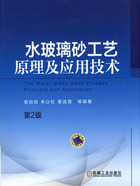
1.1.1 CO2吹气硬化水玻璃砂
CO2吹气硬化水玻璃砂(简称“CO2水玻璃砂”)自20世纪50年代引入铸造工业以来一直是最被广泛采用的工艺,此法既可用于大量生产和单件小批量生产的铸型制造,也适用于大、小泥芯的生产。普通CO2水玻璃砂工艺,大都由纯净的人造(或天然)硅砂加入6.0%~8.0%[1]的钠水玻璃配制而成。对于几十吨的大型铸件或质量要求高的铸钢件砂型(芯),全部面砂或局部采用镁砂、铬铁矿砂、橄榄石砂、锆砂等特种砂代替硅砂较为有利。为了使水玻璃砂具有一定的湿强度和可塑性,以便脱模后再吹CO2硬化,可加入1%~3%的膨润土或3%~6%的普通黏土;为了改善水玻璃砂的溃散性或出砂性,可加入一定量(通常为1%~5%)的溃散剂或溃散性物质(如木屑、石棉粉等)。
水玻璃砂可采用各类混砂机混制,如辗轮式混砂机、叶片式混砂机等。混好的砂通常放在有盖的容器内或覆盖有湿麻袋的场地待用,以免砂中的水分挥发和与空气中的CO2接触而硬化。
水玻璃砂具有良好的流动性,造型、制芯时可采用手工紧实,也可采用振动紧实。通常是吹CO2气体硬化后起模;再硬化一定时间后,组芯、合箱等再浇注。
CO2吹气硬化的方式也多种多样。有插管吹气法、盖罩吹气法等(工艺装置详见第3章)。要求CO2能迅速均匀地进入型(芯)的各个部位,以最少的CO2消耗量达到均匀硬化型(芯)各部位之目的,避免出现不能硬化(或硬化不良)的死角。
普通CO2水玻璃砂工艺的缺点:水玻璃加入量较多(7.0%~9.0%),溃散性较差,旧砂再生困难;硬化过程不太稳定,会使铸型(芯)产生“过吹”现象,导致铸型(芯)强度的下降;对于大型铸件的型(芯)表面易粉化,而内部又难以硬透,使铸件形成夹砂、鼠尾、砂眼等缺陷;型(芯)砂的吸湿性较强,在湿度较大的天气下,贮放的稳定性较差。
普通CO2水玻璃砂工艺中,CO2不能被充分吸收、消耗量大,同时常出现硬化不均匀的现象。真空CO2吹气硬化水玻璃砂克服了普通CO2吹气硬化水玻璃砂的某些缺点,它是CO2吹气硬化水玻璃砂工艺的技术进步。
真空CO2吹气硬化水玻璃砂工艺(Vacuum Replace Hardening),简称为VRH法,是于1982年由日本人小林一典研究发明的。VRH法是把真空V法与CO2水玻璃砂工艺结合起来形成的一种“物理-化学”硬化法。它是将造型紧实后的水玻璃砂型(芯),连同模板一起送入一真空箱内抽气,当达到一定的真空度后,向箱内通入CO2气体,几分钟后铸型(芯)即可硬化达到一定的强度。铸型(芯)从真空箱内取出、进行起模,2~4h后即可浇注。
CO2吹气硬化之前对型(芯)抽真空,有两个优点:一是抽真空时,水玻璃中的水分蒸发,促使水玻璃脱水硬化;二是砂粒间隙中的空气几乎被抽净,当通入CO2时,气体迅速进入间隙中与砂粒表面的水玻璃均匀反应,进一步使之硬化。由于VRH法是一定真空度的条件下,CO2气体以极高的浓度与水玻璃接触,反应充分、迅速、均匀,用较少的水玻璃和CO2气体即可达到足够的铸型(芯)强度。VRH法的水玻璃加入量可降至3%~4%,CO2气体的消耗比普通CO2水玻璃砂工艺减少1/2~2/3。因此,VRH法既是来源于普通CO2水玻璃砂的工艺,又是优于普通CO2水玻璃砂的工艺。
VRH法的缺点是设备投资大,操作和维修要求严格,固定的真空室尺寸对于不同大小和不同形状型(芯)的适应能力差,因而制约了该工艺的广泛应用。
除VRH法外,用空气稀释的CO2吹气硬化(用“约10%CO2+约90%空气”的混合气体吹气硬化),加热的CO2吹气硬化(吹入铸型内前,将CO2加热至30~60℃),脉冲CO2吹气硬化(采用间隔脉冲方式吹入CO2气体)等,这些都是CO2水玻璃砂工艺的改进。有人将普通的和改进的CO2水玻璃砂工艺统称为“第一代水玻璃砂工艺”。
CO2水玻璃砂工艺的应用经过了发明初期的快速增长后,由于其缺点逐步被认识,加之自硬树脂砂的发明及应用(20世纪60年代)和黏土砂技术的改进及发展,取代了部分水玻璃砂工艺。一些国家CO2水玻璃砂工艺的应用迅速减少。但在我国,CO2水玻璃砂一直是生产铸钢件的主力型砂种类。