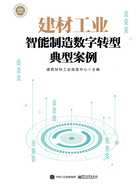
05 建筑陶瓷工业互联网智能制造工厂——山东统一陶瓷科技有限公司

企业简介
山东统一陶瓷科技有限公司成立于2003年12月,主要产品涵盖功能陶瓷、民用陶瓷地砖,是一家集创新、研发、设计、生产、销售于一体的高附加值高新技术企业。2020年公司接入海尔集团旗下的工业互联网生态平台卡奥斯,成为建陶行业首家入选企业。
公司自主创立的品牌“瓦伦蒂诺”被国家工商总局认定为“中国驰名商标”“山东省著名商标”“山东名牌”。公司先后被认定为“山东省高新技术企业”“山东省院士工作站”“山东省企业技术中心”“山东省工业设计中心”“山东省‘专精特新’中小企业”等,被誉为引领陶瓷行业走向创新之路和转型升级快车道的模范。
案例实施情况
总体设计
本着高起点规划、高标准建设、高效能管理的原则,该公司以自动化+信息化的双核机制积极拥抱工业互联网,在自动化端引入全新自动化装备,在信息化端以U8 ERP+科达IOT+科达MES为核心信息化中枢,通过对自动化的设备联网、能源管理、数字化生产,打通设备层—执行层—管理层的信息化链条,将各系统数据汇聚到数据分析平台,进行数据汇聚分析,实现赋能业务,提供决策支持,让数据产生价值,以集成化、数字化、智能化手段解决生产控制、生产管理、营销、经营等问题,提高能源利用率,最终打造陶瓷行业的绿色生产车间。
实施内容与路径
(1)陶瓷砖智能化车间的生产线建设:包括制粉、干燥、成型、施釉、烧成、拣选、自动化包装生产线等。
(2)核心短板装备的研制:用于陶瓷砖生产过程中大规格砖联动生产线与后包装设备。

建筑陶瓷工业互联网智能制造工厂架构图
(3)车间网络及基础设施建设:采用分层网络架构(骨干层、传输层、接入层)建设内网设施,并专门建设车间工控网,两者之间采用工业安全网关进行隔离。建设覆盖加工设备、在制产品、物料、人员、控制系统和生产管理信息系统的无线网络,并实现有线网和无线网的结合,为实时生产数据和信息的互联互通提供网络基础。建设智能化车间的机房等设施,对服务器、数据库等软硬件基础设施进行选型和布置。
(4)MES制造执行系统:通过陶瓷砖生产过程中物料管理、工艺管理、称重管理、电子批发记录、生产任务申请、质量追溯、设备管理、生产批报表管理、工参数管理、生产监控、人脸识别,使得陶瓷砖生产信息可视化,从而监控、协同、调度、分析、预警制造执行过程,实现管控一体化。同时与计划层和控制层进行信息交互,通过企业的连续信息流实现信息全集成,提高车间流水线生产效率,降低生产成本。
(5)大数据分析平台:建立大数据分析平台,自动抽取企业各信息系统、生产运营系统、生产监控系统、生产自动化控制系统产生的海量数据,经过自动清洗、数据组织、数据分析,组成工业大数据平台,形成一套工业数据仓库。
(6)产品在线检测系统:通过近红外光谱技术,实现陶瓷砖生产过程检测。实现检测数据的实时监控和数据采集、分析与处理。
(7)数据采集与监控系统(SCADA):对生产、物流单元、生产环境智能控制系统、生产智能供应与调度系统的生产工艺类数据、生产用公共工程类设备数据、能源系统类设备数据进行采集、监控、分析与报警。
(8)智能仓储管理系统:主要包括出入库管理、订单管理、物料盘点、质检管理、货位管理。系统接口模块(TINF)、物流管理模块(TM)、物流调度模块(TDCS)三大模块,分别实现与外围信息系统的接口、物流管理层和物流调度层相对应的功能。
(9)远程监控系统:采用中控大屏幕CRT实时监控动态仿真技术来实现对车间运行过程的安全监控和仿真,建立可以对生产现场进行实时监控的中央控制室。
(10)能源及排污管理系统:能源及排污管理系统是对涉及水、电、汽等相关能源或介质的计量和管理,建立能源管理与决策系统,实现对各种能源介质和重点耗能设备的实时监控、控制、优化调度和综合管理,及时了解和掌握各种能源介质的生产、使用及关键耗能设备的运行工况,对设备能效及能源实绩进行分析。在线检测废水、废气、废渣的指标,对排污过程进行监管。
(11)质量管理系统(QMS):通过对设计质量、供方质量、生产质量、试验量、计量理化、售后质量等进行管理,实现对产品全过程的精细化和智能化质量控制。
(12)企业资源计划系统(ERP):在生产信息化的基础上,通过对整个企业信息系统的整合,实现陶瓷砖生产过程中信息流、资金流等数据的统一管理与优化,提高企业的生产效率。
(13)实验室信息管理系统(LIMS):主要功能模块包括样品管理、检验记录、仪器数据、文件管理、稳定性试验、方法验证、分析和报告。
(14)系统集成:规划了智能化车间MES、智能仓储管理系统、LIMS及ERP的数据接口,通过对管理控制软件的协同集成,实现覆盖产品全生命周期的全流程智能化车间智能制造。全流程制造信息集成中心为工厂级别的综合管控平台,利用设备互联与集中监控,LIMS、智能仓储管理系统、MES、设备管理系统等在设计时预留的第三方信息接口进行集成,将信息进行整合,实现对生产车间全流程、全方位的管理,实现智能化车间可视化统一调度与监控。
(15)实施路径:对生产线生产设备的物联数据采集,进行信息化升级,实现全过程产量数据的实时监控,并对核心生产设备压机、干燥窑、烧成窑、抛光机等设备运行参数、工艺参数进行数据统计分析,有利于后续构建智能化业务应用分析平台,辅助管理决策,提高生产效率,优化生产管理流程。
案例特点
针对建陶企业普遍小、散、乱、杂,行业附加值低、库存高、耗能高、污染高等痛点,对建陶行业进行数字化智能化改造,可有效提高企业生产效率、降低库存周转率,对能耗、污染排放进行实时监控预警。建筑陶瓷大多连线生产,生产线自动化水平高,有利于智能化改造的推广。改造之后,能源利用率提高了12%,产品优等率提高了0.5个百分点,企业利润率提高了10%。由此所带来的效率提升,将帮助企业解决由环保、人工等因素带来的成本上升问题,实现可持续发展。
实施效果
生产线经过智能化改造后,实现了MES制造执行系统、大数据分析平台、产品在线检测系统、数据采集与监控系统(SCADA)、质量管理系统(QMS)、企业资源计划系统(ERP)、实验室信息管理系统(LIMS)与公司现有信息化技术的融合,实现了复杂工业现场的数据采集、过程监控、设备运维与诊断、产品质量的跟踪追溯、优化排产与在线调度、污染源实时监测。较之前相比能耗节约了5%,减少二氧化硫排放量4.79吨,达到节能减排的目的。生产效率提高25%,产品不合格率降低22%,节约人工10人,实现了订单式定制,库存最优化甚至达到“零库存”,节约了资金占有,库存周转率提高了13个百分点;降低单位产品能源消耗,能源利用率提高12%,SCADA可实现全线预警处置,大大提升了安全防控水平。
该公司打造陶瓷工业互联网智能制造工厂,探索建陶行业生产新模式、新业态。该公司将生产工艺与数据融合,增强生产设备的自主控制,把分散的、自主智能化的制造设备,通过网络的形式紧密地连接在一起,即用技术手段实现人为控制在时间、空间等方面的延伸,实现人、机、物的融合,实现了工业互联网智能化改造,推动了建陶行业由制造型向智造型的转型升级。通过工业互联网的有效链接,可满足海量消费者的个性化需求,能够实现以消费者为中心的商业模式,同时实现网络化的工厂间大规模协作,这是对建陶行业发展模式的重大创新。通过平台合作模式,有效对接了国际顶尖研发资源,实现了新产品的快速研发迭代,彻底打破行业技术壁垒,推动行业发展与商业模式的创新,能够在建陶行业和其他生产型行业领域快速复制与推广应用,具有很好的示范作用。