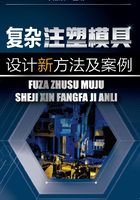
1.6 注塑件上的塑料与批量要素
塑料要素是指注塑件所用的高分子材料,在注塑件图纸上会注明塑料的名称或牌号及其收缩率。批量要素是指注塑件成型加工的产量,可分成小、中、大和特大四种产量。注塑件形体分析的塑料要素会影响到熔体加热的温度范围、流动充模状态和冷却收缩性能等。
塑料有无弹性,又会影响到注塑模的结构,而影响最大的是注塑件收缩率和模具温控系统的设计。如哪些塑料在成型加工时需要进行冷却、哪些塑料在成型加工时需要有加温装置、哪些塑料在成型加工时需要有热流道装置等。注塑件的塑料品种不同,收缩率和模具温控系统的结构就不同;塑料品种不同,也会影响模具用钢和热处理。如具有腐蚀性的塑料,必须采用不锈钢;塑料中含有增强(如玻璃)纤维,应选用耐磨钢材;具有透明性能的塑料制品的模具,应选用具有一定硬度的模具钢。
注塑件形体分析的批量要素的不同,同样会影响模具的结构、模具用钢及其热处理。对于大批量和特大批量的制品,模具必须具有高寿命,所采用的模具钢需要耐磨损。还会影响模具是采用手动抽芯或手动脱模,还是采用自动抽芯和自动脱模。
故在进行注塑件形体分析时,一定要将注塑件形体分析的塑料与批量要素找出来,以便确定模具的结构方案。若在注塑件形体分析时,不能提取塑料与批量要素,必定会导致模具结构方案的缺失。
1.6.1 注塑件形体分析的塑料要素
注塑模的工作温度及其调控系统,对塑料熔体的充模流动、冷硬定型、注塑件质量和生产效率都具有重要的影响。因为任何品种的塑料均有一个适合熔体流动充模的温度范围,为了能够控制塑料熔体在合理的温度范围之内,模具就必须设计有温控装置。熔体在充模和反复加工过程中的温度,是在不断地变化,导致模具各个部位的温度存在着差异,从而影响注塑件的收缩率、内应力、变形和熔接痕的强度。为了改变这种状况,现在出现了一种智能注塑模,就是在模具各个部位安装一些温度传感器和电热器。传感器可以将它所在部位的温度传递给计算机,计算机则可以将温度降低到某数值时启动电热器加温,温度达某值时再切断电热器电源。当然,通过传感器还可以控制熔体的流速和流量等。
注塑件在注射成型的过程中,开始注射时模具是冷的,由于受到模具型腔中熔体温度传热的作用,模温会逐渐地升高。根据注射成型的材料不同,模具的温度要求也是不同的。为了获得良好的注塑件质量,应该尽量地使模具在工作过程中维持适当和均匀的温度。所以在模具设计时必须考虑用加热或冷却装置来调节模具的温度。在个别情况下,是需要冷却与加热同时使用或交替使用。在通常情况下,热塑性塑料,模具常需要进行冷却,热固性塑料注射成型时则必须加热。模温是根据塑料品种、注塑件厚度、结晶性塑料所要求的性能而决定的。
(1)不正常模温对注塑件质量的影响
由于注塑件成型时要求模具有一定的模温,若模温过高或过低都会影响注塑件的质量。模温过高会产生缩孔和溢料等缺陷;模温过低则会产生填充不足、熔接痕和表面不光洁等缺陷;模温不均匀会产生变形的缺陷;模温调整不当则会造成注塑件力学性能不良。
(2)模温控制
注塑件成型时的温度、压力和时间三大工艺因素,就是通常所指的成型的工艺条件。成型工艺条件是除塑料品种型号、注塑件结构、注射机、模具结构和注塑件成型环境之外,影响注塑件质量的主要因素之一。而成型工艺条件的温度,包括料筒温度、喷嘴温度、注射温度(熔体温度)和模具温度。料筒温度和喷嘴温度是注塑机控制熔体的注射温度,只有模具温度才是模具设计人员需要考虑设计的部分。
①热塑性塑料成型时模温的控制 提高模温可以改善熔体在模具型腔内的流动性,增强注塑件的密度和结晶度,减小充模压力;降低模具温度,可降低塑料熔体在模具型腔中的充模流动性,以及缩短冷却定型的时间从而提高生产率,还会使注塑件产生较大的应力和熔接痕等缺陷。具体的模具加热或冷却,需要根据塑料品种型号、注塑件壁厚和成型周期来确定。
②热固性塑料成型时模温的控制 热固性塑料成型时一般都需要进行加热,模温选择控制在150~220℃,动模需要比定模高出10~15℃。模温过低,会导致硬化时间过长,注塑件出现组织疏松、起泡及颜色发暗等缺陷。
(3)注塑件形体分析的塑料要素与注塑件的收缩率
注塑件形体分析的塑料要素与注塑件的收缩率,是决定模具型面和型腔尺寸的主要因素。我们知道任何物质都具有热胀冷缩的性质,塑料受热后体积会膨胀,冷却后体积又会收缩。故注塑件图纸上在给出塑料的品种之后,我们都会根据塑料的品种找出该种聚合物的收缩率,从而在模具型面和型腔的尺寸设计时,在注塑件的尺寸之上再加上塑料品种的收缩量。
(4)塑料弹性的运用
热塑料大多数具有一定的弹性,对于一些具有较小高度筋和较浅槽的塑料件,可以利用其弹性进行强制性脱模。进行强制性脱模的条件:①注塑件上筋高度较小,槽深较浅。②成型注塑件只保留具有筋槽的形体,其他的形体均敞开。强制性脱模时,必须注意防止注塑件产生变形和出现裂纹等缺陷。
(5)塑料与模具用钢
塑料品种对模具用钢的影响很大,塑料模具用钢包括热塑性塑料模具和热固性塑料模具。塑料模具用钢要求具有一定的强度、硬度、耐磨性、热稳定性和耐腐蚀性等性能。此外,还要求具有良好的工艺性,如热变形小、加工性能好、耐腐蚀性好、研磨和抛光性能好、补焊性能好、粗糙度值低、导热性好和工作条件尺寸和形状稳定等。在一般情况下,注射成型或挤压成型模具可选用热作模具钢;热固性成型模具和要求高耐磨、高强度的模具可选用冷作模具钢。为了确保塑料模具的质量和使用寿命,当然最佳是选用新型专用塑料模具钢。
塑料模具钢种有通用型、耐磨型、渗碳型、耐腐蚀型、高镜面型、无磁型和预硬化易切削塑料模具钢。注塑模除了要正确地进行模具结构最佳优化方案可行性分析与论证以及模具结构的设计之外,合理地选择注塑模用钢与热处理,也是注塑模设计中十分重要的一环。模具的耐磨性、耐腐蚀性、加工性能和维修性,都与模具用钢与热处理的选择息息相关,进而影响模具使用的寿命、模具制造和维修的成本、模具制造的周期。虽然模具用钢成本只占制造成本的10%~20%,但由于上述的原因,模具用钢与热处理的选择确实可以决定注塑件的整体经济效益。
近年来,随着钢材冶炼技术水平的提高,产生了许多优质高性能的钢材和先进的热处理技术,如预硬钢、高强度模具钢、无缺陷模具钢、耐腐蚀模具钢、镜面模具钢、易切削模具钢和高速钢基体钢等。这些钢材从价格上讲要比普通的注塑模用钢高一些,但是却比普通的注塑模用钢的性能高出很多。不管从模具的使用寿命,还是从整体经济效益都比普通的注塑模用钢强得多。故采用新型的模具用钢和先进的热处理技术,也是模具技术人员应该掌握的知识。
(6)注塑件形体分析塑料要素实例
塑料要素是影响模具温控系统设计的主要因素,而模具温控又是影响塑料熔体流动的因素,也是注塑件产生缺陷的因素。在进行注塑件形体分析时,一定要找出注塑件的塑料要素。当主浇道的长度超过60mm时,塑料熔体料流接触低温模具的浇道距离过长,熔体温降会过大,从而会降低熔体的流动性,也会造成注塑件产生各种的缺陷。为了避免注塑件各种缺陷的产生,则应采用热流道或热延长喷嘴等措施。
[例1-23] 面罩主体是供氧面罩中一个十分重要的橡胶件,其形状曲折复杂、厚度变化大,最薄处仅为0.7mm。面罩主体裙围需与人的脸部造型完全吻合。通过对面罩主体形体的分析,在裙边与裙围转接处存在着弓形高“障碍体”。橡胶模便采用了二次分型的方法,使得凸模与凹模及凸模与中模都能够分型。成型面罩主体型腔的中模,是一个大的凸台“障碍体”。面罩主体的脱模,是利用了硅橡胶面罩主体的弹性,采用了手工剥离或吹入压缩空气使其膨胀脱模的形式。在距凹模模腔0.2mm的沿周,制有1.5mm×90°的余胶槽,余胶进入余胶槽中形成飞边。凹槽边缘与型腔边缘形成0.20mm的刃口,当面罩主体压制后脱模时,飞边能自动被刃口切落。模具结构的形式,实现了面罩主体顺利成型和脱模及飞边的处理。
面罩主体二维图,如图1-24(a)所示,面罩主体三维造型,如图1-24(b)所示。面罩主体裙围处孔是人鼻和嘴的开口孔,在面罩主体背面左侧有供氧及通信系统的连接孔,右侧有负压囊的连接孔,面罩主体下端是呼气系统的连接孔。面罩主体主要尺寸,如图1-24(a)所示。面罩主体裙围为0.7mm,裙边为2.0mm,裙背为1.5mm,呼气系统连接孔壁的厚度为2.5mm。

图1-24 面罩主体二维图与三维造型
[例1-24] 豪华客车带灯箱锁主体部件,如图1-25所示。材料:30%玻璃纤维增强聚酰胺6(黑色)QYSS08—1992,收缩率1%。我国地域辽阔、人口众多,又是世界经济的引擎,豪华客车的市场一定是很大的。那么,豪华客车带灯箱锁主体部件的产量一定是特大批量。聚酰胺6塑料存在着30%玻璃纤维,要使成型加工的该产品模具寿命长,一般选取高耐磨的模具钢。由于塑料具有热胀冷却的特性,各种塑料的收缩率是不同的。模具型腔和型芯的尺寸需要增加补偿值,有了收缩率就能计算出模具型腔和型芯的尺寸。

图1-25 带灯箱锁主体部件的形体
1—主体部件;2—圆螺母
[例1-25] 盒如图1-26所示,材料:ABS。在盒的右边型腔的前后处存在着1.0mm×0.2mm的槽,成型该浅槽是模具型芯上的凸台。由于盒左边存在通风栅口,成型盒外形的凹模必须在Ⅰ—Ⅰ处分型。那么成型1.0mm×0.2mm槽的凸模,可以用脱件板进行脱模。这就是在成型盒外形敞开后,利用高于室温塑料的塑性进行强制脱模。

图1-26 盒
[例1-26] 转换开关大、小件,如图1-27所示。材料:30%微珠玻璃聚碳酸酯(黑色),收缩率为:0.3%~0.4%,亚光。注塑件形体分析时应提取“塑料”要素,只要将塑料材料品种找出即可。注塑件的塑料要素是影响模具温控系统设置的因素,什么样的模具需要设置加温装置,什么样的模具需要设置冷却装置,完全取决于塑料品种。模具温控系统设置是否得当,都将直接影响注塑件成型加工的质量。由于转换开关大、小件是气动切换工位的机械手,其精度超过了金属产品。选用30%微珠玻璃聚碳酸酯,一是要使转换开关大、小件具有一定的耐磨性和小的收缩性,二是要使转换开关外观更为美观,而不要像30%玻璃纤维聚碳酸酯制品那样外观能够见到许多玻璃纤维。

图1-27 转换开关大、小件
1.6.2 注塑件形体分析的批量要素
注塑件形体分析的批量要素,是影响模具的结构因素之一。就注塑件的批量而言,批量小的注塑件模具在用钢方面可以选用如45碳素结构钢材,不进行热处理,批量大的注塑件模具用钢则应选用新型专用的模具钢。就模具结构而言,批量小的注塑件的模具结构能简就简,而批量大的注塑件模具结构则要求高自动化、高效率和高寿命,甚至是智能化。可以说注塑件的批量不同,模具的结构也就不同。注塑件的批量越大,模具的结构可以越完善和越复杂,反之,模具的结构可以简单化。
(1)注塑件形体分析的批量要素
注塑件形体分析的批量要素,也是影响模具结构、价格和制造周期的因素之一。注塑件批量不仅影响模具用钢和热处理的选择,还影响模具的结构。一般可以将注塑件批量分成小批量、中批量、大批量和特大批量。模具设计时,一定要根据注塑件批量的大小进行模具结构的设计、模具用钢及其热处理的选择,否则会造成模具制造成本增加和模具效率低下及模具寿命降低。而模具用钢及热处理是决定模具寿命的因素,模具的结构则是决定模具自动化和模具效率的因素。注塑件的批量一旦确定下来了,模具的结构和用钢也随之确定下来,模具的价格和制造周期也就可以确定下来。
(2)注塑件批量与注塑模用钢
注塑料模具用钢可依据塑件批量选用,可以参考表1-1。
①传统模具材料 也称为比较模具材料,是最早用于模具的模具钢材,有普通碳素钢、优质碳素钢、工具钢、合金工具钢、高速钢、不锈钢、轴承钢、硬质合金和粉末冶金等。传统塑料模具钢的型号,如40Cr、T8Mn、2Cr13、1Cr18Ni9和0Cr19Ni9等。
②新型模具(或特种)钢 是在与传统模具钢性能的基础上,为了弥补传统模具钢种性能的不足,再根据模具加工产品的性质和失效的原因,进行钢材合金成分的添加与减少以及采用适当的冶炼方法所得到的钢材称为新型模具钢。新型模具钢类型有新型冷作模具钢、热作模具钢和塑料模具钢,它们的性能均比相应传统模具钢要好,使用寿命要长。其他类型的模具用钢可以比对模具的使用性质和失效原因进行选用。新型塑料模具钢有预硬化钢、析出硬化钢、时效硬化型塑料模具钢、易切削高韧性模具钢、易切削调质型预硬钢、低镍马氏体时效钢、时效硬化型钢、马氏体时效钢、非调质塑料模具钢、镜面塑料模具钢钢、耐腐蚀塑料模具钢、耐磨高寿命超强度塑料模具钢及高寿命和耐腐蚀镜面模具钢。
(3)模具与新型模具钢的应用
模具是由具有各种功能的机构和零部件组成的,具体地说有工作件和结构件两大类型。工作件是指直接与加工产品接触的零部件,如凸模、凹模、型腔与型芯等。结构件是指相对于工作件起到支撑和连接的零部件,如模架、导柱、导套、定位和连接件等。对于模具工作件而言应该要求它们具有高耐磨性、低变形性、耐腐蚀性、优越加工性,优良耐热性和长的寿命。对于结构件为了降低模具成本,均可以采用传统模具材料。对于工作件而言,如手工裱糊和喷射裱糊的成型模,由于是试制生产或单件生产或小批量生产,模具材料还可以采用非金属材料。对于小批量生产的冲压模和热作模,也可以采用传统的冷作和热作模具钢。
①塑料模具用钢的要求 应具有一定的强度、硬度、耐磨性、热稳定性和耐腐蚀性等性能,还应具有良好的工艺性,如热变形小、加工性能好、耐腐蚀性好、研磨和抛光性能好、补焊性能好、粗糙度低、导热性好及工作尺寸和形状稳定等。
②目前开发的新型钢种 包括有合金结构钢、不锈钢、耐酸钢、耐磨钢、耐热钢、合金工具钢、滚动轴承钢、合金弹簧钢和特殊性能钢(如软磁钢、永磁钢、无磁钢等)等。
a.新型优质碳素结构钢 包括合金结构钢、碳素工具钢、合金工具钢、高速工具钢、碳素弹簧钢、合金弹簧钢、轴承钢、不锈钢、耐热钢、电工钢,还包括高温合金、耐腐蚀合金钢和精密合金等。
b.新型低合金钢 包括低合金焊接高强度钢、低合金冲压钢、低合金耐腐蚀钢、低合金耐磨损钢、低合金低温钢、甚至还纳入了低、中碳含量的低合金建筑钢和中、高碳含量的低合金铁道轨钢。
③当前新型材料研究内容 新型金属功能材料除上述几类以外,还有能降低噪声的减振合金;具有替代增强和修复人体器官和组织的生物医学材料;具有在材料或结构中植入传感器、信号处理器、通信与控制器及执行器,使材料或结构具有自诊断、自适应,甚至损伤自愈合等智能功能与生命特征的智能材料等。
(4)模具寿命对比案例
同种模具通过采用新型模具钢和传统模具钢后寿命的对比。
[例1-27] Cr12MoV钢较常规淬火、回火处理的CrWMng钢,用于同类模具寿命能提高10倍以上,经渗硼后其使用寿命又可再提高5~10倍。
[例1-28] 65Nb高速钢复合模经1140℃油淬,540℃二次回火后与T10钢相比,使用寿命能提高60倍。同时,经辉光离子氮化和渗硼处理还可进一步提高其使用寿命。
[例1-29] V3N超硬冷作模具钢寿命均比 Cr12MoV、Cr12等制造的模具寿命能提高3~5倍,比现用普通高速钢能提高2~10倍。
[例1-30] LD钢其寿命比W18Cr4V、W6Mo5Cr4V2、Cr12MoV、Cr12、GCr15、60Si2Mn等钢分别能提高几倍至几十倍。ER5钢用于硅钢片冲裁模,一次刃磨寿命为21万次,总寿命高达360万次,是目前以冲裁模冲裁硅钢片具有较高寿命水平的合金钢。
选用不同的模具钢材,对模具使用寿命的影响是巨大的。一般模具材料的费用是整副模具费用的10%~20%。如果对模具工作件采用新型高性能钢材,模具的费用以增加了10%计算,模具使用寿命如果提高了10倍,10%的钢材费用换来10副模具,经济效益是显然易见的。哪怕是使用寿命提高了1倍,等于多花10%的钢材费而得到2副模具,经济上也是很划算的。由此可见,对于各种模具来讲,选用适当的新型模具材料及热表处理方法,是发挥模具最大的性能、效率和经济效益的最好途径。SM1钢制作的部分模具使用寿命,如表1-1所示。
表1-1 SM1钢制作的部分模具使用寿命

注塑件形体分析的塑料与批量要素不太为注塑件设计人员所注意,也不为注塑模设计人员所注意。其实塑料与批量要素不仅影响模具用钢及其热处理,还影响模具的结构、价格和制造周期,故塑料与批量也是注塑件形体分析的要素之一。如何确定注塑件形体分析的批量要素,需要模具设计人员深入地了解产品的市场和发展潜力,这样才能确定产品的批量情况,因为注塑件的批量一般在注塑件图纸上是不会作出标注或说明的。而对注塑件形体分析的塑料要素的确定就再简单不过了,一般注塑件的图纸上一定会标注塑件的材料。若没有标注,可找设计人员询问。
(5)注塑件形体分析的批量要素案例
[例1-31] 连接环,如图1-28所示,材料:聚氨酯弹性体。技术要求:①一般公差按HB 5800—1999;②去毛刺和飞边。连接环注塑模具,当连接环为试制件时,意味着连接环还需要作若干次改进,试制模具越简单越好,模具构件的动作最好全部为手动。当连接环定型后为少批量生产时,模具可以部分构件动作为自动,另一部分模具构件为手动。当连接环产量为大批量或特大批量时,所有模具构件动作全部为自动。

图1-28 连接环
①连接环试制注塑模结构设计 针对塑料试制件加工数量极少,试制件在定型过程中还将会出现改进。试制模具必须做到结构越简单越好,费用越低越好,制造过程越容易越好,不允许追求高效率、高自动化。通过对连接环试制注塑模设计介绍,说明了这类模具只要能够加工出合格制品就可以了,并且连接环内外形的成型、抽芯、脱模和脱浇口料的动作,全部是利用手工装模和拆模来实现的。目前,塑料试制件,虽可采用3D打印技术进行加工。但3D打印价格是根据制品数量、重量和复杂程度来确定的,大型试制品数量超过10件,采用试制模具加工还是比3D打印更经济一些。可见试制模具的设计,现今仍是一种常用的技术,设计好试制模还是十分必要的。
②连接环低效注塑模结构设计 通过对连接环形体分析,找到了其外形上有弓形高和三处凸台与内形中有两处凸台“障碍体”。由于连接环产量较少,只能采用低效的模具结构方案。经过充分论证分析,连接环以放在模具中倒置位置方案为最佳优化方案。成型连接环外形,采用了弯销和滑块抽芯机构。成型连接环内形的型芯,是以凸台A面为分型面,将A面内凸台分成五个独立部分。抽取中间部分可腾出足够空间,再分别抽取其他部分,避开内形二处凸台对连接环脱模的阻挡,以到达脱模的目的。该模具结构方案,能使连接环顺利地成型和脱模。但手工抽取五块模块毕竟效率低下,故只能适应小批量产品的加工。若要实现大批量加工,需将手工抽取五块模块改成自动化抽芯才行。
③连接环高效注塑模结构设计 通过采用了三种不同自动抽芯模具结构,才能够适应制品大批量加工。而要实现注塑模自动抽芯,就必须安排好模具中三种六处抽芯运动的先后程序,这样才能避免抽芯运动干涉现象。通过采用了弯销滑块外抽芯机构、弯销滑块内抽芯机构和单滚轮式斜推杆内抽芯机构,从而实现了避开连接环外形弓形高和外形三处凸台及内形二处凸台“障碍体”对脱模的阻挡作用。又通过采用了复位杆完成推板和前后外滑块的先复位,使得三种六处抽芯运动有序进行。如此,连接环外形和内形左右凸台成型和抽芯是同时进行的。并使得它们先于内形前后凸台抽芯,后于前后凸台复位,这些动作的严格安排,才避免了抽芯运动产生的运动干涉而实现了连接环的顺利成型和脱模。
注塑件的塑料和批量要素,也是影响注塑模结构的因素。注塑件的塑料要素影响到塑料收缩率、模具用钢的选取、模具浇注系统、镶嵌件和塑料性能的运用。注塑件的批量要素影响到模具结构的成型加工效率,即注塑模手动与自动化水平和模具使用寿命的长短。