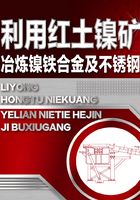
1.3 镍的冶炼技术
金属,通常是指具有金属光泽、可塑性、导电性及导热性良好的化学元素。在元素周期表中,金属元素有80多个。现代工业习惯把金属分为黑色金属和有色金属两大类:铁、铬和锰三种金属属于黑色金属,其余的所有金属都属于有色金属。有色金属一般分为4类:重金属,如铜、铅、锌、镍等;轻金属,如铝、镁等;贵金属,如金、银、铂等;稀有金属,如钨、钛、钼、钽、铌、铀、钍、铍、铟、锗和稀土金属等。稀有金属除稀土金属外,还可分为稀有轻金属、稀有高熔点金属、稀有分散金属和半金属等。重金属是指密度在4.5g/cm3以上的有色金属,其中包括铜、镍、铅、锌、钴、锡、锑、汞、镉、铋等。轻金属包括铝、镁、钠、钾、钙、锶、钡等。轻金属的共同特点是相对密度小(0.53~4.5)、化学活性大,与氧、硫、碳和卤族元素的化合物都相当稳定。
因此,冶金工业通常分为钢铁冶金工业和有色冶金工业。钢铁冶金工业是指黑色金属的生产,包括铁、钢和铁合金(如铬铁、锰铁);有色冶金工业是指有色金属的生产。
自然界中的金属矿石大多以氧化物、硫化物和卤化物等形式存在。冶金是一门研究如何经济地从矿石或其他原料中提取金属或金属化合物,并用各种加工方法制成具有一定性能的金属材料的科学。冶金方法可归纳为三种方法:火法冶金、湿法冶金和电冶金。
(1)火法冶金 它是指在高温下矿石经熔炼与精炼反应及熔化作业,使其中的金属和杂质分开,获得较纯金属的过程。整个过程可分为原料准备(如选矿、干燥、焙烧、煅烧、烧结、球团等)、冶炼和精炼三个工序。
①选矿 根据矿石中不同矿物的物理、化学性质,把矿石破碎磨细以后,采用重选法、浮选法、磁选法、电选法等,将有用矿物与脉石矿物分开,并使各种共生(伴生)的有用矿物尽可能相互分离,除去或降低有害杂质,以获得冶炼或其他工业所需原料的过程。选矿能够使矿物中的有用组分富集,降低冶炼或其他加工过程中燃料、运输的消耗,使低品位的矿石能得到经济利用。
②干燥 除去原料中的水分。干燥温度一般为400~600℃。
③焙烧 将矿石或精矿置于适当的气氛下,加热至低于它们的熔点温度,发生氧化、还原或其他化学变化的冶金过程。其目的是为改变原料中提取对象的化学组分,满足熔炼的要求。焙烧的产物称为焙砂。按焙烧过程控制气氛的不同,可分为氧化焙烧、还原焙烧、硫酸化焙烧、氯化焙烧等。例如,硫化镍矿在氧化焙烧中可以去掉矿石中的硫。红土镍矿(氧化镍矿)在还原焙烧中可以预还原出金属镍、部分金属铁和低价氧化铁。弱磁性的赤铁矿(Fe2O3)通过还原磁化焙烧使其转变为具有强磁性的磁铁矿(Fe3O4),以便磁选。
④煅烧(焙解) 将碳酸盐或氢氧化物的矿物原料在空气中加热分解,除去二氧化碳或水分变成氧化物的过程。如石灰石煅烧成石灰。
⑤烧结和球团 将粉矿加热焙烧,固结成多孔块状或球状的物料,是粉矿造块的主要方法。
⑥熔炼(冶炼) 将处理好的矿石或其他原料,在高温下通过氧化还原反应,使矿石中金属和杂质分离为两个液相层,即金属液和熔渣的过程。按熔炼条件可分为还原熔炼、造锍熔炼、吹氧熔炼等。
⑦精炼 进一步处理熔炼所得含有少量杂质的粗金属,以提高其纯度。如熔炼铁矿石得到生铁,再经氧化精炼成钢。
火法冶金过程所需能源,主要依靠燃料燃烧供给,也有依靠过程中的化学反应热来提供的。
(2)湿法冶金(水法冶金)它是在温度不高的条件下进行的,一般低于100℃,即使是在现代湿法冶金中的高温高压过程,温度也不过200~300℃。湿法冶金是金属矿物原料在酸性介质或碱性介质的水溶液进行化学处理或有机溶剂萃取、分离杂质、提取金属及其化合物的过程。整个过程包括浸出、分离、富集和提取等工序。
①浸出 浸出的实质是将原料中有用成分转入溶液,即用适当的溶剂处理矿石或精矿,使要提取的金属成为某种离子(阳离子或络阴离子)形态进入溶液,而脉石及其他杂质则不溶解,这样的过程叫浸出。浸出后经澄清和过滤,得到含金属(离子)的浸出液和由脉石矿物组成的不溶残渣(浸出渣)。对某些难浸出的矿石或精矿,在浸出前常常需要进行预备处理,使被提取的金属转变为易于浸出的某种化合物或盐类。例如,转变为可溶性的硫酸盐而进行的硫酸化焙烧等,都是常用的预备处理方法。
②分离 浸取溶液与残渣分离,同时将夹带于残渣中的冶金溶剂和金属离子洗涤回收。
③富集 浸取溶液的净化和富集,常采用离子交换和溶剂萃取技术或其他化学沉淀方法。
④提取 从净化液提取金属或化合物。
(3)电冶金 利用电能提取和精炼金属的方法。按电能形式可分为两类。
①电热冶金 利用电能转变成热能,在高温下提炼金属,同火法冶金。
②电化学冶金 用电化学反应使金属从含金属的盐类的水溶液或熔体中析出。前者称为溶液电解,如铜的电解精炼,可归入湿法冶金;后者称为熔盐电解,如电解铝。
从矿石或精矿中提取金属的生产工艺流程,常常是既有火法过程又有湿法过程,即使是以火法为主的工艺流程,如硫化镍精矿的火法冶炼,最后还须要有湿法的电解精炼过程;而在湿法炼锌中,硫化锌精矿还需要用高温氧化焙烧对原料进行炼前处理。
由于镍矿石之红土镍矿无法利用传统的方法选矿,即使硫化镍矿可以选矿,但精矿品位也较低,因此镍矿具有入炉矿品位低、成分复杂、伴生脉石多、难容等特点,导致镍的冶炼技术、生产方法比较复杂。此外,由于产品销售形态、能源、交通运输和经济发展差异原因也导致镍的冶炼方法多样化。
根据矿石的种类、品位和用户要求的不同,可生产多种不同形态的产品,如纯镍类包括电解镍、镍丸、镍块、镍锭和镍粉等;非纯镍类包括烧结氧化镍、镍铁等。镍的生产方法如图1-4所示,采取哪种方法提取镍,在很大程度上取决于所用的原料以及要求的产品。

图1-4 镍的主要生产方法
这些冶炼方法中,火法造锍熔炼历来是最主要的生产方法,现在利用红土镍矿火法冶炼镍铁又成为新一代的重要方法。硫化镍矿造锍熔炼的工艺有反射炉、鼓风炉、电炉、闪速炉以及氧气顶吹熔炼、熔池熔炼等。其中闪速炉在降低能耗、提高硫实收率、防止污染等方面有优势。红土镍矿火法冶炼镍铁的工艺有鼓风炉、高炉、矿热炉和回转窑粒铁法。其中矿热炉熔炼,从原料性质、能源消耗和产品销售形式等方面看具有领先地位。
1.3.1 火法冶炼
镍的火法冶炼原理根据使用镍矿的不同而异。使用硫化镍矿造锍熔炼是利用铜、镍、钴对硫的亲和力近似于铁,而对氧的亲和力远小于铁的性质,在氧化程度不同的造锍熔炼过程中,分阶段使铁的硫化物不断氧化成氧化物,随后与脉石造渣而除去。主金属经过这些工序进入锍相得到富集,品位逐渐提高。造锍熔炼过程中是一个氧化过程;而使用红土镍矿(氧化镍矿)冶炼镍铁是利用镍(钴)对氧的亲和力远小于铁等元素的性质,利用还原剂进行有选择性的还原冶炼。镍、铁等元素被还原进入金属熔体相,脉石、熔剂和未被完全还原的铁氧化物等进入渣相。镍铁冶炼是一个还原过程(参见3.1氧化还原的基本规律)。
1.3.1.1 硫化镍矿的火法冶炼
硫化镍矿的火法冶炼主要包括造锍熔炼(如电炉熔炼)、低镍锍的吹炼(如转炉吹炼)、高镍锍的分离(如缓冷-磨浮)以及电解精炼等过程(图1-5)。造锍熔炼的工艺和设备类似于铜熔炼,但不同之处是,吹炼(普通转炉以空气吹炼)不能得到粗镍金属而只能得到高镍锍。但据报道:加拿大铜崖镍精炼厂在氧气顶吹转炉的条件下,开创了高温吹炼高锍得金属镍的先例。

图1-5 硫化镍矿的火法冶炼流程图
(1)造锍熔炼 造锍熔炼是铜、镍、钴火法冶金流程的一个重要工序,以制得一种称为锍的主金属硫化物和铁的硫化物共熔体而得名。从选矿厂送来的硫化镍精矿主要成分为镍、铜、钴、铁的硫化物和SiO2、MgO、CaO、Al2O3等,此外还有金、银、铂、钯和其他钯族金属,这种硫化精矿一般含镍和铜5%~15%。由于硫化精矿的主金属含量还不够高,除脉石外,伴生有大量铁的硫化物,其量超过主金属,用火法由精矿直接炼出粗金属,在技术上仍存在一定困难,因此需要造锍熔炼,分离除去铁的硫化物和SiO2、MgO、CaO、Al2O3等杂质,使镍、铜、钴等和贵金属得到富集。硫化镍精矿的造锍与硫化铜精矿一样属于氧化熔炼。
红土镍矿也可在有硫化剂存在的条件下进行造锍熔炼,将镍富集于镍锍中。但是需要配入硫化剂,先制团或烧结成块,然后加入鼓风炉中熔炼,焦炭配入率达20%~30%,属于还原性,所以又称为还原硫化熔炼。
①造锍熔炼的基本原理 硫化镍精矿的火法冶金过程实质上,铁和硫是通过熔炼过程选择性氧化和造渣除去的。铜、镍对硫的亲和力与铁相近,但铁对氧的亲和力大于铜和镍,更易氧化为FeO,如果没有足够的SiO2熔剂与其造渣,FeO将继续氧化成Fe3O4,但Fe3O4在高温下易被C还原为FeO。在相对低的温度(1200~1300℃)下,使Cu2S氧化可得到金属铜,同样的过程对于镍则需要1600℃以上的高温。对炼镍而言,造锍熔炼和吹炼的产物是一种低铁(0.5%~3%)、含硫(10%~22%)的转炉镍锍而不是粗镍。
②造锍熔炼过程的主要物理化学反应 进行造锍熔炼时,炉料有铜镍硫化矿和熔剂等,如镍黄铁矿(Ni,Fe)9S8、含镍磁黄铁(Ni,Fe)7S8、辉铁镍矿3NiS·FeS2以及与硫化镍矿伴生的磁黄铁矿Fe7S8、黄铜矿CuFeS2、黄铁矿FeS2以及Fe2O3、SiO2、MgO、CaO、Al2O3等脉石氧化物。这些物料经过在尚未与氧充分接触时高价硫化物分解[如辉铁镍矿3NiS·FeS2=Ni3S2+3FeS+1/2S2(气)]、硫化物的氧化(如Ni3S2+7/2O2=3NiO+2SO2)和造渣反应(如氧化反应生成的FeO在SiO2存在的条件下形成炉渣,2FeO+SiO2=2FeO·SiO2),最终形成互不相容的镍锍或铜镍锍和炉渣。
③造锍熔炼工艺技术 造锍熔炼可在反射炉、鼓风炉、电炉、闪速炉中实现。其中反射炉、鼓风炉、电炉熔炼统称为传统熔炼方法,而闪速炉熔炼是新的熔炼方法。下面对电炉熔炼、闪速炉熔炼做一介绍。
a.电炉熔炼 电炉(矿热炉)是一种用电加热的膛式炉,有一个高温熔池。精矿或焙砂从炉顶加入炉内熔化成液体镍锍和液体熔渣。电极从炉顶插入渣层内,熔炼所需的热量是由通过电极之间的渣层的电流转化而成的。电流通过的路线有两种:一种由电极通过炉渣流向镍锍;一种由一根电极通过炉渣流向另一根电极。这两种负荷的比例取决于电极插入的深度。有效放热区占整个熔池的30%~40%。炉内不产生热量的部位,由于熔池内部的热交换作用(主要是炉渣的对流运动),也可获得热量。镍锍和炉渣从炉子的铁口、渣口间歇地放出,烟气从炉顶的一端排除。
电炉炉料必须是干精矿或焙砂,不能装湿精矿,因为湿精矿所含的水分在炉内蒸发会引起炉料喷出。
电炉熔炼的优点是热源来自于电,可以有效地控制熔池温度,可以使炉渣过热,所以对炉料的适应性强,适合熔炼含氧化镁高的难熔精矿,同时,由于炉渣可以过热,导致炉渣和镍锍分离的比较好,金属回收率比较高;由于电炉不需要燃料燃烧获得热量,因而烟气量少。不足是耗电量比较高;脱硫量比较低。
在电炉里,当物料加热到1000℃时,复杂硫化物、硫酸盐、碳酸盐和氢氧化物产生热分解反应:
Me(SO4)=MeO+SO3
MeCO3=MeO+CO2
Me(OH)2=MeO+H2O
当物料加热到1000℃以上时,物料中各种化合物之间开始产生交换反应:
Cu2O+FeS=Cu2S+FeO
CoO+FeS=CoS+FeO
2Cu2O+Cu2S=6Cu+SO2
2Cu+FeS=Cu2S+Fe
CuO·Fe2O3+(Cu2S+FeS)=3Cu+Fe3O4+S2
上述反应生成的各种硫化物互相溶解生成电炉熔炼的主要产物——低镍锍。在低镍锍中还溶解有贵金属和一部分磁性氧化铁。
氧化铁和其他碱性氧化物(CaO、MgO)与SiO2反应生成各种硅酸盐mMeO·nSiO2,成为电炉炉渣。
造渣反应
10Fe2O3+FeS=7Fe3O4+SO2
3Fe3O4+FeS+5SiO2=5(FeO)2·SiO2+SO2
2FeO+SiO2=(FeO)2·SiO2
CaO+SiO2=CaO·SiO2
MgO+SiO2=MgO·SiO2
(FeO)2·SiO2、CaO·SiO2、MgO·SiO2以及Fe3O4互相溶解成为炉渣。
当电炉炉料中加入还原剂时,大量的金属铁被还原,生成以铁为主的金属合金,金属合金溶解在低镍锍中形成金属化低镍锍。当金属化低镍锍与渣中铜、镍、钴的氧化物相遇时,则渣中铜、镍、钴被铁还原,还原后的金属溶解在低镍锍中,再与FeS转变成硫化物,故使渣中的有价金属量可以进一步降低,从而提高了金属回收率。
b.闪速炉熔炼 闪速炉熔炼法最初用于熔炼铜精矿,是由芬兰奥托昆普公司哈贾法尔塔冶炼公司于1959年应用于熔炼硫化镍精矿的。
硫化镍精矿的造锍熔炼一般分为三个过程:焙烧、熔炼、吹炼。焙烧和吹炼过程实质上都是硫化铁的氧化过程,它是一种放热反应,产生大量的热能,除供给过程本身消耗的热能外,往往还有过剩热;而熔炼过程则往往是一个消耗大量热能的过程。闪速熔炼则是将硫化物的焙烧、熔炼和部分吹炼合在一个冶金炉内完成,利用焙烧和吹炼时硫化物氧化产生的热供给熔炼所需要的大部分热能,不足的热量可靠补充部分燃料供给。可见,闪速熔炼的能耗低。
闪速炉熔炼是将磨细的粉状干精矿与预热空气(或富氧空气)一起吹入一个高温炉膛内成为一种均匀的悬浮体。精矿颗粒被其周围的氧化性气体迅速氧化并加热熔化,这个过程在0.3s内完成。因此闪速熔炼是一个强化的冶金过程,生产能力大。
奥托昆普的闪速熔炼生产过程:其闪速炉由反应塔(相当一个竖炉)、沉淀池和上升烟道三部分组成,如图1-6所示。经充分干燥的粉状炉料(含水<0.3%)和预热空气(或富氧空气)按一定的比例加到精矿喷嘴中,混合后喷入炉内。炉料从精矿喷嘴进入反应塔后,呈悬浮体向下运动,迅速被加热燃烧,发生剧烈氧化反应,颗粒温度上升到熔融温度。熔融颗粒和反应气体进入水平的沉淀池得到分离。炉气通过沉淀池上空进入上升烟道排除炉外,经冷却、收尘后送入硫酸厂制酸。熔融产物在沉淀池与气体分离后落到熔池内,完成造锍和造渣反应并进行分离。生成的镍锍液滴通过炉渣层沉降而形成镍锍层。镍锍品位可以通过调节空气和精矿比例来控制。镍锍从沉淀池放出送往转炉吹炼。炉渣一般采用电炉贫化处理。

图1-6 闪速炉示意
闪速熔炼反应过程分为两段进行:第一段为精矿-空气悬浮体的氧化熔化过程。氧化首先生成硫酸盐,温度升高时硫酸盐再分解为氧化物。反应产物为悬浮熔融硫化物相,以及由固体磁性氧化铁、浮氏体和炉渣氧化物构成的一种悬浮氧化物相;第二段为沉淀池的镍锍和炉渣生成过程。当大部分反应悬浮体落到熔体表面时,镍锍和炉渣开始互相分离。悬浮体中的硫化物通过熔体与沉淀池底部已有的镍锍相汇合。在反应塔产物中硫化物过渡到镍锍相,硫化铁量大大下降,这部分硫化铁主要用于把氧化时产生的三价铁还原成二价铁,并且使镍、钴、铜的氧化物还原或硫化,最后在镍锍层表面上产生有价金属和三价铁含量低的炉渣。
闪速熔炼的化学反应和产物基本和传统熔炼流程是相同的。但是闪速熔炼有它特殊的机理,使产出的镍锍一般比电炉熔炼产出的镍锍所含镍和铜要高,而含硫低。
(2)低镍锍的吹炼 通过造锍熔炼获得低镍锍,其主要由Ni3S2、Cu2S和FeS组成,此外还有少量的CoS和一些游离贵金属及合金。低镍锍的密度取决于其成分,FeS密度为4.6g/cm3,Ni3S2密度为5.3g/cm3,Cu2S密度为5.7g/cm3。低镍锍越贫,其密度越小,一般密度为4.6~5g/cm3。低镍锍与炉渣的密度差越大,分离越完全。由于精矿的化学成分及熔炼方式(反射炉、鼓风炉、电炉、闪速炉和各种熔池熔炼炉)、操作条件的不同,低镍锍的化学成分多数波动在以下范围:Ni10%~25%、Cu4%~12%、Fe45%~50%、S24%~28%。因其成分不能满足精炼工序的处理要求,故必须对低镍锍进一步处理,处理过程通常在卧式转炉中进行。卧式转炉具有较低的液面静压力,因此鼓风压力低,一般为50~120kPa,对鼓风机的选择及能耗均有利。通过转炉侧面的一排风口向转炉送风。卧式转炉的直径一般为2~4m、长度3~10m。风口数量因炉子的大小而异,通常15~48个,风口直径通常40~60mm。
在转炉吹炼的条件下(鼓入空气、加入适量熔剂——石英),熔融低镍锍与吹入空气中的氧反应,可除去大部分铁和一部分硫,产出高镍锍和转炉渣,由于它们各自的密度不同而进行分层,密度小的转炉渣浮于上层被排出,高镍锍中的Ni、Cu大部分仍然以金属硫化物状态存在,少部分以合金状态存在,低镍锍中的贵金属和部分钴也进入高镍锍中。转炉吹炼是一个自热过程,通过铁、硫及其他杂质的氧化放热和造渣反应放热来提供所需的全部热量。高镍锍的成分一般为Ni40%~45%、Cu20%~30%、Fe2%~4%、S18%~24%、Co0.5%~0.8%。
①低镍锍的吹炼原理 其实质是金属硫化物的氧化反应。由于铁对氧的亲和力最大,依次为铁、钴、镍、铜,即铁最易被氧化。而铁、钴、镍、铜对硫的亲和力较对氧的亲和力正好相反,铜对硫的亲和力最大,依次为铜、镍、钴、铁,因此,在低镍锍吹炼过程中铁最易被氧化造渣除去,若继续吹氧接下来便是钴、镍、铜相继被依次氧化造渣。由于钴含量很少,又不能使镍被氧化,这样就必须控制在铁还没完全氧化造渣之前停止吹炼,以免镍被氧化造渣损失。由于铜硫化物比镍硫化物更稳定而不易被氧化,在转炉鼓风吹炼的条件下绝大部分Cu2S被保留在镍高锍中。
②在低镍锍吹炼过程中主要元素的行为
a.铁的氧化造渣反应 鼓入空气、加入适量熔剂——石英(85%SiO2):
FeO+SiO2=2FeO·SiO2
b.镍的富集 在吹炼后期,锍中含铁量降低一定程度时或在风口附近,Ni3S2被氧化入渣,但由于吹炼工艺控制炉内熔体中有适量FeS存在,生成的氧化镍又被硫化,镍入渣量很少,仍以Ni3S2形态存在于镍高锍中:
c.铜的富集 在吹炼过程中,虽然铜不易被氧化,但也有少部分的Cu2S被氧化为Cu2O,Cu2O进而与未氧化的Cu2S反应生成少量的金属Cu,Cu又还原镍锍中的Ni3S2,得到金属Ni进入高镍锍:
Cu2S+2Cu2O=6Cu+SO2
4Cu+Ni3S2=3Ni+2Cu2S
d.钴的富集于去除 在镍锍和渣中的分配主要取决于镍锍中铁的含量,若铁含量低,FeS大量氧化造渣以后,则CoS开始氧化入渣。当镍锍含铁量在15%左右时,钴在镍锍中的含量最高,此时钴得到最大程度的富集。
e.硫的去除 在低镍锍中,硫与金属结合以化合物的形态存在。在对低镍锍吹炼的过程中,在吹入的空气对金属氧化的同时,硫也被氧化生成二氧化硫气体随烟气排出。但高镍锍中的含硫量不应太低,因为这不仅会延长吹炼时间、增加了有价金属在渣中的损失,同时使高镍锍中合金含量增加,给以后的高镍锍处理工序带来麻烦。
f.金、银、铂族金属抗氧化性能较强 在吹炼过程中大部分入锍。
(3)高镍锍的分离 转炉吹炼产出的高镍锍主要是镍和铜的硫化物,并含有少量的铁、钴和氧以及极少量的贵金属、硒、碲等元素,其中含铁量已降至1%~3%。因此,高镍锍的铜镍分离和精炼是硫化镍矿冶炼的生产关键。通常采用分层熔炼法和磨浮分离法处理高镍锍,前者现在已经不用了。
①分层熔炼法的理论依据 将高镍锍和硫化钠混合熔化,在熔融状态下,硫化铜极易溶解于硫化钠中,而硫化镍不易溶解于硫化钠中。硫化镍和硫化铜的密度为5.7g/cm3,而硫化钠的密度仅为1.9g/cm3。当高镍硫和硫化钠混合熔化时,硫化铜大部分进入硫化钠相,因其密度小浮在顶层,而硫化镍因其密度大留在底层。当温度下降达到凝固温度时,二者分离得更彻底,凝固后的顶层和底层很容易分开。
②磨浮分离法的理论依据 当熔融的高镍锍缓慢冷却时,其中的硫化镍和硫化铜生成粗颗粒的结晶体,二者以其化学成分进行离析。其结晶颗粒的大小,决定于凝固时的冷却速度。高镍锍由硫化镍、硫化铜和铜镍合金三种晶体组成,缓冷的高镍锍结晶颗粒较粗。当缓冷的高镍锍破碎并磨成矿浆在强碱性的介质中进行浮选时,大部分硫化铜被泡沫浮起,硫化镍则进入尾矿,分别产出两种精矿,而铜镍合金可以用磁选的方法分出,贵金属基本富集在铜镍合金中。
(4)电解精炼 高镍锍通过磨浮分离后得到高镍精矿(硫化镍),一般含硫20%~25%,含镍65%~75%。但还需要进一步精炼,目的是为了得到电镍及其他商品镍产品,主要方法包括硫化镍阳极电解和粗镍电解精炼。
①硫化镍阳极电解精炼 将高镍精矿熔铸成阳极进行电解。电解时,阳极上发生氧化反应,而阴极上得到电子发生还原反应析出金属镍,其主要反应为
阳极: Ni3S2=3Ni2++2S0+6e-
阴极: Ni2++2e-=Ni
②粗镍电解精炼 首先将高镍精矿焙烧得到氧化镍,然后再在电炉内用焦炭还原熔炼成粗镍阳极(或镍产品),再通过电解精炼得到金属镍。
NiO+CO=Ni+CO2
硫化镍阳极电解和粗镍电解精炼两种工艺的共同特点是溶液需要深度净化;采用隔膜电解;电解液为弱酸性。
电解产物:纯镍、阳极泥(提取贵金属)、电解液渣(提钴、提铜)。
1.3.1.2 红土镍矿的火法冶炼
火法冶炼处理红土镍矿有两类方法:一类是还原硫化熔炼产出含铁的镍锍;另一类是还原熔炼产出镍铁。前者一般在鼓风炉中进行,也可用电炉熔炼。后者主要在电炉中进行,也可以在鼓风炉、高炉和回转窑中进行。
红土镍矿一般含水较高,熔炼前需脱水干燥,有时还需要制团或烧结。主要的生产方法有高炉法、鼓风炉法、矿热炉法和回转窑粒铁法等。其中镍铁熔炼的高炉法、鼓风炉法基本与黑色冶炼生产炼铁法一样,矿热炉法即与黑色冶炼生产铁合金生产相近又与有色冶炼相似;造锍熔炼,鼓风炉法、矿热炉法是有色冶炼的方法。本书主要讲述的就是利用红土镍矿基于火法的冶炼。
(1)鼓风炉法 鼓风炉法是最早用于红土镍矿炼镍的方法。鼓风炉主要用来还原硫化熔炼生产镍锍和还原熔炼生产镍铁。
①生产镍锍 还原硫化造锍熔炼是指将矿石中的镍、钴和部分铁还原出来使之硫化,形成金属硫化物的共熔体与炉渣分离。红土镍矿的鼓风炉还原硫化造锍熔炼和镍硫化矿的造锍熔炼有其本质的不同:后者,矿石中的矿物(如镍黄铁矿、黄铜矿和磁黄铁矿)本身即是硫的来源,而前者却需要另外配入含硫的物料(如黄铁矿、石膏等)。鼓风炉是竖炉的一种,通常使用石膏作硫化剂,当从鼓风炉上部加入的物料(由矿石、焦炭、石膏及石灰石组成)在炉中下降时,与上升的由风口鼓入炉内的空气与焦炭燃烧产生的热还原气体形成对流,从而实现炉料的预热、还原焙烧、熔化和造锍过程。鼓风炉产出的低镍锍用转炉吹炼成高镍锍,这种高镍硫与硫化矿冶炼产出的高镍锍略有不同,它不含铜或者是含铜很少,可经焙烧直接产出氧化亚镍,再用电炉还原成金属。或还需要铸成阳极进行电解精炼。
②生产镍铁 鼓风炉还原硫化熔炼红土镍矿的方法长期以来是最受欢迎的方法。以后随着合金钢,特别是不锈钢产量的日益增长,为满足其对镍和铁的需要,促使将这种矿石炼成镍铁来直接使用,而不需要再进一步地将镍与铁分开,更不需要将镍铁硫化造锍。镍铁已成为商品镍的一种重要形式。
鼓风炉熔炼镍铁的流程简单,只是一个还原过程,而不需要加入硫化剂造锍,产出粗镍铁,再进一步精炼产出商品镍铁。
(2)高炉法 高炉也是一种竖炉,用高炉冶炼红土镍矿产出镍铁原理与其炼铁相同,只是有红土镍矿综合品位(含Ni+Fe品位)低、烧结矿强度低、透气性不好、焦比高、渣量大、渣碱度低等不同点。如红土镍矿烧结矿强度较铁矿低,导致炉料空隙度(ε)、炉料空隙当量直径(d∂)减小,使得炉料对煤气的阻力(ΔP)增加,透气性不好。通过物料(矿石、石灰、燃料、还原剂配比混合)烧结成烧结矿,将烧结矿、焦炭、熔剂从炉顶按规定批次加入炉中,炉料不断在炉中下降,与上升的由风口鼓入炉内的热空气与焦炭燃烧产生的热还原气体形成对流,从而实现炉料的干燥、预热、脱水、间接还原、直接还原、熔化和渣-镍铁分离过程。
由于高炉法是剩碳操作,不能控制氧化铁的还原量,使铁几乎全部进入镍铁中,因此镍铁品位除与矿中的镍含量有关外,主要取决于矿的含铁量,所以高品位的镍铁对矿的成分要求是高镍、低铁。有工业价值的红土镍矿的镍含量为1%~3%,与其对应的铁含量是49%~10%,由于高品位镍铁要求矿镍高铁低,进而使得镍矿的综合品位较低,造成炉渣量大、烧结矿强度低,使得综合品位低的红土镍矿在大高炉上几乎不能顺行,必须使用中小高炉(≤450m3)。这就是高炉生产镍铁的品位越高,反而使用的高炉容积越小的原因。
高炉容积的选择原则:在利用红土镍矿火法冶炼镍铁的鼓风炉法、高炉法、矿热炉法和直接还原粒铁法四种方法中,鼓风炉法、高炉法(小高炉)在含镍高的镍铁(Ni≥10%)生产工艺中逐渐被矿热炉法所取代,直接还原法还在发展完善中。由于含镍较低的镍铁(Ni2%~8%)在不锈钢的冶炼中作为母料(而不是作为合金剂)的出现,加之适合于矿热炉工艺矿石的短缺和昂贵,使得利用低品位红土镍矿高炉法冶炼低品位镍铁的工艺得以保存,且有较大的发展空间。高炉和矿热炉生产镍铁的主要区别在于:前者使用焦炭作为还原剂、料架和热源,是富碳操作,不能对铁进行有选择性的还原(铁几乎被全部还原),同时,S、P等杂质加入合金较多;后者使用电作热源,用煤作还原剂,可采用缺碳操作,对铁进行有选择性的还原,同时,S、P等杂质加入合金较少。
镍铁品位取决于原矿的镍铁比、冶炼所采用的工艺以及镍的回收率。镍铁比高,则镍铁品位高;利用选择性还原工艺,则镍铁品位高;镍的回收率低,则镍铁品位高。
可见,在使用同样的原矿时,矿热炉工艺比高炉工艺镍铁品位高,但经济适合矿热炉的原矿资源少;由于红土镍矿金属品位低(含Ni+Fe量低),烧结矿强度也低,同时渣量也较大,造成炉缸温度低,导致高炉不易顺行。所以,尽管使用中小高炉,则较低炉身高炉比高炉身高炉冶炼镍铁品位高。适合高炉冶炼原矿资源多且便宜。但高炉越小,燃料比会越高,操作成本会增高,镍铁成分波动大、铁水温度偏低、每炉铁水量少,使得与下步炼钢不易匹配。
选择高炉冶炼红土镍矿高炉容积的原则是:视红土矿金属品位和镍铁比确定镍铁品位,在满足冶炼工艺的前提下,在使用小高炉的前提下尽可能选大的。
在表1-10中,根据红土矿镍铁比、金属量及冶炼成相应的镍铁品位,给出了高炉容积选择意见,仅作参考。选择意见相对分为五级:最好、好、一般、不好、最不好。
表1-10 高炉炉型选择建议

(3)矿热炉法 红土镍矿之硅酸镍矿的特点是熔点高,矿热炉的特点是能容易地达到熔炼所要求的高温。
①熔炼镍铁 电炉熔炼镍铁一般需要增加炉料预热和预还原的过程。炉料预热时同时进行干燥脱水,旨在降低电能消耗,将炉料熔化时翻料事故降到最低限度。例如,利用回转窑还原焙烧工艺对红土镍矿进行预热和预还原,所获得的高温预还原焙砂直接热装入矿热炉熔炼,该工艺称为回转窑-矿热炉工艺,即RKEF工艺。炉料的预热和预还原是在固态下进行的,温度在538~980℃之间,窑内呈还原气氛。预还原程度取决于反应时间、温度和气体的还原强度。
由于矿热炉炉料含碳量低,炉料内的镍钴氧化物是在回转窑预还原阶段生成的金属铁还原的。
进入矿热炉的焙砂在熔化的过程中进行还原反应,几乎所有的镍和钴的氧化物都被还原成金属(被金属铁),金属铁被氧化。如果炉料中的金属铁量超过反应的需要,则多的铁将进入镍铁合金中。所以镍铁合金中镍和钴的含量取决于炉料中的NiO、CoO与Fe之比。氧化铁还原成金属的量由加入的还原剂量确定。为了控制镍铁品位,则必须严格控制铁的还原量,通常并不把氧化铁完全还原成金属铁,而是将其一部分还原成氧化亚铁并进入炉渣(氧化铁的还原次序是Fe2O3→Fe3O4→FeO→Fe),因为将过多的铁还原成金属,会降低镍铁的品位。同时,增加炉渣中的氧化亚铁的含量可降低炉渣的熔点,降低操作温度,还可提高炉渣的导电性。氧化亚铁的含量还决定渣的氧势,从而决定镍铁中碳、硅、铬、磷等杂质的含量。
但是,随着镍铁品位的提高,即氧化铁不完全还原成金属Fe的量越大,镍的还原率越低,导致镍的回收率降低。
随着进入矿热炉的固态物料温度逐渐提高,物料与其他造渣物料一起生成镍铁钴的合金和含硅酸铁的炉渣。
还原熔炼产出的粗镍铁需经过进一步的精炼去除碳、硫、磷、硅等杂质。脱硫是在还原条件下进行,而脱硅、脱碳、脱磷则是在氧化条件下完成。因此,精炼作业是通过还原和氧化两个阶段完成。
②熔炼镍锍 危地马拉某厂的生产流程:红土镍矿石经干燥窑干燥至含水18%~20%后用回转窑(ϕ5.5m×100m)进行选择性还原,并在窑尾喷入熔融硫黄使金属镍和铁硫化(还原硫化段温度900℃),然后加入电炉(ϕ18m三根电极、功率45MW)熔化产出低镍锍,再用转炉(7.6×4m卧式转炉)吹炼产出高镍锍。选择电炉生产镍锍而不生产镍铁是为了使用当地含硫的燃料。该厂红土镍矿成分、电炉产出低镍锍成分、电炉渣成分及转炉产出的高镍锍成分见表1-11。
表1-11 危地马拉某厂镍锍成分

(4)回转窑粒铁法 该法是指采取直接还原炼粒铁的方法,即克虏伯-雷恩(Krupp-Renn)法冶炼镍铁合金。回转窑粒铁法就是使炉料在回转窑中经过预热和还原后,再进一步提高温度(>1200℃)进入粒铁带,金属铁与炉渣开始软化,在半熔化状态下金属铁由小颗粒堆集成卵状粒铁,炉料出炉后经水淬冷却后很容易用磁选把粒铁与脉石分开。
回转窑粒铁法冶炼红土镍矿就是利用回转窑将红土镍矿中的镍铁还原,再经破碎-重选-磁选冶炼镍铁。该法始于用低质煤作燃料和还原剂,在回转窑内将低品位高硅铁矿石还原,实现渣铁分离,铁聚合成细颗粒被夹裹在半液态的黏稠渣中,经水淬、破碎、磁选分离出铁粒。
典型的例子是日本冶金工业公司大江山冶炼厂,其采用回转窑高温还原焙烧产出粒铁,经跳汰、磁选富集产出镍铁合金。
1.3.2 湿法冶炼
直到20世纪40年代,火法冶炼仍然是处理镍矿的唯一方法。因为湿法冶金能更好地综合利用资源,保护环境,现代湿法冶金技术已成为从矿石中,特别是从红土镍矿中提取镍的一种重要手段。湿法冶金过程的最终工序是生产纯金属。这一工序可以用置换法(如利用铁屑置换铜、锌粉置换金等)或用电积法(如铜、锌等电积)来完成,也可以用气态还原剂(如SO2、CO、H2等)来进行。
1.3.2.1 高镍锍的湿法提取技术
现行高镍锍精炼工艺如图1-7所示。20世纪40年代以前,除英国克莱达奇镍精炼厂采用常压羰基法处理高镍锍生产高纯镍外,几乎其他镍厂都采用电解精炼法处理高镍锍生产电解镍,但该法流程比较烦琐。20世纪60年代后,国内外同步开展高镍锍的湿法提取技术研究,目前国外已经工业化的方法主要有三类:奥托昆普的硫酸选择性浸出电解提取法,鹰桥公司的氯化浸出电解提取法和舍里特·高尔顿的氨浸-氢还原法。下面将这三种方法的工艺作一介绍。

图1-7 现行高镍锍精炼工艺方法示意
(1)硫酸选择性浸出电解提取法 该法基本工艺为高镍锍经水淬、细磨,再采用常压和加压结合的方法进行分段浸出,镍、钴选择性被浸出进入溶液,铜、铁、贵金属则抑制于浸出渣中。浸出液经脱铅和除钴净化,经净化后的浸出液用电解沉积法或氢还原法产出金属镍。与镍电解精炼法相比,硫酸选择性浸出法的生产流程比较短,用一个浸出工序代替了高镍锍磨浮、焙烧、电炉还原熔炼等若干工序。镍电积回收率可达98%。
用于硫酸选择性浸出的高镍锍最好含硫较低,因为镍的溶解率主要取决于高镍锍的含硫量,镍的溶解率随含硫量的增高而降低,对于镍铜比小于2的高镍锍,在含硫量一定时,镍的溶解率随含铜量的增高而增大。这种高镍锍主要由铜镍合金、Ni3S2和Cu2S三相组成。镍主要存在于合金相和Ni3S2相中,铜存在于Cu2S和合金相中,铁和钴存在于合金相中。
硫酸选择性浸出由二段或三段常压浸出和一段加压浸出组成。在常压浸出时,金属相的镍基本上能全部溶解,而Ni3S2相中的镍最多只能溶解1/3,Cu2S相则不溶解。加压浸出工序的目的是使镍、钴达到尽可能高的浸出率,同时浸出部分的铜供常压浸出工序使用,而将高镍锍中大部分铜和贵金属抑制于浸出渣中,以实现选择性浸出。
浸出液富含镍、钴,几乎不含铜、铁等杂质,因而浸出液的净化作业只需要脱铅和除钴。采用碳酸钡(或氢氧化钡)脱铅,将碳酸钡与粉状高镍锍一起加入浸出系统中,生成硫酸钡和硫酸铅共结晶沉淀物,铅被脱除。除钴的氧化剂采用特制的镍的高价氢氧化物——黑镍(NiOOH),用其氧化溶液中的二价钴离子,使之呈三价氢氧化钴(CoOOH)沉淀出来。镍钴分离后,硫酸镍溶液用电解沉积法或氢还原法生产金属镍。
浸出渣中残存的镍大部分呈硫化镍状态,并有极少量的未浸出的NiO及含镍的碱式硫酸盐。渣中的铜基本是以Cu2S和CuS状态存在。
(2)氯化浸出电解提取法 氯化浸出是指在水溶液中进行的湿法氯化过程,即通过氯化使高镍锍中的镍、钴、铜等呈氯化物形态溶解的过程。由于氯和氯化物化学活性很高,生成的氯化物溶解度大,对杂质的络合能力又较强,因此,在常温、常压下,氯化浸出就能达到在其他介质中必须加温、加压下才能达到的技术指标。根据浸出剂的种类不同,高镍锍氯化浸出分盐酸浸出和氯气浸出两种。
①盐酸浸出法 盐酸是一种强酸,能够与多种金属、金属氧化物以及某些金属硫化物作用,生成可溶性的金属氯化物。因而盐酸浸出法具有以下特点。
a.盐酸浸出过程有一定的选择性。高镍锍中的FeS、Ni3S2、CoS能被盐酸选择浸出,而Cu2S、CuS和铂族金属则很难被浸出。
b.在浸出液中,除镍以外,大多数金属离子都能与Cl-络合成络阴离子,镍则不形成络阴离子。利用这一特性,可以用胺类熔剂萃取,分离镍与其他金属离子。
c.浸出液中氯化镍的溶解度随盐酸浓度的增加而减低,因此,可利用提高盐酸浓度的方法,如向浸出液中鼓入氯化氢,不用中和即可沉淀出氯化镍。
②氯气浸出法 在酸性水溶液中通入氯气,使物料氯化溶出的过程称为氯气浸出。氯气是一种强氧化剂,其氧化-还原电位很高。氯在水溶液中还会水解生成盐酸和次氯酸,次氯酸有比氯更正的氧化-还原电位。因此,用氯气浸出高镍锍时,高镍锍中的镍、钴、铜等贱金属和金、银、铂、钯等贵金属都会氯化进入溶液。在炼镍的工业生产中仅需要镍、钴氯化进入溶液,而要求铜及贵金属留在浸出渣中。由于高镍锍中的镍、钴等贱金属的氧化-还原电位较负,而铜及贵金属的氧化-还原电位较正,因而利用两者电位的差异,选择适宜的电位进行浸出,可以达到选择性浸出的目的。
在氯气浸出的过程中,溶液的氧化-还原电位随氯气的通入而升高,并随高镍锍的加入而下降。因此,只要控制溶液的通氯速度和高镍锍的加入速度,就可以把溶液的氧化-还原电位控制在适宜的范围内。
氯气浸出精炼工艺:在110℃下,通氯气选择性浸出镍,浸出液经置换脱铜,溶剂萃取分离镍钴,分别电积阴极镍和阴极钴,在阳极上产生的氯气返回浸出。原料中的铜和硫几乎全部以CuS形态留在浸出渣中。
(3)氨浸-氢还原法 该法原理同用加压氨浸法处理硫化精矿相同,参见1.3.2.2一节。其主要生产工艺流程包括:加压氨浸、蒸氨除铜、氧化水解、液相氢还原制取镍粉和镍粉压块等工序。其过程是将粉状高镍锍置于加压釜内,通入空气和氨,镍、铜、钴等有价金属在加压条件下溶解。铁和其他杂质则留在浸出渣中被废弃。从浸出液中除铜采用一种称为“蒸氨除铜”的过程,当溶液中蒸出部分氨之后,铜呈硫化铜沉淀。为了避免不饱和硫在氢还原制取镍粉时分解,使镍粉含硫增高,脱铜后液用氧化水解法将不饱和硫氧化成硫酸盐。氧化水解后的溶液用氢气在加压条件下将镍还原成镍粉。还原后的尾液通入硫化氢沉淀出残留的镍和钴。不含金属的尾液用真空蒸发结晶法回收硫酸铵。
1.3.2.2 硫化镍矿的湿法提取技术
目前工业上应用的硫化镍矿的湿法冶金方法主要有高压氨浸法、硫酸化焙烧浸出法、氧化焙烧还原氨浸法和氧压浸出法四种。
(1)高压氨浸法 其主要生产工艺流程包括:加压氨浸、蒸氨除铜、氧化水解、加压液相氢还原制取镍粉和镍粉压块等工序。该法只适宜处理不含贵金属的镍精矿。
①加压氨浸 氨浸的目的是使硫化镍精矿中的镍、钴、铜能最大限度地溶入氨溶液中。在一定的压力和温度条件下,当有氧存在时,镍精矿中的金属硫化物与溶解的氧、氨和水起反应,镍、钴、铜等生成可溶性的氨络合物[如镍的六氨络合物Ni(NH3)6SO4]进入溶液。由于铁的络合物很不稳定,转变为不溶的三氧化二铁留于浸出渣中。金属硫化物中的硫经过一系列的反应最终氧化成硫酸盐和氨基磺酸盐[(NH4)SO3NH2]。
加压氨浸法通常采用两段逆流操作。第一段称为“调节”浸出,要求产出的浸出液中含有一定数量的未饱和硫氧离子((、
、
),以满足下一工序脱铜的需要。第一段浸出的矿浆经浓密、过滤后,滤饼用新的氨溶液浆化,送入加压釜中进行第二段浸出(又称“最终浸出”)。通常加压氨浸的技术条件见表1-12。
表1-12 通常加压氨浸的技术条件

②蒸氨除铜 浸出液中含有镍、铜、钴的氨络合物,游离氨以及、
、
、
等离子。在其后的镍氨还原工序,则要求降低游离氨含量。因此,大部分游离氨必须在除铜过程中用蒸馏法除去。这是蒸氨除铜工序的“蒸氨”过程。由于铜为正电位的金属,溶液中若有铜,在其后液相氢还原制取镍粉的条件下,铜会与镍粉一起被还原出来,污染了镍粉,因此,必须在氢还原之前除去铜。随着蒸氨过程的进行,游离氨逐渐减少,铜离子与未饱和的硫氧离子发生反应,生成硫化物沉淀。这是蒸氨除铜工序中的“除铜”过程。除铜过程生成的产物是CuS、Cu2S的混合物。除铜后液含有一定量的Cu(如0.1~0.3g/L),若进一步送液相氢还原制取镍粉,需要液相含铜量低于0.005g/L。因此,再需要采用硫化氢深度除铜,但硫化氢除铜选择性较差,铜渣内会含有相当数量的镍和钴,需要返回浸出车间处理。
③氧化水解 氧化水解是指氧化和水解两个化学反应。其目的是把溶液中的未饱和硫氧离子和氨基磺酸盐转变成硫酸盐。因为未饱和的硫氧离子和氨基磺酸盐在液相氢还原制取镍粉的条件下会发生分解,使镍粉含硫升高。因此,蒸氨除铜后的溶液送往氢还原之前,必须将硫代硫酸根和连多硫酸根氧化成稳定的硫酸根离子,而使氨基磺酸根水解成硫酸根离子。
氧化水解过程是在加压釜内进行的,其结构于浸出加压釜相似。氧化水解的主要技术条件是温度250℃,压力4.1MPa,溶液在釜内停留时间约20min。其反应如下:未饱和硫氧离子很容易氧化成硫酸根离子
氨基磺酸盐水解
(NH4)SO3NH2+H2O=(NH4)2SO4
④加压液相氢还原 镍的液相氢还原是一个气、液、固多相反应,通常采用硫酸亚铁(FeSO4)作晶种来提供初始固相表面。硫酸亚铁在氨溶液中能生成分散的Fe(OH)2固体微粒,氢还原过程即以此为核心,镍离子吸附在Fe(OH)2表面,再被还原成金属粉。
镍粉长大是在晶种制取之后进行的。排除晶种尾液之后,再往还原釜内注入料液,通入氢气,料液与氢气在晶种表面发生反应,镍在晶核上沉积,镍粉颗粒增大。还原完成后,澄清适当时间,排除尾液,再开始下一循环,这样的过程称为“长大”。
⑤镍粉压块 镍粉可以直接销售,但用于生产不锈钢或合金时需要将镍粉压成块。为了保证压块的强度,还需要将压块进行烧结。此外,烧结还可以脱除大部分的硫和碳。
压块烧结工艺:将加压氢还原产出的镍粉干燥后加入0.5%胶黏剂,在对辊压块机上压成圆枕形块。压块烧结时(800℃以上)用氢气和少量的CO2脱硫(H2S↑)、脱碳(CO↑)。
镍块烧结前含S0.02%、C0.02%,烧结后分别为S0.003%~0.05%、C0.002%。
(2)硫酸化焙烧浸出法 用该法处理镍磁黄铁矿的过程是,将含镍磁黄铁矿精矿先在流态化焙烧炉内进行硫酸化焙烧,使精矿内含的镍、铜、钴等转变为水溶性硫酸盐。然后将焙砂进行浸出,再从浸出液中回收有价金属;浸出渣经烧结后可作为炼钢原料。
硫酸化流态化焙烧是在含氧的气氛、较低的焙烧温度下进行的。焙烧过程发生的反应:
MeS+3O2=2Me+2SO2
2SO2+O2=SO3
当焙烧温度低于金属硫酸盐的分解温度时,SO3就能与金属氧化物发生下列反应生成金属硫酸盐:
MeO+SO3=MeSO4
为了促进镍选择性硫酸化,在焙烧的过程中添加硫酸钠。焙砂的主要成分是硫酸镍、硫酸钴、硫酸铜、硫酸钠、氧化铁。
(3)氧化焙烧还原氨浸法 用该法处理镍磁黄铁矿的过程是,将精矿在流态化焙烧炉中氧化焙烧后,加入回转窑内进行选择性还原。还原后的焙砂用碳酸氨溶液进行逆流浸出,浸出液经蒸氨除铜处理后沉淀得出碳酸镍,最后经干燥、煅烧后得到高品位的氧化镍产品。铁渣制粒和烧结。
氧化焙烧与硫酸化焙烧不同,控制焙烧温度在760℃,要高于硫酸铁和其他金属硫酸盐的分解温度(670℃),要能将绝大部分磁黄铁矿死烧成赤铁矿。
焙烧炉产出的焙砂所含的镍绝大部分是铁酸盐,少部分与磁性氧化铁形成固溶体,极少量的镍呈硫化镍形态。还原作业的目的是把焙砂中的镍转变成金属镍,使其能在氨液中溶解。
(4)氧压浸出法 该法的过程是将精矿用富氧空气进行加压浸出,浸出渣为铁精矿,浸出液采用硫酸化沉淀法使镍、钴沉淀,用浮选法选出镍精矿送火法处理。
1.3.2.3 红土镍矿的湿法提取技术
对于含镍较高而含铜和钴低的红土镍矿,较多采用火法冶金还原熔炼生产镍铁或还原硫化造锍。火法冶炼红土镍矿适合处理品位较高的矿石,但能耗较大、钴不能回收等是其主要缺点。红土镍矿的湿法冶金工艺主要适宜处理低品位褐铁矿层及过渡层红土镍矿,这类矿石一般含MgO比较低。浸出是常用的湿法处理方法,目前红土镍矿的湿法提取工艺可归纳为湿法氨浸和湿法酸浸两种流程。氨浸和酸浸是两种完全不同的浸出方法,所用方法取决于矿石中碱性氧化物氧化镁含量的高低。氨浸法适用于含硅酸盐较多、氧化镁较高的矿石,而酸浸法适用于褐铁矿高、氧化镁低的矿石。
普遍采用的红土镍矿湿法冶金工艺主要有三种:即还原焙烧-氨浸工艺(RRAL)、加压酸浸工艺(HPAL)和硫酸常压浸出法(AL)。此外,湿法技术还包括盐酸常压浸出(ACPL)、硫酸化焙烧-浸出工艺(RAL)、硫酸加压-常压联合工艺(HPAL-AL)以及生物冶金工艺、微波浸出工艺、氯化离析工艺等。
红土镍矿湿法处理工艺的主要优点是金属回收率高,能够综合回收镍、钴、铁等有价金属,能耗低,能够处理低品位矿石等。
(1)还原焙烧-氨浸法(RRAL)还原焙烧-氨浸工艺又称Canon法,由Canon教授发明,并最早应用于古巴尼加罗冶炼厂。氨浸法是基于红土镍矿中的镍一般与铁结合成铁酸盐状态,经过还原焙烧使铁酸镍(NiFe2O4)转变成金属镍或镍铁合金,以便在氨液中溶解。其原则工艺流程为:将磨细后的矿石在多膛炉或回转窑内进行还原焙烧。经还原焙烧后,矿石中的镍、钴和少量的铁转变为金属状态。焙砂用氨-碳酸氨混合溶液浸出,浸出液经浓密机处理,得到的浸出液经净化、蒸氨后产出碳酸镍浆料,再经回转窑干燥和锻烧后,得到氧化镍产品。同时采用磁选法从浸出渣中选出铁精矿。氨浸的目的主要是在氨性溶液中将焙砂中的镍、钴以氨络离子的形式浸出,而铁、镁等杂质则留在浸出渣中,从而实现镍、钴与铁等杂质的初步分离。
氨浸法主要优点是能选择性溶解焙砂中的镍、铜、钴,并生成稳定的络合物分离回收,设备简单;主要缺点是镍、钴的回收率较低,全流程镍回收率仅为75%~80%,钴的回收率为40%~50%。是火法-湿法联合工艺,导致工艺流程长,加工成本高。目前新建工厂采用氨浸工艺的不多。
(2)加压酸浸法(HPAL)硫酸加压浸出红土镍矿工艺最早应用于古巴的毛阿镍厂,该厂于20世纪50年代由美国负责设计建设。该工艺的最大优点就是镍、钴的浸出率达到90%以上,大大高于还原焙烧-氨浸工艺,而且能耗及试剂消耗均低于氨浸工艺。该工艺适合于处理低品位褐铁矿层含氧化镁低、含钴相对较高的红土镍矿。近年来,世界上新近建成的镍红土矿湿法处理厂绝大部分均采用该工艺,如澳大利亚的考斯(Cawse)、布隆(Bulong)、莫林莫林(Muffin Murrin)以及菲律宾的珊瑚湾项目等。该工艺是国际上比较成熟的主流工艺,优点是镍钴浸出率高,酸耗低;缺点是投资过大,操作条件要求严格。
硫酸加压浸出红土镍矿工艺:在240~265℃条件下,用硫酸进行浸出,使Ni、Co等氧化物与H2SO4反应形成可溶的硫酸盐进入溶液,而铁则形成难溶的赤铁矿留在渣中。浸出过程是在高压浸出釜内进行的,高压浸出釜的材质为碳钢衬砖或钢-钛复合。早期的古巴毛阿厂采用的是立式碳钢衬砖加压釜,20世纪以后,随着材料工业的发展,新建的红土镍矿加压浸出厂均采用钢-钛复合材质的卧式加压釜,单台浸出釜的有效体积可以达到300m3以上,使红土镍矿的生产规模得到大幅提升,从而促进了该工艺的应用进展。加压浸出矿浆经浓密机逆流洗涤后,得到的浸出液在加压釜内通入硫化氢,选择性沉淀浸出液中的Ni、Co,得到品位较高的镍钴硫化物精矿,送镍钴精炼厂进行镍钴的分离提取。
(3)硫酸常压浸出法(AL)虽然硫酸加压浸出工艺具有较高的镍钴浸出率以及较低的加工成本,但是由于其浸出过程是在高温高压条件进行的,操作控制要求较高,且设备投资大。因此,越来越多的研究者开始关注常压酸浸工艺,寻求在常压条件下有效地从红土镍矿中分离出镍、钴的工艺方法。
常压浸出方法适合处理过渡型红土镍矿,具有工艺简单、能耗低、投资费用低、操作简单、环境友好、综合回收镍、钴、镁等优点,但也存在浸出矿浆液固分离困难、镍钴浸出率低、浸出液杂质含量高、浸出液处理困难等缺点。目前,中国云锡元江镍业有限责任公司、广西银亿科技矿冶有限公司、江西江锂科技有限公司等生产厂,均采用常压硫酸浸出工艺处理红土镍矿。
(4)硫酸化焙烧-浸出工艺(RAL)该工艺是将硫酸与矿石混匀后,在700℃左右的温度下进行焙烧,矿石中的镍和钴形成可溶性硫酸盐,而矿石中的铁则转化为难溶于水的赤铁矿,焙砂经过水或稀酸浸出后,镍钴进入到浸出液中,铁则留在渣中,从而实现了镍钴的选择性浸出。该工艺目前尚处于研究阶段,大规模工业化应用尚需要解决镍浸出率低的问题。
(5)盐酸常压浸出工艺(ACPL)红土镍矿盐酸常压浸出比较成熟的工艺是加拿大切斯巴尔资源公司(Chesbar Resources)开发的切斯巴尔法——氯化物常压酸浸工艺。该工艺的主要特点是通过喷雾热解工艺使浸出剂——盐酸和中和剂——氧化镁在流程中循环使用,从而大幅度降低了试剂消耗,废水排放量也大幅度减少,同时矿石中的镁得到综合回收。
盐酸常压浸出工艺虽然镍的浸出率可以达到90%以上,但同时矿石中的铁也被大量浸出,给后续浸出液处理工序带来较大困难。因此,该工艺应用于实际生产,还需要解决铁被大量浸出的问题。
(6)硫酸加压-常压联合工艺(HPAL-AL)不管是硫酸加压浸出工艺,还是硫酸常压浸出工艺,都面临除铁的问题。由于加压酸浸或硫酸常压浸出工艺处理低镁矿时,浸出液中有一定浓度的游离酸,从而导致浸出过程中主要杂质离子——铁离子不能发生完全水解而被除去。因此,出现了用镁质红土镍矿进行二段常压浸出的工艺,其目的就是中和浸出液中的游离酸,有利于铁离子的沉淀去除。
1.3.3 红土镍矿的其他处理工艺
对于红土镍矿而言,除了成熟的火法和湿法处理工艺外,还有其他一些处理工艺方法在不断的研发中。如生物冶金工艺、微波浸出工艺和氯化离析工艺等。
(1)生物冶金工艺 生物冶金工艺是利用微生物自身的氧化或还原特性,使矿物的某些组分氧化或还原,从而达到有价组分从矿物中分离出来的目的。其具有投资少、成本低等优点。但也存在反应速度慢、生产效率低、受环境影响较大、细菌对环境的适应性和耐热性较差、可用于红土镍矿浸出的细菌种类较少等缺点。
目前该工艺仍处于实验室研究阶段,一些学者采取使用特殊添加剂,通过电场、磁场、超声波等进行强化浸出过程,以及通过基因工程对菌种进行优良,但是浸出效果未得到明显改善。
(2)微波浸出工艺 由于微波能对物质具有选择性加热,并对吸波物质的化学反应具有催化作用,物质吸收的微波能几乎100%转化为热效应等特点,使微波加热矿物的热效率较高、吸波物质升温速度较快。
微波浸出工艺具有加热速度快、镍的浸出率高,选择性好等优点,但大型微波设备研发难度大,将该工艺用于大规模生产还需要开展大量的试验工作。
(3)氯化离析工艺 氯化离析法是一种气化冶金方法,是指在矿石中加入一定量的炭质还原剂(煤或焦炭等)和氯化剂(氯化钠、氯化钾、氯化钙等),在中性或弱还原气氛中加热,使有价金属从矿石中氯化挥发并同时在还原剂表面还原成金属颗粒的过程,它既不是单纯的氯化挥发过程,也不是单纯的还原过程,而是两者的结合过程。其目的在于使矿石中呈难选矿物形态存在的有价金属转变为金属颗粒,然后采用常规的选矿方法进行富集,得到品位比较高的金属精矿。因此,离析法实际上是选矿工艺中的一种对矿石的预处理方法,适宜于处理一些贫镍矿,即低品位红土镍矿及复杂的硫化镍矿。贫镍矿的共同特点是:不能用选矿的方法富集或选矿回收率很低;矿相及脉石组成复杂,且常伴生有少量的贵金属,故不宜采用还原氨浸或加压酸浸等常规湿法流程。
1.3.4 气化冶金-羰基法炼镍
羰基法是一种气化冶金方法。气化冶金主要是指金属或杂质通过气相迁移达到分离提取的冶金方法。气化冶金是利用金属单质或化合物的沸点与所含杂质的沸点不同的特点,通过加热控制温度使挥发性金属化合物的蒸汽热分解或还原而由气相析出金属的方法。按反应方法可分为气相热分解法和气相还原法两种。适用于气相析出法的金属是高熔点、难挥发的,但必须是能够生成在低温易于合成,而在高温易于分解的挥发性化合物的金属。镍的气化冶金主要指羰基法及氯化挥发焙烧和氯化离析法。
早在1898年,L.蒙德和C.兰格首先发现镍与CO在低温下能生成易挥发的羰化镍;在加热升温的条件下,该羰化物又分解为镍粉及CO。常与镍伴生的铜却很难生成羰化物,铁、钴等虽然与CO较易作用,但根据生成及挥发性质的差异,可达到选择性挥发及分解的目的。
镍羰基法冶金的基本原理:羰基是由碳和氧两种原子通过双键连接构成的一种很活泼的原子团(C=O),由几个这种原子团与金属原子在特定的条件下结合而成的一种特殊的化合物,即金属羰基配合物。在铁、钴、镍的化合物中,它们常见氧化态是+2、+3。但在羰基络合物中,铁、钴、镍的氧化态表现为0,例如五羰基合铁[Fe(CO)5],八羰基和二钴[Co2(CO)8]和四羰基合镍[Ni(CO)4]。羰基络合物的熔点、沸点一般都比常见的相应金属化合物低,容易挥发,受热易分解为金属和一氧化碳,利用上述特性,可先将金属制成羰基配合物,使它挥发与其他杂质分离,然后进行分解得到纯的金属。
镍在常压和高于室温(>38℃)条件下,可与一氧化碳作用生成羰基镍[Ni(CO)4]:
Ni+4CO=Ni(CO)4
当温度高至180~200℃时,羰基镍又分解为金属镍。
基于各种羰基镍络合物热物理性质的差异,在进行羰基合成反应时,粗镍中的杂质大部分不能进入气相,而残留于渣中,得到的粗羰基络合物又可按沸点的不同进行蒸馏分离,然后再加热分解就可以得到高纯度的金属镍。例如镍和铁的羰基络合物由于沸点相差很大,可用简单的方法分离。而羰基镍则用无水的液态氨形成羰基钴氨络合物[Co(NH3)6][Co(CO)4]2,从粗液态羰基镍中沉淀析出。