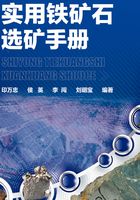
3.3 赤铁矿选矿工艺
3.3.1 赤铁矿石选矿工艺的进步
赤铁矿石是一种弱磁性铁矿石,所用选矿方法较多,包括重选、浮选、强磁选、焙烧磁选及几种方法的联合流程。近年来,普遍应用既有并联又有串联组合的联合流程。如鞍山地区的贫赤铁矿石采用重选、磁选及浮选联合流程,获得精矿铁品位在65%~67%的高指标。
(1)单一赤铁矿石
这类矿石包括沉积变质、沉积型、热液型及风化型矿床的赤铁矿石、菱铁矿石、褐铁矿石和赤(镜铁)-菱铁矿石等。常用的选矿方法有两种:磁化焙烧磁选和重选、浮选、强磁选及其联合流程。
①磁化焙烧磁选。焙烧磁选是选别细粒到微粒(<0.02mm)赤铁矿的有效方法之一。当矿物组成比较复杂,而其他选矿方法难以获得良好的选别指标时,往往采用磁化焙烧磁选法。75~20mm块矿的竖炉还原焙烧工艺成熟,有长期生产实践经验;20~0mm回转炉磁化焙烧生产实践较少。对粉矿常用强磁选、重选、浮选等方法及其联合流程进行选别。
②重选、浮选、强磁选及其联合流程。浮选是选别细粒到微粒赤铁矿石的常用方法之一,分正浮选和反浮选。重选和强磁选主要用于选别粗粒(20~2mm)和中粒赤铁矿石,随着技术上的发展,也用来选别细粒赤铁矿石。块状(>20mm)和粗粒矿石的重选,常用重介质或跳汰选矿法;中、细粒矿石的重选,则用螺旋选矿机、摇床和离心选矿机等流膜选矿法。
粗、中粒矿石的强磁选常用感应辊式强磁选机,细粒矿石的强磁选常用湿式感应介质立环、平环强磁选机和脉动高梯度磁选机。目前由于细粒矿石的强磁精矿品位不高,而重选处理能力又低,所以常组成强磁选-重选和强磁选-浮选联合流程,强磁选丢弃大量合格尾矿,重选和浮选进一步处理强磁选精矿,以进一步提高铁品位。
各种选矿方法及其联合流程的应用,随矿石类型而异。沉积变质型赤铁矿石和沉积变质型镜铁-菱铁矿石都呈细粒嵌布,生产上几乎采用了所有的选矿方法。沉积型鲕状赤铁矿石和赤铁-菱铁矿石,铁矿物常为细粒嵌布,且与脉石矿物紧密共生呈鲕状结构,不易单体解离,此类较难选。如果是富矿或自熔性矿石,常用重介质、跳汰或干式强磁选等方法剔除脉石矿物,得到块状成品铁矿石。如果是较富的鲕状矿石,常用焙烧磁选法,有时在焙烧磁选前先预选除去块状脉石矿物。对于较贫的鲕粒矿石,即使采用焙烧磁选,精矿品位也难以达到50%以上,因此常在提出围岩后与其他高品位精矿配矿使用或采用直接还原等选冶联合方法。热液型石英质赤铁矿石和赤铁-褐铁矿石,常为不均匀嵌布,多采用重选、强磁选、浮选等方法的联合流程。
赤铁矿可选性差,一直是我国选矿界的一大难题。近年来,赤铁矿选矿技术取得了重大突破,我国“贫赤铁矿选矿工艺技术”居国际领先水平,以鞍钢集团矿业公司赤铁矿选矿工艺最为成功,代表了国内赤铁矿选矿工艺发展的最高水平。目前鞍山地区的贫赤铁矿选矿厂主要采用阶段磨矿,粗细分选,重选-磁选-反浮选流程。
(2)含多金属赤铁矿石
它主要是热液型和沉积型含磷或含硫化物的赤铁矿石和菱铁矿石。此类矿石一般用重选、浮选、强磁选或其他联合流程回收铁矿物,用浮选回收磷或硫化物。热液型含磷灰石赤铁矿石和含铜、硫菱铁矿石可以用浮选法处理。沉积型含磷鲕状赤铁矿石,磷呈胶磷矿状态,虽然可用浮选法使之与铁矿物分离,但往往难以富集成磷精矿,使铁回收率降低甚多。沉积型含磷鲕状赤铁矿石的开发,可以考虑采用重选或磁选对矿石进行粗粒预选,剔除大粒度围岩、夹石,恢复矿石的地质品位,然后全烧结入炉冶炼,生产高磷生铁,再以转炉炼钢,同时生产钢渣磷肥。该方法的优点在于选矿方法简单,避免了细磨深选降磷、除硅、除铝的复杂工艺,而且保持了矿石的自熔性,使磷得到充分利用。
(3)磁铁-赤(菱)铁矿石混合矿石
①单一磁铁-赤(菱)铁矿石。单一磁铁-赤(菱)铁矿石主要是沉积变质型磁铁矿石和磁铁-菱铁矿石。此类矿石常用的选矿方法有两种:一是弱磁选与重选、浮选、强磁选联合流程,用弱磁选回收磁铁矿,用重选、浮选或强磁选回收弱磁性铁矿物的联合流程,该流程用得较多;二是磁化焙烧磁选法或其他选矿方法的联合流程,该磁化焙烧磁选与单一赤铁矿石的磁化焙烧磁选流程相似,但在与其他选矿方法的并联流程中,粉矿采用弱磁选联合其他选矿方法处理。此外也有焙烧磁选与其他选矿方法的串联流程,即焙烧磁选精矿再用浮选或重选精选,以进一步提高精矿品位。微粒嵌布的磁铁-赤铁矿石,用一般选矿方法难于得到良好效果,应采用选择性絮凝脱泥、絮凝浮选、絮凝强磁选和絮凝重选等方法。
②含多金属磁铁-赤(菱)铁矿石。属于此类矿石的有矽卡岩型含硫化物的混合铁矿石和热液型含磷、硫或稀土的混合铁矿石。此类矿石的选矿方法是铁矿石中最为复杂的。一般都用弱磁选与其他选矿方法的联合流程,即用弱磁选回收磁铁矿;重选、浮选或强磁选回收弱磁性赤(菱)铁矿物;用浮选回收伴生组分。流程包括:弱磁选-浮选-强磁选、弱磁选-强磁选-浮选和弱磁选-重选-浮选等。对于含稀土的混合铁矿石,如果铁矿物以大量赤铁矿为主,也有采用还原焙烧磁选-浮选流程,即用还原焙烧回收赤铁矿矿物,用浮选回收稀土矿物。稀土矿物在还原焙烧后进行浮选,有利于提高选别指标。此外,浮选-选择性絮凝流程也可获得高指标。
3.3.2 典型工艺流程和生产实践
在赤铁矿的工艺流程方面,主要体现在赤铁矿的阴离子反浮选技术的应用。我国赤铁矿资源储量大,可选性差,主要分布在辽宁、河北、甘肃、安徽、内蒙古、河南、湖北、山西、贵州等地。赤铁矿选矿一直是我国选矿界的一大难题。20世纪50~70年代,主流技术是焙烧-磁选和单一浮选。生产指标较差,鞍钢东鞍山选矿厂是处理能力最大的贫赤铁矿浮选厂,精矿品位<62%,回收率<70%;处理难选矿时,精矿品位<59%,回收率仅46%左右。2001年来,鞍钢调军台选矿厂、齐大山选矿厂、东鞍山选矿厂和舞阳矿业公司成功地研究出连续磨矿-弱磁-强磁-阴离子反浮选、阶段磨矿-粗细分选-重-磁-阴离子反浮选和阶段磨矿-粗细分选-磁-重-阴离子反浮选全套工艺流程,并配套开发了新型高效阴离子捕收剂(RA系列和MZ系列)和相应的药剂制度,在国内外首次成功地将阴离子反浮选技术工业应用于赤铁矿选矿,在调军台选矿厂取得精矿品位66.80%、SiO2含量3.90%、精矿回收率84.28%的指标,在齐大山选矿厂取得精矿品位67.10%、SiO2含量4.50%、精矿回收率72%的指标,两个选矿厂的选矿技术经济指标达到国际领先水平。东鞍山选矿厂铁精矿品位达到了65%以上,取得历史性突破。这一创新性的成果为阴离子反浮选在我国赤铁矿选矿厂的推广应用起到了示范作用。此后司家营选矿厂、舞阳红铁矿选矿厂、弓长岭红铁矿选矿厂均按此流程新建或改建,并取得成功。至此,我国赤铁矿选矿技术取得了突破性进展,全行业技术水平和经济效益得到大幅提升。
3.3.2.1 连续磨矿-弱磁-强磁-阴离子反浮选工艺
鞍钢齐大山铁矿选矿分厂(简称调军台选矿厂)是国内最大的红铁矿选矿厂,设计年处理铁矿石900万吨,年产铁精矿300万吨,采用的工艺流程是连续磨矿、弱磁-强磁-阴离子反浮选工艺。该艺流程研究工作正式始于1984年,是国家“七五”重点攻关项目,由以长沙矿冶研究院、鞍钢集团鞍山矿业公司研究所、马鞍山矿山研究院为主的多家研究单位共同完成。这些研究单位于1984年1月至1987年5月间完成了多个工艺流程的实验室研究、实验室扩大试验研究工作;于1987年6月至1990年12月间完成了优化后的3个工艺流程的工业试验研究工作,最终选定连续磨矿、弱磁-强磁-阴离子反浮选工艺作为鞍钢齐大山铁矿选矿分厂新建选矿厂的工艺流程。1998年3月该选矿厂投产以来,选矿技术指标连年提高,2003年实现原矿处理量677万吨,精矿产量263万吨,原矿品位29.86%,铁精矿品位67.54%,尾矿品位8.31%,金属回收率82.32%的技术指标,经济效益4亿元以上,具有国际领先水平。由于齐大山铁矿选矿分厂是全国首家率先应用阴离子反浮选工艺的厂家,对阴离子反浮选工艺在我国的应用起到了先导作用,较好地推动了该工艺流程在我国的应用。2005年全年生产技术指标:原矿品位29.50%,铁精矿品位67.61%,尾矿品位9.21%,金属回收率79.65%。
鞍钢齐大山铁矿选矿分厂原来采用“连续磨矿-弱磁-强磁-阴离子反浮选”工艺流程,如图3.26所示。

图3.26 鞍钢齐大山铁矿选矿分厂“连续磨矿-弱磁-强磁-阴离子反浮选”工艺流程图
其工艺流程具有以下特点:
①强磁选与阴离子反浮选的结合有利于实现工艺流程的优势互补,这不仅表现在两个工艺本身提质降尾上,也表现在强磁选能为反浮选提供良好的选别条件上。
②该工艺流程便于生产稳定操作。据铁矿石嵌布粒度细的特点,连续磨矿工艺直接将矿石磨至单体解离度较高的水平,避免了阶段磨矿中矿再磨量的波动较大和效率不高给流程带来负面影响的问题;另外,用强磁机脱泥抛尾,既为阴离子反浮选工艺准备了较高品位的入选物料,也消除了原生矿泥和次生矿泥对阴离子反浮选工艺的影响,且强磁选本身具有较好的稳定性。阴离子反浮选本身由于强磁选为其提供了较好入选物料,故也具有较好的稳定性。因此,“连续磨矿、弱磁-强磁-阴离子反浮选”工艺控制好最终磨矿粒度后,工艺具有较好的稳定性,对矿石具有较强的适应性,便于生产稳定操作。
③该工艺流程具有较好的工艺操作特点。由于该工艺具有精矿品位高、浮选温度低、适于管道运输、分选效果好、浮选泡沫稳定性好、流动性好等工艺特点,在生产操作上易于控制,有利于生产指标的稳定。
④该工艺流程存在因为磨矿粒度细而导致选矿成本高的问题。
3.3.2.2 阶段磨矿、粗细分选、重选-磁选-阴离子反浮选工艺
目前鞍山地区的贫赤铁矿选矿厂主要采用阶段磨矿,粗细分级,重选-磁选-反浮选流程,即原矿经一段磨矿分级后,一次溢流经水力旋流器粗细分级,粗粒产品由重选处理,细粒经弱磁和强磁选别,混合磁精矿反浮选,粗、细粒二者均产出最终精矿。重选精螺尾与扫螺精经扫中磁后的扫中磁精再磨返回水力旋流器。扫中磁尾、强磁尾和反浮选尾矿合并为综合尾矿。鞍钢齐大山、东鞍山烧结厂阶段磨矿、粗细分选、重-磁-阴离子反浮选工艺流程如图3.27所示。其工艺流程具有以下特点:

图3.27 鞍钢齐大山、东鞍山烧结厂阶段磨矿、粗细分选、重-磁-阴离子反浮选工艺流程图
①鞍钢齐大山铁矿、东鞍山烧结厂和弓长岭铁矿三选车间的阶段磨矿、粗细分选、重选-磁选-阴离子反浮选工艺流程,采用了阶段磨选的工艺,使得该工艺流程具有较为经济的选矿成本。一段磨矿后,在较粗的粒度下实现分级入选,一般情况下可提取60%左右的粗粒级精矿和尾矿,这大大地减轻了进入二段磨矿的量,有利于降低成本。同时,粗粒级铁精矿有利于过滤。
②该工艺选别针对性强。矿物在磨矿过程中解离是随机的,这种过程使得磨矿粒度不等的矿物颗粒均存在解离的条件,这是粗细分级入选工艺具有较强生命力的重要基础之一。阶段磨矿、粗细分选、重选-磁选-阴离子反浮选工艺一次分级后的粗粒级相对好选,采用简单的重选工艺,及时选出合格粗粒精矿,抛掉粗粒尾矿;分级后的细粒级相对难选,采用选矿效率高相对复杂的强磁-阴离子反浮选工艺获得最终精矿,并抛除最终尾矿。粗粒级选矿方法和细粒级选矿方法的有效组合使得该工艺流程具有经济上合理、技术上先进的双重特点。同时,重选工艺获得含量较大、粒度较粗的精矿有利于精矿过滤。
③该工艺实现了窄级别入选的合理过程。在矿物的选别过程中,矿物的可选程度既与矿物本身特性有关,也与矿物颗粒比表面积大小有关,这种作用在浮选过程中表现的更为突出。因为在浮选过程中,浮选药剂和矿物之间的作用与气泡间作用力的最小值有关,与矿物比表面积大小有关,与药剂跟矿物作用面积的比率有关。这使得影响矿物可浮性的因素是双重的,容易导致比表面积大而相对难浮的矿物与比表面积小而相对易浮的矿物具有相对一致的可浮性,有时前者甚至具有更好的可浮性。实现窄级别入选的选矿过程,能在较大程度上杜绝上述容易导致浮选过程混乱的现象的发生,提高选矿效率。
④该工艺对细粒级选别效率有很大的提高。阶段磨矿、粗细分选、重选-磁选-阴离子反浮选工艺应用前,红铁矿选矿应用的阶段磨选工艺细粒级采用的工艺是磁-酸性正浮选工艺,选矿效率很低,影响阶段磨选工艺技术指标的提高。而将细粒选别工艺由磁-酸性正浮选改为磁-阴离子反浮选工艺形成现在的阶段磨矿、粗细分选、重选-磁选-阴离子反浮选工艺后,细粒级的选别指标得到了空前的提高。
以鞍钢齐大山选矿厂工艺改造前后考查为例,细粒级应用磁-酸性正浮选的技术指标为:入选品位23.77%,精矿品位60.65%,尾矿品位13.30%;细粒级应用磁-阴离子反浮选的技术指标为:入选品位23.83%,精矿品位65.72%,尾矿品位13.16%。显然,在阶段磨选工艺中,细粒级应用磁选-阴离子反浮选工艺比应用磁选-酸性正浮选工艺使细粒级选别效率得到了空前的提高。
⑤阶段磨矿、粗细分选、重选-磁选-阴离子反浮选工艺也存在工艺流程线长、二段磨矿效率低等问题。
3.3.2.3 阶段磨矿、粗细分选、磁选-重选-阴离子反浮选工艺
安钢舞阳矿业公司具有较多的红铁矿资源。由于其红铁矿内存在碧玉,具有比石英更大的密度和磁性,使其与铁矿物分离变得较为困难。早期,长沙矿冶研究院为之进行了大量的工作,取得了一定成效。进入21世纪,选矿技术水平得到了较大的提高,新工艺、新药剂、新设备得以较快发展。在此情况下,舞阳矿业公司决定加快其红铁矿研究步伐。先后委托马鞍山矿山研究院、鞍钢矿山研究所进行选矿试验研究,马鞍山矿山研究院为此进行了大量的工作,先后完成了多个工艺流程的探索性研究,并就强磁-反浮选工艺、强磁-重选-反浮选工艺进行了连选试验研究。其中强磁-反浮选工艺取得了原矿品位28.86%、精矿品位65.02%、尾矿品位12.31%、金属回收率70.74%的指标;强磁-重选-反浮选工艺取得了原矿品位28.79%、精矿品位65.22%、尾矿品位11.26%、金属回收率72.56%的指标。最终推荐阶段磨矿、粗细分选、强磁-重选-阴离子反浮选工艺为建厂工艺。
安钢舞阳铁山庙铁矿阶段磨矿、粗细分选、磁-重-阴离子反浮选工艺流程如图3.28所示。

图3.28 安钢舞阳铁山庙铁矿阶段磨矿、粗细分选、磁-重-阴离子反浮选工艺流程图
其工艺流程具有以下特点:
①阶段磨矿、粗细分选、磁选-重选-阴离子反浮选工艺,其阶段磨选工艺与阶段磨矿、粗细分选、重选-磁选-阴离子反浮选工艺一致,由于采用了阶段磨选工艺,减少了二段磨矿量,比较经济。
②与阶段磨矿、粗细分选、重选-磁选-阴离子反浮选工艺不同的是:该工艺将使得二段磨矿量比阶段磨矿、粗细分级、重选-磁选-阴离子反浮选工艺明显增加。这是因为采用阶段磨矿、粗细分选、重选-磁选-阴离子反浮选工艺,粗粒部分和细粒部分分别用中磁机和强磁机抛尾。中磁机与强磁机的场强差别较大,表明粗粒矿物比细粒矿物在磁场中具有较好的磁选效果。这样,在应用阶段磨矿、粗细分选、磁选-重选-阴离子反浮选工艺中,由于粗粒尾矿和细粒尾矿和在一起用强磁机抛尾,相对粗粒级来讲,抛尾场强过高,使得粗粒级贫连生体难以抛掉。
③强磁预先抛尾对后续作业影响较大。强磁预先抛掉的尾矿量一般在45%以上,大大减少了后续作业入选矿量,节约了设备。与此同时,经过强磁预先抛尾后,进入后续强磁作业的矿石入选品位较高,有利于重选作业提高精矿品位。但是,由于该工艺流程强磁预先抛尾后,使得相对较粗的贫连生体进入到强精中,加剧了后续分级旋流器的反富集作用,对反浮选作业不利。
④二次磨矿控制比较重要。采用该工艺流程后,由于二段磨矿产品进入粗细分级旋流器,没有进行脱泥抛尾直接给入重选及反浮选作业,容易对重选特别是反浮选效果产生不利的影响。
⑤粗细分级旋流器的控制比较关键。经过强磁预先抛尾后,强磁精矿的品位一般提高到45%以上。这样高品位的物料进入粗细分级旋流器显然没有30%的原矿容易取得好的分级效果。因此,与阶段磨矿、粗细分选、重选-磁选-阴离子反浮选工艺相比,该工艺应加强对粗细分级旋流器的控制。
3.3.3 微细嵌布赤铁矿选矿技术与实践
3.3.3.1 微细嵌布赤铁矿的选矿技术
细粒嵌布赤铁矿的常用选矿方法如下:
①赤铁矿全浮选流程。采用脂肪酸类阴离子捕收剂,碳酸钠作矿浆调整剂(矿浆pH值为9~10),浮选赤铁石英岩类型矿石中的赤铁矿,解决了矿浆黏度大、精矿脱水难等问题。采用二段浓缩作业,降低了金属流失。
②强磁-浮选流程。主要特点是通过强磁选将矿石中的单体石英和易泥化的绿泥石等脉石矿物在粗磨条件下排出,成为合格精矿,从而为进一步细磨和浮选创造有利条件。
③焙烧-磁选流程。采用竖炉对20~75mm赤铁矿石,以焦炉和高炉混合煤气加热与还原,生成人造磁铁矿石,再进行磁选获得铁精矿产品。
④焙烧磁选-反浮选流程。为了提高焙烧磁选铁精矿质量,采用十二胺阳离子捕收剂,在中性矿浆中进行反浮选。
⑤强磁选流程。俄罗斯中央采选联合企业克里沃罗格矿床为氧化铁质石英岩,1989年由磁化焙烧改为强磁选。新流程投入运行后解决了焙烧产生的灰尘和废气净化问题,且解决了能耗问题,用当量燃料吨数表示的总能耗由磁化焙烧工艺的0.202降到强磁选工艺的0.054,是氧化铁质石英岩选矿的重大进展。
⑥阶段磨矿、重磁-阴离子反浮选流程。齐大山选矿厂采用高效低耗无毒新药剂和SLon型立环脉动高梯度强磁机,在金属回收率没有降低并保持选厂原有生产能力的条件下,铁精矿品位达到67.14%,选矿药剂费用降低24.89%,淘汰了传统的焙烧磁选工艺,能耗费用降低48.93%,精矿加工成本降低3.28%,还杜绝了焙烧使用煤气造成的人身安全和环境污染问题。
⑦正浮选法和选择性絮凝脱泥反浮选法。美国针对细粒嵌布赤铁矿石主要采用浮选方法处理。浮选存在正浮选法和选择性絮凝脱泥反浮选法两种。正浮选采用塔尔油作捕收剂,这和我国东鞍山浮选厂相同,但在流程中它们有预先脱泥作业,浮选在中性矿浆中进行,从而使精矿过滤比较容易,滤饼水分也低。选择性絮凝脱泥反浮选是1974年才用于生产的新工艺,经过生产实践证明是成功的。这项新工艺较为突出的两点是:采用极细磨矿(-0.025mm占80%)和以玉米淀粉作选择性絮凝剂及反浮选中铁矿物的抑制剂。矿石在自磨机、砾磨机、三层振动筛和分级水力旋流器组成的回路中细磨,在自磨机中加入烧碱及水玻璃,调整矿浆pH值至10.5~11。分级水力旋流器溢流粒度控制在-0.025mm占80%,溢流中加入玉米淀粉,使铁矿物絮凝而石英继续保持悬浮状态并在脱泥浓密机内排出,浓密机底流即为初步得到富集的铁矿。蒂尔登浮选厂经过这一选择性絮凝脱泥作业,使含铁35%的原矿提高到含铁44%的浓密机底流。此底流给入浮选系统,在浮选过程中加入玉米淀粉作铁矿物的抑制剂,用醚胺类阳离子捕收剂进行反浮选,得到铁精矿品位65%、含SiO25%、回收率为70%的生产指标。
由于精矿粒度极细,为了过滤作业的顺利进行,采取了下列几项措施,以期达到滤饼水分不超过11%,否则在造球前必须进行干燥:
①精矿过滤前通入CO2,调整pH值至中性;
②加入表面活性剂Aerodri104,以降低水的表面张力;
③加入聚合物絮凝剂CatflocV.C.,以团聚精矿粉;
④在过滤机上加罩,通入蒸汽,加速滤饼脱水。
这一新工艺对水质的要求是:钙离子浓度应低于40×10-6,悬浮物不高于500×10-6。由于操作条件比较严格,药剂种类繁多,尤其是玉米淀粉的制备和精矿过滤比较困难,现场生产人员对此并不满意。但是对细粒赤铁矿的选矿,他们认为舍此尚无其他更好的途径。因此,美国寄托很大的希望,用这一新工艺来开发默萨比矿带150亿~200亿吨氧化铁隧岩的资源。美国矿务局双城研究中心用选择性絮凝反浮选和强磁选的联合流程对默萨比西部氧化铁隧岩进行试验。据美国矿务局双城研究中心的介绍,采用选择性絮凝反浮选工艺时,原矿中含水铁矿物如针铁矿、褐铁矿等不能太多,否则这些含水铁矿物在脱泥作业中随石英一起流失,使铁的回收率大幅度降低。
低成本开发微细粒赤铁矿,选矿技术方面的工作仍然是围绕着能丢早丢,能收早收,最大限度提高效率、节约成本而进行的,除了要重视多碎少磨、阶段磨选外,还有如下三个方面的工作应引起重视:
(1)选择性高效磨矿技术
磨不细与过磨现象并存是微细粒选矿技术中最突出的问题,有针对性地磨矿并在第一时间将已经磨好的合格粒级矿石高效分级出来,是减少过磨、提高选矿效率最关键的环节。世界著名选矿学者A.F.塔加尔特曾明确指出:“磨矿的功用和目的依其所磨原料的不同而不同。在选矿厂主要的任务是将矿物原料粉碎,以使有用矿物大部分得以从脉石中解离出来,并在许多情况下使两种有用矿物互相分离开来;其次一个任务是将单体的有用矿物依其粒度的必要缩小程度,将粒度减小,以使它们在下一个选矿过程中(如浮选过程)得以有不同的性态表现”。可见,A.F.塔加尔特把解离矿物列为磨矿的主要任务及首要任务,而减小粒度仅列为其次的任务。我国著名磨矿专家李启衡教授指出,碎矿和磨矿就是为选别准备好解离充分但过粉碎轻的入选物料,这就是碎矿和磨矿的基本任务。机械地靠减小矿粒尺寸来提高解离度,必然造成解离不够和过粉碎并存的现象。但如果能使矿物沿矿物间的接触面选择性解离,则可以使矿物充分解离并显著放粗磨矿细度。可见,使铁矿物充分单体解离却不过粉碎,使有利于分选的有效粒级含量最大化是微细粒嵌布铁矿及褐铁矿选矿中要解决的关键技术难题。但目前大家普遍关注磨矿细度,却很少从追求充分解离下的有效分选粒度着手研究磨矿技术,因而在矿山工作中形成充分解离比磨矿细度更加重要的意识是推进选择性磨矿实施的前提。实践证明,选择性磨矿由于在提高有用矿物单体解离度的前提下能有效放粗磨矿细度,减少过粉碎,从而可优化入选物料矿物组成,达到品位和回收率双提高的目的。
(2)超细磨技术
超细磨矿成本高是制约微细粒贫赤铁矿开发利用的关键因素。采用普通球磨机磨矿,随着磨矿细度的增加,新生合格粒级含量显著减少,而单位磨矿能耗成倍增加。当磨矿细度要求20μm占80%以下时,塔磨机、搅拌磨机和ISA磨机均是很好的选择。据资料介绍,在某黄铁矿精矿再磨时,当达到磨矿细度12μm占80%时,球磨机(球介质直径9mm)需要超过120kW·h/t的电耗,而ISA磨机(介质直径2mm)仅需要40kW·h/t,节能效果显著。但尽管塔磨机、ISA磨等超细磨设备已经在很多大型铁矿应用,但较高的设备价格及ISA磨近期难以在中国市场应用的现实制约了其在国内铁矿山尤其是中小型矿山的应用。对铁矿物嵌布粒度微细的中小型铁矿山而言,长沙矿冶研究院开发的立式搅拌磨作为最终细磨设备是较好的选择。与球磨机相比,立式搅拌磨用于产品细度要求为40~20μm的磨矿,能耗减少70%。立式磨矿机已经能达到5μm的磨矿粒度下限。目前立式搅拌磨已在非金属和有色金属磨矿中使用了60多台,在给矿细度为180μm占80%时,磨矿细度达到20μm占80%,效果显著。如湖南柿竹园有色金属矿铁精矿的再磨再选,过去多年来都是采用普通卧式球磨机,磨矿粒度一直都是-43μm占60%,铁品位在53%~55%之间,磨矿细度达不到,铁精矿品位不能提高。经过多次试验,柿竹园有色金属矿铁精矿再磨设备采用长沙矿冶研究院研制的立式螺旋搅拌磨矿机。从2005年开始在柿竹园有色金属矿尾矿回收铁精矿生产线上应用,磨矿粒度-38μm达到95.10%,铁精矿品位达到65%以上,提高了铁精矿品位,经济效益显著。
(3)强磁选技术
强磁选设备是回收赤铁矿的关键设备,但强磁选设备回收铁矿物时-30μm的微细粒赤铁矿流失严重,细粒铁矿物回收率不到30%的问题始终无法解决。2008年以来,长沙矿冶研究院采用新型高效ZH-Ⅰ型组合式湿式强磁选机作为回收微细粒弱磁性赤(褐)铁矿的关键设备,取得了满意效果。该机采用隔粗筛加三道分选盘式结构,前置专门配套的隔粗装置隔除矿浆中的粗渣,分选主体采用梯度高达1.0T的多层感应磁极介质及三盘对应的介质参数,形成上盘0.1~0.3T磁感应强度的弱磁选体系,以回收少量强磁性的Fe3O4;中盘是1~1.5T磁感应强度的中磁选体系,用于回收中粗粒级赤铁矿及假象赤铁矿,下盘磁感应强度高达1.7~1.8T,对回收微细粒赤铁矿及易泥化的褐铁矿极其有效。这种设备相对于目前工业上常用的SHP仿琼斯强磁选机和SLon强磁选机,由于下盘磁感应强度高出0.8T,铁回收率要高出10个百分点以上,且由于对不同磁性的铁矿物分阶段选别,大幅度减少了磁性夹杂,某些赤褐铁矿选矿厂使用该设备甚至实现全磁选流程将铁精矿品位提高到65%以上,而传统的磁选机由于只有一种磁场强度,磁夹杂严重,磁选铁精矿品位只能提高到43%~47%,必须采用浮选进一步选别才能得到65%以上品位的铁精矿。ZH-Ⅰ型强磁选设备比单一功能的磁选机功能强,操作简易,占地少,电耗少。由于前端隔粗和隔磁,完全消除了粗杂碎屑物堵塞和磁性堵塞,分选畅通无阻,强磁分段磁选效果十分明显,具有很好且更广泛的实用性。
(4)细粒浮选技术及高效浮选药剂
自鞍钢集团矿业公司东鞍山烧结厂于1958年开始采用浮选分选铁矿石以来,我国氧化铁矿石选矿技术已经取得长足进步,尤其是在国家科技攻关项目的支持下,鞍山式磁、赤铁矿选矿技术已经达到世界领先水平,长沙矿冶研究院张泾生教授开创并成功应用于鞍钢调军台选矿厂的弱磁选-强磁选-阴离子反浮选工艺流程已成为此类矿石的经典流程,在我国大中型铁矿山选矿厂如齐大山选矿厂、调军台选矿厂、弓长岭选矿厂、尖山铁矿选矿厂、司家营铁矿选矿厂、舞阳铁矿选矿厂中广泛推广应用。伴随该工艺流程而开发的NaOH、苛化淀粉、石灰和脂肪酸类捕收剂也成为经典的药剂制度而沿用至今。虽然近年来各研究院所及企业在阴离子捕收剂种类上推陈出新、百家争鸣,但20多年来始终没有超越该工艺流程开发之初所确立的原则工艺流程、四种反浮选药剂、30℃以上的浮选温度等关键技术根本。为了解决微细粒铁矿浮选效果差,尾矿夹带严重影响精矿质量的问题,长沙矿冶研究院以太钢袁家村铁矿、湖南祁东铁矿等典型的微细粒铁矿为研究对象,进行了以减少矿泥干扰、提高铁精矿质量、同时降低浮选成本为目标的新药剂开发,研制的新型阴离子浮选药剂成功实现了两种浮选药剂(调整剂和捕收剂)常温(15℃)浮选的目标,该药剂已经完成了工业试用,结果理想。
3.3.3.2 微细嵌布赤铁矿的选矿实践
(1)太钢袁家村铁矿
太钢袁家村铁矿属于微细粒嵌布的鞍山式赤铁矿石,属大型铁矿床,保有储量有13多亿吨。矿床中矿石有多种类型,主要可分为氧化铁矿石和原生铁矿石。氧化铁矿石又可分为石英型、镜(赤)铁矿型、闪石型和砾岩型;原生铁矿石又可分为石英型和闪石型。每种矿石依据铁品位的不同,还有贫铁矿石和次贫铁矿石之分。由于袁家村铁矿石类型较多,结构、构造复杂,各种矿物嵌布粒度微细,给选矿造成很大难度,致使到目前为止尚未全面开发利用。石英型和闪石型氧化铁矿石的多元素分析和铁物相分析分别见表3.30~表3.33。
表3.30 石英型氧化矿的化学多元素分析

表3.31 闪石型氧化矿的化学多元素分析

表3.32 石英型氧化矿的铁物相分析

表3.33 闪石型氧化矿的铁物相分析

两种氧化矿石中的金属矿物均以假象赤铁矿、半假象赤铁矿、赤铁矿、镜铁矿为主,其次为磁铁矿、褐铁矿、黄铁矿等。脉石矿物主要为石英、闪石类矿物(透闪石、镁铁闪石、少量铁闪石)和方解石等。两种氧化矿石均以条带状构造为主,在金属矿物条带中嵌布有细粒的脉石矿物,在脉石矿物条带中嵌布有细粒的金属矿物。金属矿物和脉石矿物的结晶粒度均极细。石英型矿石中金属矿物粒度多在0.045mm以下,有部分极细者粒度在0.01mm以下;脉石矿物粒度较金属矿物稍粗,多在0.05mm以下,相当数量粒度在0.01mm以下。闪石型矿石的矿物粒度比石英型矿石粒度略粗,但闪石型矿物因纤维结构较多,且纤维直径通常仅几微米,造成解离困难。
2005年中钢集团马鞍山矿山研究院对石英型原生铁矿石:石英型氧化铁矿石:镜(赤)铁矿型氧化铁矿石为3:1:1的矿样,采用阶段磨矿-弱磁-强磁-反浮选工艺(工艺流程如图3.29所示),即矿样先磨至-0.076mm占85%后进行1次弱磁选,其尾矿经强磁1次粗选1次扫选,弱磁选和强磁选的混合粗精矿再磨至-0.037mm占85%,通过阴离子反浮选1次粗选、1次精选、3次扫选得到最终精矿。该工艺采取了细磨、高效强磁选设备及高效阴离子反浮选捕收剂等手段,混合样的选矿试验获得了精矿铁品位65.36%、回收率82.03%的较好指标,为太钢(集团)公司开发袁家村铁矿石提供了重要技术依据。

图3.29 混合样阶段磨矿-弱磁-强磁-反浮选工艺流程图
(2)鞍钢关宝山铁矿
关宝山铁矿位于鞍山市东南20km,眼前山铁矿西侧,东起关宝山,西至三印子,南以河谷为限,北至马圈子。其地理坐标为北纬41°04'17″,东经123°08'13″。矿区交通十分便利。本地区属山地。海拔高度在96~176m,相对高差80m。年平均气温为8.6℃左右,最高为七月,达26℃以上,最低气温为一月份,达-14℃以下。年平均降雨量为729.5mm,月平均降雨量185.5mm。关宝山铁矿原隶属于眼前山铁矿一个采区。1970年开始筹建,1972年由鞍钢设计院完成初步设计。设计确定一期露天底为-4m,二期定为-100m,设计矿石规模为200万吨/年。1974年基本建成,成为鞍钢铁矿石基地之一,但由于该矿难磨、难选,当年的选别方法不过关,故投产3年(到1976年)后,停产待采。随着选矿技术的进步、精矿价格的上涨,关宝山铁矿重新开采又成为可能。2003年5~9月,鞍钢集团鞍山矿业公司研究所及东鞍山烧结厂对关宝山铁矿的铁矿石进行了可选性试验,试验采用两段磨矿、中矿再磨、重选-强磁-阴离子反浮选连选工艺试验,在原矿品位为31.09%的情况下,获得了精矿品位为64.68%、尾矿品位为12.47%、金属回收率为74.19%的较好选别指标,证实了关宝山铁矿石应用新的选别工艺进行选别并得到合理指标的可行性。
鞍钢关宝山铁矿以微细嵌布的赤、褐铁矿为主,细分布不均,其多元素化学分析结果和铁物相分析结果如表3.34和表3.35所示。
表3.34 关宝山铁矿石的多元素化学分析结果

表3.35 关宝山铁矿石的铁物相分析结果

结果可知,矿石中FeSiO3、FeCO3含量不高,有害元素S、P含量较低,矿物组成比较简单,主要由赤铁矿和石英组成,同时含有少量磁铁矿、褐铁矿、硅酸盐和碳酸盐类矿物,属于高硅、贫铁,低钙、镁、铝的酸性矿石。
关宝山矿石铁矿物嵌布粒度平均46.57μm,脉石矿物嵌布粒度平均53.66μm,铁矿物+0.074mm粒级占58.57%,0.074~0.015mm粒级占36.69%,-0.015mm粒级占4.74%。铁矿物粗细分布不均匀,适宜采用阶段磨矿、阶段选别工艺。铁矿物和脉石矿物粒度分布基本一致,适于连续磨矿后入选。
根据该矿矿石性质,鞍山矿业公司确定采用阶段磨矿、粗细分选工艺,磨矿采用两段连续磨矿,粗粒中矿再磨再选重磁浮联合流程首先进行了粗细分级重选条件试验,即一段磨矿磨至-0.074mm占75%,进行粗细分级,粗粒进行一次粗选、一次精选、两次重选,扫中磁抛尾,中矿再磨后返回粗细分级作业。结果表明,中矿返回量为119.28%;粗细分级中粗粒级品位32.14%,产率175.41%;细粒级品位35.29%,产率43.87%。在粗选获得重选精矿品位64.27%、产率16.43%的基础上,实现了扫中磁抛尾产率39.70%、品位9.38%的选别指标。对粗细分级中的细粒部分进行磁场强度为900kA/m、1000kA/m的条件试验,结果见表3.36。
表3.36 强磁选脱泥条件对比试验结果

进一步将强磁选精矿进行了反浮选试验,反浮选采用的药剂为NaOH调整剂、淀粉抑制剂、CaO活化剂、MZ-21捕收剂。在进行药剂条件试验的基础上,选取NaOH用量为1125g/t,淀粉用量为1125g/t,CaO用量为500g/t,MZ-21用量为粗选390g/t、精选210g/t,进行一次粗选、一次精选、三次扫选的反浮选闭路试验。试验在入选品位47.12%的情况下,取得了浮选精矿品位65.50%、浮选尾矿品位19.24%、浮选作业回收率83.79%的选矿技术指标。
鞍山矿业公司在实验室实验的基础之上进行了连选试验。连选试验稳定运行8h,在磨矿细度-0.074mm含量占74%、原矿品位31.09%、中矿细度-0.074mm含量占72.27%、产率123.3%、再磨后细度-0.074mm含量占84%、粗细分级旋流器溢流细度-0.074mm含量占99%条件下,得到精矿品位64.68%、尾矿品位12.47%、精矿产率35.66%、回收率74.19%的较好指标。
进一步利用东烧一选车间进行了工业试验,流程如图3.30所示。原矿经两段闭路磨矿后的产品给入粗细分级旋流器分级,旋流器沉砂给入螺旋溜槽粗选,粗螺精矿给入螺旋溜槽精选,获得重选精矿,精螺中矿自循环,粗螺尾矿用中磁机抛弃粗粒尾矿,扫中磁精矿和精螺尾矿合并为中矿再磨后返回粗细分级旋流器分级;分级溢流给入弱磁,弱磁尾矿经浓缩机给入强磁,抛掉细粒级尾矿,弱磁精矿与强磁精矿合在一起成为混磁精矿,经浓缩机进行反浮选,经一次粗选、一次精选、三次扫选得到浮选精矿和尾矿。重选精矿与浮选精矿合在一起为综合精矿,扫中尾、强尾和浮尾合在一起为综合尾矿。

图3.30 关宝山铁矿石选矿工业试验工艺流程
工业试验结果表明,原矿处理量53t/(台·h),一次磨矿细度-0.074mm含量占40%~45%,二次磨矿细度-0.074mm含量占75%~80%,粗细分级旋流器溢流细度-0.074mm含量占95%,粗细分级旋流器分级比例为75:25,再磨细度-0.074mm含量占50%~60%,中矿产率132.67%,强磁励磁电流1300A,扫中磁励磁电流750A;浮选每吨原矿加药量:NaOH495g,淀粉374g,CaO204g,捕收剂177g;取得的试验结果为:原矿品位30.69%,精矿品位64.62%,尾矿品位15.63%,精矿产率30.73%,回收率64.61%。
(3)河南舞阳铁山庙铁矿
舞阳矿业有限责任公司是安阳钢铁集团重要的原材料基地。目前公司开采的主要是原生矿,受资源的影响,生产规模虽然近些年有了较大的提高,但是仍满足不了安钢对铁精矿的需要。长期以来,受选矿技术水平的影响,公司内部有近亿吨已经完成基建剥岩的贫赤铁矿没有得到有效的利用,加快利用这些资源有利于舞阳矿业有限责任公司更好地求得生存和发展。舞阳矿业有限责任公司对如何利用这一资源十分重视,先后委托长沙矿冶研究院、鞍钢集团鞍山矿业公司等科研单位围绕这部分铁矿进行选矿试验研究工作,取得了一定进展。
河南舞阳铁山庙矿石是一种较难处理的红铁矿矿石,主要矿物有(半)假象赤铁矿、赤铁矿、石英、黑云母等。其原矿化学分析结果见表3.37,矿物组成见表3.38。
表3.37 河南舞阳铁山庙矿石的化学成分分析结果

表3.38 河南舞阳铁山庙矿石的矿物组成

赤铁矿的嵌布关系十分复杂,且很细,多小于0.025mm。假象赤铁矿、半假象赤铁矿、赤铁矿是主要的铁矿物,实现铁矿物单体解离,有效回收这三种矿物是选矿分离的关键。东北大学近期研究了一种新的铁矿浮选工艺——正反浮选工艺流程,即用正浮选首先来抛尾,获得品位较合理的粗精矿,再用反浮选来提高精矿品位,同时保证较高的回收率。研究结果表明,针对铁山庙矿石,该工艺流程的适宜工艺条件是:磨矿细度为-0.074mm占90%;药剂用量:碳酸钠用量3000g/t,正浮选捕收剂为700g/t,活化剂为1200g/t,抑制剂为1200g/t,反浮选捕收剂为400g/t;矿浆温度为35℃,矿浆pH值11.5。闭路试验结果为:金属回收率78.37%,精矿品位59.45%,正浮选尾矿品位10.15%,反浮选尾矿品位20.30%,综合尾矿品位14.75%。
闭路数据质量流程如图3.31所示。

图3.31 河南舞阳铁山庙正-反浮选闭路数质量流程
另外,舞阳铁山庙有近亿吨已经完成基建剥岩的贫赤铁矿没有得到有效的利用,这部分铁矿石主要以赤、褐铁矿为主,其原矿矿物组成、多元素化学分析和物相组成分别见表3.39~表3.41。
表3.39 铁山庙贫赤铁矿原矿矿物组成

表3.40 铁山庙贫赤铁矿原矿多元素分析

表3.41 铁山庙贫赤铁矿原矿铁物相组成

粒度分析表明,该贫赤铁矿-0.074mm占68%时铁矿物解离度为66.49%,-10μm产率为27.12%;-0.074mm占85%时铁矿物解离度为50.49%,-10μm产率为35.17%。表明该矿的嵌布粒度极细。
长沙矿冶研究院对该矿石进行了强磁选-重选试验,其流程有两个方案:一个方案是一段磨矿后二次强磁选抛尾,强磁精矿分级后分别给入螺旋溜槽进行重选,粗粒用一段螺旋溜槽,细粒用两段螺旋溜槽分别得到精矿。尾矿给入离心选矿机,中矿再磨后用三次强磁选抛尾,其精矿经过脱泥后给入两段螺旋溜槽各得精矿,其第一段螺旋溜槽尾矿与脱泥作业的矿泥一起给入离心选矿机,而第二段尾矿作为最终尾矿抛掉,离心选矿机获得合格精矿后,尾矿作为最终尾矿抛掉。该工艺流程的选别指标为原矿品位25.52%,精矿品位60.51%,尾矿品位11.09%,金属回收率69.23%。另一方案是一段磨矿后进行一次粗选、一次精选、一次扫选、三次强磁选,得到最终精矿,尾矿经脱泥作业抛尾后,经高梯度磁选机得到最终精矿和最终尾矿。该工艺流程的指标是原矿品位25.48%,精矿品位57.41%,尾矿品位10.68%,金属回收率71.36%。
另外,长沙矿冶研究院还对该矿石进行了单一强磁选-阶段磨矿-阶段选别流程和还原焙烧磁选流程。单一强磁选方案为一段磨矿后进行一次粗选、一次精选、一次扫选、三次强磁选,得到精矿并抛尾后中矿再磨,再磨产品再经一次粗选、一次扫选、两次强磁选后抛掉最终尾矿,二者精矿成为最终精矿。该工艺流程的指标是原矿品位25.19%,精矿品位57.75%,尾矿品位11.46%,金属回收率68.00%;还原焙烧磁选方案为焙烧后两段连续磨矿,共进行五次弱磁选。一次弱磁选的精矿再经过二次弱磁选得到最终精矿,弱磁尾矿经一次弱磁选后,得到精矿和尾矿;一次弱磁选的尾矿再经一次弱磁选扫选抛掉最终尾矿,精矿给入最后一次弱磁选得到最终精矿和尾矿。该工艺流程的指标是原矿品位25.52%,精矿品位60.06%,尾矿品位70.5%,金属回收率82.00%。
鞍钢集团鞍山矿业公司对该矿石进行了水力旋流器分级、粗粒重选、细粒强磁选浮选流程试验,结果表明,重选部分精矿品位可达65.72%,产率25.85%。但是,重选部分的尾矿品位高达19.63%,产率为42.53%;强磁和浮选部分的精矿量很少,尾矿品位也较高;因此,把工艺流程进行了调整,采用强磁选抛尾、重选得精、重尾再磨、强磁选-正浮选工艺流程,即在磨矿细度-0.074mm占65%的情况下,用强磁抛尾,强磁精矿给入两段螺旋溜槽重选得到精矿,重选尾矿再磨后用强磁抛尾,强磁精矿再进行正浮选。该工艺流程的指标是原矿品位30.46%,精矿品位65.71%,尾矿品位16.45%,金属回收率65.71%。
3.3.4 鲕状赤铁矿选矿技术与工艺的进步
鲕状赤铁矿是以鲕状集合体形式存在的赤铁矿,而鲕状集合体是某种物质的胶体以其他物质颗粒为核心逐层凝结,具有同心层状构造,即赤铁矿逐层凝聚而形成呈鱼子状样的一系列球体(称鲕状体)所组成的赤铁矿物集合体。鲕状体一般较小。鲕状体通常彼此间都胶结在一起。由于鲕状赤铁矿嵌布粒度极细及其相互层层包裹的结构,所以很不利于矿石的单体解理,并且矿石经碎矿和磨矿后特别容易形成微细颗粒,而且含泥量大。这就决定了该铁矿石的选冶是非常困难的。
我国鲕状赤铁矿储量较大,占我国铁矿资源的10%左右。鲕状赤铁矿常形成大型矿山,嵌布粒度极细且经常与菱铁矿、鲕绿泥石和含磷矿物共生或相互包裹,如我国北方的宣龙式铁矿和南方的宁乡式铁矿,在已探明的超过100亿吨(以金属铁计)的难选铁矿资源中,鲕状赤铁矿所占的比例最大。鲕状赤铁矿的成矿原理基本一致,只是成矿年代有所不同,宣龙式鲕状赤铁矿成矿年代为震旦纪,而宁乡式鲕状赤铁矿的成矿年代为侏罗纪。其中宁乡式铁矿是我国分布最广、储量最多的沉积型铁矿床,广泛分布于湖南、湖北、江西、四川、云南、贵州、广西及甘肃南部地区,现已探明该类铁矿在我国储量达37亿吨(含表外矿),占全国沉积铁矿储量的70%以上,其中鄂西鲕状赤铁矿储量约22亿吨。
宣龙-宁乡式铁矿石基本上可分为以下三类:
①自熔性矿石。如湖北长阳,主要铁矿物为赤铁矿及菱铁矿,脉石矿物为方解石、白云石、绿泥石和胶磷矿。鲕状多呈椭圆形,少数呈拉长的扁球形;含铁较高,含磷也较高,一般大于1%。
②酸性富矿石。如河北龙烟及湖南湘东铁矿,主要脉石矿物为石英、绿泥石、玉髓和绢云母等,原矿品位较高,一般大于Fe45%。
③酸性中、贫矿。如四川綦江、广西屯秋的贫鲕状铁矿,贵州赫章、云南鱼子甸及鄂西的官店、黑石板等地的贫鲕状铁矿,原矿含铁较低,脉石矿物主要为硅酸盐。处理这类矿石的选厂有宣化钢铁公司选厂、綦江铁矿选厂等。
3.3.4.1 宣龙式鲕状赤铁矿
1914年当时的农商部矿政司顾问安德森、米斯托等人在张家口龙关、庞家堡、烟筒山勘察发现“宣龙式”赤铁矿床。卓宏谋主编的《龙烟铁矿之调查》一书中称“龙烟铁矿矿层之厚,矿质之佳,亦足为世界太古纪以后水成铁矿中之罕见者,推龙烟为首创,而肾状,鲕状矿并生,亦为其它矿所未有”。矿床规模一般为中、小型,因该类型铁矿主要分布于河北宣化、龙关一带,故而得名“宣龙式”铁矿。
宣龙式赤铁矿主要分布在龙泉寺、烟筒山、庞家堡、黄草梁、新窑、大岭堡等地,不同地区矿层厚度如表3.42所示。
表3.42 宣龙区不同地段矿层厚度

鲕状赤铁矿嵌布粒度极细,且经常与菱铁矿、鲕绿泥石和含磷矿物共生或相互包裹,因此鲕状赤铁矿石是目前国内外公认的最难选的铁矿石类型之一。
研究表明,宣龙式鲕状赤铁矿,当原矿磨矿粒度为-0.074mm占55%时,赤铁矿的单体解离度仅为12.33%;其中-0.045mm粒级赤铁矿的单体解离度仅为22.25%;随磨矿粒度-0.074mm含量增加,赤铁矿单体解离度增加,但变化区间不大,-0.074mm达到95%时,赤铁矿的单体解离度为52.23%;-0.045mm粒级单体解离度为65.78%。并且矿石经碎矿和磨矿后,特别容易形成微细颗粒而且泥特别多,这就决定了该铁矿石的选冶非常困难。
河北理工大学白丽梅等对宣龙式鲕状赤铁矿摇床分选显示,当给矿品位为TFe46%~47%时,通过改变磨矿细度进行摇床分选,摇床重选结果表明中矿和尾矿品位都很高。当磨矿细度从-0.074mm含量为65%提高到95%时,精矿品位从59.89%提高到62.40%,尾矿由41.48%上升到43.09%,中矿却由43.94%上升到55.28%,磨矿细度的增加导致摇床分选中矿品位增大。
刘红召等对宣龙鲕状赤铁矿采用深度还原-磁选工艺可以取得理想的金属化率和分选指标。矿样主要化学成分分析见表3.43,深度还原所用煤粉的工业分析结果如表3.44所示。
表3.43 矿样主要化学成分分析结果

表3.44 煤粉的工业分析结果

在原矿磨矿细度为-0.074mm占70%、煤粉添加量为20%、还原温度为1350℃、保温时间为50min条件下的深度还原产物的铁金属化率达到97%以上,还原产物碎磨至-0.074mm占70%后经一次弱磁选(磁场强度为90kA/m),可以获得铁品位为88.79%,回收率为92.85%的优质铁粉。
为更好地开发利用张家口地区的铁矿资源,牛福生等对宣钢龙烟鲕状赤铁矿资源进行了阶段磨选的强磁-反浮选工艺试验研究。试样的化学多元素分析、铁物相分析结果、铁精矿化学多元素分析结果分别见表3.45~表3.47,选别数质量流程如图3.32所示。
表3.45 矿样主要化学成分分析结果

表3.46 矿样化学多元素分析结果

表3.47 精矿化学多元素分析结果


图3.32 阶段磨矿-强磁-反浮选数质量流程
由表3.45可知,矿样全铁品位为47.66%,其中有害元素硫、磷含量分别为0.22%和0.24%,烧失量为4.5%。赤、褐铁矿中的铁占到矿样全铁含量的91.17%,磁铁矿中的铁仅占全铁的1.22%,碳酸铁、硫化铁和硅酸铁在矿样中也有少量分布。
试验结果表明,以SLon脉动高梯度磁选机为强磁选设备,以NaOH、淀粉、CaO和TS为反浮选药剂,在一段为-0.074mm65%、二段为-0.074mm95%的磨矿细度下,经过两次强磁选和一粗一精反浮选,可以获得较好的分选指标,精矿铁品位为62.34%、铁回收率为53.07%。
白丽梅等对张家口宣钢庞家堡龙烟矿山的鲕状赤铁矿进行了焙烧-弱磁选试验研究。原矿化学多元素分析及铁物相分析如表3.48和表3.49所示,数质量流程如图3.33所示。
表3.48 矿样主要化学成分分析结果

表3.49 试样多元素分析结果


图3.33 磁化-焙烧工艺数质量流程图
全铁品位47.66%,其中有害元素硫含量为0.22%,磷含量为0.24%,烧失量为4.5%。赤、褐铁矿占到全铁含量的91.17%,菱铁矿占到全铁的6.23%,磁铁矿占到全铁含量的1.22%,硫化铁和难溶硅酸铁合起来仅占全铁的1.38%。
试验研究表明,在矿煤比为11、焙烧温度为850℃、焙烧时间为75min、磨矿细度为-0.074mm占80.00%、磁感应强度为80kA/m时,经过一次精选,可得到产率为65.04%、品位为63.06%、回收率为86.05%的铁精矿。
李克庆等基于煤基焙烧还原-磁选工艺,进行了宣龙式难选鲕状赤铁矿石提铁过程及其影响因素的实验研究,以铁精矿品位和铁回收率为评价指标,确定了适合于该类矿石的最佳工艺条件。原矿化学组成及铁物相组成如表3.50和表3.51所示,最终试验结果及铁精矿多元素分析结果如表3.52和表3.53所示。
表3.50 试样多元素分析结果

表3.51 原矿铁物相组成

表3.52 全流程试验结果

表3.53 铁精矿多元素分析结果

试验研究表明,焙烧还原温度为1200℃,还原剂用量为30%,焙烧还原时间60min,焙烧产物磁选前的磨矿细度为-45μm占96.19%,磁选的磁场强度为111kA/m,在该工艺条件下,可以使铁精矿品位达到92.53%,铁回收率达到90.78%。
河北理工大学牛福生等人对宣龙式鲕状赤铁矿分别进行了强磁-反浮选、强磁-重选等工艺研究,结果表明,在磨矿细度-0.074mm95%的条件下,强磁-反浮选工艺流程获得精矿品位62.74%、回收率48.70%的开路浮选指标;在三段磨矿、三段磁选和三段重选的条件下,强磁-重选工艺流程获得精矿品位61.09%、回收率45%的阶段性成果;在焙烧温度800℃、焙烧时间75~90min、矿煤比11的条件下,焙烧-磁选工艺流程可获得精矿品位62%、回收率87%的指标。
河北理工大学白丽梅等对宣龙式赤铁矿用阶段磨矿-强磁选抛尾-重选的工艺流程进行选别研究。原矿多元素分析及铁物相分析如表3.54和表3.55所示。试验数质量流程如图3.34所示。
表3.54 矿样主要化学成分分析结果

表3.55 试样多元素分析结果


图3.34 强磁选-重选数质量流程图
由图可以看出,经过四次磨矿、四次重选出精矿、三次强磁选抛尾,在最终磨矿细度为-0.074mm95%的试验条件下,可以获得全铁品位为61.01%、回收率为47.85%的最终精矿。
3.3.4.2 宁乡式鲕状赤铁矿
1923年,丁格兰在江西萍乡考察时,发现了鲕状赤铁矿层,命名为“萍乡式铁矿”。丁格兰当时并未确定含矿层时代且认为此类铁矿无重大经济价值。谢家荣、孙健初和程裕淇等在考察长江中下游地区时,于江西萍乡,湖南攸县、茶陵、宁乡、新化、安化及湖北宜都、枝江、长阳等地,发现有鲕状赤铁矿层,将产于上泥盆统海相地层中的鲕状赤铁矿命名为“宁乡式”铁矿。20世纪50~70年代,我国对宁乡式铁矿投入了大量的勘查工作,提交了数百余份普查、勘探报告和选冶研究报告。之后,宁乡式铁矿的开发利用问题一直在研究中,并开展了数次规划论证,但终因矿石“磷高难降”、“铁贫难富”而未能大量开采。特别是储量巨大的鄂西高磷鲕状赤铁矿石。
近年来为开发国内新的铁矿资源,平抑进口矿石的增幅,提高中国铁矿资源的安全性,宁乡式铁矿的开发利用问题逐渐引起人们的重视。经过选矿工作者的艰辛努力,宁乡式铁矿的提铁降磷工作终于有新的突破。
宁乡式铁矿矿石以鲕状构造最为典型。矿石中金属矿物主要有赤铁矿、菱铁矿、褐铁矿等。非金属矿物主要有石英、绿泥石、胶磷矿、黏土矿物等。含铁品位一般为30%~45%;含磷通常偏高,介于0.4%~1.1%之间,有的甚至更高,磷的含量通常与矿床所在的地理位置有关。
由于鲕状赤铁矿嵌布粒度极细,且常与菱铁矿、褐铁矿、鲕绿泥石、黏土和含磷矿物共生、胶结或相互包裹,采用常规选矿方法难以达到富铁低磷的指标,宁乡式鲕状赤铁矿跟宣龙式赤铁矿一样,均是国内公认的最难选的铁矿石类型之一。
宁乡式铁矿的自然类型可划分为三种类型:鲕状赤铁矿矿石、鲕绿泥石菱铁矿矿石及两者的混合矿石,总体上以鲕状赤铁矿为主。宁乡式铁矿主要成分含量如表3.56所示。
表3.56 宁乡式铁矿主要成分含量

由宁乡式铁矿主要成分含量表可以看出:
①宁乡式铁矿的矿石属于低硫高磷贫铁矿石。
②矿石中SiO2、Al2O3含量高,CaO、MgO含量低,属酸性矿石。据统计,有85%以上的资源为高硅酸性矿石,少部分矿石为自熔性或碱性矿石,因此CaO和MgO对于宁乡式铁矿是重要的应利用成分。
③矿石中含有可综合利用元素,也是炼铁有害元素磷。据鄂西宁乡式铁矿中伴生磷的资源量计算结果,伴生磷总量为1664万吨,折合成P2O530%的矿石9370万吨,接近于两个大型磷矿的资源量,因此,应该设法回收其中的磷资源。
目前的研究资料显示,宁乡式铁矿石中的矿物有20余种,其中铁矿物有:赤铁矿、褐铁矿(针铁矿、水针铁矿)、菱铁矿、铁白云石、磁铁矿、磁赤铁矿、鲕绿泥石、镁铁矿、兰铁矿;磷矿物有:胶磷矿、磷灰石、碳磷灰石;硫化矿物有:黄铁矿、硫磷铝锶矿;主要脉石矿物有:方解石、白云石、石英、玉髓、黏土;次要脉石矿物有:白云母、电气石、绿帘石、海绿石、锆石、蛋白石、绢云母、斜长石、金红石,其他有:黄铜矿、硬锰矿、菱锰矿、斑铜矿、有机质。伴生元素锰、钒、钛、镓等含量均很低,无单独提取价值,可在冶炼过程中作为有益成分进入钢铁而得到利用。铁矿物选冶要充分回收,磷硫矿物有害,选冶除去或回收,变害为利。脉石矿物中的方解石、白云石为熔剂矿物,在选矿过程中应尽量保留。
宁乡式铁矿的主要结构有:赤铁矿微粒、极微粒针状结构,菱铁矿微粒-细粒自形、半自形粒状结构,鲕绿泥石微粒-细粒鳞片结构,磁铁矿微粒-细粒半自形-他形粒状结构。脉石矿物常有结构有:石英碎屑结构、方解石他形粒状结构、白云石自形-半自形粒状结构、黏土矿物泥质结构、玉髓纤维状结构、胶磷矿凝胶状结构、生物碎屑结构。
宁乡式铁矿的构造有:鲕状构造、砾状构造、粒状构造、纹层构造、块状构造,其中以鲕状构造最为典型。鲕状构造的鲕粒由赤铁矿、鲕绿泥石、玉髓、方解石、胶磷矿和黏土矿物组成,这些矿物围绕一个中心,层层环状包裹形成鲕粒。鲕粒大小0.1~1.0mm,最常见为0.3~0.5mm。鲕粒形状有球状、椭球状、枕状、纺锤状、长条状等。鲕粒有时有核心,鲕粒环带数不一,少则十余环,多的达50多环。各环厚度不一,疏密相间。赤铁矿环带一般较厚,37~72μm;方解石、胶磷矿的环带最薄,一般只有几微米宽。赤铁矿的环带由核心向鲕粒外层有密集的趋向。鲕粒中的赤铁矿环带本身并非纯净的赤铁矿,而是由赤铁矿极微细的针状晶体(一般长1~3μm,宽<1μm)交织成絮状小鳞片(长7~14μm,宽1~4μm),再相互连接成环带。在赤铁矿的晶体之间,鳞片的孔隙中又充填黏土矿物、玉髓及少量胶磷矿。鲕粒之间由微细粒状的赤铁矿、细粒的碳酸盐及黏土矿物、玉髓等充填。
宁乡式铁矿广泛分布于扬子地台及周边的赣、鄂、湘、桂、滇、黔、渝、川、甘、陕、豫11个省市区,经地质勘查提交矿产地212处,查明铁矿资源储量37.2亿吨,约占全国铁矿资源总量的7%。鄂西地区为宁乡式铁矿最重要的产区,探明资源储量19.92亿吨,占宁乡式铁矿总量的53.57%。代表性铁矿床有:乌石山、株岭坳、六市、火烧坪、海洋、大石桥、松木坪、阮家河、碧鸡山、官店、十八格、鱼子甸、菜园子、杨家坊、利泌溪等。不同矿区的矿物成分如表3.57所示。
表3.57 14个矿区的矿物成分表

宁乡式铁矿石有以下特点:
①矿石中赤铁矿的含铁量及其密度和比磁化系数与脉石矿物有明显差异,采用重选和强磁选均可将铁矿物和脉石矿物部分分离,获得TFe>50%的精矿,回收率80%左右。对原矿进行梯形跳汰(粗级别)和强磁选(细级别)处理,恢复矿石地质品位,提高产品含铁量,在技术上和经济上都是必不可少的。
②因赤铁矿单晶粒度极为微细,在磨矿过程中不可能使其成为单体,选矿只能以选铁矿物集合体为目标。由于铁矿物的集合体尺度较大,故没有必要将加工的细度提得很高。铁矿精矿品位不够高,主要并不是由于磨矿细度不够,而是受铁矿集合体中纯赤铁矿含量的限制。铁矿精矿品位一般在52%~53%,已说明选矿有效,如能达到55%~57%,则就是不错的指标。如想继续提高精矿品位,采用提高磨细度和絮凝选矿等方法,从已有试验结果看,效果不佳,且铁回收率大打折扣。采用低温焙烧加磁选的方法,同样不会有明显效果。因为焙烧过程中赤铁矿在氧化气氛(680℃)下转变成磁赤铁矿(γ-Fe2O3),在还原的气氛下转变成磁铁矿,但是这样的相变并未改变原矿的嵌布特征和铁矿物的颗粒结构。虽然铁矿物的选别性提高,选别效果或许改善,但改变不了选集合体的事实。官店铁矿原矿还原焙烧磁选及铁精矿的品位为57.01%,火烧坪铁矿为55.20%,仍没有重大突破。如欲获得含铁量>64%的精矿,唯一的办法是提高焙烧温度、破坏赤铁矿晶格,使赤铁矿中的铁不同程度地还原为金属铁,但这样的工艺实际已属冶炼范畴。
③磷矿物的工艺矿物特征表明,有90%的磷矿物易于与铁矿物解离而被分选出去,因此对宁乡式铁矿选矿“提铁降磷”的目标而言,提铁难、降磷易。通过一般的浮选就可将铁精矿中磷的含量降至0.25%以下。但由于有少部分磷以星散状分布于赤铁矿小晶体之间,因此铁精矿中的磷要降到很低,只靠机械选矿是难以办到的。矿石中的磷矿物与中国沉积型磷块岩中的磷矿物属同一种矿物,在铁矿选矿工艺中应有使胶磷矿进一步富集的流程,使其达到磷精矿的标准。但要通过选矿做到这一点是非常困难的。据国外同类矿产利用经验和国内冶炼试验,选矿不除磷,让它随铁还原进入生铁,在转炉炼钢过程中以钢渣磷肥的形式得到回收和综合利用。
④脉石矿物工艺矿物特性决定了宁乡式铁矿除硅是一个难题,因为有相当数量的含硅矿物与赤铁矿呈极微细嵌布状态,铁矿精矿品位上不去的主要原因是硅难以除去。含钙矿物方解石和白云石的嵌布粒度较粗,与铁矿物界线清楚且易解离,因此,实现钙铁分离是很容易办到的。但由于宁乡式铁矿大多是高硅酸性矿石,少部分自熔性矿石中的钙是宝贵的可利用的成分,在选矿过程中应尽量留在精矿中,而保持产品的自熔性。研究浮选除磷时的保钙技术是宁乡式铁矿选矿的一个重要课题,通过研究浮选药剂等途径解决这个问题是值得尝试的。
⑤根据宁乡式铁矿工艺矿物学禀赋特征,解决矿石利用问题的最终途径可能是冶炼方式,但应充分利用矿物物性差异和可能达到的解离程度,采用重选、强磁选、浮选等选矿方法作为补充和辅助工艺,以提高冶炼物料的质量和降低成本。
近年来,由于国家钢铁工业的迅猛发展,铁矿石需求强劲,国内铁矿资源供给不足,进口矿石连年量增价升,为有效开发国内新的铁矿资源,平抑进口矿石的增幅,提高国家铁矿资源的安全性,宁乡式铁矿的开发利用问题又重新受到选矿工作者的重视,并开始了新一轮的科技攻关。与宣龙式铁矿相比,宁乡式鲕状赤铁矿的工艺研究更为充分。
针对宁乡式铁矿提铁降磷,实验室研究较多的工艺整体上分为单一工艺和联合工艺。单一工艺主要有常规的重选、磁选、浮选等;联合工艺主要有磁化焙烧-磁选-反浮选、脱泥-反浮选、直接还原-磁选、解胶浸矿等。其中磁化焙烧-磁选-反浮选和直接还原-磁选是比较有发展前景的工艺。
(1)单一流程
①重选法。重选法不仅成本低,而且对环境影响小,是处理粗粒级赤铁矿的有效方法。重选设备的处理能力和回收率会随着粒度减小而降低,常规的重选处理设备的粒度下限为0.037mm,-0.037mm粒级的矿物即使选别效果较好的离心选矿机指标也不高。重选可以在较粗磨矿细度条件下,分离一部分脉石,不仅能极大地降低磨矿成本,而且对后续选别也是有利的。
姜涛等采用阶段磨矿-重选(螺旋溜槽和摇床)的工艺流程处理湖南某地的鲕状赤铁矿,获得了良好的分选指标。该工艺流程在磨矿的过程中添加水玻璃作为分散剂,最终结果得到了铁品位为60.72%、铁回收率34.55%的铁精矿。该工艺流程已成功申请专利。在此专利的理论基础上,有人对原矿铁品37.51%的湖南宁乡鲕状赤铁矿进行了研究,在磨矿细度为-0.074mm占90%、2kg/t的碳酸钠用量条件下进行螺旋溜槽-摇床的联合选矿试验研究,最终得到的铁精矿品位和回收率分别为58.67%和51.93%。
朱江在磨矿细度-0.076mm占80%条件下,对湖北宜昌某高磷鲕状赤铁矿进行了螺旋溜槽粗选-中矿再选流程实验,该矿石中的铁矿物以赤铁矿为主,并有少量菱铁矿,脉石矿物以方解石、白云石、石英、绿泥石、胶磷矿为主。矿石呈鲕状构造(也有呈肾状和豆状构造),由鲕粒和胶结物组成。鲕粒以赤铁矿为核心,呈椭圆形。矿石中的磷杂质呈非晶质胶磷矿形式存在。原矿碱比为1.09,属自熔性铁矿石。磷是矿石中的主要有害元素,必须予以脱除。试验原矿多元素分析及铁物相分析结果见表3.58和表3.59,试验结果如表3.60所示。
表3.58 原矿多元素分析结果

表3.59 原矿铁物相分析结果

表3.60 螺旋溜槽分选结果

从表3.60可以看出,采用螺旋溜槽重选法仅仅使得铁精矿铁品位提高了3.26%,最终磷含量为0.981%,精矿磷的含量远远高于冶炼对磷的最低要求。中矿磷的含量最高,故如果抛弃产率为11.17%的高磷中矿,为获得合格的精矿,需要对不同粒级再选处理。
肖巧斌对云南某鲕状赤铁矿用螺旋溜槽-摇床进行了联合选别。实验中矿石磨矿细度-0.074mm占90%,先在螺旋溜槽中进行粗选,粗选所得粗精矿再入摇床精选。该流程铁矿品位由给矿TFe48.22%提高到56.47%,铁的回收率却只有21.31%,尾矿品位高达46.45%。该流程尾矿磷的含量最高,中矿中磷的含量次之,精矿磷的含量无法满足冶炼对磷的最低要求。重选脱磷效果差与该矿中磷的嵌布粒度密切相关,该矿的粒度分析显示,产品粒度越细,磷的含量越高。
北京矿冶研究总院分别用重液分选、摇床、隔膜跳汰机、水力旋流器、Folcon离心流膜选矿机等进行了重选试验,利用湿式立环强磁选机进行了单一磁选和粗精矿再磨再选试验,结果显示各种方法的分选效果均不理想。
从不同地域鲕状赤铁矿重选实践可以看出,宁乡式鲕状赤铁矿矿石确实极难选别,重选不是该类型铁矿提铁脱磷的最佳方法,重选分离产物需要结合其他分选方法进一步处理才能满足脱磷的需要。对于石英嵌布粒度较粗的鲕状赤铁矿,在粗磨的条件下合理使用重选脱除一部分石英,可以降低磨矿成本并在一定程度上防止过磨。可以看出,常规单一选矿技术难以见效,因此应考虑多种选矿技术的联合流程。
②高梯度磁选法。新型高梯度磁选机的研制成功,能较大幅度地降低有效分选粒度下限,较好地解决了堵塞与夹杂问题,为高磷铁矿石脱磷提供了一条新的途径。SLon系列立环脉动高梯度湿式磁选机已用于工业生产,它的鼓动脉动结构使高梯度磁选效率得到明显提高,有效分选粒度下限可达0.01mm。
文勤等用SLon高梯度强磁选机使用一次粗选一次扫选的工艺流程处理了鄂西某鲕状赤铁矿,并做了一次粗选、一次扫选的闭路试验,最终得到了铁品位为52.37%、回收率为86.31%的精矿,获得了较好的分选指标。
朱江对湖北宜昌某高磷鲕状赤铁矿,在磨矿细度-0.074mm占80%的条件下进行强磁选实验,实验结果表明,强磁有明显的脱磷效果,但是铁的分选效果很差。
肖巧斌对云南某鲕状赤铁矿用湿式强磁机磁选。实验将矿石磨到-0.074mm占90%,在不同电流下的实验结果表明,强磁选仍然不能有效地降低铁精矿中的磷,脱磷的效果不佳,铁的回收率较低,这主要是因为在该矿中铁和磷是紧密共生的。
陈文祥对巫山桃花高磷鲕状赤铁矿强磁选脱磷的实验表明,精矿中磷的含量由原来的1.13%降为0.95%,铁的品位变化不大。可见针对该高磷鲕状赤铁矿强磁分选,不仅脱磷的效果一般,而且提铁的效果也不明显。
王代军和文清对鄂西某鲕状赤铁矿强磁选进行了详细的研究。磨矿细度-0.074mm占85%,最终强磁抛尾结果产率为16.87%,铁矿品位为33.16%。显然该磨矿细度条件下,强磁流程由于尾矿品位过高造成铁的损失较大,所以铁精矿的回收率较低。
李广涛对四川某地高磷鲕状赤褐铁矿进行了强磁分选,原矿磨至-0.074mm大于80%,在给矿浓度25%的条件下进行高梯度强磁实验。从实验结果来看,精矿中的磷的含量都高于0.47%,强磁分选尾矿产率46.80%,尾矿铁品位31.12%,铁矿损失较大。
北京矿冶研究总院进行的鄂西鲕状赤铁矿强磁选磨矿细度实验表明,-0.074mm从45%提高到85%,精矿中磷的含量仅仅由0.81%降到了0.62%,铁品位由50.51%提高到了51.70%,尾矿品位都大于32%,铁矿回收率不足36%。改变磁场强度效果也不明显。
由单一磁选工艺选别指标可以看出,强磁选仅仅在粗磨-0.074mm小于60%的情况下才能获得较满意的回收率,粗磨-强磁抛尾是可行的流程;但是,为了保证回收率而放宽磨矿粒度,就无法保证鲕状赤铁矿的有效解离,所以精矿的品位提高幅度有限,而且粗颗粒会对强磁机造成堵塞。
③浮选法。肖巧斌使用油酸和氧化石蜡皂对某鲕状赤铁矿进行了反浮选研究,由于磷在矿石中嵌布粒度极细、-0.058mm产品中磷的含量最高,当磨矿细度-0.074mm占90%时,反浮选脱磷效果非常差,获得的精矿含铁50.92%、含磷1.64%。
韦东对原矿含铁42.59%、磷0.87%的鄂西鲕状赤铁矿进行了直接浮选研究,一粗一精闭路试验获得的铁精矿试验结果为铁品位45.22%、磷含量0.23%、铁回收率83.74%。该铁品位不高,提铁效果有限。
朱江采用反浮选工艺处理湖北宜昌鲕状赤铁矿,磨矿细度-0.074mm占80%,可获得铁精矿品位57.09%、含磷0.163%、产率57.01%、铁回收率71.76%的选别指标。磷、硫、砷等有害杂质均未超标,碱比为0.22,反浮选在脱磷时也将CaO、MgO脱去,对SiO2、Al2O3未脱除,使得精矿铁品位不高。烧失后精矿的铁品位可达到59.39%。原矿多元素分析结果和铁物相分析结果如表3.61和表3.62所示,试验流程和最终精矿多元素分析如图3.35和表3.63所示。
表3.61 原矿多元素分析结果

表3.62 原矿铁物相分析结果


图3.35 浮选试验流程图
表3.63 铁精矿产品多元素分析

庞玉荣对国内某地鲕状赤铁矿采用阴离子反浮选工艺同样取得了较好的效果。进行了“一次粗选、一次精选、一次扫选、中矿顺序返回”的闭路浮选实验,铁精矿品位和回收率分别为56.01%和76.1%。
王兢等采用正交浮选试验法考察了某地鲕状赤铁矿浮选的主要影响因素,研究发现,对浮选精矿的铁品位和铁回收率影响最大的是十二胺用量,其次是调整剂用量,适当的磨矿时间和NaOH用量对铁精矿品位和铁回收率也有一定的影响。研究过程中发现,用十二胺作为捕收剂来浮选鲕状赤铁矿有优点也有缺点,优点是其对鲕状赤铁矿的富集作用很明显,缺点是药剂用量较大且泡沫太过丰富与稳定,对后续作业会产生不良影响。所以选择适当的捕收剂和调整剂来减少和削弱泡沫的数量与稳定性是至关重要的。回收率分别为54.70%和74.94%。
(2)联合流程
①焙烧-磁选工艺。焙烧磁选法和直接还原磁选法是处理难选铁矿物最有效的分选方法。矿石在焙烧炉中加热并在适宜的气氛中进行复杂的物理化学作用,使弱磁性铁矿物转变为强磁性铁矿物,脉石矿物在大多数情况下变化不大。焙烧后,利用矿物间磁性的差异磁选后可得到较高的选别指标。磁化焙烧工艺能简化选别流程且焙烧精矿具有易于烧结、易于脱水和过滤等优点。但磁化焙烧基建投资和生产费用较高,为此,研发新型焙烧设备,节能降耗,是该工艺工业化应用的前提。
左倩等对鄂西原矿品位为43.71%的某宁乡式鲕状赤铁矿进行了磁化焙烧-磁选试验研究。矿石中主要铁矿物为赤铁矿,其次为褐铁矿,其他还有少量菱铁矿、磁铁矿等;磷的独立矿物主要为磷灰石;脉石矿物主要为石英、鲕绿泥石和高岭石,其他还有微量的无定形碳、方解石、锆石等。矿石中主要有用元素是铁,主要有害杂质是磷、硅。试样是赤铁矿晶体与黏土类矿物、胶磷矿、绿泥石等脉石矿物以微细分散状态的颗粒紧密共生构成的鲕状赤铁矿矿石。矿石中赤铁矿和磷灰石的嵌布粒度都很细,而且不均匀。赤铁矿在+0.074mm粒级中的占有率仅为45.80%,而在-0.020mm粒级中的占有率达21.47%;磷灰石的嵌布粒度从0.015mm至0.25mm不等。试样的化学多元素分析结果见表3.64,铁物相分析结果见表3.65,磷赋存情况见表3.66,试验流程及最终结果如图3.36和表3.67所示。
表3.64 试样化学多元素分析结果

表3.65 试样铁物相分析结果

表3.66 试样中磷的赋存情况


图3.36 磁化焙烧-弱磁选试验流程图
表3.67 试验流程结果

由表3.64可以看出,虽然矿石铁品位较高,为43.71%,但有害元素磷的含量也较高,达0.93%。矿石中的磷主要分布于磷灰石及菱铁矿中,其次分布于褐铁矿和赤铁矿中,其他矿物中磷含量极少。
对影响磁化焙烧效果的各个因素如磁化焙烧温度、磁化焙烧时间、磁化焙烧还原剂用量等进行了单因素条件试验,确定了最佳的焙烧条件。在磁化焙烧温度为750℃、磁化焙烧时间为60min、还原剂与原矿的质量比为1:5的最佳条件下焙烧后,对焙烧矿采用不磨矿弱磁粗选抛尾-磨矿至-0.045mm占96%-弱磁精选(两次)的工艺流程,可以获得铁品位60.12%、铁回收率为77.42%(对原矿+煤粉)的铁精矿。矿石中的磷含量从原矿的0.93%降到精矿的0.62%,精矿中的磷含量偏高,对冶炼有一定的危害,需经过进一步的研究使其降低。
王国军等对原矿铁品位为47.20%的湖北巴东鲕状赤铁矿进行了磁化焙烧-弱磁选试验研究。试验采用一氧化碳与氮气的混合气以及电加热方式模拟燃煤还原焙烧气氛,在试验室循环流化床装置中进行。原矿多元素分析结果如表3.68所示,试验流程如图3.37所示。
表3.68 矿样化学多元素分析结果


图3.37 焙烧-弱磁选试验流程图
本试验中循环流化床试验装置主要由流化床反应炉及预热管、高温旋风分离器组成,见图3.38。流化床内部为一根内径为42mm、高度为1000mm的耐热不锈管,床层内装有测量床温的K型热电偶。N2和CO的混合气体经预热管预热后进入到反应段,作为床料的矿样由流化床上部的投料口投入。试验时,将炉膛温度稳定在某一范围内,从加料口投入矿样,然后通入N2和CO的混合气体,使物料进行流态化焙烧并开始计时。焙烧到指定时间后,切断气体,打开下部的卸料管将物料卸入水中淬冷。流化风量可根据床层压降-流量特性曲线确定。

图3.38 循环流化床试验装置示意图
1—N2;2—CO;3—流量计;4—预热管;5—卸料管;6—风室,外接U形管测压力;7—布风板;8—反应炉;9—高温旋风分离器;10—投料口;11—烟气出口;T—测温点
由表3.69可见,采用循环流化床对试验矿样进行磁化焙烧后,经过阶段磨矿、一粗一精两次弱磁选,可以获得铁品位为56.60%、铁回收率为77.79%的铁精矿,证明采用循环流化床焙烧技术处理鲕状赤铁矿是可行的。
表3.69 试验流程平均结果

童雄等对某鲕状赤铁矿进行了磁化焙烧的影响因素的试验研究,确定了最优的磁化焙烧-弱磁选工艺。原矿化学多元素分析和铁物相分析如表3.70和表3.71所示,流程图及最终精矿技术指标如图3.39和表3.72所示。
表3.70 矿样化学多元素分析结果

表3.71 铁物相分析结果


图3.39 焙烧-弱磁选原则工艺流程
表3.72 铁精矿技术指标

在无烟煤5%、焙烧温度850℃、焙烧时间60min、磨矿细度-0.074mm占70%、弱磁选磁场强度145.6kA/m的最优组合条件下,得到了铁品位和回收率分别为58.40%和87.86%的铁精矿指标,精矿中的硫达到冶炼要求,可以作配料使用;磷超标,如直接作为冶炼原料,尚需进一步试验研究。
②絮凝-强磁选。河北省矿业开发与安全技术实验室通过矿石性质分析,对某地鲕状赤铁矿采用絮凝-强磁选工艺流程进行选别。原矿多元素分析及铁物相分析如表3.73和表3.74所示,试验数质量流程如图3.40所示。
表3.73 原矿化学多元素分析结果

表3.74 原矿铁物相分析结果


图3.40 试验数质量流程图
原矿全铁品位为47.41%;矿石中主要杂质是SiO2,其次为Al2O3、MgO和CaO;有害元素S和P含量稍高;w(CaO+MgO)/w(SiO2+Al2O3)=0.296,表明矿石为酸性矿石。原矿中有用铁矿物主要是赤褐铁矿,其铁分占有率达91.17%,其次是碳酸铁和磁铁矿,并含有少量的硫化铁和硅酸铁,磁铁矿铁分只占1.22%。试验结果表明,采用絮凝-强磁选工艺,在最佳的试验条件下,经过一次粗选、一次扫选,可以得到精矿铁品位为55.51%,铁回收率为76.02%的选矿指标。
孙达对某微细粒嵌布的鲕状赤铁矿采用阶段磨矿-强磁-反浮选工艺处理后的尾矿进行了提高回收率的工艺试验研究。矿样中主要回收的金属矿物为铁矿物,全铁品位为37.55%,矿石中主要杂质是SiO2,其次为Al2O3,S和P含量均不超标。矿样中有用铁矿物主要是赤、褐铁矿,其次是碳酸铁,磁铁矿很少。化学多元素分析和化学物相分析分别如表3.75和表3.76所示,试验数质量流程如图3.41所示,试验流程结果见表3.77。
表3.75 原矿化学多元素分析结果

表3.76 矿样铁物相分析结果


图3.41 絮凝-强磁选试验流程
表3.77 絮凝-强磁选流程试验结果

由试验结果可知,在最佳条件下,对矿样进行一次粗选、一次扫选的流程试验,可以将尾矿铁品位降至24.96%,并得到铁品位56.07%、回收率60.44%的精矿,对原矿而言,铁的回收率增长了28.29%,使该部分产品得到有效的回收。
③强磁-反浮选。韦东对原矿含铁42.59%、磷0.87%的鄂西鲕状赤铁矿进行了阶段磨矿-强磁-反浮选工艺脱磷提铁联合工艺研究,闭路试验获得的铁精矿铁品位为50.52%、磷含量为0.20%、铁回收率为75.39%。该工艺的脱磷效果较为明显,但铁品位不高,尤其是强磁抛尾过程损失的铁较多,导致铁回收率较低。
林祥辉等采用强磁选-絮凝脱泥-反浮选工艺流程处理了鄂西某鲕状赤铁矿,获得了较好的分选指标。试验先对捕收剂用量、抑制剂用量、絮凝剂用量等各因素进行了单因素条件试验,然后在最佳药剂用量条件下,获得了铁品位为56.29%、铁回收率为59.22%、磷含量为0.109%的铁精矿。该试验采用的捕收剂为RD-31、絮凝剂为DA-18。
④磁化焙烧-磁选-浮选流程。以余永富院士为首的科研团队,经过多年潜心研究,开发出新型多级悬浮预热器和闪速反应炉等具有自主知识产权的装置,形成了闪速磁化焙烧技术。闪速磁化焙烧具有工艺参数操作范围较宽、控制方便、单位产能高、矿石还原速度快、时间短、能耗低等优点,能在数秒或数十秒内完成,是处理1mm以下粉矿的理想工艺。“磁化焙烧-磁选-反浮选”工艺过程:原矿经闪速炉磁化焙烧后,采用弱磁选获得粗精矿,然后采用反浮选脱磷脱硅,进一步提高精矿品质。其最佳试验指标为:最终磨细度-0.037mm95.83%,铁精矿品位TFe60.17%,P0.24%,TFe回收率81.99%。闪速磁化焙烧工艺原理如图3.42所示。

图3.42 闪速磁化焙烧工艺原理图
气体物料;
固体物料
王秋林等对鄂西某高磷鲕状赤铁矿进行了选别试验研究,原矿多元素化学分析及铁物相分析如表3.78和表3.79所示,试验流程如图3.43所示。
表3.78 原矿的主要化学成分

表3.79 原矿中铁的化学物相分析结果


图3.43 全流程试验工艺流程图
由图3.43可以看出,采用磁化焙烧-弱磁选-阴离子反浮选流程处理原矿铁品位为43.50%、含磷量为0.85%的鄂西某鲕状赤铁矿,经过一系列的条件探索试验,如磁化焙烧温度、磁化焙烧时间、磁化焙烧还原剂用量、反浮选抑制剂用量、捕收剂用量等条件的单因条件素试验,最后在最优条件下,做磁化焙烧-弱磁选-阴离子反浮选闭路试验,获得了铁品位为61.88%、含磷量0.25%、铁回收率为79.95%的铁精矿。
重庆某高磷鲕状赤铁矿,主要以鲕状赤褐铁矿形式存在。鲕粒中赤、褐铁矿大多为0~8μm,与石英、碳酸盐矿物、黏土矿物、胶磷矿紧密结合,以石英或其他矿物为核心组成鲕粒。胶磷矿粒度微细,集中于1~5μm,与黏土矿物、石英、赤褐铁矿等紧密共生,产于鲕粒、岩屑中。菱铁矿及碳酸盐类矿物集合体粒度集中于0.2~10mm间。胶磷矿在鲕粒、胶结物、岩屑中的粒度、嵌布情况无大差别,以细微颗粒与赤褐铁矿、菱铁矿、脉石等紧密共生,解离十分困难,难以分选。龙运波等采用焙烧-磁选-反浮选工艺流程,可以获得铁精矿产率为46.16%、TFe58.15%、P0.28%、铁回收率为69.37%的指标。原矿化学多元素分析结果和铁物相分析结果如表3.80和表3.81所示。工艺流程如图3.44所示。
表3.80 矿石化学多元素分析结果

表3.81 矿石铁物相分析结果


图3.44 焙烧-磁选-反浮选闭路工艺流程图
艾光华等用磁化焙烧-弱磁选-反浮选工艺流程处理云南某高磷鲕状赤铁矿。先进行了影响磁化焙烧效果的各单因素条件试验,在最佳焙烧条件下获得焙烧产物,然后对焙烧产物进行一次粗选一次精选的反浮选脱磷试验。进行反浮选试验时,对碳酸钠(pH调整剂)、淀粉(抑制剂)、RP(捕收剂)、2#油(起泡剂)等的用量进行了探索试验,最终进行磁化焙烧-弱磁选-反浮选全流程闭路试验,获得了铁品位61.20%、磷含量0.02%、铁回收率67.49%的铁精矿,分选效果比较理想。
罗立群等采用磁化焙烧-弱磁选-反浮选工艺流程对湖北某宁乡式鲕状赤铁矿进行了可选性研究。矿样多元素分析结果如表3.82所示,工艺流程如图3.45所示。
表3.82 试样多元素分析结果


图3.45 磁化焙烧-弱磁-反浮选试验闭路流程
试验在最佳选别条件下得到了铁品位为60.24%、总回收率为74.54%的最终铁精矿,但其中磷含量为0.28%,可以作为冶炼铁的配料,若要作为炼铁的原料,还需要进一步的试验研究以降低杂质P含量。
李广涛等对四川某鲕状赤铁矿进行了焙烧-磁选-反浮选提铁降磷工艺研究。原矿化学成分多元素分析及铁物相分析结果见表3.83和表3.84所示。该矿主要呈块状构造,少量具有土状、脉状构造。微观上主要为鲕粒状构造,鲕粒粒度一般在0.2~1mm左右,呈圆状、椭圆状,部分呈层理状分布。试验研究表明,该工艺可大幅度提高精矿中铁品位(TFe可达60.89%),但精矿中磷元素含量稍高,需进一步研究。试验流程如图3.46所示。
表3.83 化学成分分析结果

表3.84 铁物相分析


图3.46 焙烧-磁选-浮选试验流程图
⑤直接还原-磁选法。采用高品位的铁矿石进行直接还原,其产品直接作为炼钢的原料,这已是一个成熟的技术,并在工业中广泛采用。还原过程是个冶金物理化学过程,涉及铁的相变和硅酸盐传递质的作用。在高温还原环境中赤铁矿被还原成金属铁,金属铁在高温下通过一定程度的聚集长大,使得鲕状结构转变为粒度粗大的粒状结构,目的是改变铁的赋存状态。这个过程涉及一个化学还原过程和铁富集的物理过程。高磷赤铁矿直接还原过程中铁颗粒的重建和长大,是实现铁和磷以及硅分离的前提。在实际操作中,控制还原气氛可以把化学还原过程进行到100%,但是由于受鲕粒层与层之间厚度、铁矿与脉石的结合方式各异的影响,实际上铁富集的物理过程只在很小一部分和只在有限的区域内发生。还原温度的提高,有利于直接还原反应的加快;当温度升高后,煤的反应活性也会提高,CO2反应率提高。所以,升高温度可以促进产品的金属化,有利于铁相凝聚。但是当温度超过一定值后,由于FeO和SiO2易生成铁橄榄石(2FeO·SiO2),铁橄榄石本身熔点低,它与FeO或SiO2组成的低共熔点为1177℃和1178℃,所以当温度升高到一定程度后,将生成极难还原的2FeO·SiO2,并产生软化和熔化,阻碍CO的扩散,影响铁矿石还原,而且对铁相凝聚不利。通过添加消石灰生成硅酸钙,可以在一定程度上消除铁橄榄石生成对还原的不利影响。还原温度、渣相碱度(石灰的添加量,添加石灰是为了硅酸盐造渣)和反应时间,以及冷却方式都对还原过程有至关重要的影响。最近几年鲕状赤铁矿直接还原磁选取得了一定的进展。
孙永升等研究了在原料均为-2mm、还原温度1350℃、还原时间50min、铁矿与煤的配比3:2的工艺条件下,可以得到金属化率97%左右的还原物料,磁选后精矿铁品位达85%以上,金属化率97%以上,金属铁的回收率达92%以上。研究发现,在直接还原焙烧的过程中,赤铁矿按照如下反应路径被还原为单质铁:Fe2O3→Fe3O4→FeO→Fe,随着时间的推移,金属铁颗粒由小变大,由几个微米长大到10μm以上。
赵志龙对鄂西高磷鲕状赤铁矿球团直接还原磁选的研究表明,温度1323~1523K、配煤量过量5%~15%、还原时间在15~30min、金属化率71%时,经过磁选,精矿TFe 68.44%,磷的含量降低了55%。由此可见,该研究提铁效果较好,但是铁矿中的磷有待于进一步脱除。
沈慧庭等针对某难选鲕状赤铁矿,进行了采用磁化焙烧-磁选工艺获取铁精矿和采用直接还原工艺制取海绵铁的试验室试验。结果表明:采用无烟煤作还原剂进行磁化焙烧,焙烧产品经过磁选后铁精矿铁品位达到61.60%,铁回收率达到96.65%;在环状装料方式下采用无烟煤和碳酸钙的混合物作为还原剂进行直接还原焙烧,焙烧产品经过磁选得到的海绵铁的铁品位、金属化率和铁回收率分别达到89%、90%和85%。
周继程对湖北地区黑石板鲕状赤铁矿进行了还原焙烧研究,实验前把赤铁矿、煤粉和消石灰粉团块干燥后在立式高温碳管炉内进行还原焙烧。实验采用TFe47.92%、P1.05%的鄂西高磷鲕状赤铁矿,在直接还原温度1150~1300℃、团块碱度0.163~1.600、内配碳比0.7~1.0、还原时间15min的条件下,分别可以得到铁的收得率>90%、脱磷率>85%,最终可以获得铁品位大于85%、磷的含量0.2%~0.5%的优质还原铁粉。
杨大伟等用焙烧时添加脱磷剂NCP的方法对鄂西铁含量和磷含量分别为43.10%和0.82%的某高磷鲕状赤铁矿进行了还原焙烧同步脱磷工艺研究。试验流程如图3.47所示。

图3.47 直接还原-磁选工艺流程图
经过对影响还原焙烧效果的还原焙烧温度、还原焙烧时间等进行单因素条件试验之后,在最佳还原焙烧条件下对原矿进行焙烧,然后对焙烧产物进行磨矿-磁选处理,得到最终精矿铁品位为90.59%,铁回收率88.19%,磷含量为0.85%。
⑥脱泥-反浮选工艺。鲕状赤铁矿由于嵌布粒度极细,且硬度低,在磨矿过程中容易产生大量矿泥,矿泥在微细粒矿物表面形成罩盖,严重恶化浮选效果,且部分细泥进入精矿,还将造成精矿质量降低。预先脱泥可以消除矿泥在浮选中的不良影响,确保浮选顺利进行,有利于提高最终铁精矿质量。
北京矿冶研究总院对“宁乡式”鲕状赤铁矿进行了分散-选择性聚团脱泥-反浮选脱磷工艺的试验研究。矿样原矿的主要化学成分分析、矿物含量分析与铁在各种矿物中的分布分别见表3.85~表3.87所示。
表3.85 “宁乡式”鲕状赤铁矿原矿的主要化学成分分析

表3.86 “宁乡式”鲕状赤铁矿原矿的矿物组成及含量

表3.87 “宁乡式”鲕状赤铁矿铁在各种矿物中的分布平衡

试验矿样中赤铁矿、菱铁矿、鲕绿泥石分别占整个矿物量的43.6%、26.0%和24.5%,总计占矿物量的94.1%,其他矿物含量均较低。经电子探针测试,赤铁矿、菱铁矿、鲕绿泥石中的铁分别为69.09%、44.82%和34.60%,其铁的加权平均品位是53.40%,赤铁矿呈针状、片状集合体嵌布在菱铁矿与鲕绿泥石中,常与它们互层构成鲕粒;在针状、片状赤铁矿中,存在着许多微细粒的鲕绿泥石的包体,铁矿物呈粗、中、细粒不均匀嵌布,粗、中粒较少,细粒较多,由于嵌布粒度微细,单体解离困难。磷矿物主要由磷灰石及胶磷矿组成,微细粒磷灰石一部分浸染在赤铁矿、菱铁矿、鲕绿泥石中,作为它们中的包体存在;另一部分磷矿物浸染在石英等脉石矿物中。
针对该鲕状赤铁矿,北京矿冶研究总院研究了浮选脱泥-选择性聚团-反浮选脱磷技术,其闭路试验流程如图3.48所示。

图3.48 “宁乡式”鲕状赤铁矿闭路试验流程
试验结果表明,通过适当调整药剂制度和流程结构,铁的回收率达到90.57%,精矿中铁品位达54.11%;含磷量由原矿的0.57%下降为铁精矿中含磷0.236%,取得了较好的降磷效果。
湖北省恩施巴东黑石板矿属含胶磷矿赤铁矿石,主要为鲕状赤铁矿,其次为砾状赤铁矿,磁性铁、碳酸铁和其他类型矿物含量均不高。原矿多元素分析、铁物相分析结果如表3.88和表3.89所示。
表3.88 巴东黑石板矿原矿多元素分析结果

表3.89 巴东黑石板矿原矿铁物相分析结果

武汉科技大学对该矿矿石进行了选矿试验,确定了选择性絮凝-脱泥-阴离子反浮选原则流程,结果表明,采用添加分散剂水玻璃、絮凝剂G-DF选择性絮凝脱泥、Ca2+活化含硅矿物、淀粉抑制赤铁矿物、油酸为捕收剂阴离子反浮选的工艺方案,选择性絮凝、二次脱泥、一次粗选三次扫选阴离子反浮选的选别流程,获得铁精矿含铁56.23%、含磷0.098%、铁回收率75.28%的良好指标。浮选试验流程和试验条件如图3.49所示。

图3.49 巴东黑石板矿浮选试验流程
闫武用自行研制的脱磷剂和脱硅药剂采用脱泥-反浮选脱磷-反浮选脱硅流程对铁、磷品位分别为48.80%、1.02%的原矿进行试验研究,试验取得较好结果。矿石化学多元素分析结果如表3.90所示,试验流程和最终试验结果如图3.50和表3.91所示。
表3.90 原矿化学多元素分析结果


图3.50 反浮选脱磷-反浮选脱硅闭路试验流程图
表3.91 反浮选脱磷-脱硅闭路试验结果

矿石中主要有用矿物为赤褐铁矿和微量磁铁矿;脉石矿物主要是碳酸盐和石英类矿物,其次为绿泥石(鲕绿泥石、鳞绿泥石)、黏土类(高岭石、水云母),有少量黑云母、绢云母等;主要含磷矿物为胶磷矿。
矿石以鲕状构造为主,矿石具有典型的同心环带结构,鲕粒中赤铁矿与胶磷矿、石英、长石、绿泥石、黏土矿物等矿物胶结共生,这些矿物颗粒都十分细,即使在细磨矿条件下矿物间也不能充分单体解离。
矿石中的磷矿物以三种形式出现:一种是在鲕粒中成环带;一种是在砾状矿石中以较纯的块状胶磷矿出现;再一种是以胶磷矿的质点分布在岩屑中,其中块状胶磷矿和含磷质岩屑中胶磷矿粒度集中于0.2~0.8mm,适合机械选矿方式去除,鲕粒中有65%左右的胶磷矿粒度小于0.02mm粒级,有20%左右的磷矿物难以用常规选矿去除。
由表3.91可以看出,脱泥-反浮选脱磷-反浮选脱硅流程最终可获得浮选铁精矿品位为58.89%、磷品位为0.24%、铁回收率为74.05%的指标。
云南文山铝业有限公司对云南某磷含量达0.87%、铁品位为45.14%的鲕状赤铁矿进行了脱泥-反浮选试验研究。矿石多元素分析及铁物相分析结果如表3.92、表3.93所示。试验流程及结果如图3.51和表3.94所示。
表3.92 矿石主要化学成分

表3.93 铁物相分析


图3.51 脱泥-浮选试验闭路流程图
表3.94 脱泥-浮选脱磷试验结果

从表3.94可以看出,脱泥-反浮选能获得铁品位为52.66%、铁回收率为56.07%、磷含量为0.14%的铁精矿,脱磷效果显著,同时铁品位也大于52%,各药剂用量相对于直接反浮选也有明显降低。
中国地质科学院矿产综合利用研究所研制了高效脱磷系列捕收剂EM-501和新型脱硅捕收剂EM-508。对原矿TFe含量为48.55%、含P1.14%的湖北官店鲕状赤铁矿完成了重选脱泥-反浮选工艺的扩大连续试验。原矿细磨至-0.075mm 92.50%左右,经重选脱泥后,采用反浮选工艺,配以自主研发的浮选药剂,取得了铁精矿TFe品位57.32%、P0.28%、TFe回收率80.7%的优良指标。
重选脱泥-反浮选工艺处理鄂西鲕状赤铁矿经济、合理、可行,用于处理脉石矿物以石英为主的酸性鲕状赤铁矿矿石效果较好。与磁化焙烧-磁选-反浮选工艺相比,重选脱泥-反浮选具有流程结构简单,选矿成本较低、效率高,易于工业实施等优势,但由于脱泥,部分铁矿物不可避免会损失于矿泥中,从而导致铁的回收率较磁化焙烧-磁选-反浮选工艺略低。
和单一的磁选、重选、浮选相比,联合分选流程结合了后者的各种优点,扬长避短。因而,联合分选流程能够更有效地提高铁精矿的品位,并更有效地降低铁精矿中有害元素如硫、磷的含量。但是由于重选、磁选、浮选并没有取得实质性的突破,因而简单地把三者联合使用,铁精矿的分选指标并不会有明显改善,铁精矿的品位不会有实质上的提高。