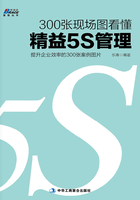
5.5S管理维持要注意的4个问题
非常多的企业推行了5S管理,但80%的企业仅仅是搞卫生,而即使搞卫生仍然有很多企业维持不了、坚持不了。为什么维持不了?笔者根据自身经验来解剖企业5S管理难以维持的幕后凶手。
(1)建立管理标准。
第一大幕后凶手——没建立5S管理标准,就算建立了也模棱两可、难以理解、难以操作,剖析一下三种5S管理标准的差距。
企业5S管理标准大致有三种类型:
第一,潜意识型。这类企业刚有5S管理意识。为什么叫潜意识?因为这类企业几乎没有5S管理检查标准,每次检查凭检查人员的潜意识。靠认为、觉得、好像、还不错、差不多等去判定现场是否合格,甚至看检查人员的心情去判定现场是否合格,这样的检查必然给现场员工造成错觉。今天检查是合格的,明天检查又不合格,后天检查又是一个标准,到底要做成什么样才算好?这也是一些企业普通工人与5S管理检查人员有言语冲突,甚至打架的原因之一。这样的潜意识5S管理检查必然引起员工的愤怒,最终导致大家都厌烦了5S管理。
第二,纯文字型。做到这步的企业在5S管理上花了不少心思,一般来说有专职的5S管理专干或者公司有主要管理部门,如行政部。5S管理标准还有改善的地方,请看表2-1中的箭头1和箭头2。什么叫整齐?整齐是竖着放还是横着放?每个人理解的标准不一样,导致做法也不一样。最终执行的人按自己以为的整齐、不凌乱去执行,检查人员按自己心中的整齐、不凌乱去判定现场,结果可想而知。
第三,图文标准型。就是目前最适合、最接地气、最实用的5S管理标准,员工看了马上知道如何做,检查人员到现场检查再也不会出现言语冲突等问题。好的标准一定要图文并茂,规定好工具的摆放、放置的数量、定量管理。如果现场是这样的5S管理标准,员工执行起来是不是更容易、更方便,管理者管理起来是不是更方便?丰田的《标准操作要领书》把图文并茂利用得淋漓尽致并达到准时化。
思维拓展:图文标准化不仅仅用在5S管理上,所有岗位SOP、操作规程都可以做成图文并茂的操作要领书。
(2)责任区域合理划分。
目前企业的现状有三种:
第一种,按岗位划分,岗位所占的面积就是5S管理的区域。这个方式比较好,缺点是有一些盲点,比如公共区域没划分到。
第二种,A岗位管理的5S区域会涵盖A、B、C岗位的区域。这种方式最不好,容易把事情搞复杂。
第三种,比较好的方式是图文并茂的“岗位定置图+岗位区域图”,如图2-10所示。

图2-10 4S管理区域标准
表2-1 5 S管理对物品卫主的标准要求


制作岗位责任及定置平面图并在现场目视化,让每个人都知道哪一个区域放什么、谁管理。这样就不会出现“我不知道”“我不清楚”“没人告诉我”等借口。
图2-11 责任区平面图
现场的简易定置图所有人都知道,但很多现场什么都没有,只是地上画了一些线而已。
图2-12 平面图
做到现场定置图、责任图目视化管理,再配合5S管理图文并茂的标准,对维持5S管理有巨大帮助。
(3)要坚持检查。
5S管理标准、5S责任区域图(图2-13)建立完毕后,很多公司没有做5S岗位点检表,要养成习惯——必须每天检查,检查必须留下痕迹,这就需要用5S岗位点检表来帮助管理者。5S岗位点检表包含点检项目、点检标准、点检期限、点检人、点检日期。
图2-13 责任区平面图
图2-14对点检内容做了区分。

图2-14 点检内容
表2-2 5 S点检表

整理和整顿:整理的含义就是区分必需品和非必需品,让空间最大化,整顿就是“三定”原则——定品、定量、定位。有的地方可以不需要定量,不要死板地定量。比如维修房的小螺丝、小垫片怎么定量,每天都数吗?每天数工作量非常大,一般根据工作情况,用盒子装半盒或者一盒基本够用就可以;或者用小袋子装螺丝,1个小袋子装100个螺丝,这样做定容管理。
检查项目(检查标准):表格只能用文字大概描述,还要加上一句——具体见岗位5S管理标准,一定要在岗位上贴5S管理标准或者将5S管理标准做成手册。
三级点检:5S点检表是岗位操作工自己填写的。
5S点检表还要设计三级点检保障机制:
第1级:岗位操作工(1天1次)。
第2级:当班班长或组长(3天1次)。
第3级:班长或车间主任(1周1次)。
点检完了必须签字,操作工检查并做记录,班长负责检查操作工的执行情况,车间主任负责检查班长的管理情况。如果按这个检查周期检查,每个岗位严格执行,5S管理维持就不难。没有做5S管理标准、没有责任区域、没有5S检查表定期检查等,员工永远只会做检查的事情,不检查的不做,没有检查就没有执行力。嘴上要求万遍,不如行动检查一遍。
(4)建立奖罚措施。
阻挠5S管理维持的第四大凶手就是没有建立奖罚措施。5S管理标准做好了,5S责任区域做好了,5S管理表也有了,就必须配套奖罚措施,这样才能鼓励做得好的人,警醒做得差的人。如果没有奖罚措施,会导致做得好的岗位或者部门没动力继续保持并持续改善,做得差的岗位或者部门无所谓,反正检查完了又没什么事情,得过且过,长久下去会瓦解所有做的5S管理工作。那么如何建立5S奖罚措施?我分享一下5S奖罚制度的框架。
明确区域:明确检查区域、岗位或者生产线。
明确区域负责人:明确区域的管理人或者负责人,未来5S管理问题由谁承担,一般是部门负责人。
明确检查时间:明确每周检查时间,很多企业是周五,上午或者下午自己定。
明确检查人员:哪些人是检查人员?应为涉及区域部门的第一负责人,必须这样设计,如果只是为各部门代表,力度不大,根本维持不了。
明确检查评分标准:评分不仅有扣分项目,还要有加分项目。加分项目设计内容为部门负责人参加检查加5分/次,员工答对5S问题也可以加2~5分。评分不要死板,只知道列出扣分项,还要激发员工自主维持、持续改善,要通过加分项激发员工。看5S奖罚制度好不好,就看扣分标准有没有加分项,有没有激发员工的制度。
明确奖罚:记住,奖励需要前面五项条款做支撑,不是觉得哪个好就奖励哪一个。奖罚比例一般是8(奖):2(罚),尽量通过“奖”来激励员工,不要一味地罚罚罚,罚了几次,会被罚崩盘,没人陪你继续“玩”5S管理。
请记住奖罚二原则:
第一,领导主责。如果一个部门5S管理做得不好,部门领导要负90%以上的管理责任,因为是他管理能力不行或者不重视,导致本部门连最基础的5S管理都做不好。处罚先处罚部门领导,连续3次以上评比最后一名建议撤职处理。
第二,奖励基层。部门评比下来,80%的奖励要发给基层员工,继续激励员工保持并持续改善。颁奖形式各种各样,如流动红旗、证书、红包等。
总结:
“5S管理一紧二松三垮台四重来。”这句话非常有道理,说出了各企业做5S管理的现状。能发现现状就是好事情,有现状我们就要进行分析,连续要问5个为什么。
为什么会紧?三分钟热度:刚开始大家觉得很新鲜,做试点打造,上面抓得很紧,兴致勃勃地管理,甚至抛开生产做5S管理。这本身就是错误的,企业要活必须有利润,没有生产就没有利润。抛开生产做5S管理是巨大的错误,只能利用生产间隙见缝插针地做。
为什么会松?急功近利。任何事物发展都有规律,急功近利,短时间紧抓5S管理想达到预期很难。我的做法是300人左右的企业要达到预期效果,要6个月左右时间。很多企业刚开始几个月抓得很紧,后面看到效果不如预期就开始动摇、放松,开始考虑放弃。
为什么会垮台?有了松动的想法,就开始视而不见或者口是心非,只是嘴巴上说要做,其实没有实际行动。特别是企业一把手没有实际行动,上行下效,中层能感觉到一把手是否真正要做变革、要做5S管理。只有一把手亲自做了,才能带动中层去做,开会解决不了问题,要行动、要实践。企业一把手(老板、总经理)对5S管理的态度是只开会、只提要求、喊口号,不亲自行动、不亲自实践是5S管理垮台的信号。
为什么要重来?企业一把手的态度导致5S管理垮台,又重新说明企业一把手要具备敢于创新、突破传统思维的思想。你要做的任何东西,99%这个世界上已经有人解决,你只要找到那个人就可以。企业要做5S管理,为什么不去咨询一些已经会的人,去请教一些老师?为什么一定要自己摸索?一张白纸被画得不成样,再请人辅导就很难画出心仪的画。
企业为什么要自己开展5S管理?因为自认为5S管理就是搞卫生、大扫除。这样的思维阻碍了企业学习专业的5S管理方法及知识。不如换个角度思考。因为某件事情要打官司,为什么会直接请律师而不是直接打官司,或买基本法律书籍学习后再去打官司?因为我们知道自己不了解法律。