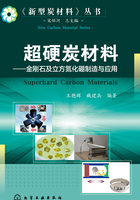
3.7 金刚石的提纯、分选与检测
人造金刚石的后处理包括提纯、分选和质量检测三个工序。提纯处理就是除去反应料中未反应的石墨以及混杂的催化剂金属或合金、叶蜡石等杂质,以便获得高纯度的金刚石。分选就是将提纯后的人造金刚石进行整形、筛分和选型,从而划分出不同质量和粒度的金刚石。质量检测就是将分选后不同粒度和质量的金刚石按照国家标准统一进行标定,以便获得不同品级的正式产品。
3.7.1 金刚石的提纯
静压催化剂法合成金刚石,合成工艺不同,石墨等碳素材料转化为金刚石的转化率也就不同,最高大约为30%,一般的只有10%左右。产物除金刚石外,还有未反应的石墨、催化剂金属或合金,同时还混有部分叶蜡石,它们紧密地粘在一起,并把金刚石包裹得很严实。要获得纯净的金刚石,就得清除这些包裹物以及杂质,即金刚石的提纯处理。
为了选择环保、经济、迅速的提纯方法和工艺,首先应了解反应料中各物质的物理化学性质。产物金刚石的硬度高,化学性质稳定,抗腐蚀,不被电解,而反应物石墨的化学稳定性较弱,抗腐蚀性差,加热条件下便会被强氧化剂氧化。催化剂金属或合金则与多种酸反应,且易被电解。叶蜡石则易与碱发生反应。据此,便可选择提纯处理的方法。
金刚石的提纯(图3-21),必须首先清除催化剂金属,然后再分离叶蜡石和石墨杂质。

图3-21 金刚石提纯工艺流程
3.7.1.1 除催化剂金属或合金
催化剂金属或合金的去除方法很多,这里仅介绍稀硝酸法、王水处理法和电解法。
(1)稀硝酸法
合成金刚石所用的催化剂一般为Ni、Fe、Cr、Mn等元素及其合金,它们易溶于硝酸。将合成出来的金刚石混合体砸碎,浸泡在30%左右的稀硝酸溶液中,几天以后,金属或合金就逐步被稀硝酸溶解,生成一种可溶性盐类,并置换出氢气。
以Ni为例,反应原理如下:
Ni+2HNO3Ni(NO3)2+H2↑
(2)王水处理法
王水是一种氧化性极强的溶液,由盐酸、硝酸按体积比为3∶1配制而成,可溶解盐酸或硝酸不能单独溶解的物质。其反应原理如下(以Ni为例):
3Ni+2HNO3+6HCl3NiCl2+2NO↑+4H2O
王水的强氧化性是由于盐酸与硝酸混合后,硝酸会氧化盐酸,析出游离态氯和氯化亚硝酸等氧化性极强的物质。因此王水与催化剂反应的产物为氯化物,而非硝酸盐。
将合成后的金刚石合成棒砸碎后与王水一起装在烧杯或其他耐酸容器中,并置于电热板上加热。在加热过程中,王水与混体中的催化剂金属或合金进行激烈的反应,在很短的时间内,把金属或合金溶解,并生成盐。当反应十分微弱时,即可停止加热,待冷却后,倒出废液,产品用自来水清洗数次至洗涤液呈中性便可。
但上述两种酸泡法耗酸量大,成本高,污染极其严重,仅适于实验或小批量处理。
(3)电解法
电解法适于大批量处理,不仅可以回收金属,且污染小,成本低。
电解过程是相应原电池的逆过程,是外加电流通过电解质溶液,并靠离子的定向移动而产生化学反应的过程,从能量角度来说就是把电能变为化学能的过程。在电解时,在阳极上发生氧化反应,由于所用电极分为可溶电极和不溶电极。当使用可溶电极时,阳极主要是金属溶解变为阳离子的过程,如CuCu++e。当使用不溶电极时,则阳极上发生的是阴离子的放电,如Cl-
Cl+e。还有一些电极在不同的介质和电解条件时,既可表现为可溶电极,也可以表现为不溶电极,如Fe、Ni、Al等,这类电极称为“半溶解”电极。与阳极相对应,电解时,在阴极上发生的是还原反应。通常是金属离子或氢离子的还原反应,如Cu2++2e
Cu,H++e
H。
在实际电解过程中会产生一些副反应,造成电解反应与相应的原电池反应不是可逆的。因此,电解时加在两电极上的电位差要大于相应的原电池的电动势。电解电压一般为6~8V,电解质溶液pH值为5~6,电解温度范围为323~333K。
电解过程如下:
①将合成棒捣碎,放入电解料槽中;
②将电解料槽和阳极板(常用不锈钢)放入电解槽内;
③将电解液导入电解槽,调节pH值;
④通电进行电解。
在电场的作用下,电解液中的金属阳离子迁移到阴极板,生成金属单质。经过一系列的电解循环,最终使金属或合金不断解离出来。
3.7.1.2 除石墨
除石墨的方法主要分为物理方法和化学方法。物理方法主要包括磁选法、重液法、摇床法;化学方法主要是酸泡法。
(1)磁选法
人造金刚石在生长过程中,均不同程度地掺杂或包裹了催化剂材料,而国内所用的催化剂材料大部分为铁磁物质,正由于这个缘故,人造金刚石均表现有铁磁性。而石墨是非磁性物质,磁选除石墨,就是利用人造金刚石的磁性和石墨的非磁性的差异来实现的。
经过电解的物料,除金刚石外,剩下的主要是石墨和小量的叶蜡石。经烘干、研碎后进行筛分。把筛分好了的不同粒度号的金刚石混料,置于一般选矿用的磁选机上,将精矿金刚石和尾矿石墨等分离。
(2)重液法
这种方法是借助于金刚石和石墨的密度差异,前者为3.49~3.54g/cm3,后者为2.25~2.35g/cm3,在重液介质中一浮一沉来达到分离目的。所用重液为碘化钾和碘化汞的混合液。它的配比是碘化钾∶碘化汞=1.24∶1,重液密度为2.14g/cm3。
这种方法的好处是,重液可重复使用。但重液本身的价格较贵,分选效果差,而且有毒,不宜推广。
(3)摇床法
摇床选矿法通常用来选择细粒的重矿物。根据矿物的密度不同,矿物在沿斜面流动的横向水流中具有分层特性以及床面纵向的摇动作用来进行选择。
摇床是一个矩形或菱形的床面。其纵向是水平的或者稍具坡度,其横向则常为倾斜的。使床面做纵向往复摆动的传动机构装在摇床的一端。传动机构使床面做不对称的摇动。当床面前进时,最初的运动速度小,最终的运动速度大,反之,在床面做后退运动时,最初运动速度大,最终运动速度小。
(4)酸泡法
将合成料用大量浓硫酸(浓度约为96%)浸泡,使金属与石墨松散、分离,然后便可用水冲洗,冲去大量石墨。如此反复,直至剩余微量石墨。然后,在高温条件下,用高氯酸对剩余的微量石墨进行净化处理,至全部清除。
3.7.1.3 除叶蜡石
在除叶蜡石之前,要先进行金刚石整形,具体操作就是用球磨机进行研磨。研磨的目的是将金刚石连晶体分成单晶体,同时还能将粗颗粒的叶蜡石细化,便于清除。常用的除叶蜡石方法是碱除叶蜡石法。
由于叶蜡石是含水铝硅酸盐,易与碱发生反应,因此,实际生产中叶蜡石的去除方法就是碱处理法,不能使用玻璃容器。具体原理如下:
Al2O3·4SiO2·H2O+10NaOH2NaAlO2+4Na2SiO3+6H2O
叶蜡石与氢氧化钠反应,生成偏铝酸钠和硅酸盐,产物都易溶于水,所以用水即可除去。但在水洗时,随着碱浓度的降低,偏铝酸钠(NaAlO2)易水解,生成Al(OH)3白色絮状沉淀。在实际生产中,要去除Al(OH)3,先水洗至中性再加酸中和。如果加酸过早,虽然去除了Al(OH)3,但是Na2SiO3会与酸反应,生成一种硅酸聚合物胶体沉淀,不易清洗。烘干后,这种硅酸聚合物沉淀会脱水生成白色的SiO2,它是金刚石成品中经常见到的杂质。
3.7.2 金刚石的分选
人造金刚石的分选是将体提纯后的金刚石进行整形、筛分和选型,按标准划分出不同质量和粒度的金刚石。
3.7.2.1 金刚石的整形
提纯处理后的人造金刚石晶体形态各异,包括单晶体、连聚晶体(由很多微小单晶体聚合起来)以及无定型晶体等。金刚石整形处理的目的就是获得理想的形状和表面状态,主要针对连聚晶体或有缺陷的非完整单晶体。其中连聚晶体的整形处理可用球磨法或棒磨法,将其进行颗粒破碎,使其成为单晶体或等积形颗粒。对其他不规则金刚石颗粒进行钝化处理或浑圆处理,以提高金刚石的产品质量。
3.7.2.2 金刚石的筛分
金刚石的筛分是按照标准要求对金刚石进行粒度尺寸分级的过程,筛分的目的是将金刚石颗粒按大小分成若干级别,每个级别颗粒的粒径限制在一定范围内。
按颗粒尺寸可将金刚石分为磨料和微粉两类。磨料的分级常用筛分法,即采用一定孔径尺寸的筛网对金刚石颗粒进行粒度分级。筛网的孔径尺寸一般以目数表示,而目数指的是每英寸长度上被等分的线数。
我国GB/T 6406—1996将金刚石分为25个粒度等级,其中窄范围20个,宽范围5个。各个粒度号的尺寸范围以本粒度上、下检查筛的网孔尺寸范围表示。如50/60粒度表示可以通过50目筛网,而不可以通过60目筛网的金刚石粒群。各粒度尺寸范围见表3-3。
表3-3 金刚石粒度分级(GB/T 6406—1996)

将磨料级金刚石放入振筛机的筛子中,筛子有不同的筛网号,按照由细到粗的筛分顺序进行筛分。一般将筛网依筛孔尺寸的大小顺序组装起来,底部装上接料盘,将待筛料倒入顶部粗筛中,盖好上盖,将整套筛子安装在振筛机上,进行筛分。具体过程一般是从100/120起分成16/18~100/120和120/140~325/400两个粒度段,进行初筛,如图3-22所示。16/18~100/120粒度段的物料进一步通过三组筛分,完成单号粒度的分级;120/140~325/400粒度段的物料继续通过二组筛分获得单号粒度的分级。

图3-22 金刚石的筛分过程
筛网每次用过后都要用刷子进行清扫,以免筛网堵塞。筛分后的物料需要进行选型处理。
在金刚石粒度低于400目时,可以直接用微米表示金刚石的粒度,比如30-40,10-20,8-16等。
3.7.2.3 金刚石的选型
金刚石晶形分为完整晶形、等体积晶形、非等体积晶形、连晶、聚晶、破碎料等。图3-23(a)显示了部分不同晶形的金刚石。

图3-23 不同晶形的金刚石(a)和金刚石选型机(b)
①完整晶形 满足以下一点即为完整晶形:晶面、晶棱清晰,晶体生长饱满;没有两个以上的孪生或共生体;允许有1/4的缺角和晶面上有1/4的蚀坑。完整晶形的强度高、耐冲击,是理想的切磨材料。
②等体积晶形 晶体长轴与短轴比值不超过1.5。这类金刚石主要应用于高端的锯切工具中。
③非等体积晶形 晶体长轴与短轴比值大于1.5。这类金刚石强度较低,主要应用于低端的工具以及树脂结合剂工具中。
④连晶 具有两个以上共同晶面或晶棱的晶体及若干非完整晶体连生者。使用这类金刚石时应将其破碎为单晶,主要应用于低端的陶瓷结合剂工具中。
不同晶形的金刚石颗粒,其性能是不同的。经验表明,完整晶形或等积形颗粒的金刚石,其强度和耐热性总是高于非等积形的粉粒。因此,选型实际上是将金刚石分选成性能高低不同的各种牌号产品的主要方法之一。
金刚石的晶形主要通过金刚石选型机进行区分,如图3-23(b)所示,其工作原理是利用振动和摩擦的作用以及它们两者之间的相互作用和影响,从而达到人造金刚石磨料分级选型的目的。当具有一定粒度、密度、形状的被选物料,经给料振动装置的V形给料槽,按一定给料速度连续投放到振动着的具有一定振幅、一定三维空间倾斜角度、一定表面粗糙度的三角形盘面上时,因为物料和分选盘面间的摩擦阻力大小和形式不同(滑动摩擦、滚动摩擦、静摩擦),使得物料在分选盘面上沿着不同的运动轨迹前进。完整晶体的单晶颗粒沿着分选盘面较低的一边向前滚动,连晶体或针片状等不规则的单晶颗粒沿着分选盘面较高的一边向前爬行,介于两者之间的物料沿着分选盘面中间部位走完全程。经过分料漏斗,物料落入依次排列的13个集料斗中,从而达到连续分选的目的。
由于颗粒形状以及表面粗糙度不同,选型机工作时,金刚石在三角形振动分选台上的受力情况不同,会沿倾斜的台面均匀铺开,晶形越完整,越容易滚动。因此,完整晶形的金刚石会进入台面较低的收料斗内,非完整单晶体进入中间收料斗,无定形单晶体则进入台面较高的收料斗内。这样便达到了选型的目的。
3.7.3 金刚石的质量检测
我国金刚石合成自试制成功到投入工业性生产,已经走过了50多年的历史。在这段时间里,无论是产量、质量或品种都有大幅度的增长和提高,特别是金刚石的制品,更是绚丽夺目,品种繁多,用途宽阔。人们对金刚石提出了越来越多的要求,以图更大地发挥这种制品的特殊效能。由于各个领域对金刚石的需求不同,因此对金刚石的质量检测有不同的内容和指标。
金刚石的质量检测,合理取样对于准确判断一批样品的质量是非常重要的。这一环节要求取样需具有代表性。根据我国超硬材料行业取样方法标准的规定,金刚石粒度为16/20~325/400区间的样品取样采用二分器。
3.7.3.1 金刚石的粒度组成检验
将粒状物料按其大小分成若干颗粒尺寸相近的粒群的过程叫作粒度分级。各粒度的尺寸范围用公称筛孔的尺寸范围来表示,由上检查筛和下检查筛两个相邻筛网的网孔尺寸来确定,如50/60。每种粒度都是由粗粒、基本粒、细粒组成。其中,基本粒是指上、下筛网之间的粒群。基本粒群含量的高低决定着该粒度号组成的相对稳定程度。基本粒群含量愈高,该粒度的可变范围愈小,表示相对稳定程度愈高。
金刚石按照尺寸大小可分为25个粒度,见表3-3。
金刚石各个粒度的尺寸范围是以基本粒群的尺寸范围来表示的。基本粒群则是以相邻筛网的网孔尺寸来确定的。
对人造金刚石粒度组成的检测,常用拍击式振筛机(图3-24)。将所选检查筛从上到下按照筛孔尺寸由大到小的顺序组装起来,被检试样倒入上部粗筛中,筛分过程保证筛机运动自如。待筛分完成后,从上层开始,依次对各筛中样品进行称量。对于粗筛,可用软刷轻轻刷掉嵌在筛网中的颗粒,对于细筛则要定期使用超声波清洗机进行清洗。各筛中的样品按总样品重量的百分比来表示。

图3-24 拍击式振筛机
3.7.3.2 金刚石的强度检验
金刚石的强度是衡量金刚石质量优劣的重要参数之一。对于磨料级金刚石的强度检测能反映其实际使用的效果,并能指导实际工业生产。
(1)抗压强度
抗压强度是指单颗粒金刚石受静态压力破碎前的负荷值。目前,工业上采用单颗粒抗压强度测定仪进行检测,如图3-25所示。每个试样需要连续测量40粒,取其负荷值的平均值作为该样品的单颗粒抗压强度。一般来说,金刚石颗粒尺寸越大,抗压强度越高,因此,对于某一粒度范围应以基本粒级进行测定。

图3-25 单颗粒抗压强度测定仪
影响抗压强度测定的因素有很多,除了颗粒尺寸,还包括颗粒形状、颗粒表面状况以及晶格缺陷等。因此,抗压强度的测量误差较大,可重复性差。国外有通过测定金刚石的冲击韧性来进行质量检验的方法。该方法金刚石的受力情况与实际金刚石使用的情况更接近。
(2)冲击强度
我国冲击强度的测定应用冲击韧性测定仪。将钢球和已筛分的样品装入试样管中,如图3-26所示,在一定的冲击速度和次数条件下进行试验,结束后求其破碎率。冲击韧性以未破碎率为50%时的冲击次数进行表征。

图3-26 冲击强度测试原理
在进行冲击强度测定时,要求一个钢球最大累计冲击次数为12000次,试样管内的硬质合金垫片单面最大累计冲击次数为24000次。同一试样的测定要求使用同一个钢球。
3.7.3.3 金刚石的堆积密度
堆积密度是指样品在自然堆积的情况下,单位体积所含样品的质量,单位为g/cm3。
它是最常用的表示粉末样品填充特性的物理量,是金刚石等磨料密度、粒度组成、颗粒形状等性能的综合反映。该方法适于测定16/20~325/400粒度区间的金刚石。
影响样品堆积密度测定的因素也有很多,具体如下:
①颗粒大小 一般来说,样品粒径越小,堆积密度越小。
②粒度分布 样品的粒度分布范围宽,则堆积密度大。
③颗粒形状 样品的颗粒形状越不规则,则堆积密度越小;样品越接近等积形,则堆积密度越大。
④颗粒间相互作用 样品表面越粗糙,则摩擦力越大,附着力越强,越易产生颗粒粘接,堆积密度越小。
3.7.3.4 比磁化系数
比磁化系数是样品的磁化系数与质量的比值,即样品单位质量磁化率。它是一种有效的无损检测人造金刚石中杂质(尤其是包裹体)含量的方法。其测定方法有很多种,如磁导计冲击发、等磁力天平法、磁力天平法等。国外早已把其纳入金刚石的质量检测标准。
该方法可以通过改变磁场的强度将金刚石进行磁性分离:强磁性、中磁性、弱磁性以及非磁性等。金刚石的磁性强,比磁化系数较大,杂质的含量越高;反之磁性越小,比磁化系数越低,杂质也越少。