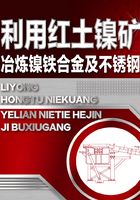
1.4 用红土镍矿火法冶炼高品位镍铁、铁、镍、“半钢”、钢及不锈钢
在第3~第6章中分别叙述了还原熔炼生产镍铁,其中在“5.2.1.1镍铁的选择性还原”一节,图5-7所示讲到了利用红土镍矿焙砂熔炼镍铁、铁、钢和金属镍工艺;在“5.4.4拉里姆纳冶炼厂”一节,图5-127也讲到了利用红土镍矿焙砂熔炼镍铁、铁、钢和金属镍工艺。
在“8.4.17.1利用矿热炉镍铁冶炼300系不锈钢”和“8.4.17.2利用高炉镍铁生产节镍型奥氏体不锈钢”两个小节,叙述了利用红土镍矿直接生产不锈钢。
1.4.1 高品位镍铁、金属镍、铁、钢的生产
图5-7所示为利用红土镍矿冶炼镍铁、金属镍、铁和钢工艺流程。原矿经回转窑焙烧,焙烧产品焙砂入电炉(矿热炉)有选择性的还原镍和一部分铁(铁不完全还原),还原的金属铁和金属镍一同入金属熔体,未还原的氧化铁和其他脉石及熔剂一同入渣,生成粗镍铁和富含铁的炉渣。用氧气转炉根据选择性氧化的原理吹炼粗镍铁使其中的部分铁氧化入渣,镍得到富集,产出高品位的镍铁,再将镍铁铸成电解电极,用电解的方法生产金属镍和钴。电炉渣和转炉渣富含铁。同时利用另一座电炉利用焦炭对富含铁的电炉渣、转炉渣进行还原熔炼,从而获得生铁(不含Ni、Co),进而再将此生铁投入转炉吹氧炼钢。
(1)高品位镍铁、金属镍的生产
①高品位镍铁的生产 在“1.3.1.2红土镍矿的火法冶炼中(3)矿热炉法①熔炼镍铁”已述,一般镍铁含镍20%~25%。为了获得高品位镍铁,利用选择性氧化的原理,采用吹氧转炉吹炼。在转炉吹炼的过程中,因大量的金属铁被氧化入渣使得镍得到富集,获得高品位镍铁。由于大量的金属铁被氧化放热使得炉温升高,此时用红土镍矿作为冷却剂比较合适,在冷却的同时,还能给转炉以简单而又廉价的镍和氧,可以抵消部分甚至全部处理费用。
虽然铁优先镍被氧化,但随着镍铁品位的提高,镍铁中镍被氧化的量逐渐加大,即炉渣中NiO的含量随合金-镍铁品位的提高而提高,因而合金品位的提高受到限制。有研究表明,当合金富集到60%时,渣中含镍量迅速升高。将产出的富镍渣返回处理,用吹氧的方法可将合金富集到所要求的任何品位,并能获得较高的镍回收率,这样做在经济上是有利的。希腊拉瑞姆纳矿业公司已把合金品位提高到镍和钴占90%,而镍的回收率仍可达到97.18%。
②金属镍的生产 电解方法主要适用于有色金属的生产。电解的实质是电能转化为化学能的过程。有色金属的电化学冶金工艺可分为可溶阳极电解与不溶阳极电解。根据电解质性质的不同,将电解过程分为熔盐电解和水溶液电解。有些金属元素,如Al、Mg等,其析出电位较负的金属离子在水溶液中无法生成,必须采用熔盐电解法;而有些金属元素,如Ni、Co、Cu、Zn等不适合熔盐电解法,可适用于水溶液电解法。镍的水溶液电解质电解应用在两个方面:从浸出液中提取镍;从粗镍、镍铁或镍锍中提取镍。
这样,在镍的电解实践中有两种电解过程:从粗镍、金属合金(镍铁)阳极及硫化镍阳极电解属可溶阳极电解;从浸出的镍盐水溶液中电解属电解沉积或不溶阳极电解。
将上面所述的高品位镍铁铸成合金阳极(镍铁阳极),采用电解的方法生产出高质量的金属镍(电解镍)。如希腊拉瑞姆纳矿业公司使用的镍铁合金阳极,含镍和钴90%、铁10%。
镍铁合金电解的阳极过程:主要是金属镍在阳极上放电溶解,负电性金属杂质也一起被溶解。而正电性的贵金属等则不溶解而留于阳极泥中。但由于大多数杂质金属与镍形成固溶体合金,加之镍的阳极化超电压比较大,使得一些较正电性的金属杂质元素,在阳极过程中也与镍一道溶解。为此,阳极液必须经过复杂的净化过程,才能返回到阴极室使用。
阳极液净化通常包括除铁、除铜(视含铜量)和除钴等工序。如氧化中和除铁、除钴。
净化后的阳极液送入阴极室作为阴极液,镍在阴极沉积到一定的时间后被剥下,即得电解镍。
(2)铁的生产 铁的生产实质是从炉渣中回收铁。电炉渣含铁较高,通常含铁45%、铬3%,同时还有1550℃的高温,因此利用渣中含有的热量和使用廉价的劣质燃料来回收铁是经济的。
利用炉渣、铁矿石和焦粉使用另一台炼渣电炉炼铁的工艺流程为:氧化铁渣、铁矿石和焦粉按比例先后加入炼渣电炉中,在电炉炉床上形成一个相对较薄的料层,从而料层能被均匀加热,迅速还原成含铬生铁和含铬渣。电炉生产的生铁含碳3.5%和少量的硅、磷,含锰和铬的量取决于还原操作的条件。由于利用液态渣内的热焓,吨铁电耗较低,仅为1700~2000kW·h/t。
(3)钢的生产 将上述得到的含铬生铁用纯碱脱硫(S<0.05%),脱硫后的生铁加入转炉内精炼可生产各种规格的优质钢。炼钢所需要的热量主要来源于生铁中的碳和铬的氧化。生铁精炼时,碳氧化成CO,铬氧化成Cr2O3,形成一种奶酪状的高熔点渣浮于熔池面上。由于吹炼时造成剧烈的搅动,因此部分铁与Cr2O3混在一起。在氧的作用下,这一部分铁也会被氧化成FeO和Fe2O3进入炉渣。为了减少铁的损失,必须避免加入诸如熔剂之类的转炉附加料以及增加扒渣次数,以便尽量限制固体渣的数量。
用这种方法生产的钢含铬0.12%、含碳低于0.15%,不含硅和锰。因处理红土镍矿得到的钢常含有一定数量的镍,但由于加入了大量的普通铁矿石,钢中含镍量很容易保持在0.25%以下。
1.4.2 “半钢”的冶炼
接图5-7所示工艺流程,红土镍矿焙砂经电炉熔炼、氧气转炉吹炼所得的铁渣含有红土矿内几乎全部的Cr2O3,即含铬铁渣,送往电炉或高炉冶炼可获得含铬铁水。铬是一种合金元素,但在炼钢过程中又容易氧化入渣,其氧化程度与炼钢工艺有关。从炼含铬合金钢的角度看,希望铬按要求的成分留在钢内,但由于铬易于氧化以及红土镍矿品位的波动,钢水中的铬很难控制到所需要的成分。此外,铬在氧化过程中生成氧化铬在渣内溶解度较低,炉渣能为Cr2O3饱和,析出固相Cr2O3和尖晶石CrO·Cr2O3,使熔渣变稠,流动性很差,不利于脱硫和脱磷。基于上述两种原因,使得人们决定要先脱铬再炼钢。
若利用该含铬铁水炼钢必须先脱铬,此外,还要必须保留一定量的碳,才能在炼钢时有充足的热源以达到出钢的温度,即“脱铬保碳”,详见“8.4.9.2”一节。为此要进行选择性的氧化。脱铬并保留有一定量碳(C1.4%~2.4%)的铁水通常称作“半钢”。
依据选择性的氧化原理,脱铬保碳,即是在低于Cr、C氧化转化温度(参见“3.1.1氧化转化温度”)时选择铬的氧化。在转炉吹炼的过程中,利用碳焰上来之前,即熔池温度低于转化温度之前将铬氧化入渣。如果温度过高,则要向熔池加冷却剂控制温度,以保证碳不被或少被氧化。
Cr、C氧化转化温度不是一成不变的,是随半钢和炉渣成分的变化而变化。当半钢中[C]维持一定时,余[Cr]越低,转化温度越低,吹炼必须在更低的温度下进行。换言之,余[Cr]越低,保[C]越难。一般的情况下熔池的温度不宜超过1400℃。如果脱铬达到一定程度,而要求半钢温度较高,则只能在多氧化一部分碳的条件下才能做到。
1.4.3 奥氏体不锈钢冶炼
镍是奥氏体不锈钢中形成奥氏体相的主要元素,故奥氏体不锈钢的冶炼除需要铬、铁外,同时还需要镍。即同时需要镍和铁,不必将镍从镍铁合金中分离。利用红土镍矿火法冶炼得到的镍铁正适合这个要求,由于不用进一步提取金属镍,这样可使得镍的获得成本大大降低。
不锈钢冶炼与普碳钢冶炼的主要区别是钢中加入大于12%的铬,为了获得更好的耐蚀性能铬加入量高达16%~27%,同时却需要低碳(如<0.12%)乃至超低碳(如0.02%)。在吹氧脱碳时,铬与碳氧化转化温度很高,如冶炼含18%Cr、9%Ni、0.02%C的奥氏体不锈钢,氧化转化温度高达2133℃。如果温度达不到,则会有大量的铬被氧化掉。因此,如何“脱碳保铬”(详见“8.4.9.1”一节)便成了奥氏体不锈钢冶炼的核心问题,高碳真空吹炼法既是针对其展开的,如氩氧混吹脱碳法即AOD法、用水蒸气代替氩气的H2O-O2混吹法即CLU法和真空吹氧脱碳法即VOD法。如用VOD法同样冶炼含18%Cr、9%Ni、0.02%C的奥氏体不锈钢,炉中真空度高于3.91kPa,则氧化转化温度可降到1650℃。
(1)300系奥氏体不锈钢的冶炼 矿热炉冶炼镍铁采用的是选择性还原法,通常矿热炉冶炼的镍铁较高炉生产的镍铁品位高,含镍量大于10%,其镍含量与300系奥氏体不锈钢含镍量接近,用其作金属母料最经济。其工艺流程如下。
采用二步法有三种工艺:①镍铁(铸块)-电炉-AOD(或VOD)-LF;②矿热炉(镍铁水)-电炉(或转炉)-AOD(或VOD)-LF;③矿热炉(镍铁水)-AOD-LF。
采用三步法也有三种工艺:①镍铁(铸块)-电炉-AOD-VOD;②矿热炉(镍铁水)-电炉(或转炉)-AOD-VOD;③矿热炉(镍铁水)-AOD-VOD。
详见第8章及“8.4.17.1”一节。
(2)节镍型奥氏体不锈钢的冶炼 通常高炉冶炼的镍铁较矿热炉生产的镍铁品位低,目前生产的镍铁产品有含镍量1.5%左右所谓的低镍铁及含镍量4%~6%所谓的中镍铁,其中镍含量1.5%左右的与牌号J4不锈钢含镍量接近,含镍量4%~6%的与201、202、J1不锈钢含镍量接近,用其作金属母料最经济。采用二步法有三种工艺:①镍铁(铸块)-电炉(或感应炉)-AOD-LF;②高炉(镍铁水)-电炉(或转炉)-AOD(或VOD)-LF;③高炉(镍铁水)-AOD-LF。
详见第8章及“8.4.17.2”一节。