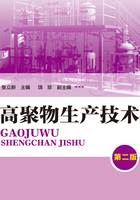
任务一 聚氯乙烯生产原理
【任务介绍】
依据单体氯乙烯的结构特征,从理论上分析判断合成聚氯乙烯所遵循的聚合机理,生产上如何选择合适的引发剂,采用什么方法控制聚合反应速率及产物的相对分子质量。
【相关知识】
氯乙烯的聚合按自由基聚合反应机理进行。聚合反应式可表示如下:
一、单体的性质及来源
氯乙烯单体在常温常压下是一种无色带有乙醚香味的气体,易液化,易发生氧化、加成、聚合等反应,是基本有机化工的重要基本原料。
工业上,氯乙烯主要通过乙炔路线、乙烯氧氯化路线和混合烯炔法三种途径获得。
二、聚氯乙烯的生产原理
前已述及,高聚物的形成反应按照反应机理的不同可分为连锁聚合反应和逐步聚合反应两大类。
1.连锁聚合反应及应用
连锁聚合反应是指单体经引发后,形成反应活性中心,单体迅速加成到活性中心上,瞬间生成高聚物的化学反应。
一个共价键化合物在受到热、辐射及超声波等能量的作用时,共价键将发生断裂,断裂形式有均裂、异裂两种。均裂时,共价键上的一对电子会形成两个带有独电子的中性基团,称为自由基;异裂时,共价键上的一对电子全部归属于某一个基团,形成阴离子;另一个缺电子基团称作阳离子。均裂和异裂可表示如下:
自由基和阳、阴离子均可作为活性中心,打开烯烃类单体的π键,形成单体活性中心,而后进一步与单体加成,使链不断增长,因此,连锁聚合反应根据反应中形成活性中心的性质不同,分为自由基聚合、阳离子聚合、阴离子聚合及配位聚合等。
连锁聚合反应是合成碳链高聚物的主要聚合反应,在连锁聚合反应中,自由基聚合反应的理论最成熟,工业上也处于最重要的地位,通过自由基聚合的产品占聚合物总产量的60%以上。比如,广泛应用的高压(低密度)聚乙烯(LDPE)、聚苯乙烯(PS)、聚氯乙烯(PVC)、聚甲基丙烯酸甲酯(PMMA)、ABS树脂、聚醋酸乙烯酯(PVAc)、丁苯橡胶(SBR)、丁腈橡胶(ABR)等都是通过自由基聚合反应合成的;丁基橡胶(IIR)、聚异丁烯(PIB)等是通过阳离子聚合反应合成的;聚丙烯(PP)、顺丁橡胶(BR)、异戊橡胶(IR)、乙丙橡胶(EPR)等是通过配位聚合反应合成的。
2.连锁聚合反应的单体
能够进行连锁反应的单体主要有三种类型,即含有碳-碳双键的单烯烃或共轭双烯烃类、羰基化合物及杂环化合物,其中烯烃类最为重要,应用最为广泛。由于烯烃类单体的结构不同,聚合能力也不同,对聚合类型的选择也就不同。单体究竟适合于何种聚合机理,主要取决于双键碳原子上取代基的电子效应(包括诱导效应、共轭效应);取代基的空间位阻效应主要影响单体的聚合能力。常用的烯烃类单体对聚合类型的选择性如表2-3所示。
表2-3 常用烯烃类单体对聚合类型的选择性

注:“+”表示可以聚合,“”表示已工业化,“-”表示不能聚合或只能得低聚物。
(1)电子效应对聚合类型的影响
乙烯基单体取代基的诱导效应和共轭效应能改变双键的电子云密度,对所形成活性种的稳定性有一定的影响,从而决定着对自由基、阳离子或阴离子聚合的选择性。许多实验也表明,烯烃类单体对聚合类型的选择性主要受取代基电子效应的影响。
①取代基为推电子基团 推电子基团能使单体双键电子云密度增大,易与阳离子活性种结合进行阳离子聚合。这类取代基有烷基、烷氧基、苯基、乙烯基等。但烷基的给电子性较弱,只有1,1-二烷基取代烯烃异丁烯才能进行阳离子聚合,而单取代烯烃、丙烯则不能进行阳离子聚合。
②取代基为吸电子基团 吸电子基团能使单体双键电子云密度降低,易与阴离子活性中心结合,分散负电性而形成稳定的活性中心。带吸电子基团的烯烃类单体易进行阴离子聚合或自由基聚合。这类取代基有氰基、羰基(醛、酮、酸、酯)等。但取代基吸电子性太强时,如含两个强吸电子取代基(氰基)的单体偏氰基乙烯,一般只能进行阴离子聚合。带卤素取代基的单体有些特殊,例如氯乙烯,氯原子的诱导效应是吸电子,而共轭效应则是推电子,两种效应都很弱。因此,氯乙烯既不能进行阴离子聚合,也不能进行阳离子聚合,只能进行自由基聚合。
③共轭效应的影响 像苯乙烯、丁二烯、异戊二烯等共轭烯烃,由于共轭体系中π电子流动性大,极易极化,所以既能进行自由基聚合,也能进行离子型聚合。
(2)位阻效应对聚合能力的影响
烯烃类单体上取代基的数量、大小和位置等空间位阻效应对单体聚合能力有很大影响,决定了它们能否进行加聚反应。
①无取代基烯烃单体 乙烯分子无取代基且结构对称,偶极矩等于零,不容易聚合,只有在高压高温下才能进行自由基聚合反应合成低密度聚乙烯;但采用齐格勒-纳塔引发剂,可在常温低压条件下通过配位聚合获得高密度聚乙烯。
②一取代基烯烃单体 通常情况下,取代基大小不会影响单体的聚合反应,如氯乙烯、丙烯等都能进行聚合。即使是取代基较大的乙烯基咔唑也能聚合。
③1,1-二取代基烯烃单体 这类单体由于结构的不对称,易诱导极化,故容易聚合,如偏二氯乙烯比氯乙烯更容易进行自由基聚合反应,异丁烯
容易进行阳离子聚合。但如果取代基的体积较大,聚合将不能进行。如1,1-二苯基乙烯
,由于苯基的体积较大,对聚合有空间位阻作用,只能形成二聚体而得不到高聚物。
④1,2-二取代基烯烃单体 这类单体结构对称,极化程度低,且空间位阻效应大,一般不容易进行均聚合,如2-丁烯、1,2-二氯乙烯
等。但有些单体能与其他烯烃类单体进行共聚。如马来酸酐可以与苯乙烯或醋酸乙烯酯共聚,得交替共聚物。
⑤三、四取代基烯烃单体 这类单体由于空间位阻较大,原则上都不能聚合。但唯一例外的是,当取代基是氟原子时,无论氟原子的数量和位置如何,都容易进行自由基聚合反应,如氟乙烯、1,2-二氟乙烯
、四氟乙烯
等都很容易聚合。主要是因为氟原子半径很小(仅大于氢),无空间位阻。
3.连锁聚合反应的特征
连锁聚合反应的特征可归纳为以下几个方面。
(1)典型的基元反应
连锁聚合反应一般由链引发、链增长和链终止三个基元反应组成,有时也伴随着链转移反应。各基元反应机理不同,反应活化能和反应速率相差很大。
(2)快速的形成过程
连锁聚合反应的单体只能与活性中心反应生成新的活性中心,单体之间不能反应;链增长速度极快,反应体系中没有中间产物,始终是由单体、聚合产物和微量引发剂及含活性中心的长链所组成。
(3)平均相对分子质量与反应时间的关系
连锁聚合反应一旦开始形成反应活性中心,便在极短的时间(通常以秒计)内,大量单体就会加成上去,形成高聚物,因此,延长反应时间不能增加聚合物的相对分子质量,关系曲线如图2-3所示。

图2-3 相对分子质量与反应时间关系曲线
(4)单体转化率与反应时间的关系
连锁聚合反应发生后,单体会随着反应时间的增长而逐步消失,因而,转化率随着反应时间的增长而逐渐提高,关系曲线如图2-4所示。

图2-4 单体转化率与反应时间关系曲线
(5)聚合反应不可逆
连锁聚合反应的大多数烯烃类单体在加成过程中,打开双键的π键同时会形成两个σ单键,由于键能的变化,会放出能量,属于放热反应且热效应较大,因而在一般温度条件下是不可逆的。
4.自由基聚合反应机理
自由基聚合反应是指单体借助于光、热、辐射、引发剂等的作用,使单体分子活化形成自由基活性中心,再与单体分子连锁聚合形成高聚物的化学反应。
自由基聚合反应按照参加反应单体的种类数目可以分为均聚合和共聚合两种。只有一种单体参加的自由基聚合反应称为均聚反应,如聚乙烯、聚氯乙烯、聚甲基丙烯酸甲酯、聚醋酸乙烯酯等。由两种或两种以上单体参加的自由基聚合反应称为共聚反应,如丁苯橡胶、丁腈橡胶、ABS树脂等。
自由基聚合反应遵循连锁聚合反应机理,通过三个基元反应,即链引发、链增长和链终止使小分子聚合形成大分子,在聚合过程中也可能存在链转移反应,链转移反应对聚合产物的相对分子质量、结构和聚合速率均产生影响。
(1)链引发反应
链引发反应是形成单体自由基活性中心的反应。单体可借助光、热、高能辐射或引发剂四种方式引发聚合,其中以引发剂引发最普遍。
引发剂是产生自由基聚合反应活性中心的物质,在分子结构上应具有弱键,容易分解形成自由基,并能引发单体使之聚合的化合物。其作用与催化剂类似,在聚合过程中将不断被消耗,但分解后的残基会存在大分子链末端,不能分离出来,成为所得高聚物的组成部分。
①引发剂引发机理 采用引发剂引发时,链引发反应通常分两步来完成,引发剂先分解产生初级自由基,初级自由基再与单体加成生成单体自由基活性中心(活性种)。
第一步:一个引发剂分子I发生均裂,形成两个初级自由基R·:
式中,kd为引发剂分解速率常数,s-1。
第二步:初级自由基与单体加成,形成单体自由基活性中心(活性种):
式中,ki为引发速率常数,s-1。
上述两步反应中,第一步引发剂分解反应是吸热反应,活化能高,分解速率常数kd小,反应速度慢;第二步是放热反应,活化能低,反应速率常数ki大,反应速度快。因此第一步引发剂分解反应不仅是控制整个自由基聚合反应速率的关键步骤,也是影响聚合产物相对分子质量的重要因素。
②引发剂的种类 前述自由基产生于共价键化合物的均裂,难易程度主要取决于共价键的键能大小,也和外界条件有关。比如,键能较小的化合物在较低温度下就可以断裂,键能较高的化合物需要较高温度才可以断裂。常见共价键的键能见表2-4。
表2-4 常见共价键的键能

由表2-4可见,碳-氮键(C—N)和过氧键(O—O)的键能较低,因此,这两类化合物适合作引发剂。
常用的引发剂有四种类型,即偶氮类引发剂(偶氮化合物)、有机过氧类引发剂(有机过氧化合物)、无机过氧类引发剂(无机过氧化合物)和氧化-还原引发体系。
a.偶氮类引发剂 偶氮类引发剂中最常用的是偶氮二异丁腈(AIBN)和偶氮二异庚腈(ABVN)。
偶氮二异丁腈是白色柱状结晶或白色粉末状结晶,不溶于水,溶于甲醇、乙醇、丙酮、乙醚、石油醚和苯胺等有机溶剂,属于油溶性引发剂。其分解温度为64℃,适用于大多数反应;100℃急剧分解,放出氮气和对人体危害较大的数种有机氰化物,能引起爆炸着火,易燃、有毒;应在10℃以下贮存,且远离火种、热源。
其分解反应式如下:
偶氮二异庚腈是在AIBN基础上发展起来的活性较高的偶氮类引发剂,有逐步取代偶氮二异丁腈的趋势。
其分解反应式如下:
偶氮类引发剂的分解反应几乎全部为一级反应,只形成一种自由基,并且分解均匀,无诱导分解,性质稳定,容易贮存、运输;分解速率较慢,属于中、低活性引发剂;产品容易提纯,价格便宜;分解时有N2逸出,工业上可用作泡沫塑料的发泡剂,科学研究上可利用N2放出速率来研究它的分解速率,广泛应用在高分子的研究和生产中。
工业上最典型的应用是聚氯乙烯的悬浮聚合、醋酸乙烯酯的溶液聚合。
b.有机过氧类引发剂 过氧化氢(HO—OH)是有机过氧类引发剂的母体,如果过氧化氢中的两个H原子都被有机基团取代,就形成了有机过氧化合物(R—OO—R')。
有机过氧类引发剂中最常用的是过氧化二苯甲酰(BPO)和过氧化十二酰(LPO)等。
过氧化二苯甲酰是白色粉末状晶体,不溶于水,溶于苯、氯仿、乙醚等有机溶剂,属于油溶性引发剂。其分解温度为73℃,干品极不稳定,贮存时加20%~30%的水,加热时易引起爆炸。
过氧化二苯甲酰按两步分解。
第一步:当过氧化二苯甲酰受热时,其弱键(O—O)发生均裂形成两个苯甲酸基自由基:
第二步:当有单体存在时,形成的自由基将引发聚合;无单体存在时,苯甲酸基自由基进一步分解成苯基自由基,并放出CO2,但分解不完全。
过氧化十二酰(LPO),也称为过氧化月桂酰,也是常用的有机过氧类引发剂。其分解反应式与过氧化二苯甲酰相类似。
过氧化二苯甲酰和过氧化十二酰作为引发剂的特点是分解速率较慢,容易发生诱导分解,属于低活性引发剂。为了提高聚合速率,缩短聚合周期,工业上常采用中、高活性的有机过氧化物引发剂,如过氧化二碳酸二异丙酯(IPP)、过氧化二碳酸二辛酯(EHP)、过氧化新癸酸异丙苯(CNP)等,但高活性引发剂在制备、贮存和精制时需要注意安全问题,使用时要避光、不能加热,且一般需配成溶液后在低温下(10℃以下)贮存,实验室中一般不使用。
工业上,醋酸乙烯的溶液聚合、甲基丙烯酸甲酯的聚合常常使用有机过氧化合物作为引发剂。
c.无机过氧类引发剂 最简单的无机过氧化物是过氧化氢,但因其需要较高的分解温度,一般不单独使用,要和还原剂组成氧化-还原引发剂。
水溶性过硫酸盐是常用的无机过氧类引发剂,代表物是过硫酸钾(K2S2O8)和过硫酸铵[(NH4)2S2O8]。属于水溶性引发剂,分解速率受体系pH值和温度影响较大,可单独使用,但更普遍的是与适当的还原剂构成氧化-还原体系,可在室温或更低的温度下引发聚合,常用在乳液聚合中。
K2S2O8的分解反应如下:
d.氧化-还原类引发剂 氧化-还原类引发剂是在过氧化物引发剂中加入适量还原剂组成的,通过氧化-还原反应的电子转移生成自由基,从而引发聚合。此类引发剂可降低分解活化能,使聚合反应在较低的温度下进行,具有较快的分解速率,有利于节省能源,可改善聚合产物的性能。
氧化-还原引发剂根据其是否溶于水,可分为水溶性氧化-还原引发剂和油溶性氧化-还原引发剂。常用的氧化-还原引发体系见表2-5。
表2-5 常用的氧化-还原引发体系

③引发剂的活性 工业上,常用某一温度下引发剂半衰期(t1/2)的长短或相同半衰期所需温度的高低来比较引发剂的活性。半衰期指引发剂分解至起始浓度一半所需要的时间,用t1/2表示,单位是h。
如前文所述,引发剂的分解反应为一级反应,即引发剂分解速率Rd与引发剂浓度[I]的一次方成正比,其表达式为:
若令引发剂起始浓度为[I]0,分解至t时刻时的浓度为[I],将式(2-1)移项积分,得:
当[I]=[I]0/2时,则:
由式(2-3)可见,半衰期仅与分解速率常数成反比,与引发剂起始浓度无关;分解速率常数越大,半衰期越短,引发剂的活性越高。常见引发剂的分解速率常数、半衰期和活化能见表2-6。
表2-6 常见引发剂的分解速率常数、半衰期和活化能

由表2-6可以看出,随着聚合反应温度的升高,分解速率常数kd增大,半衰期t1/2减小。
目前,常采用引发剂在60℃测得的半衰期来区分引发剂活性高低。t1/2>6h,为低活性引发剂;t1/2<1h,为高活性引发剂;1h<t1/2<6h,为中等活性引发剂。
④引发剂的引发效率 引发剂分解形成的初级自由基并不能全部用于引发单体,形成单体自由基活性中心,有部分引发剂将由于一些副反应而消耗掉,主要的副反应有诱导分解与笼蔽效应。初级自由基用于引发形成单体自由基的百分数或分率称为引发剂的引发效率,用f表示。一般引发剂的f值在0.5~0.8之间,数值的大小与引发剂种类、反应条件和单体活性有关。
a.诱导分解 在自由基聚合反应过程中,由于自由基很活泼,有可能与引发剂发生反应,使原来的链自由基终止生成稳定分子,另外产生一个新的初级自由基去引发单体,反应体系中自由基数没有变化,但消耗了部分引发剂分子,从而使引发效率降低。诱导分解的实质是链自由基向引发剂分子发生的转移反应。此类反应主要发生在过氧化物引发剂中,而偶氮类引发剂一般不发生诱导分解。
b.笼蔽效应 若聚合体系中引发剂浓度很低,引发剂分子处于在单体或溶剂分子的包围中,像关在“笼子”里一样,笼子内的引发剂分解成的初级自由基必须扩散并冲出“笼子”后,才能引发单体聚合。但自由基的平均寿命很短,只有约10-11~10-9s,如果来不及扩散到“笼子”外面去引发单体,就可能发生一些副反应,形成稳定分子,使引发剂效率降低,这种现象被称为“笼蔽效应”。大多数的引发剂均会发生这种现象,但偶氮类引发剂最容易发生。
此外,单体的活性大小对引发效率也有较大影响。像丙烯腈、苯乙烯等活性较大的单体,能迅速与自由基作用而引发增长,通常情况下f值较高;相反,像醋酸乙烯酯类低活性单体,对自由基的捕捉能力较弱,很易发生诱导分解,因此f值较低。
⑤引发剂的合理选择 工业上,合理地选择适宜的引发剂,对提高聚合反应速率、保证产品质量及安全生产具有重要的意义。通常,从以下几个方面考虑选择引发剂。
a.依据聚合反应的实施方法选择引发剂的类型 自由基聚合反应的工业实施方法有本体聚合、悬浮聚合、溶液聚合和乳液聚合。本体聚合、油相单体悬浮聚合、有机溶液聚合等要选择油溶性的偶氮类和有机过氧化物类引发剂,乳液聚合和水溶液聚合要选择水溶性的过硫酸盐类引发剂或氧化-还原引发体系。
b.依据聚合温度选择半衰期适当的引发剂 聚合温度是影响聚合速率和产物相对分子质量的重要因素,半衰期适当的引发剂可使自由基的形成速率和聚合速率适中,保证产品质量。半衰期过长或过短都不利于聚合反应正常进行。如果引发剂活性过低,造成分解速率过低,使聚合时间延长或需要提高聚合温度。相反,若引发剂活性过高,分解半衰期过短,虽然可以提高聚合速率,但反应放热集中,温度不好控制,容易引起爆聚;同时,也会因引发剂过早分解,造成低转化率阶段聚合反应停止。
若无适当半衰期的引发剂,也可以考虑选用复合引发剂,即采用两种或两种以上不同半衰期引发剂的混合物,针对实际聚合反应初期慢、中期快、后期又转慢的特点,最好选择高活性与低活性复合型引发剂,通过前期高活性引发剂的快速分解以保证前期聚合速率加快,后期维持一定速率,缩短了聚合反应的周期,能达到复合引发剂的“协同”效果。
常见引发剂的使用温度范围见表2-7。
表2-7 常见引发剂的使用温度范围

c.依据聚合物的特殊用途选择合适的引发剂 在选用引发剂时,有时还需要考虑引发剂对聚合产物的用途有无影响。如有机过氧类引发剂具有氧化性,合成的聚合物容易变色,不能用于有机玻璃等光学高分子材料的合成;偶氮类引发剂有毒因而不能用于医药、食品有关的聚合物合成;过氧化物在醇、醚、胺等溶液中迅速分解,易发生爆炸,故在这些溶剂中不易选择过氧化引发剂;在进行动力学研究时,多选择偶氮类引发剂,以防止发生诱导分解反应。
d.依据聚合反应选择适当的引发剂用量 引发剂浓度不仅影响聚合速率,还影响聚合产物的相对分子质量。通常,在保证温度控制和避免爆聚的前提下,尽量选择高活性引发剂,以减少引发剂用量,提高聚合速率,缩短聚合时间。在实际的生产中,引发剂用量大约为单体质量的0.8%~1.0%,但大多数情况下需要通过大量实验才能决定合适的引发剂最佳用量。
此外,在选择引发剂时,还要综合考虑如贮运安全、价格、来源、稳定性以及对聚合物外观的影响等各方面的因素。
⑥其他引发方式 其他引发方式包括热引发、光引发、辐射引发等。
a.热引发 热引发是指某些烯烃类单体可在热的作用下不加引发剂便能发生自身聚合反应。研究表明,仅少数单体,如苯乙烯在加热时(或常温下)会发生自身引发的聚合反应,其他单体发生的自聚合反应往往只是一种表面现象,绝大多数情况下是由于单体中存在的杂质(包括由氧生成的过氧化物或氢过氧化物)的热分解引起的;若将单体彻底纯化,在黑暗中,十分洁净的容器内,就不能进行纯粹的热引发聚合。
目前,苯乙烯的热聚合已经实现工业化。甲基丙烯酸甲酯虽然也能进行一定程度的热聚合,但聚合速度较低,还不能满足工业生产的要求。因此,对于热聚合机理的研究多限于苯乙烯的聚合。
b.光引发 光引发通常指单体在光的激发下形成的自由基引发单体聚合的反应。可分为直接光引发和光敏剂间接光引发两种类型。
直接光引发是单体分子直接吸收光照产生自由基而引发的聚合,单体一般是一些含有光敏基团的单体,如丙烯酰胺、丙烯腈、丙烯酸酯、丙烯酸等。
光敏剂间接引发是指在光照下,光敏剂吸收光后,本身并不直接形成自由基,而是将吸收的光能传递给单体而引发聚合,常用的光敏剂有二苯甲酮类化合物和各种染料。有光敏引发剂存在下的光引发聚合的反应速率比相应的单纯光引发聚合的速率要大得多。
光引发聚合的特点是自由基的形成和反应时间都比较短,聚合产物较纯净,实验结果重现性好;光引发聚合总活化能低,可在较低温度下聚合,能减少因温度较高而产生的副反应。
光引发聚合广泛应用于印刷制版、光固化油墨、光刻胶集成电路、光记录等。
c.辐射引发 辐射引发是指单体在高能射线辐射下完成的引发。辐射引发机理比较复杂,单体受辐射后可形成自由基、阳离子或阴离子,大多数烯烃单体的辐射引发遵循的是自由基聚合机理。辐射过程中还可能引起聚合物的降解或交联。
辐射引发聚合与光引发聚合相似,也可在较低温度下进行,温度对聚合速率影响较小,且聚合物中无引发剂残基,较纯净;此外,辐射引发吸收无选择性,穿透力强,可进行固相聚合。
辐射引发聚合多用于聚合物的接枝和交联改性。
(2)链增长反应
在链引发反应阶段形成的单体自由基活性中心,具有很高的活性,能很快打开第二个单体分子的π键,形成新的活性自由基,与此类似,自由基可以不断与其他单体分子结合形成高分子活性链,这就是链增长过程。
①链增长反应的机理及特征
链增长反应就是利用自由基与烯烃的反复加成地使聚合度增大的过程。例如:
为了书写方便,上述链自由基可以简写成,
代表碳链骨架。R代表引发剂残基。
链增长反应是放热反应。大多数烯烃类单体聚合热约55~95kJ/mol,反应热很大。
链增长反应速度极快。链增长反应活化能(20~34kJ/mol)较低,链增长速率常数[102~104L/(mol·s)]极高,链增长速率极快,在0.01s至几秒钟内,就可以使聚合度达到数千,甚至上万。因此,聚合体系内往往由单体和聚合物两部分组成,不存在聚合度递增的一系列中间产物。
由上述可见,链增长反应一旦开始,就会集中放出大量的热量,在生产中如果不考虑及时散热,将会造成体系温度过高,易引起生产事故。
②链增长反应的链结构 在链增长反应过程中,不仅要研究反应速率,还需分析大分子微观结构的变化。
以单取代乙烯基单体为例,在链增长反应中,大分子链中结构单元间的连接顺序可能存在下列三种连接方式:
表达式中的“头”代表有取代基的碳原子,另一端代表“尾”。综合极性效应和位阻效应的因素,链增长反应主要是按“头-尾”方式连接。因为按“头-尾”形式连接时,取代基与孤电子连在同一碳原子上,能与相邻亚甲基的超共轭效应形成共轭稳定体系,能量较低,自由基最稳定。而“头-头”形式连接时,没有共轭效应,自由基不稳定;另外,亚甲基一端的空间位阻较小,“头-尾”连接反应容易进行。所以大多数单烯烃类单体聚合的链增长以“头-尾”方式连接为主。
当单烯烃类取代基很小、空间位阻也不大时,可能得到相当数量的头-头连接(或尾-尾连接)结构。例如聚氯乙烯的头-头连接(或尾-尾连接)可达30%。
实践证明,聚合反应温度对链增长的链结构也会产生一定的影响。温度升高,头-头连接(或尾-尾连接)的比例将略有增加。例如醋酸乙烯酯的聚合温度从30℃升高到90℃时,大分子链结构中头-头连接(或尾-尾连接)的含量会从1.3%增加到1.98%。
此外,从立体结构看来,自由基聚合物分子链上取代基在空间排布是无规则的,所对应的聚合物往往是无定型的,这也是自由基型聚合产物的重要特征之一。
对于共轭二烯烃类单体的自由基链增长反应,可以按照1,2-加成或1,4-加成两种方式进行。如丁二烯:
由于1,2-加成时链增长的空间位阻较大,故高聚物中1,4-加成结构总是多于1,2-加成结构。在1,4-加成结构中又有顺式和反式两种异构体,由于空间位阻的影响,一般以反式结构为主。且1,2-加成结构的量几乎不随聚合温度的改变而改变,但顺式1,4-加成结构的量会随聚合温度的升高而增加。
(3)链终止反应
链终止反应是指链增长反应的长链自由基彼此相互作用,失去活性而生成稳定的高分子化合物的过程。自由基聚合的链终止反应主要是双基终止,包括偶合终止和歧化终止两种方式。
①偶合终止 偶合终止是两链自由基的孤电子相互作用结合成共价键的终止反应。偶合终止的特点是大分子的聚合度是两个链自由基重复单元数之和;若有引发剂引发聚合,大分子两端各带一个引发剂残基;大分子链中间以“头-头”结构方式连接。
②歧化终止 歧化终止是某链自由基夺取另一链自由基相邻碳原子上的氢原子或其他原子的终止反应。歧化终止的特点是大分子的聚合度和链自由基的重复单元数相同,每个大分子只有一端带有引发剂残基,其中,一个大分子的另一端为饱和,而另一个大分子的另一端为不饱和。
单体在自由基聚合反应中究竟以什么方式终止,主要取决于单体的种类和反应条件。
通常由实验测定,如苯乙烯、丙烯腈以偶合终止为主;甲基丙烯酸甲酯在60℃以下聚合时,两种终止方式都有,60℃以上时则以歧化终止为主。常见几种单体自由基聚合的终止情况见表2-8。
表2-8 自由基聚合终止方式

由表2-8可见,升高温度,会使歧化终止比例增加。这是由于歧化终止需要夺取氢原子或其他原子,其活化能比偶合终止高。另外,升高温度,自由基碳原子带有侧烷基的歧化终止比例也会增加。
在工业生产中,链自由基可能与反应器壁碰撞,而被金属的自由电子终止,这种终止方式是单基终止。因此,自由基聚合的主要设备聚合釜和搅拌器等都不能使用碳钢,一般应使用不锈钢或搪瓷衬里。
链终止和链增长是一对竞争反应,主要受反应速率常数和反应物浓度的影响,二者的活化能都很低,反应速度均很快。相比而言,链终止速率常数远大于增长速率常数,但从整个聚合体系宏观来看,反应速率还与反应物浓度成正比,而单体浓度远远大于自由基浓度,所以增长速率要比终止速率大得多。否则,将不可能形成长链自由基和高聚物。
(4)链转移反应
在自由基聚合过程中,链自由基可以与单体加成使链自由基增长,同时还可能从单体、引发剂、溶剂、相对分子质量调节剂等低分子或已形成的大分子上夺取一个原子终止形成稳定大分子,而使这些失去原子的分子成为新的自由基,继续新链的增长,使聚合反应继续进行下去,这一反应称为链转移反应。通式可以写为:
分子YS可以是单体、引发剂、溶剂、相对分子质量调节剂或大分子等,其结构中往往含有容易被夺取的原子,如氢、氯等。可见,链转移反应实质是活性中心的转移,转移后自由基的数目不变,因此,对聚合反应速度影响不大,主要影响聚合产物的相对分子质量。
链转移方式主要有向单体转移、向引发剂转移、向溶剂(链转移剂)转移及向大分子转移四种方式。
①向单体转移 向单体转移的速率与单体结构有关,如氯乙烯单体因C—Cl键能较弱而易于链转移,可用下式表示。
从活化能看,(a)形式活化能较大,因此,向单体转移以(b)的形式为主。向单体转移结果使原来的长链自由基因链转移而提前终止,造成聚合度降低,但转移后自由基数目并未减少,活性也未减弱,故聚合速率不变。
②向引发剂转移 也称为引发剂的诱导分解。自由基聚合体系中存在着引发剂,链自由基可能向引发剂分子夺取一个基团,使链自由基终止为一个大分子,引发剂变为一个初级自由基,可用下式表示:
向引发剂转移结果,自由基数目并无增减,只是损失了部分引发剂分子,因此,反应体系中自由基浓度不变,聚合物相对分子质量降低,引发剂效率下降。有机过氧化物引发剂相对较易链转移,偶氮化合物一般不易发生引发剂链转移。由于引发剂用量一般较少,因而向引发剂转移对聚合度的降低影响不大。
③向溶剂或链转移剂转移 向溶剂转移主要发生在溶液聚合中,如果溶剂分子中有弱键存在,易发生链转移,且键能越小,其转移能力越强。可用下式表示:
向溶剂分子转移的结果是聚合度降低,对聚合速率的影响程度取决于新自由基与原自由基活性的对比,若S·活性大于M·活性,则聚合速率加快,相反就减小;两者活性相等,则聚合速率不变。
如果溶剂分子中带有活泼氢原子或卤原子,则很容易发生这种转移,工业上将这种溶剂称为相对分子质量调节剂或链转移剂。例如丁二烯与苯乙烯乳液共聚制备丁苯橡胶时,加入十二硫醇作为相对分子质量调节剂,乙烯、丙烯聚合时以氢气为相对分子质量调节剂。
④向大分子转移 这类链转移反应一般发生在叔氢原子或氯原子上,使叔碳上带有孤电子,形成大自由基,再进行链增长,形成支链高分子,也可相互偶合成交联高分子,可用下式表示:
向大分子转移主要发生在聚合物浓度较高的聚合后期,此时单体的转化率较高,体系中大分子的浓度也很大,容易发生这种转移。
向大分子转移还有一种形式是向活性链内转移,这种转移也称为“回咬”转移,乙烯在高温、高压下自由基聚合时,聚乙烯链自由基发生转移反应使聚乙烯大分子产生长支链和C2~C4短支链,其中乙基、丁基等短支链的形成就是发生了向活性链内转移的结果。丁基支链是自由基夺取第5个亚甲基上的氢形成。乙基是加上一单体分子后作第二次转移而产生的。
综上所述,自由基聚合反应的基元反应中,链引发速率最小,是控制总聚合速率的关键。可归纳为慢引发、快增长、速终止、有转移。
5.自由基聚合反应速率
聚合速率是控制聚合反应过程最重要的指标之一,根据聚合体系单体转化率的变化可分为微观动力学和宏观动力学两部分。微观动力学主要研究聚合初期低转化率下(5%~10%)的聚合速率与单体浓度、引发剂浓度、聚合温度等参数之间的关系。宏观动力学主要研究高转化率下的动力学变化曲线、凝胶效应对聚合的影响等。
(1)自由基聚合反应微观速率方程
聚合速率指单位时间内消耗单体量或生成聚合物量,常以单体消耗速率(-d[M]/dt)或聚合物的生成速率(d[P]/dt)表示,以前者的应用为多。
自由基聚合反应包括了链引发、链增长、链终止三步主要基元反应,往往还伴随着链转移反应,各个基元反应对聚合速率均有影响。因此,其过程相当复杂,要想得到描述聚合反应速率方程式,需要进行简化处理。
①基本假设 如前文分析,链转移反应对自由基数几乎没有影响,若活性不变,对聚合速率也没有影响,因此在分析聚合速率时,可以不考虑链转移反应。尽管如此,在推导微观速率方程式时,还要作如下四个基本假设。
a.自由基等活性假设 假设链自由基的活性与链的长短无关,即各步链增长速率常数相等,不同链自由基对单体的链增长反应速率常数可用同一个kp来表示。即:
b.稳态假设 假设在聚合反应初期,体系中自由基浓度保持不变,进入“稳定状态”,即d[M·]/dt=0。也可以说链引发速率和链终止速率相等,构成动态平衡。即:
Ri=Rt
c.聚合度很大假设 假设单体自由基在很短时间内可以加上成千上万个单体,链引发所消耗的单体远远小于链增长消耗的单体,即:Ri≪Rp,由此,聚合总速率近似等于链增长速率。即
d.假设聚合过程中无链转移,链终止方式仅为双基终止。
②微观速率方程
微观聚合速率方程的导出依据是聚合机理。
a.链引发速率方程
引发剂引发时包括以下两步:
第一步:1个引发剂分解成2个初级自由基。
第二步:初级自由基同单体加成形成单体自由基。
由于引发剂分解反应最慢,是反应的控制步骤,因此引发速率一般仅取决于初级自由基的生成速率,而与单体浓度无关。即:
Ri=d[R·]/dt=2kd[I] (2-4)
由于诱导分解和笼蔽效应的影响,初级自由基分解的引发剂并不全部参加引发反应,因此需引入引发剂效率f,则引发剂引发速率方程为:
Ri=2fkd[I] (2-5)
式中 [I]——引发剂浓度,mol/L;
Ri——链引发速率,mol/(L·s);
kd——引发剂分解速率常数,s-1;
f——引发效率,通常为0.5~0.8。
b.链增长速率方程 链增长反应是单体与自由基反复加成的反应,速率可用增长反应中单体消耗速率——d[M]/dt表示。
在链增长过程中,链增长速率是各步链增长反应速率之和,根据等活性假设,则链增长总速率方程为:
令[M·]表示体系自由基总浓度,即[M·]=[RM1·]+[RM2·]+…+[RMn·],则链增长速率可表示为:
Rp=kp[M][M·] (2-6)
式中 Rp——链增长速率,mol/(L·s);
kp——链增长速率常数,L/(mol·s);
[M]、[M·]——分别代表单体和自由基总浓度,mol/L。
c.链终止速率方程 链终止为双基终止,终止速率以自由基消失速率表示。
偶合终止:
歧化终止:
令:kt=ktc+ktd,即kt为双基终止速率常数。则链终止速率为:
式中 Rt——链终止速率,mol/(L·s);
Rtc、Rtd——分别为偶合终止速率与歧化终止速率,mol/(L·s);
kt——双基链终止速率常数,L/(mol·s);
ktc、ktd——分别为偶合终止速率常数与歧化终止速率常数,L/(mol·s);
[M·]——自由基总浓度,mol/L。
式(2-7)中的数字2表示每次链终止同时消失2个自由基,这是美国习惯,欧洲习惯不加2,查表时需注意。
d.聚合总速率方程 根据稳态假设,Ri=Rt,则式(2-7)可变为:
[M·]=(Ri/2kt)1/2 (2-8)
根据聚合度很大假设,聚合总速率R总≈Rp,将式(2-8)代入式(2-6),即得自由基聚合反应微观速率方程为:
Rp=kp[M](Ri/2kt)1/2 (2-9)
可见,引发方式不同,其聚合反速率的表达式不同。若为引发剂引发,将式(2-5)代入式(2-9),整理后,得:
上式表明,引发剂引发时,聚合速率与单体浓度的一次方成正比,与引发剂浓度的平方根成正比。许多在低转化率下的聚合实验结果也表明了上述关系的正确性,聚合速率方程成为了指导高聚物工业生产的理论基础。
从聚合速率方程推导过程可见,该方程是在等活性、稳态、大分子以及在反应初期不发生链转移反应的基础上推导得到的。该方程的结论Rp∝[I]1/2,是双基终止的结果。但实际情况有时会存在单基终止与双基终止并存,如在高黏度或沉淀聚合中,结果使聚合速率偏离单体浓度的1/2次方而变成1次方,也就是存在的情况可能是Rp∝[I]0.5~1。该方程的结论Rp∝[M],是单体自由基形成速率远大于引发分解速率的结果。但若初级自由基与单体的引发反应较慢,或引发反应与单体浓度有关(例如成正比),则实际也可能是Rp∝[M]1~1.5。
该方程的结论是在低转化率条件下成立,也就是反应的初期阶段。当转化率较高时,体系黏度增高,会有自加速等反常现象,使聚合速率变化更加复杂,难以用某一方程式来表示,常用单体转化率-时间曲线来直观描述聚合速率的变化规律。
(2)自由基聚合反应宏观速率曲线 在自由基聚合反应的全过程中,聚合速率是不断变化的,尤其是高转化率时,难以用适当的函数式来描述,因此,一般常用单体转化率-时间曲线来直观地描述聚合速率的变化规律。其速率变化主要存在三种类型,如图2-5所示。

图2-5 自由基聚合反应
转化率-时间曲线1—常见S形曲线;2—匀速聚合型;3—前快后慢型
①常见S形曲线 如图2-5中曲线1所示,该曲线可以明显地分为诱导期、聚合初期、聚合中期、聚合后期四个阶段,影响各阶段速率的因素并不完全相同。
a.诱导期(聚合速率为零) 此阶段引发剂分解产生的初级自由基被阻聚杂质所终止,不能引发单体,无聚合物生成,聚合速率为零。在实际工业生产上,存在诱导期的危害是延长聚合周期,增加动力消耗。缩短或消除诱导期的根本途径是必须清除阻聚杂质,将杂质含量控制在0.003%以下,单体纯度达99.9%~99.99%以上。非常纯净的单体聚合时,可以没有诱导期。
b.聚合初期(稳态期或等速期) 此阶段在微观动力学研究时,转化率控制在5%~10%以下,工业生产中控制在10%~20%以下,转化率与时间之间呈近似线性关系。主要原因是在诱导期过后,阻聚杂质已基本耗尽,单体和长链自由基开始正常聚合,且体系中的大分子数量较少,黏度较低,体系处于稳态阶段,聚合恒速进行。此阶段聚合速率关系符合微观动力学方程。
c.聚合中期(加速期期) 随着转化率进一步提高达10%~20%以后,体系黏度增大,体系会出现自加速现象,将一直延续至转化率达50%~70%。此阶段由于转化率增高,体系内大分子数目增多,体系黏度不断增大,使长链自由基的活动受阻,甚至活性链的端基被包裹,很难发生双基终止。但低分子单体仍可以自由地与长链自由基碰撞,不影响链增长反应,聚合速率相应增加,由此出现自加速现象。这种由于体系黏度增加所引起的不正常动力学行为称为自加速现象或凝胶效应。
自加速现象将随单体种类及聚合条件的变化有所不同,如图2-6所示是甲基丙烯酸甲酯在不同浓度下聚合时的自加速情况。从图中可以看到,浓度在40%以下时的溶液聚合时,没有自加速现象;浓度在60%以上时,自加速现象明显,且随着单体浓度的增加,开始出现自加速现象时的转化率提前。如果是不加溶剂的本体聚合,自加速更激烈。此外,溶剂的种类、聚合温度、引发剂用量与活性、链转移反应等对自加速现象也有一定影响。

图2-6 甲基丙烯酸甲酯溶液聚合时单体浓度对自加速的影响
注:引发剂:BPO;溶剂:苯;温度:50℃;曲线上数字为甲基丙烯酸甲酯的浓度。
自加速现象在自由基聚合反应中是一种普遍存在的现象,在工业生产中很容易造成放热集中,引起爆聚和喷料等生产事故的发生,使生产难于控制,同时高温使单体气化,在产物中产生气泡,甚至会产生支链及交联,影响聚合产品的质量,因此必须严格加以避免和控制。
自加速现象是由于体系黏度的增加而引起的,因此,凡是能降低黏度的办法都能够推迟或尽量避免自加速的发生,常用的有四种方法。一是采用溶液聚合,利用适当的溶剂来稀释聚合物,降低体系的黏度;二是适当的提高温度,利用液体黏度随温度的升高而降低的性质,将体系的黏度控制在出现自加速的黏度以下;三是采用低温引发剂实现低温乳液聚合;四是添加适当的链转移剂控制聚合物的相对分子质量,降低体系黏度。
有时也可利用自加速现象使聚合反应速率加快,可以缩短聚合周期,提高生产效率。如在聚合开始时,向单体中加入一定量的高聚物粉末,使体系黏度增大,促进自加速作用提前出现。
d.聚合后期(减速期) 当单体转化率达50%~70%以后,体系黏度更大,单体和自由基的浓度减小,聚合速率大大降低。此阶段单体的自由碰撞也开始受阻,使链增长速率也大大下降,向大分子发生链转移反应的机会增加,使聚合产物出现支链、分枝或交联结构。工业生产上,为了保证产品质量和缩短聚合生产周期,往往达到预期的转化率就停止聚合反应。例如,聚氯乙烯的悬浮聚合最终转化率不超过90%;丁苯橡胶合成中转化率达60%~70%左右即行停止,分离聚合物,回收未反应单体。
②匀速聚合型 如图2-6中曲线2所示,如果选用半衰期适当的引发剂,使正常聚合速率的衰减与凝胶效应的自动加速过程互相抵消,就可能出现理想的反应。从工业生产过程控制的角度来说,很希望能达到匀速聚合,但需要合理地选择引发剂。例如聚氯乙烯悬浮聚合生产时,若选用半衰期为2.0h左右的引发剂,基本上能达到匀速聚合,也可以选用高活性和低活性复合型引发剂。
③前快后慢型 如图2-5中曲线1所示,如果选用活性特高的引发剂,聚合初期就会有大量的自由基产生,聚合速率很快,中期以后,由于引发剂浓度很低,聚合会变得很慢,甚至在转化率不高时就停止了聚合,从工业角度看不愿意出现这样的局面,可以采用分批加入引发剂的方法来解决。
6.自由基聚合反应产物的平均相对分子质量
平均相对分子质量及其分布是衡量聚合产物质量的重要指标,也是工业生产中的主要控制因素。高聚物的许多性能,如强度、力学性能、热稳定性、加工性能等,都和平均相对分子质量有着密切的关系。
如前文所述,链转移反应对聚合速率影响可不予考虑,但对聚合产物的平均相对分子质量的影响很大。分述两种情况如下:
(1)无链转移时的聚合度方程
无链转移时的聚合度通常用动力学链长表示。所谓动力学链长是指每个活性中心从引发到终止所平均消耗的单体分子数,以ν表示。动力学链长为增长速率和引发速率的比,依据稳态时引发速率等于终止速率,则动力学链长可表示为:
将式(2-6)、式(2-7)和式(2-8)代入上式,得:
若自由基聚合反应由引发剂引发时,用Ri=2fkd[I]代入式(2-12),得:
由上式可知,动力学链长与单体浓度的一次方成正比,与引发剂浓度平方根成反比。可见,在自由基聚合体系中,增加引发剂用量虽然可以提高聚合速率,但又使聚合产物的相对分子质量降低,因此,生产中要严格控制引发剂的用量,此外,动力学链长还和聚合温度有关,聚合温度升高,聚合速率增大,平均相对分子质量降低。
(2)动力学链长与平均聚合度的关系
平均聚合度是指平均每个聚合物分子中所含重复结构单元数,它与动力学链长的关系取决于链终止方式。偶合终止时;歧化终止时
,两种终止方式同时存在时,可按比例计算。
(3)有链转移时的聚合度方程
在自由基聚合反应中,当有链转移反应发生时,一般不会影响聚合反应速率,但会对聚合产物的相对分子质量产生很大影响。此时产物的平均聚合度应包含以下几个部分:
向单体、引发剂、溶剂及大分子转移的反应式及聚合速率方程可表示如下:
向单体转移:
向引发剂转移:
向溶剂转移:
向大分子链转移:
歧化终止时,将式(2-15)、式(2-16)、式(2-17)及式(2-18)代入式(2-14),取倒数,整理得:
式中 ktrM,ktrI,ktrS,ktrP——向单体、引发剂、溶剂、大分子转移速率常数;
[S],[P]——溶剂、大分子浓度。
令:,
,
,
,分别代表向单体、引发剂、溶剂、大分子转移常数,则式(2-19)变为:
上式表明,正常聚合时双基终止(歧化终止)、向单体转移、向引发剂转移、向溶剂转移和向大分子转移等项对产物平均聚合度均有贡献。各类链转移常数,可以从聚合物手册中查取,选用时,必须注意指定单体、溶剂和温度条件。聚合产物的平均聚合度不仅与单体浓度、引发剂浓度、链转移剂浓度有关,而且还与单体、引发剂及链转移剂的链转移能力有关。
①向单体转移 当实施本体聚合时,体系中没有溶剂,则CS=0;若采用无诱导反应发生的偶氮类引发剂或热引发,则CI≈0;若向大分子转移很少,则CP≈0。式(2-20)将简化为:
此时,体系可近似看成只发生向单体链转移反应,聚合度与向单体链转移常数CM有关。向单体转移的能力与单体结构、聚合温度等有关。当单体分子中带有叔氢原子、氯原子等键合力较小的原子时,容易被自由基夺取而发生转移反应;向单体链转移常数CM随温度升高而增大。表2-9中列出了常见单体在不同温度下的链转移常数CM。
表2-9 向单体的链转移常数(CM×104)

从表2-9中可以看到,多数单体像甲基丙烯酸甲酯、丙烯腈和苯乙烯的链转移常数CM都很小,对产物的相对分子质量影响不大。但氯乙烯由于结构中的C—Cl键能较低,氯原子很容易被夺取,其链转移常数CM值是乙烯基单体中最大的,甚至远远超过了正常的终止速率,即RtrM≫Rt,因此,聚氯乙烯的平均聚合度仅取决于向单体链转移的速率常数CM。
从表中也可以看出,聚合温度升高,CM增大,则聚氯乙烯产物的聚合度降低。生产实践证明,氯乙烯悬浮聚合时产物的聚合度与引发剂用量、单体转化率基本无关,只取决于聚合温度。因此,生产上采用聚合温度控制聚合度,引发剂的用量调节聚合反应速率。
②向引发剂转移 向引发剂发生链转移是由于引发剂的诱导分解而引起的,主要发生在过氧化物类引发剂中,不仅影响了引发剂的引发效率,也会使聚合产物的平均聚合度降低。通常情况下,虽然向引发剂转移常数CI比CM和CS大,但一般情况下引发剂的浓度很小,因此,向引发剂转移造成产物聚合度下降的影响不大,可以忽略不计。
③向溶剂或链转移剂转移 向溶剂转移对平均聚合度的影响只有在实施溶液聚合时才加以考虑。将式(2-20)右边的其余四项合并,用表示无溶剂或链转移剂时的平均聚合度倒数,可写成:
实验测定,在不同[S]/[M]下的产物聚合度,以对[S]/[M]作图,可得到一条的直线,该直线的斜率即为向溶剂转移常数CS。图2-7所示为100℃时苯乙烯热聚合烃类溶剂对平均聚合度的影响。

图2-7 烃类溶剂对聚苯乙烯平均聚合度的影响(100℃苯乙烯热聚合)
1—苯;2—甲苯;3—乙苯;4—异丙苯
向溶剂链转移常数CS的大小受溶剂结构、单体(或自由基)结构及聚合温度的影响。如溶剂分子中有活泼氢或卤原子时,CS一般较大,特别是脂肪族的硫醇CS较大,常用作相对分子质量调节剂。温度升高,向溶剂转移常数CS增大。
在高分子合成生产工业上,有时为了控制产物的相对分子质量,确保合适的加工性能,需要人为加入特殊的溶剂(链转移剂)。另外,制备低相对分子质量的聚合物,如制备润滑油、表面活性剂等化工材料时,也需要选用适当的链转移剂来调节相对分子质量。
④向大分子转移 如前文所述,向大分子发生链转移的结果是在大分子主链上生成活性点,单体在活性点上增长,形成许多长支链及短支链。这种转移对平均聚合度的影响不大,支链的存在主要影响高聚物的结晶度、密度、强度等物理力学性能。向大分子转移常数CP随温度升高而增加。
7.阻聚与缓聚
在高分子合成的科学研究及实际工业生产中,一般对聚合级单体的纯度要求较高,在聚合前必须要清除或限制影响聚合反应的有害杂质在一定的含量以下,否则将使聚合反应出现诱导期增长或降低聚合反应速率。但部分烯烃类单体,如苯乙烯、甲基丙烯酸甲酯等,在单体分离、精制、贮存、运输过程,很容易发生自聚反应,为保证安全,往往要加入一定量的“阻聚杂质”——阻聚剂,在单体使用前再把阻聚剂除掉,否则需使用过量的引发剂。可见,阻聚剂的作用并不次于引发剂,因此,有必要了解这类物质的类型、作用机理,从而选择适用的阻聚剂。
(1)阻聚剂与缓聚剂
从“阻聚杂质”对聚合反应的抑制程度,可分为阻聚剂和缓聚剂两类。
能使反应中的每个活性自由基都消失,而使聚合完全停止的物质称为阻聚剂;只消灭部分自由基或使自由基活性衰减,而使聚合速率减慢的物质称为缓聚剂。阻聚剂与缓聚剂在作用机理上无本质差别,只是作用的程度不同而已,分别称为阻聚作用和缓聚作用,有时两者很难区分。
当体系中存在阻聚剂时,在聚合反应开始以后,并不能马上引发单体聚合,必须在体系中的阻聚剂全部消耗完后,聚合反应才会正常进行。从引发剂开始分解到单体开始转化存在一个时间间隔,称诱导期。
图2-8所示是苯醌、硝基苯和亚硝基苯等对100℃苯乙烯热引发的影响。由图可知,苯醌是阻聚剂,会导致聚合反应存在诱导期,但在诱导期过后,不会改变聚合速率;硝基苯是缓聚剂,不会导致诱导期,不会使聚合反应完全停止,只会减慢聚合反应速率。亚硝基苯则兼有阻聚和缓聚作用,在一定的反应阶段充当阻聚剂,产生诱导期,反应一段时间后其阻聚作用消失,转而成为缓聚剂,使聚合反应速率减慢。

图2-8 苯乙烯100℃热引发阻聚剂与缓聚作用的影响
1—无阻聚剂;2—0.1%苯醌;3—硝基苯;4—亚硝基苯
(2)典型的阻聚剂与阻聚机理
阻聚剂的种类很多,一般分为分子型阻聚剂和自由基型阻聚剂两大类。
①分子型阻聚剂 常见的有苯醌、硝基化合物、芳胺、酚类、含硫化合物等,是工业普遍使用的阻聚剂。其中,苯醌是最重要的常用阻聚剂,加入量在0.001%~0.1%就能达到阻聚效果,但随单体不同其阻聚效果有所不同,如苯醌是苯乙烯、醋酸乙烯酯的有效阻聚剂,但对甲基丙烯酸甲酯、丙烯酸甲酯、丙烯腈等单体却只能起缓聚作用。
苯醌的阻聚行为比较复杂,苯醌分子上的氧和碳原子有可能与自由基发生加成反应,而后发生偶合或歧化终止,其过程可以表示如下:
醌类阻聚剂的阻聚能力与醌类结构和单体性质有关。实际应用时,通常使用对苯二酚,经氧化后生成苯醌。酚类阻聚剂同时又是抗氧剂和防老剂,其阻聚作用在单体中有氧存在时才表现出来,是用途广泛的一类阻聚剂,常用的是对叔丁基邻苯二酚和2,6-二叔丁基对甲基苯酚(俗称“264”)等。
芳胺类阻聚剂只有氧存在条件下才具有阻聚作用,与酚类一样,既能作阻聚剂也能作抗氧剂和防老剂,常用的是对甲苯胺、N-亚硝基二苯胺和次甲基蓝等。次甲基蓝也是含硫阻聚剂,在氯乙烯悬浮聚合作防黏釜剂使用。
硝基及亚硝基化合物阻聚剂一般用作缓聚剂或弱阻聚剂,它的阻聚效果与单体结构有关,如对醋酸乙烯酯是阻聚剂,而对苯乙烯则是缓聚剂,对甲基丙烯酯类和丙烯酸酯类却无阻聚作用。常用的有硝基苯、间硝基氯苯等。
②自由基型阻聚剂 常见的有1,1-二苯基-2-三硝基苯肼自由基(DPPH)、三苯甲基自由基等。自由基型阻聚剂本身均含有氮或氧自由基,是极稳定的自由基,它不能引发单体聚合,但能很快与链自由基或初级自由基作用发生双基终止而阻止聚合反应。
DPPH是自由基型高效阻聚剂,在浓度10-4mol/L时就能阻止醋酸乙烯酯、苯乙烯、甲基丙烯酸甲酯等烯烃类单体的聚合,故有“自由基捕捉剂”之称,也是理想的阻聚剂。DPPH未反应之前是黑色的,捕捉自由基后,变为无色,因此可用比色法来定量判断其消耗情况。科学研究中常用来测定引发速率,进而求引发效率。DPPH的阻聚作用可表示如下:
自由基型阻聚剂的阻聚作用虽好,但因制备困难、价格昂贵,所以单体精制、贮存、运输、终止反应等情况下一般不用,多用于测定引发速率。
③特殊物质的阻聚作用
a.氧的阻聚作用 氧具有显著的阻聚作用,可看作是双自由基型阻聚剂,氧与自由基反应,形成不活泼的过氧自由基,过氧自由基本身与其他自由基歧化或偶合终止,过氧自由基有时也可能与少量单体加成,形成相对分子质量很低的共聚物。生产中,氧的主要来源是由空气带入反应系统中,因此,聚合反应通常要先排除氧,然后在氮气保护下进行。但有时高温时过氧化物能分解出自由基而引发聚合反应,乙烯高温高压聚合用氧作引发剂就是这个原理。
b.金属盐氧化剂 常见的有氯化铁、氯化铜等,这类变价金属盐可与自由基之间发生电子转移反应(即氧化-还原反应),将自由基转化为非自由基,使之失去活性,从而阻止或减慢了聚合反应的进行。以氯化铁为例可表示如下:
氯化铁不但阻聚效率较高,并能化学计量地消灭自由基,因此,常用于测定引发剂的引发速率。
c.烯丙基单体的自阻聚作用 在自由基聚合中,烯丙基单体不仅聚合速率很低,并且往往只能得到低聚物。在这类聚合反应中,链自由基与烯丙基单体存在加成和转移两个竞争反应。
链转移后生成的烯丙基自由基由于有双键的共轭稳定性,不能引发单体聚合,只能与其他自由基终止,得到低聚物。由于起缓聚或阻聚作用的是烯丙基单体自身,因此被称为烯丙基单体的自阻聚作用。
(3)阻聚剂的选用原则
阻聚剂在实际生产中不仅种类繁多并且用途广泛,可以防止单体精制与贮运时发生自聚;使聚合在某一转化率下停止,抑制爆聚;测定引发速率,研究聚合机理;防止高分子材料老化等。
在生产中总的选择原则是用量小、效率高、无毒、无污染、容易从单体中脱除、易制造、成本低,也要考虑单体类型、副反应、复合使用与温度影响等。
阻聚剂对不同单体的阻聚效果各不相同,所以要根据单体类型来选择合适的阻聚剂。当聚合烯烃单体的取代基为推电子基团时(—C6H5、—OCOCH3等),首选醌类、芳硝基化合物、变价金属盐类等亲电子物质,其次选酚类或芳胺类物质;若取代基为吸电子基团(—CN、—COOH、—COOCH3等),首选酚类、芳胺类供电性物质,其次选用醌类和芳硝基化合物。若聚合体系中含有氧气时,则形成的自由基链除外,还有过氧自由基
,要先考虑酚类、胺类,或酚、胺合用,其次考虑选用醌类、芳硝基化合物、变价金属盐类等。
实际上,究竟选择何种阻聚剂,还需要经过大量的实验来确定。如苯乙烯在贮存过程中很容易发生自聚,可加入苯醌或对叔丁基邻苯二酚作阻聚剂,实践证明,对叔丁基邻苯二酚的加入量少,且阻聚效果好。
8.自由基聚合反应的影响因素
影响自由基聚合反应的主要因素有原料纯度与杂质、引发剂浓度、单体浓度、聚合温度、聚合压力等。
(1)聚合反应温度
和一般的化学反应一样,聚合反应对温度最为敏感,尤其是热引发或引发剂引发的聚合反应受温度的影响更为显著。温度不但影响聚合速率和产物的平均聚合度,还会影响产物的微观结构。通常,聚合速率随温度的升高而增大,产物平均聚合度随温度的升高而下降。
因此,聚合反应温度是影响聚合产物产品质量的一个重要参数,为防止产物相对分子质量的波动,必须严格控制聚合反应温度。
(2)聚合反应压力
一般来说,压力对液相聚合或固相聚合影响较小,但对气态单体的聚合速率和相对分子质量的影响较显著。通常情况下,聚合压力增高,聚合速率加快,产物相对分子质量增大,支化程度降低。但是,压力对聚合反应速率的影响要比温度的影响要小。工业生产上,只有当聚合反应温度一开始就比较高的时候,才使用高压聚合反应。
(3)原料纯度与杂质
高分子合成所用的单体、引发剂、溶剂、水及其他各种助剂等主要原料,在生产上,对它们的纯度都有严格的要求。一般聚合级的单体纯度在99.9%~99.99%,杂质的含量在0.01%~0.1%。不同的聚合反应条件,对原料纯度要求也不同。如对聚合级氯乙烯单体的要求是纯度>99.9%、乙炔含量<0.001%、铁含量<0.001%、乙醛含量<0.001,且高沸点物质微量。这里有些杂质的含量虽少,但对氯乙烯聚合的影响颇大。表2-10中列出乙炔对氯乙烯聚合的影响。
表2-10 乙炔对氯乙烯聚合的影响

总之,杂质的影响是多方面的,对高聚物性能的影响较为显著,微量杂质的存在就不能获得高相对分子质量的聚合物。
9.氯乙烯的自由基聚合反应原理
如前文所述,向单体发生链转移反应是氯乙烯聚合反应机理的基本特征,引发剂种类和用量主要用来调节聚合反应速率或生产周期长短。在实际生产上,当聚合温度在60℃以下时,聚氯乙烯平均聚合度仅取决于聚合温度,而与引发剂浓度、转化率无关,可利用调整聚合温度来改变PVC牌号。当聚合温度在60℃以上时,除适当改变温度外,还应加入少量链转移剂来控制产物相对分子质量,以免在较高温度下造成过高的操作压力,同时也可减少高温对树脂热稳定性的影响。因此,严格控制聚合温度是保证聚氯乙烯不转型的重要手段。为提高生产能力,选择半衰期适当的引发剂可使聚合过程有比较均一的聚合速率。