管径、管内质量流速、盘管道数的影响,以及管内流动状态的判断等技术。
2.4.2 废热锅炉
化工生产中的能耗很大,如何提高能量的有效利用率是化工生产中的一个重要问题。无论从企业生存、技术进步、行业发展还是国家战略、国际竞争哪个角度看,都必须持续推进节能降耗。GB 21344—2015《合成氨单位产品能源消耗限额》对不同原料生产合成氨的能耗给出了限定值,对新建企业提出了更严格的准入值,还给出了先进值,提出了节能管理、节能技术等,就是从多方面入手继续降低能耗。
影响能量有效利用率的因素是多方面的,从技术上看,其中主要原因之一是由于工序间操作条件的改变,部分能量在工艺物料的降温、降压过程中释放出来,从而成为“废热”和“废功”。如果这部分热量散失于周围环境中,不仅浪费了大量的能量,而且对环境的热污染也非常严重。因而这部分“废热”和“废功”必须进行回收。
化工生产中最常用最简单的方法就是利用锅炉来回收工艺物流中的余热,生产蒸气。通常这种回收余热生产蒸气的锅炉称为废热锅炉,也称为余热锅炉。
废热锅炉较早用来产生一些低压蒸气,回收的热量有限,只是作为生产的一般辅助性设备。随着生产技术的发展,废热锅炉的参数逐渐提高,废热锅炉由生产低压蒸气的工艺锅炉转变为生产高压蒸气的动力锅炉。废热锅炉在整个装置中已逐渐成为动力源,其运行状况直接关系到整个生产过程,甚至已经利用高压蒸汽发电且并入电网。因此,在这种情况下,废热锅炉往往成为整个装置不可分割的关键性设备之一。生产过程对于废热锅炉的依赖性也日益增大,人们对废热锅炉的重视程度也相应地增加。GB 21344—2015中就有一条:推广热电联产,提高热电机组的利用率。
2.4.2.1 废热锅炉分类
在废热锅炉中进行的是热量传递的过程,因此废热锅炉的基本结构也是一个具有一定传热表面的换热设备。但是由于化工生产中,各种工艺条件和要求差别很大,因此化工用的废热锅炉结构类型也是多种多样的。
(1)按炉管位置分类
按照炉管是水平还是垂直放置,废热锅炉可以分为卧式和立式两大类。
①卧式锅炉大都采用火管式,即管内走高温工艺气体,而管外走饱和水和水蒸气。这种锅炉的特点是管内清扫灰垢特别方便,而且结构也比较简单。但是这种锅炉的蒸发量小,蒸汽压力低,水侧循环速度慢,传热速率也较低,通常用于中、小型废热锅炉。
②立式锅炉通常比卧式锅炉水循环速度快,传热速率较高,蒸汽空间也比较大,因此这种锅炉蒸发量大。在大型化工装置中,当回收热负荷较多、蒸汽压力较高的情况下,通常采用立式水管锅炉。
(2)按压力分类
按照锅炉操作压力的大小,废热锅炉可以分为低压、中压和高压三大类。
通常把蒸汽压力在2.5MPa以下的称为低压废热锅炉,其容量较小,一般不超过20t/h。蒸汽压力在2.5~6.0MPa范围内的称为中压废热锅炉。蒸汽压力在6.0MPa以上的称为高压废热锅炉。
(3)按结构和工艺用途分类
①按照炉管的结构形式不同,废热锅炉可以分为列管式、U形管式、刺刀管式、螺旋盘管式以及双套管式等。
②按照生产工艺或使用的场合不同,废热锅炉可以分为重油汽化废热锅炉、乙烯生产裂解气急冷废热锅炉及合成氨前置式、中置式或后置式废热锅炉等。
2.4.2.2 废热锅炉结构
化工厂里常用的废热锅炉形式有固定管式、U形管式、烟道式及螺旋管式等。
(1)固定平管板式废热锅炉
这种结构的废热锅炉内部结构与固定管板式换器的结构基本相同,通常采用卧式,管内是高温工艺气体,而管外是饱和水和水蒸气。锅炉的两块平管板直接焊于壳体上,管束由炉管及中心旁通管组成。中心旁通管的作用是调节高温气出口温度。中心管出口端有调节阀,开启调节阀相当于使部分高温气体短路,废热锅炉的排气温度可随之提高。
饱和水由下降管导入壳体下部并在壳程内流动,汽、水混合物由壳体上部通过上升管进入汽包。由于循环系统阻力较小,汽包往往可以直接搁置于锅炉上面,结构比较紧凑,如图2-71所示。

图2-71 固定平管板式废热锅炉
高温工艺气从进口分配箱进入炉管,为了保护进口分配箱和进口管板避免超温过热,在进口分配箱和进口管板上都衬有耐火材料。这种废热锅炉通常可用于以天然气为原料生产合成氨的二段转化炉后,回收转化气中的余热。
(2)U形管式废热锅炉
U形管式废热锅炉为直立水管式锅炉,从外形上看上小下大,外部几何形状像个酒瓶,其基本结构如图2-72所示。

图2-72 U形管式废热锅炉
1—内人孔;2—进水管;3—人孔;4—进水均布板;5—外壳上段;6—外壳下段;7—耐热层;8—衬里;9—U形管
①高压管箱。锅炉壳体分为高压和中压两部分,管板以上的管箱部分承受高压,管板以下的壳体部分承受中压。
锅炉顶部为半球形封头,是高压管箱的组成部分,管箱内用隔板分隔为上下两部分。汽包中的高压饱和水通过下降管从半球形封头上的接管进入上管箱。在进入管的入口处装有导向板和均布板,导向板和均布板的作用是把水均匀地分布到各U形管的入口中去。水在U形管内受热沸腾后,汽、水混合物从U形管的另一侧上升汇聚到下管箱中。下管箱的出口连接上升管并将汽、水混合物送到顶上的高位汽包中去。汽包标高32m,这个高度用来保证自然循环所需要的液位。
管箱壳体上开有人孔,供维护检修之用。管箱内部的分隔板上也同样开设一个内部人孔,以便检修时能从上管箱中进入到下管箱。这样,在锅炉中、小修时可以不必整体吊出管束。
②管束。锅炉的管束由U形管和一块平管板组成。管板上侧有一圈凸缘与高压管箱壳体焊成一体,管板的外围兼作法兰。U形炉管的两端用胀焊结合的方法固定在管板上。这种结构不仅可以保证高压空间密闭性好,而且在大修时U形管束可随同高压管箱一起吊出,便于清洗或检修。
③中压壳体。由二段转化炉出来的高温工艺气体,从壳体的下部侧向进入壳体,与炉管换热后从上部出去。为了防止壳体过热,壳体下段内侧衬有高铝低硅的耐火水泥和低铁绝热水泥。壳体上段由于排气温度较低,没有耐火混凝土衬里,壳体外部没有水夹套。为了保护耐火水泥衬里以及便于管束的装拆,在耐火水泥的表面上衬有衬套,以防止高温气流的冲刷或机械损伤。
壳体底部为了避免高温气体在进入壳程后发生偏流,留出了一段空间作为缓冲区。缓冲区的作用在于降低气流速度,消除气体的入口动能,从而达到使气体在U形管间均匀分布的目的。缓冲区内也可以安装气体分布器以进一步均布气流。
壳体中部装有调节温度用的副线出口,通过这个出口可以使部分高温气体短路,从而达到调节转化气出口温度的目的。这种废热锅炉能产生压力为10MPa的高压蒸汽,用于一些年产30×104t合成氨等装置中。
(3)烟道式废热锅炉
①基本结构。烟道式废热锅炉与普通燃烧锅炉很类似,其结构如图2-73所示。它是双汽包自然循环式废热锅炉,整个管束放在用耐火砖砌成的气室内。高温工艺气在气室内流动时扫过传热管束,使管束内的饱和水受热后产生蒸汽。汽、水混合物沿管束上升进入上汽包,并分离出其中的蒸汽,然后饱和水重新沿不受热的下降管进入下汽包,从而构成一个自然循环的循环回路。

图2-73 烟道式废热锅炉
1—上汽包;2—下汽包;3—管束;4—过热器;5—过热器出口联箱;6—出灰口
这种废热锅炉的操作压力为3.5~3.7MPa,过热蒸汽温度为350℃,锅炉出口处的排气温度为450℃。这种废热锅炉除了采用自然循环方式外也可采用强制循环方式。
②主要特点。烟道式废热锅炉主要用于硫酸生产中,采用这种结构形式的原因是高温气体具有以下一些特点:炉气的压力低于大气压(负压),因此即使砖砌的气室密封不严,也不会有高温气的漏损;高温炉气中含有大量二氧化硫和三氧化硫等腐蚀性气体,一旦冷凝下来将对金属产生严重腐蚀;高温炉气中含有大量矿尘,从沸腾焙烧炉出来的炉气的含尘量高达200~250g/m3,对金属会造成严重的磨损;硫铁矿焙烧后产生的高温气体温度高达800~900℃。
这种废热锅炉除了用于硫酸生产中矿料焙烧后的炉气冷却、一氧化碳燃烧气冷却等以外,在动力、冶金、陶瓷等工业中也有应用。
(4)螺旋管式废热锅炉
这种废热锅炉的炉管不是直管束,而采用了螺旋管,其结构如图2-74所示。高温工艺气体从锅炉的底部进入螺旋管,在螺旋管中传递热量,将管外的锅炉给水加热为蒸汽,经降温后的工艺气体从锅炉的顶部排出;循环的饱和水从锅炉中心降下并获取热量,经过底部后由螺旋管的外侧上升,汽、水混合物从锅炉的顶部引出。

图2-74 螺旋管式废热锅炉
螺旋管式废热锅炉主要用于含有烟灰的高温工艺气体中,这种高温气体在直的锅炉管束中会引起烟灰的严重沉积,而沉积在管壁上的烟灰将降低传热效果并出现“局部热点”(指局部高温、超温区域)。采用螺旋管后,由于在管内可保持较高且比较均匀的气流速度,又没有死角,因此即使运行很长时间也不会发生烟灰沉积。螺旋管内少量灰垢的清洗,可采用蒸汽加喷钢砂。
螺旋管的结构类似于弹簧,能利用本身的挠曲变形来吸收管子与壳体间的热膨胀差,因此这种结构适用于压力较高、管壳之间热膨胀差较大的场合。螺旋管式废热锅炉大都用于重油裂化气的废热回收。