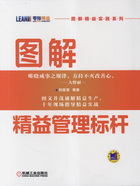
三、改善和现场管理
(一) 改善和现场管理的关系
1.何谓改善(KAIZEN)
改善就是将现状向目标靠近(甚至超过目标)的各种方法及手段运用的集合。
改善是一种对工作的细节内容加以研究、分析、简化、决定其有利的顺序并予以重新组合的技巧集合。

2.现场与管理
现场生产顾客满意的产品,才能使公司得以生存和发展。公司里的各个阶层——高级管理阶层、中级管理阶层、工程师及现场管理人员,都是为了提供现场必要的支援而存在的现场是改善的场所,也是信息的来源。为了解决现场发生的问题,管理阶层必须密切接触现场的实情,即不论管理阶层提供什么样的协助,都应是源自现场的需求。
3.改善与管理
在改善的范畴里,管理活动有两项:①进行工作的指派,使每一个人都能依照标准的程序来工作;②进行以改进现有标准为目标的活动。因此,可以总结为维持标准和改进标准。
改进又可区分为“改善”和“创新”。所谓“改善”,是由于持续不断的努力而产生诸多小改进,逐次累积形成的。“创新”则是借助大笔资金投入到新技术或设备,而产生戏剧性的变化的改进。一些管理人员往往执着于“创新”,他们既没有耐心,又忽视了“改善”能长期带给公司的利益。相反,“改善”则是强调要以员工的努力、士气、沟通、训练、团队参与及自律来达成目标,这些都是一些常识性和低成本的改进方式。
(二) 现场改善的内容与原则
1.现场改善的内容
现场改善是综合性的现场管理优化,内容十分丰富,几乎可以包括企业管理的所有内容从优化现场的角度看,它包括以下内容:作业管理;物流管理;文明生产与定置管理;质量管理;设备管理;成本控制;计划与控制;优化劳动组织与班组建设;岗位责任制;生产现场管理诊断等 。
2.现场改善的原则
(1)科学管理原则
各项工作应按科学的方法进行,改变凭经验领导生产、 组织生产的状况。从产品的设计加工、装配工艺与方法,机器、设备、工具的使用,工厂的布置与物料流动,原材料的使用,到工人的操作方法,都要讲究科学性,建立作业标准、时间标准,作业指导书要规范化标准化。只有这样,才能实现优质、高效、低耗、均衡 、安全、文明的生产,才能保持和发展企业的应变能力和竞争能力。
(2)经济效益原则
要树立经济效益原则思想,取代只抓产量、不计成本,只讲速度、不讲效率和效益的单纯生产观点。应根据市场和用户的需求选择产品,在生产过程中要坚持高质量、低消耗、低成本,以少的投入换取大的产出的经济效益原则。
3.现场改善的作用
现场改善是优化各种生产要素的技术,其主要作用体现在现场改善任务中。系统归纳现场改善的作用与目的,主要体现在两个方面:
(1)消除浪费,降低成本。这也是现场改善的作用与目的。
(2)使异常易于发现。通过现场的深入分析,发现问题并进行改善,最终形成标准化,使将来的各种不合理现象与问题能被容易地及时发现。
(三) 改善的意识
“发现问题,改进绩效”,因此要进行现场改善,首先得发现问题。如果认为没有什么问题,又谈何改善?所以,首先应具备改善的意识。下面谈谈现场改善应具备的三大意识。
1.“现场、现物、现实”的意识
“现场”是指问题发生的场所;“现物”是指对发生问题的对象进行确认;“现实”是指实实在在地进行分析,找出真正的原因。
所谓现场意识,就是把现场看作问题发生的根源、管理水平提升的基石。
所谓现物意识,就是认为现场的问题往往有形有据。哪里发生了问题,对什么造成了影响,都应该加以明确。
所谓现实意识,就是放弃完全凭经验和感觉,工作中注重数据和事实。
2.“及时、及早、及至”的意识
“及时、及早、及至”就是一种时间意识,强调及时应对、及早预防、即刻处理(及至)没有强烈的时间观念,只会让问题一拖再拖 。
及时应对的意识是要明确改善的时机,并及时对进展予以反馈。
及早预防的意识是要防患于未然,事先建立坚固扎实的预防差错的防线。
及至的意识是能迅速、正确地开展工作,遇到突发异常时不会手忙脚乱。
3.“问题、方法、协调”的意识
现场有许多问题,若看不出问题,也就谈不上改善。光有改善的愿望,没有改善的技能不会运用合适、有效的方法,也只能“有心无力”。除了有愿望、有能力,还要有气氛。现场管理也需要造势,需要配合,这就是协调意识。
塑造良好的现场气氛,养成积极的问题意识,掌握有效的改善方法,才能充分调动和发挥人的积极作用,形成企业进步的原动力。
4.改善的三视点

5.改善的理解误区
不要把日常管理的维持当成改善行动。日常管理的内容主要包括:
(1)异常情况的处理。
(2)品质问题的解析。
(3)重要特性值的测定与评价。
(4)出现异常或问题要报告。
(5)日常文书的处理。
(6)以身作则遵守公司和部门的规定。
6.改善的理解误区

7.何谓问题
问题就是现状与目标之差。得以生存的企业既不是最强的,也不是最聪明的,而是对变化最敏感的。
(1)产生问题的三种基本情形
1)没有按规定去做(规定被违反)。
2)没有规定(应该遵守的规则或应该做的工作没有被规定)。

3)即使按规定去做了,但还是发生了问题。
(2)培养发现问题的能力的基础(发现问题的能力不是天生的)
1)了解本部门的标准。
2)熟悉本部门的日常业务。
3)掌握本工段的作业内容。
4)掌握本工段的特别规定。
(3)改善意识形成的根本
问题是促使改善开始的原动力。因此,问题意识是改善意识形成的最根本的保证。不能发现问题就是最大的问题。
(4)改善的八条基本精神
1)思考问题的方法要不断提高。
2)立即行动。
3)改善≠花钱,重要是运用智慧。
4)只要肯动脑筋,就能打开创意的大门。
5)过多地强调理由是不思进取的表现,学会在不可能之中寻找可能。
6)虚心接受批评,立即纠正错误。
7)不要抱有一步登天的幻想。
8)改善是没有尽头的。
(四) 现场管理的常用改善方法
1.“三直三现”法
“三直三现”即“直接现场、直接现物、直接现实”。其目的是帮助生产现场的管理者端正正确的管理作风,准确把握问题、查明真相,实施最有效的对策,到现场解决实际问题。

2.“5W2H”法
这是一种综合分析的方法,适用于解决问题。
什么事情(What)? 什么地方(Where)? 什么时间(When)?
什么人(Who)? 什么原因(Why)? 怎样做(How)?
成本和代价是什么(How Much)?

3.目视管理
目视管理即通过视觉引起人的意识变化的一种管理方法。
目视三要素:无论是谁都能判明是好是坏(异常),能迅速判断,精度高,判断结果不会因人而异。
目视的三个水准:
初级水准:有表示,能明白现在的状态。
中级水准:谁都能判断良否。
高级水准:管理方法(异常处置等)都列明。

4.PDCA循环
它是由美国戴明博士提出的,也称戴明环,即计划(Plan)-执行(Do)-检查(Check)-处理(Act)闭环管理,环环相扣,持续改进。

5.管理看板
管理看板是管理可视化的一种表现形式,即对数据、情报等状况一目了然地表现,主要是对管理项目,特别是情报进行的透明化管理活动。它通过各种形式,如标语、现况板、图表、电子屏等,把文件上、脑子里或现场等隐藏的情报揭示出来,以便任何人都可以及时掌握管理现状和必要的情报,从而能够快速制定并实施应对措施。因此,管理看板是发现问题解决问题的非常有效且直观的手段。

6.定置管理
定置管理即为确定物品等的位置进行分类标识,以便易于找寻。应做到有物必有区有区必分类,分类必挂牌。人和物有两种结合方式:一是直接结合,这类情况较少,如个人用的钢笔、眼镜等;二是间接结合,只有通过一定的信息才能结合。人和物有三种结合状态:A状态,即人和物处于紧密结合状态,人需要的物随手可以拿到,物和人结合得非常紧密;B状态,即人和物处于寻找状态人需要物的时候不能随手拿到,需要到处寻找,要浪费一些时间才能找到;C状态,即存在对人不起作用的物,或者现场不需要的物定置管理的目标就是消除C状态,不断改善B状态,使其达到A状态,尽量保持A状态。

7.5S管理
5S是整理、整顿、清扫、清洁、素养的简称。5S活动是一项基本活动,是现场一切活动的基础。整理,即将工作场所的任何东西区分为有必要的与不必要的,把必要的东西与不必要的东西明确、严格地区分开来,将不必要的东西尽快处理掉。整顿,即对整理之后留在现场的必要的物品分门别类放置,排列整齐,明确数量,有效标识。清扫,即将工作场所清扫干净,保持工作场所干净、明亮。清洁,即将上面3S实施的做法制度化、规范化。素养,即通过晨会等手段,提高员工的文明礼貌水准,增强团队意识,养成按规定行事的良好工作习惯。

8.TPM管理
为了解决设备运行过程中的诸多问题,美国对维护设备的经验进行了总结,将装备出现故障以后采取应急措施的事后处置方法称为“事后保全(BM)”,将装备在出现故障以前就采取对策的事先处置方法称为“预防保全(PM)”,将为延长装备寿命的改善活动称为“改良保全(CM)”,把为了制造不出故障不出不良的装备的活动称为“保全预防(MP)”,最后将以上BM、PM、CM、MP四种活动结合起来称为“生产保全(PM)”,这就是TPM的雏形。第二次世界大战后,日本在向美国学习的过程中,将美国的PM生产保全活动引入日本,成功地创立了日本式PM,即“全员生产保全(TPM)”。因有80%~90%的员工都参与了此项活动于是在PM前加了"T",正式将该公司的PM活动命名为TPM。
21世纪迎来企业特色化的经营革新管理活动
[TPM+TPS、PM+IE、TPM+6Sigma、TPM+JIT…]→ PRO-TPM


9.JIT管理
(1)何谓精益生产?
精益生产(Lean Production)是美国麻省理工学院(MIT) 国际汽车计划组织(IMVP)的教授詹姆斯·沃麦克(James P.Womack)对日本“丰田JIT(Just in Time)生产方式”的赞誉之称。其核心思想是“在必要的时间以最低的成本完成必要数量的必要产品”。
9.JIT管理
(2)丰田发展历史
1)丰田佐吉。1896年,丰田佐吉发明了日本有史以来第一台不依靠人力的自动织机,即“丰田式气动织机”,经过研究和改良,于1923年发明了G型自动织机,即“自动换梭丰田自动织机”。自动织机在出问题的情况下会自动停止,这就发展为日后丰田生产系统(Toyota Prodnction System,TPS)两大支柱之一的自化。
2)丰田喜一郎。丰田喜一郎是丰田佐吉之子。受父亲启发,丰田喜一郎到美国福特公司学习,回国后,于1930年开始研究开发小型发动机;1933年在“丰田自动织机制作所”内设立汽车部; 1937年汽车部门正式独立出来,成立了“丰田汽车工业株式会社” 。
3)大野耐一。第二次世界大战中日本战败,20世纪50年代初的丰田面临濒临破产的经营危机和严重的劳资纠纷,丰田家族被迫交出绝大部分股份交与银行托管,银团紧急融资提出的苛刻条件,进一步迫使丰田放弃规模制造模式,以接近零库存的订单拉动式组织生产。1953年,副总裁大野耐一正式提出建立这套原本并不适合大批量生产方式与实时现场管理的准时管理系统(Just in Time)。

丰田喜一郎

大野耐一
大野耐一先在自己负责的工厂实行一些现场管理方法,如目视管理、一人多机、U形设备布局等。随着大野耐一的管理方法取得初步实效,他的周围同时也聚集了一些人,进一步推进变革。他们通过对生产现场的观察和思考,提出了一系列革新措施,如三分钟换模法、现场改善自化、五个WHY、看板拉动式生产等。在不断完善中,最终建立起一套丰田生产方式(TPS)
总的来说,TPS就是在丰田喜一郎的准时化思想的指导下,由大野耐一等人在现场具体实施、不断改善的产物。它的最终目标是更高品质、更低成本、更短周期和更大效益。
(3)丰田汽车的经营实绩
2003年,美国前三大汽车制造商的股价下跌,丰田汽车公司股价却比2002年上涨了24%。截至2003年,丰田的市值为1050亿美元,比福特、克莱斯勒、通用三家汽车公司的市值总和还要高。丰田汽车公司的资产报酬率比汽车业平均报酬率高出8倍。在之前的25年中,该公司年年获利,而且手中总是维持200亿~300亿美元的经营现金。
丰田自2008年起,逐步取代通用汽车公司,成为全世界排行第一的汽车制造商。不可思议的是,丰田的利润率是行业平均值的3倍。2012年4月1日——2013年3月31日,全球销售量969万辆,全年经营利润增长64%。
9.JIT管理
(4)精益生产的七个“零”目标
丰田CCC 21计划:4年降低100亿美元,喇叭28个零件减少6个,全部90种车型只有3种手把。


10.精益目标管理
(1)先有工作,还是先有目标?
先有目标,才能确定每个人的工作。战略和任务必须转化为目标,如果一个部门没有目标,这个部门就可以推卸责任或者被忽视。当目标绩效准确评价后,没有目标则没有改善。
绩效=结果+改善过程(行为+素质)
目标绩效=目标+结果+改善(活力)
(2)目标管理的推进步骤

(3)精益目标管理的构造体系

(4)精益目标目视管理及点检

