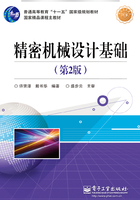
5.4 凸轮机构基本尺寸的确定
设计凸轮机构不仅要满足从动件的运动规律,而且要求传动时受力情况良好,以使机构运转灵活,结构紧凑。因此,需要正确选择凸轮机构的压力角、基圆半径及滚子半径,现讨论如下。
1.凸轮机构的压力角和自锁

图5-11 凸轮机构的压力角
压力角是决定凸轮机构能否正常工作的重要参数,确定凸轮机构尺寸时必须考虑对压力角的影响。图5-11为滚子直动从动件凸轮机构。凸轮机构与连杆机构一样,从动件运动方向和接触轮廓法线方向之间所夹的锐角称为压力角。当不考虑摩擦时,凸轮给从动件的作用力F是沿法线方向的,从动件运动方向与作用力F之间的夹角α即压力角。作用力F可分解为沿从动件运动方向的有用分力F′和使从动件紧压导路的有害分力F′,即
F′=Fcosα (5-5)
F′=Fsinα (5-6)
压力角α越大,则有害分力F′越大,由F′引起的摩擦阻力也越大。当α增大到一定程度,由F′引起的摩擦阻力大于有用分力F′时,无论凸轮给从动件的作用力多大,从动件都不能运动,这种现象称为自锁。
由以上分析可以看出,为了保证凸轮机构正常工作并具有一定的传动效率,必须对压力角加以限制。凸轮轮廓曲线上各点的压力角是变化的,在设计时应使最大压力角αmax不超过许用值[α]。根据实践经验,推程许用压力角推荐取以下数值:直动从动件,许用压力角[α]=30°;摆动从动件,许用压力角[α]=45°。
常见的依靠外力维持接触的凸轮机构,其从动件是在弹簧或重力作用下返回的,回程不会出现自锁。因此,对于这类凸轮机构,通常只需对其推程的压力角进行校核。
2.压力角与基圆半径的关系

图5-12 压力角与基圆半径的关系
凸轮基圆半径和凸轮机构压力角有关,由图5-12可知:
式中:v2为从动件的线速度;sB为从动件在B处的位移。
由式(5-7)可知,基圆半径rb越小,压力角α越大。若基圆半径过小,压力角就会超过许用值。反之,基圆半径rb越大,压力角α就越小,但整个机构的尺寸也就越大,这将使结构不紧凑。故实际设计中,在保证凸轮机构的最大压力角不超过许用值的前提下,将α取大一些,以减小基圆半径rb的值。
若对机构尺寸没有严格限制,则基圆半径可取大些,以使α减小,改善凸轮受力情况。基圆半径通常可根据结构条件,由下面的经验公式确定:
rb≥(0.8~1)dz (5-8)
式中:dz为凸轮安装处的轴颈直径,单位为mm。
在根据所选的基圆半径设计出凸轮轮廓曲线后,必要时可对其实际压力角进行检查。若发现压力角的最大值超过许用压力角,则应适当增大rb,重新设计凸轮轮廓。
3.滚子半径的选择
滚子半径的选择要考虑滚子的结构、强度和凸轮轮廓曲线的形状。从减小凸轮与滚子间的接触应力来看,滚子半径越大越好,但滚子半径增大后对凸轮实际轮廓曲线有很大影响,从而使滚子半径的增大受到限制。如图5-13所示,对于外凸的理论轮廓曲线,由于实际轮廓曲线的曲率半径等于理论轮廓曲线的曲率半径与滚子半径之差,设理论轮廓外凸部分的最小曲率半径以ρmin表示,滚子半径用rT表示,则相应位置实际轮廓的曲率半径ρ′=ρmin-rT。
当ρmin>rT时,如图5-13(a)所示,这时ρ′>0,实际轮廓为一平滑曲线。
当ρmin=rT时,如图5-13(b)所示,这时ρ′=0,在凸轮实际轮廓曲线上产生了尖点,这种尖点极易磨损,磨损后就会改变原定的运动规律。

图5-13 滚子半径的选择
当ρmin<rT时,如图5-13(c)所示,这时ρ′<0,产生交叉的轮廓曲线,交叉部分在实际加工时将被切削掉,使这一部分运动规律无法实现,因此从动件的运动将会失真。
由上述分析可知,为了使凸轮轮廓在任何位置既不变尖也不相交,滚子半径rT必须小于外凸理论轮廓曲线的最小曲率半径ρmin。另外,滚子半径rT必须小于基圆半径rb。设计时应使rT满足以下经验公式rT≤0.8ρmin和rT≤0.4rb(5-9)