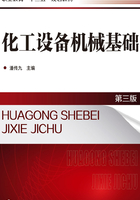
2.3 反应设备
反应设备是化工生产中实现化学反应的主要设备。按照参加化学反应物料的物态不同(气体或液体)、操作条件的不同(压力、温度以及物料静止还是流动)、反应的热效应不同(吸热反应还是放热反应),反应设备可以有很多种类和结构。例如,合成氨工厂的氨合成塔、炼油厂的加氢反应器、烯烃厂的裂解炉、合成橡胶厂的反应釜、化纤厂的聚合反应釜和抗菌素厂的发酵反应釜等,这些反应设备有的需要耐高压,有的需要耐介质的腐蚀,有的还根据操作要求设置各种内件,如催化剂支承装置、换热装置和搅拌装置等。
搅拌反应釜是一种典型的反应设备,广泛应用于化工、轻工、化纤、医药等工业。它是在一定的压力和温度下,将一定容积的两种或多种液态物料搅拌混合,促进其化学反应的设备;通常伴有热效应,由换热装置输入或移出热量。
2.3.1 主要部件及其用途
搅拌反应釜的结构如图2-45所示,它主要由以下几部分组成。

图2-45 搅拌反应釜的结构
1—电动机;2—减速器;3—机架;4—人孔;5—密封装置;6—进料口;7—上封头;8—筒体;9—联轴器;10—搅拌轴;11—夹套;12—载热介质出口;13—挡板;14—螺旋导流板;15—轴向流搅拌器;16—径向流搅拌器;17—气体分布器;18—下封头;19—出料口;20—载热介质进口;21—气体进口
(1)釜体
釜体是一个容器,为物料进行化学反应提供一定的空间。釜体通常由圆筒形筒体及上、下封头(大多为椭圆形,为卸料方便也有用锥形下封头的)组成,反应釜的直径和高度由生产能力和反应要求决定。由于化学反应物料可能易燃、易爆或有毒,而且常常要保持一定的操作温度、压力(或真空)等,所以反应釜大多是密闭的(在常压、无毒及反应过程允许的条件下也可以是敞开的)。
(2)传热装置
由于化学反应过程一般都伴有热效应,即反应过程中吸收热量或放出热量,因此在釜体的外部或内部需要设置供加热或冷却用的传热装置。加热或冷却都是为了使釜内温度控制在反应所需范围内。常用的传热装置是在釜体外部设置夹套,有时同时在釜体内部设置蛇管。
(3)搅拌装置
为了使参加反应的各种物料混合均匀,接触良好,以加速反应的进行和便于反应控制,需要在釜体内设置搅拌装置。搅拌装置由搅拌轴和搅拌器组成,搅拌装置的转动一般由电动机经减速器减到搅拌器所需转速后,再通过联轴器来带动。搅拌轴一般是悬臂的,需要时也可在釜内设置中间轴承或底轴承(有关传动构件可参考4.2及4.3两节内容)。
(4)轴封装置
由于搅拌轴是转动的,而釜体封头是静止的,在搅拌轴伸出封头之处必然有间隙,介质会由此泄漏或空气漏入釜内,因此必须进行密封,称为“轴封”(对轴伸出装置外部的位置进行的密封称为轴封),以保持设备内的压力(或真空度),防止反应物料逸出和杂质的渗入。通常采用填料密封或机械密封。
被装在搅拌轴和填料函之间环隙中的填料,多数用纤维填料,如浸渍石墨的石棉纤维填料。填料在压盖压力作用下,对搅拌轴表面产生径向压紧力。由于填料中含有润滑剂,因此在对搅拌轴产生径向压紧力的同时形成一层极薄的液膜(它一方面使搅拌轴得到润滑,另一方面阻止设备内流体逸出或外部流体渗入)。
机械密封是用垂直于轴的两个密封元件的平面相互贴合(依靠介质压力或弹簧力),并作相对运动达到密封目的的装置,又称端面密封。它具有功耗小、泄漏率低、密封性能可靠和使用寿命长的优点。机械密封主要用于在腐蚀、易燃、易爆、剧毒及带有固体颗粒的介质中工作的有压设备和真空设备,包括搅拌反应釜的轴封。
(5)其他结构
除上述几部分主要结构外,为了便于检修内件及加料、排料,还需装焊人孔、手孔和各种接管。为了操作过程中有效地监视和控制物料的温度、压力并确保安全,还要安装温度计、压力表、视镜、安全泄放装置等。
2.3.2 夹套传热及其结构
搅拌反应釜最常用的传热方式为夹套传热和蛇管传热。在釜体外侧,以焊接或法兰连接的方法装设各种形状的外套,与釜体外表面形成密闭的空间,在此空间内通入蒸汽或冷水等,用来加热或冷却釜内的物料,维持物料的温度在规定的范围,这种结构称为夹套。
常用的夹套形式为整体夹套,其结构类型如图2-46所示。图2-46(a)所示仅为圆筒的一部分有夹套,用于需要加热面积不大的场合。图2-46(b)所示为圆筒的一部分和下封头包有夹套,是最常用的典型结构。图2-46(c)所示适用于筒体细长的场合,考虑到筒体承受外压,为了增加筒体的稳定性或者是釜内反应的需要,在筒体的上下不同位置上分段设置夹套,各段夹套之间设置加强圈或采用能够起到加强圈作用的夹套封口件。图2-46(d)所示为全包式夹套,与前三种比较,传热面积最大。

图2-46 整体夹套的结构类型
整体夹套与筒体的连接方式有可拆卸式和不可拆卸式两种,分别如图2-47和图2-48所示。不可拆卸式夹套结构简单,密封可靠。“碳钢”夹套可以直接和“碳钢”(碳钢是钢材中最普通的一类材料,主要由铁和少量的碳两种元素组成,全称碳素结构钢,常用于一般工程结构)釜体焊接;图2-48所示为用“不锈钢”(能抵抗大气和一般酸、碱、盐腐蚀的钢材)釜体配碳钢夹套时两者之间的连接结构,其特点是避免了不锈钢釜体直接和碳钢件焊接,以防止不锈钢中的合金元素在焊接时有损失。如果釜体与夹套用不同材料制造,两种材料又不适合焊接连接,或者反应操作条件恶劣而要求定期检查釜体表面,应采用可拆卸式连接。

图2-47 可拆卸式整体夹套结构

图2-48 不可拆卸式整体夹套结构
整体夹套内的介质压力一般不能超过1MPa,否则釜体壁厚太大,增加制造困难。夹套内的介质压力大时,可采用焊接半圆管夹套、“型钢”(指轧钢厂轧制、市场有售的横截面为特定形状的钢材,如角钢、圆钢、扁钢等)夹套和蜂窝夹套,不但能提高传热介质的流速,改善传热效果,而且能提高筒体承受外压的能力,但是上述结构焊接工作量过大,给制造带来很大麻烦。
2.3.3 蛇管传热及其结构
当需要传热面积较大、夹套传热不能满足要求时,可采用蛇管传热。密集排列的蛇管沉浸在物料中,热量损失小,传热效果好,同时还能起到导流筒的作用,可以改变流体的流动状况,减小旋涡,强化搅拌程度,但检修较麻烦。蛇管允许的操作温度范围为-30~280℃,公称压力系列为0.4MPa、0.6MPa、1.0MPa、1.6MPa。
蛇管的长度不宜过长,否则因冷凝液积聚而降低传热效果,而且在很长的蛇管中排出蒸汽所夹带的惰性气体也是很困难的。
如果要求传热面积很大,可以制成几个并联的同心圆蛇管组。蛇管的排列如图2-49所示。

图2-49 蛇管的排列
蛇管的固定形式较多,如果蛇管的中心圆直径较小或圈数不多、重量不大时可以利用蛇管进、出口接管固定在顶盖上,不再另设支架固定蛇管。当蛇管中心圆直径较大、比较笨重或搅拌有振动时,则需要装支架以增加蛇管的刚性。
蛇管的进、出口一般都设置在顶盖上,有可拆结构和固定结构两类:可拆结构用于蛇管需要经常拆卸清洗的场合;固定结构的蛇管可以和封头一起抽出。
2.3.4 搅拌器的形式
搅拌器的形式很多,它的形状、尺寸、结构与被搅拌液体的性质以及要求实现的流型有关。常用的搅拌器按结构来分,可分为桨式搅拌器、框式和锚式搅拌器、推进式搅拌器、涡轮式搅拌器等;按流体的流动形态来分,可分为轴向流搅拌器、径向流搅拌器和混合流搅拌器。搅拌器的径向、轴向和混合流的图谱如图2-50所示。
(1)桨式搅拌器
桨式搅拌器结构最为简单,如图2-51所示。其桨叶用扁钢制造,当搅拌的物料对钢材有显著腐蚀时,桨叶可用合金钢或有色金属制作,也可采用钢制外包橡胶或环氧树脂、酚醛玻璃布等。

图2-51 桨式搅拌器
桨叶形式有平直叶和折叶两种。平直叶就是叶面与旋转方向互相垂直,折叶则是叶面与旋转方向成一倾斜角度(一般为45°或60°)。平直叶主要使物料产生切线方向的流动,加挡板后可产生一定的轴向搅拌效果。折叶与平直叶相比轴向分流略多。
在料液层比较高的情况下,为了将物料搅拌均匀,常装有几层桨叶,相邻两层桨叶常交叉成90°安装。
桨叶与轴的连接有两种情况:当搅拌轴直径d<50mm时,除用螺栓对夹外,再用紧固螺钉固定;当搅拌轴直径d≥50mm时,除用螺栓对夹外,再用穿轴螺栓或圆柱销固定。桨式搅拌器的搅拌力度不大,转速较低(一般为20~100r/min),圆周速度在1.0~5.0m/s范围内,广泛用于促进传热、溶解、混合等操作。
(2)框式和锚式搅拌器
锚式搅拌器结构简单(图2-52),它适用于黏度在100Pa·s以下的流体搅拌;当流体的黏度在10~100Pa·s时,可在锚式桨中间加一横桨叶,即为框式搅拌器,以增加容器中部的混合。为了增大对高黏度物料的搅拌范围以及提高桨叶的刚性,还常常要在框式、锚式搅拌器上加一些立叶和横梁,这样使得框式、锚式搅拌器的结构形式更多。

图2-52 锚式搅拌器
框式、锚式搅拌器桨叶与搅拌轴的连接方式与桨式搅拌器类似。这两种搅拌器由于桨叶的外廓尺寸大,为了便于装拆,桨叶之间多数用螺栓连接,只有小型的才采用铸造或焊接。当搅拌有腐蚀性的物料时,可在其外表面进行搪瓷、覆胶或覆盖其他保护层。
框式、锚式搅拌器的转速也不高(一般为20~100r/min),线速度为1.0~5.0m/s。
(3)推进式搅拌器
推进式搅拌器也称旋桨式搅拌器,如图2-53所示。标准的推进式搅拌器有三瓣叶片,其螺距与桨叶直径相等。搅拌时,流体由桨叶上方吸入,下方以圆筒状螺旋形排出,流体至容器底部再沿壁面返至桨叶上方,形成轴向流动。推进式搅拌器在进行搅拌时,流体的湍流程度不高,但循环量大,上下翻腾效果好,适用于液体黏度低、流量大的场合,常被应用于固体溶解、结晶、悬浮等操作中。

图2-53 推进式搅拌器
(4)涡轮式搅拌器
涡轮式搅拌器与桨式搅拌器相比,只是桨叶数量多、种类多,桨的转速高,可使流体均匀地由垂直方向运动改变为水平方向运动,自涡轮流出的高速液流沿圆周运动的切线方向散开,从而在整个液体内得到激烈搅动。它是应用较广的一种搅拌器,能有效地完成几乎所有的搅拌操作,并且能处理的流体黏度范围很广。图2-54给出了一种典型的涡轮式搅拌器结构。

图2-54 涡轮式搅拌器
涡轮式搅拌器形式很多,有开启式和圆盘式。桨叶又分为平直叶、弯叶和折叶。这类搅拌器和推进式搅拌器相似,搅拌速度也较高(为10~300r/min),搅拌器直径约为反应釜筒体内径的1/3,叶数以6叶为多,桨叶的厚度一般由强度计算确定。
2.3.5 其他反应类设备
(1)固定床反应器
固定床反应器多用于大规模气相反应。固定床是指设备内静止不动的固体颗粒层,在这里是指反应器内的固体催化剂层。在一些场合反应器内装有许多根管子,故也称管式反应器。固定床反应器的外形有圆筒式[图2-55(a)]和列管式[图2-55(b)]。参加反应的物料以预定的方向运动,各点的流体间没有沿流动方向的混合。这类反应器可以在一个圆柱壳体内装催化剂,或者在圆柱壳体内安装许多平行的管子(就像列管式换热器管束一样),管外或管内装催化剂,参加反应的气体通过静止的催化剂层进行反应,氨合成塔、乙烯裂解炉等就属于此种结构。固定床反应器广泛用于催化反应。

图2-55 固定床反应器
1—换热器;2—催化剂固定床;3—载热体
(2)流化床反应器
流化床反应器多用于固体和气体参加的反应,其结构如图2-56所示。在这类反应器中,细颗粒状的固体物料装填在一个垂直的圆筒形容器的多孔板上,气体通过多孔板向上通过颗粒层,以足够大的速度使颗粒浮起呈沸腾状态,但流速也不宜过高,以防止流化床中的颗粒被气体夹带出去。颗粒快速运动的结果,使床层温度非常均匀,因而避免了固定床反应器中可能出现的过热点,这对在绝热条件下进行的反应过程是一个很大的优点。这类反应器的缺点是固体颗粒快速运动会造成催化剂的磨损;另外,排出气流中含有大量的粉尘,增加了后处理难度。

图2-56 流化床反应器
1—原料沸腾床;2—气体分布板;3—换热器;4—催化剂流化床
(3)鼓泡反应器
在这种反应器中,由于液体中含有溶解了的非挥发性催化剂或其他反应物料,反应气体可以鼓泡,通过液体进行反应,产物可由气流从反应器中带出。在这种情况下,由传质过程控制反应速率。乙烯氧化生产乙醛就是在这种反应器中进行反应的。
(4)流动床反应器
在这种反应器中,固体从床层顶部加入,并向下移,自器底取出,流体向上通过填充层。这种反应器已用于二甲苯的催化异构反应以及离子交换法的连续水处理过程。
另外,在有些有机反应中,如丙烯高压水合制取异丙醇反应中,用到了滴流床反应器。在这种反应器中,固体催化剂并不呈流化状态而是作为固定床,两种能部分互溶的液体作为反应物料并流或逆流通过反应床进行反应。
用于化工生产的反应器很多,在实际使用过程中,应根据实际生产的需求,选用适合的反应器类型,并有针对性地进行设计。