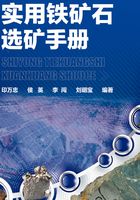
3.2 磁铁矿选矿工艺
3.2.1 磁铁矿石选矿工艺的进步
磁铁矿是人类最早利用的矿石之一,而且磁铁矿选矿是铁矿石选矿工作的主体。多年来磁铁矿选矿技术不断发展和进步,从20世纪60~70年代磁选设备的永磁化到80年代细筛工艺的应用,磁铁矿选矿生产指标有了较大的改善。但是目前入选的磁铁矿粒度逐渐细化,使得磁团聚在选别中的负面影响日益明显,磁性夹杂和非磁性夹杂导致依靠单一的磁选法提高精矿品位越来越难。而同时,2000年以后,随着钢铁工业的发展,对原料的要求越来越高,许多单位和矿山围绕“提铁降硅”做了大量的研究开发工作,并采用各种不同的技术方案对选矿厂进行了卓有成效的改造,取得了显著效果,使我国磁铁矿品位提高到了68.85%,SiO2由8%~9%降至4%。磁铁矿石的主要选矿工艺如下。
(1)单一磁选流程
磁铁矿是最早利用的矿石之一,磁铁矿选矿是铁矿石选矿工作的主体。磁铁矿石主要是沉积变质型磁铁矿石。矿石中铁矿物绝大部分是磁铁矿,以细粒嵌布为主;脉石矿物主要为石英或角闪石等硅酸盐矿物,有的含硅酸铁较多。由于磁铁矿石是一种强磁性矿物,采用弱磁选方法选别即可获得高品位、高回收率的铁精矿。不少大、中型磁选厂在磨矿粒度大于0.2~0.3mm时,常采用一段磨矿磁选流程;小于0.2~0.3mm时,则采用两段磁选流程。弱粗磨能分出合格尾矿时,则采用阶段磨矿磁选流程。如果采矿时混入一定围岩或矿石在各级破碎的产品中有一定量的单体脉石矿物产生,则在磨矿前利用干式磁选机进行预选。对有些矿石,为了获得铁品位66%~68%的高品位铁精矿,可再用细筛、磁选柱、反浮选等方法处理。
目前,随着入选的磁铁矿粒度的逐渐细化,磁团聚在选别中的负面影响日益明显,磁性夹杂和非磁性夹杂导致依靠单一的磁选法提高精矿品位越来越难。
(2)弱磁-阳离子反浮选工艺流程
弱磁-反浮选即把磁选法与反浮选结合起来,实现选别磁铁矿石过程中的优势互补,有利于提高磁铁矿石选别精矿品位。反浮选工艺根据药剂制度的不同,尤其是捕收剂的种类,分为阳离子反浮选和阴离子反浮选。阳离子反浮选以淀粉作为磁铁矿的抑制剂,十二胺等胺类药剂作为捕收剂。其优点是:药剂制度单一,要求的矿浆温度较低(25℃以上),中性矿浆。缺点是:浮选泡沫黏,不利于下道工序处理,分选的选择性差,并且铁精矿中SiO2含量较高,指标不太稳定,对橡胶有剧烈腐蚀作用等。如国内大型铁矿鞍钢弓长岭选厂即采用弱磁-阳离子反浮选工艺,取得了较好效果。鞍钢弓长岭磁铁矿选矿厂采用阳离子反浮选,可将含铁64%~65%、SiO28%~10%的弱磁选铁精矿提高到含铁68.5%~69.5%、SiO2降低到3.5%~4%。
(3)弱磁-阴离子反浮选工艺
相对于阳离子反浮选来说,阴离子反浮选有其自身的优点,如浮选泡沫不黏,指标较稳定,对橡胶基本无腐蚀作用。但阴离子反浮选药剂种类较多,要求的浮选矿浆温度较高(30℃以上)。碱性矿浆对精矿管道输送有利,有利于精矿直接过滤,过滤前需加酸处理。如尖山铁矿为鞍山式磁铁矿床,马鞍山矿山研究院对其进行了弱磁-正浮选和弱磁-反浮选工艺的比较,结合尖山铁矿的特点,确定尖山铁矿选矿厂提铁降硅工艺为阴离子反浮选工艺流程,取得较好的指标。太钢尖山磁铁矿选矿厂采用阴离子反浮选法,可以将含铁65.75%、SiO28.5%的弱磁选铁精矿提高到含铁69.08%、SiO2降低到3.5%~4%。
(4)全磁分选工艺流程
长期以来,大多数磁铁矿选矿厂一直采用常规的筒式磁选机作为磁铁矿精选设备,虽然在磁选机规格、给矿方式、槽体结构等方面作了大量的技术改造,但是强烈的“磁团聚”作用使磁选过程选择性降低,产生“磁性夹杂”和“非磁性夹杂”,造成最终磁铁矿精矿中SiO2含量居高不下,高达6.5%以上。为了获得高品质铁精矿,一些选矿厂选择各种全磁流程分选法,采用新型磁选设备在工业试验中获得铁精矿品位大于69%,SiO2含量小于4%的先进指标。例如,本钢歪头山和南芬选矿厂用磁选柱有效地将石英连生体从铁精矿中分选出去。精矿铁品位可提高至69.5%左右,精矿中的SiO2含量降至4%以下,尾矿品位和金属回收率基本不变,新增加加工成本小于20元/t。
全磁流程分选法主要靠各种新型磁选设备的搭配组合实现对磁铁矿的有效分选,其中比较典型的设备有磁选柱、高频振动细筛、磁场筛选机、磁聚机、脱磁器等,这些设备与传统弱磁选设备组合使用,极大地促进了磁选技术的进步。与反浮选提铁降硅相比,全磁选流程分选法突出了流程简单、工艺可靠、投资省、工期短、运行成本低、无环境污染等优势。但全磁流程的推广有一定的限制,对微细粒嵌布的磁铁矿往往不能得到良好的指标。
(5)超细碎-湿式磁选抛尾工艺
该工艺是将矿石细碎至5mm或3mm以下,然后用永磁中场强磁选机进行湿式磁选抛尾。该工艺对于节能降耗﹑有效利用极贫铁矿石和提高最终铁精矿质量具有特别重要的意义。马钢高村铁矿为了开发利用品位20%以下铁矿石,试验研究采用高压辊磨机将矿石细碎至3mm以下,中场强湿式磁选抛除40%左右粗粒尾矿,将入磨物料的铁品位提高至40%左右,经再磨再选后获最终铁精矿,该工艺最终铁精矿品位达65%以上,SiO2含量降至4%以下,尾矿品位10%以下。另外,山东莱芜铁矿﹑金岭铁矿等采用锤碎机-湿式永磁中场强磁选工艺,入选物料的粒度为-5mm占80%以上,可抛除产率30%~40%左右的粗粒尾矿。
3.2.2 典型工艺流程和生产实践
3.2.2.1 弱磁-阳离子反浮选工艺
铁矿的弱磁-反浮选工艺即把磁选法与反浮选结合起来,实现选别磁铁矿石过程中的优势互补,有利于提高磁铁矿石选别精矿品位。反浮选工艺根据药剂制度的不同,尤其是捕收剂的种类分为阳离子反浮选和阴离子反浮选。阳离子反浮选以淀粉作为磁铁矿的抑制剂,十二胺等胺类药物作为捕收剂,其优点是:药剂制度单一,要求的矿浆温度较低(25℃以上),中性矿浆。但其缺点也很明显,浮选泡沫黏,不利于下道工序处理,分选的选择性差,并且铁精矿中SiO2含量较高,指标不太稳定,对橡胶有剧烈腐蚀作用等。国内大型铁矿鞍钢弓长岭选厂应用了弱磁-阳离子反浮选工艺,也有不少研究单位对弱磁-阳离子反浮选进行了大量研究。
阳离子反浮选由于阳离子捕收剂对硅酸盐矿物有较好的选择性,不需钙盐活化,故浮选过程较简单,易于提高铁精矿品位。目前工业上采用单一阳离子反浮选流程的有加拿大的塞普特、艾利斯选矿厂和巴西的萨马科选矿厂。前者获得品位为62%~63%的铁精矿,回收率为89%~91%;后者精矿品位为67%,回收率为95%。这两个厂采用单一反浮选之所以能获得较高指标,主要是因为原矿品位高。前者原矿含铁55%~56%,后者原矿含铁53%,但是由于塞普特、艾利斯矿石中含有部分红土矿(含部分针铁矿、褐铁矿),故精矿指标低于萨马科选矿厂。
阳离子反浮选时,原矿品位的波动及矿泥的存在对选分指标有较大影响。胺类捕收剂捕收能力较弱,粗粒硅酸盐矿物不易浮游,故矿石需细磨。
(1)弓长岭选矿厂工艺流程与实践
弓长岭选矿厂一选车间于1959年建成投产,设计规模560万吨/年,处理磁铁矿石。二选车间于1975年建成投产,于1998年改造成处理磁铁矿矿石。两个选矿车间采用阶段磨矿,单一磁选,细筛再磨流程,精矿品位65%左右,SiO2含量8%~9%。自2001年开始,弓长岭矿山公司进行了磁铁矿精矿提铁降硅的试验研究工作,并于2002年相继完成了二选车间和一选车间的技术改造。技术改造的流程为:原有一、二车间流程不变,其细筛筛下精矿采用阳离子反浮选工艺,经一次粗选一次精选获得最终精矿,反浮选泡沫经浓缩磁选后再磨,再磨产品经脱水槽和多次扫磁选后抛尾,磁选精矿返回反浮选作业再选,见图3.4。

图3.4 弓长岭选矿厂提铁降硅工艺流程
改造后精矿品位为68.88%,SiO2含量降到4%以下,提铁降硅部分作业回收率为98.5%左右,改造前后工艺指标对比结果见表3.3。
表3.3 弓长岭选矿厂提供降硅改造前后指标对比结果

2007年,长沙矿冶研究院和中国矿业大学联合将浮选柱用于弓长岭磁铁矿的阳离子反浮选,十二胺药剂用量100g/t,循环矿浆压力0.045MPa,矿浆浓度43%,浮选时间7~8min,一次粗选可得到Fe品位70.00%左右的铁精矿,在一粗二扫开路试验条件下得到Fe品位70.95%的铁精矿,同时尾矿Fe品位降至20.88%。
(2)辽宁宽甸磁铁矿阳离子反浮选研究
沈阳有色金属研究院对辽宁宽甸某贫磁铁矿石进行了选矿研究。矿石中金属矿物主要为磁铁矿,其次为赤铁矿、褐铁矿、磁黄铁矿和少量的黄铁矿。非金属矿物主要为硅酸盐,其次为碳酸盐、绢云母和透闪石。矿石中磁铁矿呈不规则状浸染嵌布,同时磁铁矿中又有微小孔洞被后期脉石矿物充填,磁铁矿与脉石矿物关系密切,给磁铁矿精矿铁品位的提高造成困难。该矿石属难选贫磁铁矿矿石,其原矿多元素分析和铁物相分析结果如表3.4和表3.5所示。
表3.4 原矿多元素分析结果

表3.5 铁物相分析结果

对该矿石进行了磁选-反浮选试验,试验流程如图3.5所示,试验结果见表3.6。

图3.5 磁选-反浮选试验流程
表3.6 磁选-反浮选试验结果

结果表明,采用弱磁选-细磨磁选-阳离子反浮选的联合工艺流程,可获得高品位铁精矿。采用一段磨矿细度-0.074mm占80%,磁场强度95kA/m;二段磨矿细度-0.038mm占92.5%,磁场强度48kA/m。磁选铁精矿再经硫酸铵活化脱硫,可溶性淀粉作铁矿物的选择性抑制剂,混合胺作脉石矿物的捕收剂反浮选,可获得67.35%的高品位磁铁精矿。研究结果对同类难选贫磁铁矿石提高铁精矿品位、制取高品位铁精矿的研究与生产具有借鉴和指导作用。
(3)酒钢焙烧磁选精矿阳离子反浮选提质工业实践
酒钢选矿厂原焙烧-磁选精矿品位在56.50%左右,SiO2+Al2O3杂质含量在11%左右,严重影响了炼铁的技术指标和经济效益。为了提高铁精矿的品质,2005年上半年,酒钢钢铁研究院在实验室对弱磁选铁精矿提质降杂进行了进一步的研究,弱磁选铁精矿品位由55.17%提高到60.95%,精矿中SiO2含量为5.11%。弱磁选精矿提铁降硅试验结果见表3.7。
表3.7 弱磁选精矿提铁降硅试验结果

在实验室研究取得初步结果的基础上,酒钢与长沙矿冶研究院组成试验组,于2005年7月~11月对酒钢选矿厂弱磁系统二磁精矿进行了提质降杂工业分流试验。选厂二磁精矿多元素化学分析结果如表3.8所示,矿物组成结果如表3.9所示。可见二磁精矿中铁矿物总量为83.86%,脉石含量为16.14%,且主要以含铁碧玉、石英及千枚岩为主。铁矿物有20%左右呈连生体存在;脉石矿物有40%呈单体,60%与铁矿物呈贫连生体。说明精矿中一方面磨矿细度不够,连生体较多,另一方面机械夹杂的单体脉石也较严重。
表3.8 二磁精矿多元素化学分析结果

注:Ig为烧失量。
表3.9 二磁精矿矿物组成分析结果

二磁精矿不同粒级金属分布情况如表3.10所示。
表3.10 二磁精矿粒级金属分布结果

可见二磁精矿中大于0.074mm粒级产率为15.17%,且这部分粒级SiO2含量高,达到了25.96%,需要进一步细磨再选;从杂质分布情况来看,二磁精矿中SiO2主要分布于0.125~0.019mm粒级中,特别是0.037mm以下粒级,而这部分脉石矿物大多数已单体解离。因此,仅需进一步精选。由于矿石性质和生产工艺的原因,酒钢选矿厂循环水水质具有硬度高、pH值高的特点,通常pH值可达到8.6~9.0,而弱磁系统矿浆中水的pH值更高,可达到9.3左右。针对调试过程中出现的脉石矿物上浮困难、精矿质量差等问题,向矿浆中添加盐酸或硫酸进行矿浆pH值调整,调整后精矿品位都能够得到大幅度的提高,精矿中杂质含量大大降低,说明矿浆pH值是影响捕收效果的非常关键的因素。通过进行浮选条件试验及药剂筛选,确定了各作业的浮选机参数、浮选工艺条件以及酒钢弱磁精矿反浮选药剂——GE-609阳离子捕收剂。72h稳定试验结果表明,一次粗选、一次精选、四次扫选反浮选流程指标为精矿品位61.82%,SiO2含量5.46%,作业回收率93.98%。与同期生产指标相比,精矿铁品位提高4.05个百分点,SiO2降低4.65个百分点。二磁精浮选降杂工业分流试验工艺流程见图3.6,试验结果见表3.11。

图3.6 二磁精浮选降杂工业分流试验工艺流程
表3.11 弱磁选精矿提质降杂工业分流试验结果

将反浮选流程连续稳定试验产品及同期现场弱磁选三次磁选作业的产品分别进行多元素化学分析、矿物组成分析,结果分别见表3.12、表3.13。
表3.12 产品多元素化学分析结果

表3.13 产品矿物组成分析结果

可见,选矿厂焙烧-磁选系统提质降杂实施改造后,精矿品位提高4.00个百分点、SiO2降低4.50个百分点,且减少了K2O、Na2O、P、S等杂质的含量,经济效益显著。
在国外,弱磁-阳离子反浮选工艺已经广泛应用于磁铁矿的选矿。美国恩派尔选矿厂阳离子反浮选工艺主要用于选别两段弱磁选后含铁63%的铁精矿。加拿大多米尼翁铸造钢铁公司亚当斯矿采用磁选-阳离子反浮选流程,铁精矿铁品位达到68%。加拿大钢铁公司格里菲斯矿采用磁选-细筛-阳离子反浮选流程,铁精矿铁品位达到69.3%,SiO2含量3.50%。加拿大谢尔曼矿采用磁选-分级-磁选-阳离子反浮选流程,铁精矿铁品位67.5%,SiO2含量5.00%。
3.2.2.2 弱磁-阴离子反浮选工艺
相对于阳离子反浮选来说,阴离子反浮选有其自身的优点,如浮选泡沫不黏,指标较稳定,对橡胶基本无腐蚀作用。但阴离子反浮选药剂种类较多,要求的浮选矿浆温度较高(30℃以上),碱性矿浆,对精矿管道输送有利,不利于精矿直接过滤,过滤前需加酸处理。
(1)尖山铁矿生产实践
尖山铁矿为鞍山式磁铁矿床。矿石中的主要矿物为磁铁矿、石英铁闪石、透闪石、赤铁矿等。地质储量(B+C)1138亿吨,平均地质品位TFe34.45%、SFe32.14%。尖山选矿厂设计年处理原矿500万吨。矿石经破碎筛分、三段磨矿、两段细筛、五段磁选后铁精矿品位达65.5%,含SiO28%。选矿厂于1994年8月开始生产。1997年7月1日长距离铁精矿输送管道投入运行,选矿生产能力大大提高,当年生产精矿80万吨,此后逐年增加,1998年输送精矿120万吨,1999年为161万吨。选厂第四系列于2001年11月3日试车投产,投产后尖山选矿厂每年生产精矿200万吨(设计)。铁精矿在前处理车间经浓缩、加药搅拌,通过隔膜泵经102.3km的长距离管道送往太原的后处理车间过滤。
马鞍山矿山研究院在小型试验中也对两种反浮选工艺进行了探索,认为胺类阳离子捕收剂和阴离子捕收剂相比,分选的选择性差,并且铁精矿中SiO2含量较高。根据该院的选矿试验结果和鞍钢的实践经验,并结合尖山铁矿的特点,确定尖山铁矿选矿厂提铁降硅工艺为阴离子反浮选,采用一粗、一精、三扫的工艺流程(见图3.7),主要工艺指标见表3.14。

图3.7 尖山铁矿阴离子反浮选数质量流程图
表3.14 尖山磁选精矿阴离子反浮选设计指标

新增加阴离子反浮选工艺流程后,年处理磁选精矿为230万吨,年产含铁品位68.8%、SiO24%的反浮选铁精矿214.59万吨,精矿产量减少15.41万吨。综合分析,改造后每年增加的利润总额为2857万元,经济效益显著。
(2)鲁南矿业公司生产实践
鲁南矿业公司矿石为沉积变质鞍山式贫磁铁矿,主要含铁矿物为磁铁矿、假象赤铁矿及褐铁矿,主要脉石矿物为石英、铁闪石、普通角闪石,少量脉石矿物为黑云母、绿泥石、阳起石、方解石、长石、金红石等。磁铁矿是主要回收矿物,多呈半自形、自形或他形集合体产出。磁铁矿分布在两种条带中,在以铁矿物为主的条带中,磁铁矿粒度较粗,一般在0.014~0.31mm,较大颗粒可达0.33~0.57mm,细小的为0.001~0.007mm,以脉石为主条带中的磁铁矿多为细粒浸染在脉石矿物中,粒度为0.002~0.036mm,石英为主要脉石矿物,普遍成粒状或集合体嵌布在其他矿物间。嵌布粒度在两种条带中有所不同,在以铁矿物为主的条带中,石英的粒度较脉石条带中石英的粒度细一些,而以闪石为主的脉石条带中,石英粒度又比以石英为主的条带中的石英粒度细,石英粒度大而不均,一般为0.09~0.36mm,小者为0.014~0.018mm,其化学多元素分析结果见表3.15,物相分析结果如表3.16所示。
表3.15 化学多元素分析结果

表3.16 铁物相分析结果

鲁南矿业公司改造前的工艺流程为阶段磨矿、阶段选别、细筛返回再磨、高频振动细筛与三段磨矿形成闭路的多段选别工艺流程,在矿石性质先天不足的情况下,2002年精矿品位达到64%以上,磨矿细度-0.074mm占93%以上,改造前工艺流程如图3.8所示。

图3.8 改造前工艺流程
由于矿石性质的限制,单一磁选流程在充分挖潜的基础上,与莱钢对原料质量的要求仍有一定差距,2002年6月~12月生产指标见表3.17。
表3.17 2002年鲁南矿业铁精矿生产指标

马鞍山矿山研究院对鲁南矿业磁选铁精矿进行了反浮选提铁降硅的研究,对比了中矿集中返回粗选和中矿顺序返回前一两种试验流程,工艺流程如图3.9所示,闭路试验结果如表3.18所示。

图3.9 马鞍山矿山研究院磁选铁精矿反浮选提铁降硅工艺对比流程
表3.18 闭路试验结果

结果可知,采用中矿顺序返回工艺优于中矿集中返回粗选工艺,故鲁南矿业公司对原有工艺流程进行了改造,即在原单一磁选流程工艺基础上,增加了磁选精矿的阴离子反浮选工艺,改造后工艺流程如图3.10所示。

图3.10 改造后工艺流程
在阴离子反浮选流程中,入浮前设置浓密机,用于稳定入浮矿浆浓度、浮选药剂用量等诸多对浮选作业有影响的因素。另外,一扫中矿返回浓密机,与返回粗选相比,有利于分选过程的稳定,改造前后分选指标的对比如表3.19所示,003年6~12月生产指标如表3.20所示,可见,改造后大大提高了精矿品位。
表3.19 改造前后指标对比

表3.20 2003年6~12月生产指标

反浮选改造后,精矿成本每吨增加26.25元,但由于提高了铁精矿品位,每吨铁精矿价格提高100元以上,经济效益显著。
(3)大孤山选厂弱磁-反浮选提质的研究
鞍钢大孤山选矿厂采用单一磁选工艺,为了提高其磁铁矿精矿品位进行了反浮选提质的试验研究,选择四次脱水给矿和二磁精作为阴离子和阳离子反浮选的给矿,进行了对比研究。
阴离子反浮选采用的工艺条件:浮选温度30~33℃,浮选浓度33%左右,矿浆pH值10.5~11.0;阳离子(中性)反浮选采用的工艺条件:浮选温度为25℃左右,浮选浓度33%左右,矿浆pH值为中性。
四次脱水给矿阴离子反浮选流程采用一次粗选、一次精选选别,粗选尾矿进行三次扫选的中矿顺序返回前一作业。浮选药剂制度:NaOH用量为1125g/t,淀粉用量为1875g/t,CaO用量为250g/t,MZ-21用量为粗选200g/t、精选55g/t。在四次脱水给矿品位为64.66%、粒度为-0.074mm占96.50%时,取得了精矿品位68.67%、尾矿品位27.60%、回收率94.45%的选别指标,其数质量流程见图3.11。

图3.11 四次脱水给矿阴离子反浮选闭路数质量流程
四次脱水给矿阳离子(中性)反浮选-磁选抛尾工艺流程采用一次粗选、一次精选选别,浮尾采用磁选抛尾,中矿返回前一作业。阳离子反浮选以十二胺为捕收剂,其用量为粗选60g/t、精选20g/t。磁选管磁场强度为80kA/m。在给矿品位为64.66%时,取得了浮精品位68.60%、产率75.21%、磁尾品位32.00%、产率3.30%的开路选别指标。其数质量流程见图3.12。

图3.12 四脱给阳离子反浮选闭路数质量流程
二次磁选精矿再磨后阴离子反浮选工艺流程采用一次粗选、一次精选、三次扫选选别,中矿顺序返回前一作业。二次磁选精矿适宜磨矿粒度为-0.074mm占98%左右。浮选药剂制度NaOH用量为1125g/t,淀粉用量为1875g/t,CaO用量为400g/t,MZ-21用量为粗选230g/t、精选85g/t。其闭路试验,在磨矿粒度为-0.074mm98%、品位为60.82%时,取得了浮精品位69.24%、浮尾品位18.18%、回收率95.07%的选别指标。其数质量流程见图3.13。

图3.13 二磁精阴离子反浮选闭路试验数质量流程
二次磁选精矿再磨后中性阳离子反浮选-磁选抛尾工艺流程采用一次粗选、一次精选选别,浮尾采用磁选管抛尾,中矿返回前一作业。浮选药剂制度:十二胺用量为粗选70g/t、精选25g/t,磁选管磁场强度为80kA/m。当二次磁选精矿磨矿粒度为-0.074mm占98%、品位为60.82%时,开路试验取得了浮精品位68.68%、产率69.88%,浮尾品位19.96%、产率11.08%的试验结果,见图3.14。

图3.14 二磁精再磨阳离子反浮选-磁选抛尾工艺开路数质量流程
上述4种方案,因工艺流程的差别取得的选别指标也不相同。在现生产流程的相同作业引入不同反浮选工艺时,与阳离子反浮选流程相比,阴离子反浮选工艺流程图3.11、图3.13取得的铁精矿品位均较高,分别达到68.67%和69.24%。阳离子(中性)反浮选-磁选抛尾工艺流程图3.12、图3.14取得的选别指标较差,不仅尾矿品位较高,而且要取得高品位铁精矿也较困难,开路试验的铁精矿品位仅达到68.60%和68.68%,说明其选分效果较差。在现生产流程的不同作业均引入阴离子反浮选时,二次磁选精矿再磨后阴离子反浮选与四次脱水给矿阴离子反浮选流程相比,前者取得的铁精矿品位较高,提质效果明显。
3.2.2.3 全磁分选工艺
长期以来,大多数磁铁矿选矿厂一直采用常规的筒式磁选机作为磁铁矿精选设备,虽然在磁选机规格、给矿方式、槽体结构等方面作了大量的技术改造,但是由于强烈的“磁团聚”作用,磁选过程的选择性降低,产生“磁性夹杂”和“非磁性夹杂”,造成最终磁铁矿精矿中SiO2含量居高不下,高达6.5%以上。为了获得高品质铁精矿,一些选矿厂选择各种全磁流程分选法,采用新型磁选设备在工业试验中获得铁精矿品位>69%、SiO2含量<4%的先进指标。
全磁流程分选法主要靠各种新型磁选设备的搭配组合实现对磁铁矿的有效分选,其中比较典型的设备有磁选柱、高频振动细筛、磁场筛选机、磁聚机、脱磁器等,这些设备与传统弱磁选设备组合使用,极大地提高了磁选技术的进步。与反浮选提铁降硅相比,全磁流程分选法突出了流程简单、工艺可靠、投资省、工期短、运行成本低、无环境污染等优势。但全磁流程的推广也有一定的限制,对微细粒嵌布的磁铁矿往往不能得到良好的指标。
(1)歪头山铁矿全磁流程分选工艺与实践
歪头山的全磁分选流程是典型的新型磁选设备组合,工艺流程如图3.15所示。原主厂房的三磁精矿由渣浆泵送至新厂房,经过高频震动细筛-磁选机-磁选柱得到合格精矿Ⅰ,磁选的尾矿为最终尾矿,筛上及磁选柱中矿合并经浓缩磁选后进入球磨机与水力旋流器构成的闭路磨矿系统进行细磨至-0.076mm 85%后,进入磁选-细筛-磁选获得合格精矿Ⅱ,磁选的尾矿为最终尾矿,细筛的筛上产品返回浓缩再磨再选。精矿Ⅰ和精矿Ⅱ合并给入过滤机,过滤滤液返回原厂房分级作业,过滤滤饼给入胶带机转运至精矿仓。尾矿经自流槽给入ф53m浓密机。

图3.15 歪头山铁矿全磁分选工艺流程
该流程有以下优点:
该流程为单一弱磁全磁选流程,无药剂,无污染;流程切入点准确,开口少,优化整体工艺流程,达到降硅提铁的最终目的,合理而经济;工艺简单可靠,设备成熟先进;铁精矿由67%提高到69%以上,SiO2由6.5%降到4.5%以下,降硅提铁效果显著。
该工艺的新型磁选设备组成如下:
MVS2020高频振网筛20t/h(干矿量);CXZ60磁选柱15t/h(干矿量);BX-1024型磁选机50t/h(干矿量),200m3/h(矿浆量);CTB-1021磁选机60t/h(干矿量),200m3/h(矿浆量)。经过计算以及考虑设备配置要求,一段细筛选用16台MVS2020高频振网筛,二段细筛选用4台MVS2020高频振网筛,选用16台CXZ60磁选柱,筛下磁选机选用BX-1021磁选机6台,再磨后一次磁选选用BX1021磁选机4台,二次磁选选用CTB-1021磁选机4台。另外,在二段细筛前选用10台GMT-ф159高效脉冲脱磁器。
(2)南芬铁矿全磁流程分选工艺与实践
本钢南芬选矿厂在技术改造之前,铁精矿品位为67.50%、SiO26.5%。针对流程中筛分效率低、二次循环负荷大以及磁性夹杂严重的问题,进行了全面的工艺流程改造。其工艺改造提铁降硅工艺流程见图3.16。

图3.16 本钢南芬铁矿选厂提铁降硅工艺流程
南芬铁矿选厂主要进行了以下改造:
①细筛改造。将原有的尼龙细筛改成高频振动筛,提高筛分效率,使筛分效率由30%提高到55%,将筛孔变小,由原来的0.15mm降到0.125mm,提高筛下-0.074mm的含量。
②分级改造。原流程的二次分级溢流粒度偏粗,实际为+0.125mm占18%左右,而设计指标为+0.125mm占12%左右。二次分级溢流单体解离度低。考虑到分级机为高堰式,沉降区太小,造成分级返砂量不足,二次磨矿浓度太低(58%左右),造成二次分级溢流粒度不达标。因此将分级溢流堰加高80mm,增大沉降区,降低分级转数,增加沉降时间。
③成立单独的再磨系统。由于原流程一次磨矿与二次磨矿为1对1的系统,一次磨矿经过一段选别后,再进入二次磨矿。经过二段选别后,细筛筛上量返回到二次分级。系统改造后的工艺流程为:一次磨矿与二次磨矿为3对2的系统,每三台二次磨矿剩下一台单独处理筛上量。通过以上系统改造,二次分级溢流粒度由+0.125mm占18%降到12%,取得了明显的成效。
④选别改造。原流程细筛筛下量由三段脱水槽和三段磁选机处理而成为最终精矿。由于脱水槽和磁选机分离机械夹杂的效果不明显,选别改造用磁选柱代替了三段脱水槽和磁选机,因为磁选柱去除机械夹杂和连生体的能力很强。
⑤过滤改造。由于提铁降硅技术改造后,精矿粒度变细,再用原来的内滤式筒式过滤机难以处理,改用盘式过滤机,单机处理量大,过滤利用系数由0.8t/(m2·h)增大到1.0t/(m2·h)。
⑥完善自动控制系统。本钢南芬选矿厂原流程采用一次磨矿自动控制系统;为确保二次分级溢流粒度的细化和稳定,安装了二次磨矿系统的自动控制;选别段磁选柱为了稳定精矿浓度,安装了自动控制系统;盘式过滤机和高频振动筛自带自动控制系统。为了及时反馈精矿品位,从而调整各工序操作,安装了精矿品位仪。为了解决回水的水质和水压问题,进行了浓密及自动控制。总体上提升了南芬选矿厂的自动控制水平。
⑦回水系统改造。由于磁选柱的用水量相对较大,加上回水水质较差,南芬选厂对回水系统进行了改造。一方面浓缩及提高了底流浓度,增加了回水量;另一方面,浓缩机中加入了絮凝剂,以提高回水水质。
全磁流程主要新型磁选设备有:MVS2020高频振网筛82台,BX磁选机49台,CXZ60磁选柱67台。其生产指标铁精矿品位在69.5%以上,SiO2低于4%。
(3)大孤山铁矿全磁流程分选工艺与实践
鞍钢大孤山铁矿选矿厂全磁流程提铁降硅改造后工艺流程见图3.17。单系统工业试验取得了原矿品位29.73%,精矿品位67.44%,尾矿品位10.25%,金属回收率77.27%的技术指标。

图3.17 大孤山铁矿选厂提铁降硅工艺流程
针对大孤山选矿厂原流程存在的问题,根据矿石性质,决定采用图3.17的流程进行工业试验。试验流程构成:二次分级为ф500mm×5水力旋流器组,动压给矿,自动控制;一次、二次脱水槽为ф3000mm和ф2000mm脱水槽。除一次磁选用现场永磁机外,二次、三次、四次、五次磁选都采用BXф1050mm×2400mm多极磁系磁选机,一段细筛和二段细筛都采用MVS型高频振网筛,规格分别为2000mm×2000mm和1800mm×2000mm。改造单系统工艺流程特点分析如下:
①一段磨矿。因为一段磨矿自动控制方式为控制溢流浓度,间接控制台时处理能力,所以对品位高易磨的原矿,在保证溢流粒度达到-0.074mm占55%时,对一次磁选和二段磨矿的给入金属量和矿量增加,给流程后部作业造成压力。因此,应按金属量控制台时处理能力,以保证一次磁选选别效率和二段磨矿粒度及后部流程的通畅。
②一次磁选作业。一次磁选为流程的首道选别作业,受原矿量和二段磨矿排矿量的双重影响,在处理能力上应有一定的缓冲余地,以保证一次磁选尾矿抛出产率35%以上的量,确保旋流器溢流达到-0.074mm占87%、品位达到45%以上,为整个流程的运行创造良好条件。
③二段磨矿。二段磨矿采用自动控制动压给矿旋流器作为分级设备,给矿压力和泵箱液位便于平稳控制。在保证磨矿效果、提高溢流粒度和提高入筛品位等方面发挥重要作用。
④一脱作业。一次脱水槽提质幅度较大,脱泥效果发挥充分。主要是因为旋流器溢流粒度提高,自动控制和稳定给矿量,矿液面平稳,降低尾矿品位。
⑤BX型多极磁系磁选机。二次磁选以后的各段磁选均采用BX型多极磁系磁选机,由于其包角大、极数多、磁场分布更趋合理,又引入了精矿漂洗水。该磁选机选别效率较高,提质幅度大,保证入筛品位,对最终精矿品位达到67.50%以上起到了强有力的保证作用。
⑥细筛作业。流程中两段细筛均采用筛孔尺寸0.09mm×0.09mm的MVS高频振网筛。电磁振动高频振网筛与尼龙细筛相比,在筛下品位保持不变的前提下,筛分效率提高10%以上,筛上循环量可减少30%以上。该细筛可通过调整激振电流和筛孔尺寸控制筛下粒度和筛下品位,对保证最终精矿质量和减少筛上循环量有重要作用。
⑦再磨作业。流程中,将原生产流程的三脱、三次磁选放在二段细筛前,两段细筛筛上量经脱水永磁机浓缩后进入再磨机,对提高入筛品位和减少筛上循环量有明显效果。再磨通过量从90%减少到50%,再磨效果好,对保证细筛再磨循环量的稳定乃至获得较高选别指标至关重要。
(4)板石沟铁矿全磁分选工艺与实践
板石沟铁矿筛下精矿磁选柱再选工艺于2002年12月份改造完毕,设备联系图见图3.18。经4年多的生产实践,改造前后的生产技术指标对比见表3.21。精矿品位从66.14%提高至67.67%,且始终稳定在67.30%以上,比工艺改造前提高了1.16个百分点;同时由于磁选柱中矿返回二段磨机,增加循环量,造成一段球磨机处理量,比改造前降低了1.4t/h。

图3.18 板石沟铁矿磁选-细筛-磁选柱全磁流程设备联系图
1—MQG-2700mm×3600mm格子型球磨机;2—FLG-2000mm高堰式双螺旋分级机;3—CS-20S顶部磁系脱水槽;4—CTB-ф1050mm×2400mm永磁磁选机;5—4PNI胶泵;6—ф350mm水力旋流器;7—MQY-ф2700mm×3600mm溢流型球磨机;8—CS-25底部磁系脱水槽;9—CTB-ф1050mm×2400mm永磁磁选机;10—4PNI胶泵;11—尼龙固定细筛;12—4PNJ胶泵;13—ф600mm磁选柱;14—CTB-ф1050mm×2400mm永磁磁选机;15—4PNJ胶泵;16—CTB-ф1050mm×2400mm永磁磁选机;17—CN-40筒式真空过滤机;18—ф50m周边转动浓缩机
表3.21 板石沟铁矿改造前后生产指标对比

(5)峨口铁矿全磁分选工艺与实践
峨口铁矿属鞍山式沉积变质岩型贫磁铁矿石。矿石分为两种类型,即含碳酸盐磁铁石英岩型(简称石英型)和含碳酸盐铁镁闪石磁铁矿石英岩型(简称闪石型)。矿石中主要的金属矿物是磁铁矿,其次为碳酸铁矿物(镁菱铁矿),再次为少量赤、褐铁矿及黄铜矿等;脉石矿物主要为石英。其次为铁白云石、绿泥石、角闪石、方解石及少量黑云母、石榴子石等。铁矿物结构一般以半自形晶粒状变晶结构为主,其次为他形或自形晶粒状结构,局部有交代结构。铁矿物呈不均匀细粒嵌布,嵌布粒度大多数在0.01~0.1mm之间。峨口铁矿投产几十年来主流程一直采用阶段磨矿、阶段选别流程。随着服务年限增加、北区矿石的开采,矿石中的磁铁矿结晶粒度变细,原有的选矿生产工艺流程远远不能达到选矿生产计划指标。
经过技术改造,将原来的一段3台磨矿机(1、2、3号磨机)、二段的2台磨机(9、10号磨机)与新增加1台磨机形成一段、二段、三段磨矿分别为3台、2台、1台的“321”磨矿选别流程。改二次螺旋分级机为水力旋流器,三段磨矿机与德瑞克高频振动细筛构成闭路的流程。用变径型磁团聚重力选矿机代替磁力脱水槽作业,变径型磁团聚重力选矿机的溢流经过浓缩磁选后,进入三段磨矿机,减掉磁力脱水槽后的两段磁选为一段磁选。“321”流程采用磁团聚重选新工艺后,经过长时间的运转,生产指标稳定。对其工艺进行考查,其数质量、矿浆量流程见图3.19。

图3.19 太钢峨口铁矿磁选-高频振动筛-磁聚机全磁工艺数质量、矿浆流程
Q——处理量;C——矿浆浓度;β——精矿铁品位;γ——产率;W——水量;ε——回收率
变径型磁团聚重力选矿机的工作特性,决定了其产品的粒度不同于磁力脱水槽。精矿粒度与粒度组成不同。磁团聚后的磁选作业和磁力脱水槽的磁选作业效果不同。磁团聚重选新工艺不仅磁聚机作业提高值大,而且其后的磁选作业提高值也大。使用磁团聚重选新工艺,“321”流程的精矿品位达66.01%,全铁回收率66.32%;原流程的精矿品位63.88%,全铁回收率59.75%。磁选-高频振动筛-磁聚机新工艺使用,使峨口铁矿选厂精矿品位达到一个新的水平,为65.15%,全铁回收率61.28%。
(6)硖口驿铁矿全磁分选工艺与实践
硖口驿选矿厂处理的是陕西汉钢杨家坝蛇纹岩型贫磁铁矿石。主要金属矿物是磁铁矿,含有少量假象赤铁矿、褐铁矿、黄铁矿和微量黄铜矿及磁黄铁矿。脉石矿物主要是蛇纹石、滑石,其次为透闪石、绿泥石、白云石(含铁)、方解石、金云母及少量磷灰石等。磁铁矿呈自形、半自形及他形粒状集合体,颗粒一般为0.1~0.5mm,个别矿块磁铁矿颗粒较细,在0.05mm以下。磁铁矿集合体中有裂隙和破碎现象,被脉石矿物胶结充填其中。磁铁矿有的呈脉状或网状,局部磁铁矿有细小包裹体。蛇纹石以纤维蛇纹石、叶蛇纹石为主。在蛇纹石表面,常见磁铁矿细粒浸染状不均匀分布。滑石呈鳞片状集合体,分布在磁铁矿裂隙间,并交代蛇纹石、透闪石等矿物。该矿铁品位较低,仅25%左右。磁铁矿颗粒一般较粗,但部分较细,而且铁矿物与脉石互有充填或包裹或相互浸染,从而在较粗磨矿粒度下(-0.037mm<70%)难于基本解离,因此常规磁选精矿品位不高,仅为62%。采用细筛磁选柱流程方案,将一磁精矿经筛孔为0.5mm的细筛分级,筛下同二次球磨产物先进行二次磁选,精矿再进入磁选柱精选,可以将其精矿品位由62%提高到65%左右,其改造后流程见图3.20。该流程方案从粗磨条件下的一磁精矿提前拿出对应原矿产率为22.15%的矿量,绕开二次磨矿,而是直接经二次磁选及磁选柱精选将其绝大部分选别成为合格的最终精矿。该流程方案,既提高了精矿品位,又降低了二次球磨负荷。

图3.20 硖口驿选矿厂磁选-细筛-磁选柱工艺流程图
(7)水厂选矿厂全磁分选工艺与实践
首钢水厂选矿厂将原“固定细筛-永磁磁聚机-固定细筛”工艺流程提升为“高频振网筛-复合闪烁磁场精选机”新工艺,见图3.21。新流程解决了原流程中存在的磨矿分级效率低、循环负荷过大的难题。工艺流程具有结构简单、配置合理、节能降耗、运行可靠的特点,显著提高了选矿技术经济指标。筛分效率大幅度提高,新、老主厂台时处理能力分别比原流程提高了9.20%和8.10%,在入选品位仅为26%左右的情况下,铁精矿品位稳定在68%以上。

图3.21 首钢选厂磁选-细筛-复合闪烁磁场精选机流程图
3.2.3 微细嵌布磁铁矿选矿技术与实践
微细嵌布磁铁矿石包括磁铁石英岩和磁铁矿石两种类型。
磁铁石英岩即铁隧岩,或鞍山式贫铁矿石,多集中分布在鞍本、五岚及冀东地区。矿石中主含磁铁矿和石英,依据磁铁石英岩的磁学性质,一般利用磁铁矿和石英磁化系数的较大差别进行磁选,典型的这一类选矿厂有美国伊里选厂、明塔克选厂、加拿大亚当斯选厂、前苏联的库尔斯克矿石公司、中国的大石河南芬和大孤山等选矿厂。磁铁石英岩的分选工艺是:经三至四段破碎至25~15mm,或经一段破碎到350~250mm,通过自磨与球磨(砾磨)结合,实施三段细磨,进入多段磁选。磁铁石英岩选矿的工艺特点是采取阶段磨矿和磁选流程,以便阶段排出单体脉石,减少下一阶段的磨矿量。微细粒嵌布的石英铁质岩用浮选法或焙烧磁选法来处理。美国Tilden选矿厂用选择性絮凝、阳离子反浮选处理细磨到-0.025mm80%的矿石。鞍山烧结总厂和齐大山选矿厂曾用竖炉,前苏联克里沃中部采选公司选矿厂曾用回转窑对细粒嵌布赤铁矿石进行还原焙烧处理后再磁选获得铁精矿。
磁铁矿石属于矽卡岩型矿石,其中主要铁矿物为磁铁矿,还含有少量的硫化矿物,并伴生有钴、镍、钒等有色金属,脉石为矽卡岩。矿石呈斑点状、角砾状、带状和块状。磁化系数与磁铁石英岩相似。根据粒度嵌布特性可分为粗粒、细粒、微细粒和极微细粒嵌布矿石。典型的这一类选矿厂有美国恩派尔选厂、格雷斯选厂、加拿大希尔顿选厂和澳大利亚怒江选厂。中国的多集中分布在鄂东、邯郸、山东、江苏和安徽等地,有五家子铁矿和玉石洼铁矿等。依据磁铁矿石的物理性质,最有效的选矿方法是以磁选法回收磁性矿物,以浮选法回收伴生的硫化矿物。其分选工艺多是二至四段破碎,并在破碎流程中配有一至二段干式磁选,选别中碎或细碎产品。对进一步深选产品,经二至三段细磨,进行二至五次湿式磁选,获得的最终铁精矿产品采用磁选-浮选或浮选-磁选等联合流程,在提高铁精矿品位的同时,还可回收伴生矿物成为相应的精矿产品,以及进行精矿的脱硫。磁铁矿石磨矿粒度较粗且泥化的粒子含量较少,一般用磁选机即可进行脱泥。选别磁铁矿石的选矿厂按照全循环供水流程操作,循环水利用率为75%~85%。
3.2.3.1 鞍钢谷首峪铁矿
鞍钢谷首峪铁矿石属于微细嵌布的贫磁铁矿,全铁品位为31.90%,96.14%的铁分布在磁铁矿中,还有一部分以菱铁矿、硅酸铁和假象、半假象赤铁矿形式存在。其矿石的化学多元素分析、铁物相分析分别见表3.22和表3.23。
表3.22 谷首峪铁矿石的化学多元素分析

表3.23 谷首峪铁矿石的铁物相分析

鞍钢谷首峪铁矿石采用阶段磨选工艺(工艺流程如图3.22所示),试验的最终结果为原矿品位31.90%,精矿品位65.53%,精矿产率27.07%,中矿品位59.74%,中矿产率14.34%,尾矿品位9.55%,尾矿产率58.59%;对二段磨矿闭路,将三、四段细筛筛上返回三段磨矿进行连选试验,结果表明,当原矿品位为31.72%时,精矿品位65.05%,尾矿品位10.21%,金属回收率80.43%。

图3.22 谷首峪铁矿石的选矿工艺流程图
3.2.3.2 庙沟铁矿选矿厂
庙沟铁矿位于河北省秦皇岛市青龙满族自治县祖山镇,1986年1月成立,现有铁矿储量1546万吨。庙沟铁矿坐落于秦皇岛市青龙满族自治县祖山镇,1986年1月建矿,1993年扩建,2008年进行选矿改造,年产铁精粉50万吨,储量1546万吨,现正在对其深部进行扩界补勘。2002年建成炼钢冷料基地,年产炼钢生铁43.5万吨,烧结矿50万吨,球团矿42万吨。2008年6月30日,河北钢铁集团有限公司正式挂牌成立,庙沟铁矿隶属河北钢铁集团矿业公司。
庙沟铁矿的矿石属鞍山式磁铁石英岩,矿石主要由石英、磁铁矿、铁闪石-镁铁闪石等矿物组成。矿石呈细粒变晶结构,条纹状或条带状构造。主要金属矿物为磁铁矿,其次为赤铁矿和假象赤铁矿。磁铁矿呈黑色或钢灰色、半自形-他形晶粒状,沿片理方向呈拉长状定向排列,主要与铁闪石紧密共生,组成磁铁-铁闪石条带。磁铁矿属于细粒不均匀嵌布,结晶粒度一般在0.01~0.15mm之间,在粒度为-0.045mm(-325目)以下时单体解离度才可达到96%。
原选矿工艺采用阶段磨矿-磁选-细筛传统工艺流程,采用三段磨矿、三段细筛、十段磁选,细筛为固定尼龙细筛,一段细筛筛孔0.15mm,二段、三段筛孔0.10mm,三段筛下产品细度控制在-0.074mm占95%、-0.045mm占85%。该矿在历经多年的开采后,易磨易选矿石比例不断减小;矿石性质复杂,嵌布粒度较细的难选矿石比例增大,使选厂生产铁精矿品位只有TFe63%左右,个别时段只能达TFe60%,选厂只好通过降低磨机处理能力来维持TFe 63%的精矿品位,造成选矿厂产量和质量下降,原选矿工艺流程如图3.23所示。

图3.23 庙沟铁矿技改前采用的选矿工艺流程
针对由矿石性质变化带来的选矿指标偏低的状况,必须采用新技术、新设备来提高铁精矿品位和生产能力。经采用磁场筛选机工业试验后,最终确定的技改工艺方案为:采用三段磨矿-二段细筛-二段磁筛精选-磁筛中矿单独处理的工艺流程,通过磁筛精选的技改工艺流程如图3.24所示。

图3.24 采用磁筛精选技改后的工艺流程
原生产工艺流程存在的主要问题是磁选粗精矿全部通过细筛,而细筛分级效率低,造成磨机返砂量增大,严重制约了选矿厂生产能力的提高。随着矿石嵌布粒度变细,本来处于不堪重负的再磨系统长期处于过负荷状态,最后的直接后果是生产能力降低,铁精矿品位也较低。从这一传统的选矿方法来看,主要存在的问题是在磨矿细度的控制上实行“一刀切”,全部进入再磨,这样会对大多数呈粗细不均匀嵌布的磁铁矿中的粗粒磁铁矿单体造成过磨,而仍以微细粒连生体存在的铁矿物还会过筛进入精矿,从而影响精矿质量。
以磁筛精选为核心的技改后的工艺流程为二段磨矿磁选与一段细筛闭路,一段细筛筛网可适当放粗,筛下产品经第一段磁筛精选后,可提前将易磨易选的精矿和难磨的中矿分离,然后分别再磨精选,这样可充分提高磨矿效率、减少三段磨矿负荷、提高精矿品位,同时对这部分难选中矿在小选厂采用长筒型磨机进行充分再磨处理的工艺是最经济的方法。
在磁铁矿选矿传统磨矿-磁选-细筛工艺中,当磁选厂磨矿容量一定时,其生产能力取决于入选物料的磨矿细度。一般而言,精矿品位每提高1%,降低生产能力10%~13%。首钢矿山20世纪70年代引进当时较先进的磁选-细筛工艺,铁精矿品位由原来的TFe63.87%提高到68.5%,同时生产能力也下降23%。以上说明,继续使用传统磁选机多次精选提高精矿品位必须减产,不然要花费大量资金扩建、新建磁选厂,普遍存在质量与产量、质量与选矿成本的尖锐矛盾。
采用磁筛精选工艺处理磁铁矿时,它能将铁粗精矿中已解离的单矿物与连生体优先分离,只有连生体部分再磨再选,从而相对地减少了磨机循环负荷,提高了磨矿效率,在提高精矿质量的同时还能不同程度地提高生产能力。采用磁筛精选工艺先后对国内多家磁铁矿进行过不同程度和规模的精选提质试验和工业应用,这其中几乎包括了国内各大矿区中不同类型和规模的磁铁矿,普遍具有较好的提质降耗效果。
磁筛精选工艺所用的磁场筛选机能广泛适用于不同类型、不同粒度的磁铁矿、钒钛磁铁矿、焙烧磁铁矿的精选,可普遍替代原磁选机的二、三段精选和磁力脱水槽作业,具有提质降耗、简化流程的多重效果。
庙沟铁矿在2005年5月使用磁筛后,在提高精矿品位的同时,还可放粗原细筛-磁选工艺中的筛孔尺寸,从而提高磨矿能力,降低能耗;精矿质量平均达65%以上,同时磨机处理能力由原来的43t/(台·h)提高到了55t/(台·h),有时甚至超过60t/(台·h)。表3.24为磁筛作业分选效果,表3.25为2005年7月份生产指标统计与上一年同期生产标准对比结果。
表3.24 庙沟铁矿选厂二段磁筛分选指标(截至2005年6月17日)

表3.25 庙沟铁矿磁筛应用前后选厂生产指标对比结果

改造后,磁筛精选工艺提质效果明显,对给矿浓度、流量、粒度等波动适应性强,分选指标稳定;精矿浓度高(65%~75%),并采用高浓度自动化排矿装置,易于脱水过滤;设备耗电少,唯一运转部件螺旋排料机的电机功率只有1.5kW,易于操作管理,设备还具有性能稳定、维护量小、维护费用低、使用寿命长等多方面的优点,磁铁矿精矿质量得到有效提高。
3.2.3.3 河南舞阳矿业公司铁古坑铁矿
舞阳矿业公司是安阳钢铁集团的重要矿产原料基地。舞阳矿区探明铁矿石地质储量6.6亿吨,占河南全省铁矿石探明地质储量的80%,平均地质品位TFe29.12%,在河南省占有举足轻重的地位。矿区主要有铁古坑、铁山庙、赵案庄、王道行、经山寺等大小10余个矿体。其中铁古坑铁矿是舞阳矿业公司的主要采选单位。
铁古坑铁矿探明地质储量1.0991亿吨,平均地质品位TFe29.29%,既有原生矿,又有氧化混合矿。铁古坑铁矿从20世纪70年代开始建设,初拟采用焙烧-磁选工艺进行选别,后因成本高而未实现。20世纪90年代初期,采用长沙矿冶研究院研究的两段连续磨矿-中磁粗选-弱磁扫选-强磁粗选-强磁精选-强磁再选工艺和磨矿-中磁选-弱磁扫选-再磨-弱磁精选工艺投产后,取得了原矿品位28.14%、精矿品位60.83%、金属回收率63.78%的选矿技术指标。为了进一步使铁古坑矿石的选矿技术指标得到提高,舞阳矿业公司先后委托鞍钢矿山设计研究院进行电选试验研究、委托马鞍山矿山研究院进行浮选试验研究、委托北京矿冶研究总院进行磁重选矿试验研究、委托赣州有色冶金研究所进行弱磁选-SLon立环脉动高梯度磁选机强磁选试验研究,但指标均不理想。
在我国选矿技术飞速发展的同时,铁古坑铁矿却由于近年来采矿贫化率高达25%~30%而使入选矿石原矿品位降至20%左右,导致选矿单位能耗高,经济效益差。为了更好地利用国家宝贵的矿石资源,提高企业效益,舞阳矿业公司停止了氧化混合矿的开采,开展了低品位难选磁铁矿高效节能选矿技术的研究和应用。经过大量的工作,舞阳矿业公司提出了多段干式预选-多碎少磨-阶段磁选抛尾-细筛+磁聚机提质-尾矿中磁扫选的技术路线,通过降低破碎系统输出粒度、减少入磨矿量、应用细筛+磁聚机提质新工艺、强化尾矿扫选等手段,实现了低品位难选磁铁矿石选矿技术的高效节能化,选矿厂处理能力由74万吨/年提高到153万吨/年,精矿铁品位由64.05%提高到67.5%以上,铁回收率由64.49%提高到69%左右,选矿电耗由48.1kW·h/t降至25.8kW·h/t,可年增经济效益7500万元以上。
铁古坑矿原矿石为灰绿至暗绿色,粒状花岗变晶结构,条带状、片麻状构造。铁矿物主要为磁铁矿,其次为硅酸铁,有少量赤铁矿;脉石矿物主要为辉石、碧玉和石英等,其次为兰闪石、白云石和紫辉石等。原矿化学分析、铁物相分析、矿物组成分析结果分别见表3.26~表3.28。
表3.26 铁古坑磁铁矿石原矿化学多元素分析结果

表3.27 铁古坑磁铁矿石原矿铁物相分析结果

表3.28 铁古坑磁铁矿石原矿主要矿物组成及含量

由于近年来矿石贫化率的增加,入选矿石原矿品位降至20%左右。因此,舞阳矿业公司提出了低品位难选磁铁矿的高效节能技术,提出了多段干式预选-多碎少磨-细筛-磁团聚提质-尾矿中磁扫选的技术路线,特别加强了原矿破碎流程中的预选,抛弃废石,恢复了矿石地质品位,提高了整个选矿厂的处理能力。铁古坑铁矿选厂的预选流程见图3.25,预选结果见表3.29。

图3.25 河南舞阳矿业公司铁古坑铁矿预选流程
表3.29 多段破碎多段磁滑轮预选结果

采用多段破碎多段磁滑轮干式预选工艺后,废石抛弃率可达25%左右,使选矿厂磨选车间的年处理能力由74万吨提高到115万吨,可年节省电能810kW·h。
另外该矿采用多碎少磨,降低了入磨矿石粒度,减少了磨矿能耗;采用阶段磁选拋尾工艺,强化磨矿-磁选作业,提高了粗选处理量;采用先进的细筛+磁聚机工艺,提高了铁精矿质量;增加了尾矿扫选作业,提高了铁回收率;采用节能设备,降低了选矿厂能耗;广泛使用脱磁器,消除磁夹杂,改善了分选条件,提高了选别指标。