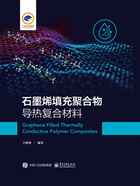
2.2 石墨烯的制备方法
石墨烯是一种由六角碳原子构成的单层结构,自2004年Novoselov[1]等通过对石墨进行重复剥离成功地剥离出单层石墨烯以来,人们对石墨烯的制备进行了广泛的研究。石墨烯的制备手段大致可分为自下而上(Bottom-Up)的化学合成手段和自上而下(Top-Down)的物理剥离手段。本节将重点论述利用这两种手段制备出的石墨烯的优缺点。
2.2.1 自下而上的方法
自下而上的方法是以较小碳源的物质为前驱体,通过对这类前驱体进行化学组装而形成石墨烯。自下而上的方法的优势为可实现精确合成控制。由于石墨烯可以由较小的碳前驱体构建,因此可以对最终合成的具有锯齿形或扶手椅结构的石墨烯带进行原子级精确控制,从而影响最终获得的石墨烯成品的电子行为[2]。对石墨烯的精确控制使得人们能够对这类新型碳材料进行详细的研究,但是由于需要大量长步骤的化学反应,因此制备所需长度的石墨烯纳米带(>200nm)仍然是一个挑战[3]。与自上而下的方法相比,自下而上的方法的缺点包括成本较高、产量较低及难以扩大规模。除此之外,自下而上的方法(如化学气相沉积法、外延生长法和有机合成法)的困难是如何将最终的石墨烯产品转移到所选的基板上。典型的自下而上的方法(如化学气相沉积法、外延生长法)用于合成较大尺寸的石墨烯(最大为几平方厘米),而有机合成法通常用于合成纳米尺寸的石墨烯(带)。
2.2.1.1 化学气相沉积法
化学气相沉积(Chemical Vapor Deposition,CVD)法是将CH4、C2H2等含碳气体作为碳源,将其高温裂解成碳原子后吸附在金属表面(如Cu),或者先将其溶解在金属基体(如Ni)中,然后在降温过程中从表面析出,形成石墨烯[4,5]。近些年来,CVD法的发展主要体现在针对基底材料和转移条件进行改进。①在基底材料的选择方面,使用不同的金属进行实验室石墨烯的制备,最终发现铜基底具有表面生长机制,析出的石墨烯纯度高。研究人员在对铜基底(诸如复合基底、铜箔、铜网等)进行改进的过程中发现,不同的基底材料会生成不同质量的石墨烯,因此,可以根据所需产品来选择对应的基底材料。同时,人们还研究了CVD法中的生长温度、生长时间、碳源、气体流量和压强等制备条件对石墨烯生长的影响规律。②在转移条件方面,传统刻蚀方法会造成石墨烯材料的浪费。近年来,科研人员研究出多种利用其他辅助材料进行转移的方法,诸如采用聚甲基丙烯酸甲酯、聚二甲基硅氧烷或热熔胶带等作为辅助材料,之后将基底刻蚀掉并去除辅助材料,进而获得石墨烯材料。
图2.1所示为石墨烯制备过程:CVD生长、Ni基底刻蚀及转移[6],其中,图2.1(a)表示在薄镍层上合成图案化石墨烯薄膜,图2.1(b)表示使用FeCl3(或酸)蚀刻并使用PDMS印模转移石墨烯薄膜,图2.1(c)表示使用BOE或氟化氢(HF)溶液蚀刻和石墨烯薄膜的转移。利用这种方法可以获得大面积、高质量的石墨烯,并且可以通过选择不同种类和尺寸的金属基底,以及碳源的量来控制石墨烯的厚度及面积,实现了对石墨烯的可控制备,并且其产量较机械剥离要高得多,但是离批量生产还有一定的距离。

图2.1 石墨烯制备过程:CVD生长、Ni基底刻蚀及转移[6]
采用CVD法制得的石墨烯的微观表征[6]如图2.2所示。图2.2(a)为在300nm的薄镍基板上生长7分钟制备的石墨烯薄膜的扫描电子显微镜(SEM)图像,该图像显示具有不同石墨烯层数的区域之间的明显对比。图2.2(b)为透射电子显微镜(TEM)图像,显示该薄膜主要由少层石墨烯组成。将薄膜转移到具有300nm厚的SiO2层的硅基板后,利用光学和共焦扫描拉曼显微镜获得相同区域的图像[见图2.2(c)和图2.2(d)]。图2.2(d)中最亮的区域对应于单层,最暗的区域由10层以上的石墨烯组成。双层结构似乎在这个特定样品的TEM图像和拉曼图像中占主导地位。研究发现,石墨烯层数、畴尺寸和基板覆盖率可以通过在生长过程中改变镍厚度和生长时间来控制,从而提供了一种针对不同应用的控制石墨烯生长的方法。
图2.2(c)中的原子力显微镜(AFM)图像显示出由于镍和石墨烯的热膨胀系数之间的差异引起的波纹结构。这些起伏褶皱使石墨烯薄膜具有稳定的抵抗机械拉伸的能力,且更具可扩展性。就大面积薄膜结构的机械强度而言,多层石墨烯样品是优秀的,而较薄的石墨烯薄膜具有更高的光学透明度。研究发现,在硅晶片上镀上约300nm厚的镍层是大规模CVD生长的最佳基板,可产生机械强度稳定、透明的石墨烯薄膜,在它们形成后进行转移和拉伸,并且更薄的镍层使生长时间较短,主要用于微电子器件应用的单层和双层石墨烯薄膜的制备。

(a)在薄(300nm)镍层和厚(1mm)镍箔(见插图)上生长的石墨烯薄膜的SEM图像;(b)不同厚度的石墨烯薄膜的TEM图像;(c)转移到300nm厚的SiO2上的石墨烯薄膜的光学显微镜图像(插图AFM图像显示了典型的波纹结构);(d)对应于图2.2(c)中的共焦扫描拉曼图像(根据G波段和2D波段峰值的强度、形状和位置估计层数);(e)从图2.2(c)和图2.2(d)中相应色点获得的拉曼光谱(532nm激光波长)
图2.2 采用CVD法制得的石墨烯的微观表征[6]
Chandrashekar[7]等利用卷对卷的方式在一定程度上实现了利用CVD法量产石墨烯,并且简化了生产工艺,如图2.3所示。图2.3(a)显示了在铜箔上生长的大面积的石墨烯到EVA/PET(乙烯-醋酸乙烯共聚物/聚对苯二甲酸乙二醇酯)基材的示意图。首先,通过卷对卷CVD工艺在铜箔上生长一卷石墨烯薄膜(见图2.3(b))。其次,快速可靠的转移过程涉及4个基本步骤:①在室温下将石墨烯/铜储存一段时间或稍微加热,以加速氧嵌入和铜氧化。②通过热层压法将石墨烯/铜黏附到EVA/PET基材上。③将层压铜/石墨烯/EVA/PET薄膜浸入热水(约50℃)中2分钟。④将层压铜/石墨烯/EVA/PET薄膜的卷对卷机械分层,以获得铜箔和石墨烯/EVA/PET薄膜。卷对卷分层装置由3个作为卷绕辊和两个作为接收辊的终端辊组成,由步进电机控制以相同的速度运行。图2.3(c)为卷对卷分层工艺实验装置的照片。层压铜/石墨烯/EVA/PET薄膜在仪器的中间卷绕辊上滚动,然后由步进电机控制机械分层过程。卷对卷分层速度可以达到1cm·s-1。将分离的铜箔和石墨烯/EVA/PET薄膜用相对的辊子卷绕起来,并用氮气枪吹干。值得注意的是,转移后的铜箔可以重新用于石墨烯的生长。

(a)铜和石墨烯在EVA/PET基材上的卷对卷分层示意图;(b)通过卷对卷CVD工艺生长的石墨烯在铜箔上的照片;(c)卷对卷分层工艺实验装置的照片;(d)分层后一卷石墨烯/EVA/PET薄膜的照片,并显示出优异的透明度
图2.3 卷对卷石墨烯的转移过程
2.2.1.2 外延生长法
外延生长法是一种物理沉积单晶薄膜的方法。利用外延生长法制备石墨烯时一般将SiC作为原材料,实验之前将其用氧气或氢气进行刻蚀处理,再将其置于超低压、高真空的环境中,用电子束轰击以去除其表面存在的氧化物,再将其加热到一定温度,使得表面的Si原子蒸发,剩余的碳原子发生重构,从而形成石墨烯[8]。除了SiC,也可以在某些金属基体上外延生长石墨烯[9]。通过上述实验步骤可以得知,利用这种方法可以可控制备高质量的石墨烯单晶,但是制备工艺复杂、条件苛刻、产量极低,因此很难实现实际生产和应用。
外延这个词来自希腊词根epi,意思是“上面”,而taxis的意思是“一个”。外延意味着在晶体衬底上生长晶体层,其遵循基板的结构,沉积层称为外延层。这种技术的优点之一是它不需要将石墨烯层转移到另一个基板上,允许电子设备直接在半绝缘的SiC上制造。生长外延石墨烯的升华方法是对SiC晶体进行低压、高温退火处理。由于在SiC衬底中,Si具有比C更高的蒸气压,在退火过程中,Si原子首先从样品表面解吸,留下C原子,并允许富碳表面出现,直到形成最终的石墨烯。在这种技术中,温度确保了有序和清洁的石墨烯的形成。石墨烯在SiC表面生长属于石墨化过程。在受控条件下,可以有不同的生长安排。立式射频加热炉由石英管、多孔石墨绝缘材料和石墨等组成,立式射频加热炉的横截面示意图如图2.4所示。

图2.4 立式射频加热炉的横截面示意图[8]
Si面和C面石墨烯层的外延石墨烯的生长机制是由相同的物理过程驱动的:Si在高温下升华的速度比C快,因为Si的蒸气压更高。剩余的C在表面形成石墨烯薄膜。然而,Si面和C面的表面重建、生长动力学和极性不同,从而导致了不同的石墨烯生长速率、生长形态和电子特性。
如图2.5(a)所示,4H-SiC具有两种分解能,分别为台阶4H1(-2.34MeV)和4H2(6.56MeV),而6H-SiC[见图2.5(b)]具有三个不同的台阶,6H1(-1.33MeV)、6H2(6.56MeV)和6H3(2.34MeV),而3C-SiC[见图2.5(c)]只有一种台阶,即3C1(-1.33MeV)。图2.6中示意性地显示了4H-SiC的生长过程。外延石墨烯的生长在SiC衬底表面上分布不均。由于Si和C原子在台阶边缘附近的键合更弱,与台阶相比,Si从这些区域解吸得更快。值得注意的是,包含在SiC衬底的三个Si-C双层中的C足以供单层石墨烯形成。
基于上述4H-SiC的台阶能量,去除4H1台阶将花费更少的能量。因此,对于4H1台阶,阶梯分解速度会更快[见图2.5(a)]。如图2.6所示,在无石墨烯表面上的4H1平台边缘,随着Si原子离开表面,C原子被发射到平台上(阶段1)。C原子聚结并成核成石墨烯岛(阶段1和阶段2),作为随后发射的C原子的源。在4H1台阶捕获4H2台阶之后,与单层高度的台阶相比,新形成的双SiC双层高度台阶提供了更多的C原子,并且第一层石墨烯层沿台阶边缘延伸(阶段2)。具有4个Si-C双层的大比例聚束台阶,即增加的源碳,会释放一些额外的C,强制形成第二层石墨烯。因此,仅用一层石墨烯完全覆盖4H-SiC衬底表面可能存在问题。
2.2.1.3 有机合成法
有机合成法从特定的前驱体分子稠环芳香烃(Polycyclic Aromatic Hydrocarbon,PAHs)开始,通过设计化学合成方法(如偶联、聚合或环化反应等)合成具有精准微观结构的石墨烯。PAHs是指包括两个及两个以上的未取代苯环的芳香烃。稠环芳香烃由sp2杂化碳原子组成,与石墨烯的结构十分相似。当稠环芳香烃的分子尺寸达到1~5nm时,其又被称为石墨烯分子。PAHs分子具有精准的结构、可调控的溶解性和优异的加工性能,可作为石墨烯 π体系的模板,实现在一维、二维和三维尺度上设计合成大面积具有特定微观分子结构的石墨烯纳米带、石墨烯片等结构。

(a)4H-SiC上的堆叠顺序和可能的台阶;(b)6H-SiC;(c)3C-SiC表面(大圆圈和小圆圈分别代表Si和C原子。箭头的长度表示不同步骤的分解速度)[10]
图2.5 SiC不同分解台阶示意图

图2.6 通过从SiC表面升华Si来形成外延石墨烯的过程示意图[11]
结构内的亚单元均为苯环的前驱体分子,是合成石墨烯的首选分子。树枝状的聚苯分子(Diphenylbis(4-(pyridin-3-yl)phenyl)silane,DPPs)包括单分散的树枝状大分子及多分散的超支化聚苯分子,它们均包含大量的苯环结构,是采用有机合成法合成石墨烯的理想前驱体分子。合成单分散的树枝状的聚苯分子DPPs主要利用二苯乙炔的环三聚反应及Diels-Alder反应[11,12]。这种方法不仅可以将功能化的组分(如噻吩)引入树枝状的结构中,也可以得到聚集的更高级别的树枝状的聚苯大分子DPPs。利用Diels-Alder反应,苯基取代炔和四苯基环戊二烯酮(Tetraphenylcyclopentadienone,CPs)发生环化加成反应。不同的CPs和炔烃的衍生物发生反应可以形成不同微观结构和多种取代基形式的分子拓扑结构。其次,利用功能化的AB2化合物作为基础结构可以合成多分散的超支化聚苯分子DPPs。包含环戊二烯酮类分子和亲二烯体炔类分子的AB2功能化分子作为前驱体可以与乙炔化合物发生分子内的Diels-Alder环化加成反应,形成高度集中的苯环结构和基本可以无限制扩展的超支化聚苯结构[13],如图2.7所示。

图2.7 分子内Diels-Alder环化反应生成超支化聚苯分子[13]
树枝状聚苯分子DPPs可在室温下与FeCl3在二氯甲烷中通过发生Scholl反应将聚苯分子中的苯环取代基融合为二维平面分子,如图2.8所示[14]。这种前驱体分子内的脱氢环化过程可以产生不同分子尺寸、对称性、边缘结构及微观结构(如三角形、直线带状等)的石墨烯分子[15,16]。实现DPPs的完全脱氢环化过程需要精确控制实验条件,如反应时间、氧化剂的选择和试剂的用量等。目前从DPPs脱氢环化合成的最大的分子石墨烯具有222个sp2杂化的碳原子。基于上述反应思路,可以利用相应的DPPs分子作为前驱体来合成具有不同微观结构和分子尺寸的石墨烯分子。

图2.8 DPPs脱氢环化为石墨烯分子[14]
利用有机合成法合成石墨烯主要有两种方法。一种方法是溶液法,首先在溶液中合成树枝状或超支化的前驱体分子,随后将其转移到目标基底上,利用前驱体分子的脱氢环化反应来制备比较纯净的石墨烯结构。这种方法的反应条件温和、化学反应过程可设计,但石墨烯的生长尺寸较小。另一种方法是热解法,即通过热处理金属基底表面的低聚苯前驱体分子来获得平面型的材料,利用这种方法可以制备较大面积的石墨烯微米结构。
对于溶液法,在反应过程中,当聚合单体增长到一定程度时,苯环的严密堆积致使聚合物分子的溶解度急速下降。这种溶解度方面的限制也限制了聚合反应的发生,进而影响了制备的石墨烯的尺寸。Wu和Yang[17,18]等分别利用Diels-Alder反应和Suzuki-Miyaura偶联反应制备了可溶的DPPs低聚物分子,随后利用DPPs低聚物分子的Scholl反应制备出石墨烯纳米带,如图2.9所示。Fogel[19]等利用微波辅助的Diels-Alder反应形成了芘聚集的DPPs低聚分子,随后通过氧化环化反应制备了多分散的石墨烯纳米带,其能够很好地溶解在四氢呋喃溶液中,在透射电子显微镜中可看到层状堆叠的石墨烯。

图2.9 合成PAH C78和石墨烯纳米带的方法
溶液法中前驱体分子在溶液中的溶解度限制[20]及Scholl平面化反应的不可预测性限制了有机合成法在溶液中的应用。而热解法是在金属基底的催化作用下,利用合适的前驱体分子发生的偶联或环化脱氢反应来制备较大面积的石墨烯微米结构的,可以促使石墨烯的生长和聚集同时在基底发生,有效地克服了溶液法的上述缺陷。在热解法中,基底提供的二维辅助模板使反应具有方向的驱动性,更易使基底表面分子发生连接反应,形成稳定的结构,发生有效的电子转移过程。其中,基底的选择、前驱体的结构及热反应条件是影响热解法的关键因素。目前有大量文献介绍以稠环芳香烃或其卤代物为前驱体,在不同的金属基底上加热制备出具有不同形貌的石墨烯[21,22]。如图2.10所示,在一定温度下,不同分子结构的卤代芳香烃在Ag(111)、Au(111)或Cu(111)晶面发生Ullmann芳基偶联反应和脱氢环化反应可以得到具有“扶手椅形”边缘的直线型纳米带、三角形的纳米石墨烯、具有空隙的聚苯结构。其中,在575K时,在Ag(111)晶面获得的孔状石墨烯结构的孔间距可达7.4Å。

图2.10 制备的石墨烯纳米带[23]

图2.10 制备的石墨烯纳米带[23](续)
2.2.2 自上而下的方法
自上而下的方法为将宏观的石墨变为少层石墨烯,其优点是可以按比例放大、不需要基板转移,以及与自下而上的制造工艺相比具有成本效益和高可重复性。然而,自上而下的方法无法预测石墨烯的精确配置。并且实验室规模的研究和商业应用之间的转化是一个至关重要的步骤。到目前为止,超声处理/电剥离、球磨和氧化石墨烯还原等方法因为具有低价批量生产高质量的石墨烯的成本优势[24],已成为较有前景的技术。
Novoselov[25]等首次制备了石墨烯,如图2.11所示,他们用胶带在高取向热解石墨薄片上反复粘脱,将黏附有石墨烯的胶带超声处理,最后用硅片将散落在丙酮溶液中的石墨烯片捞起。这是获得石墨烯最为简便的方法,并且得到的石墨烯品质高。但是这种方法不可控,无法获得面积、厚度一定的石墨烯片,效率很低,且无法大量生产。

(a)SiO2片上的大尺寸多层石墨烯(厚度为3nm)照片;(b)在2mm×2mm的面积内SiO2基底上的石墨烯边缘的原子力显微镜照片;(c)单层石墨烯的原子力显微镜照片,底部区域1为基底SiO2,中心区域2的厚度为0.8nm,左底部区域3的厚度为1.2nm;左上角区域4的厚度为2.5nm。注意底部折叠部分的厚度为0.4nm;(d)实验装置的SEM图;(e)图2.11(d)装置的示意图
图2.11 采用机械剥离法制备的石墨烯[1]
2.2.3 氧化还原法
采用氧化还原法制备石墨烯最早可以追溯到1860年,这种方法主要是利用强质子酸和强氧化剂对石墨进行插层和氧化处理,打破碳碳之间形成的σ键,连接上一些含氧官能团,包括羟基、羰基、环氧基等。这些含氧官能团的引入会增大石墨片层之间的间距,削减片层之间的相互作用力,形成氧化石墨烯(Graphene Oxide,GO)[26,27],如图2.12所示[28]。石墨烯是一种典型的疏水材料,稳定的结构使其很难与其他物质发生化学反应。通过上述氧化处理后,大量亲水性的含氧基团连接到石墨烯的表面和边缘,使得GO可以很好地分散在水溶液及一些有机溶剂中,同时这些含氧基团使得GO具有一定的化学活性,通过一系列化学修饰可以使其表面具有一些特殊性质[29]。

图2.12 氧化石墨烯的制备及表面结构[28]
获得GO后,可以通过物理或化学手段除去GO表面的含氧官能团,得到还原氧化石墨烯(reduced Graphene Oxide,rGO)。其中,物理手段包括热还原、射线还原[30]等;化学手段主要利用一些还原剂[31],如硼氢化钠、水合肼、二甲肼、对苯二酚、乙二胺、1,4-二碘丁烷等。与石墨烯的完美结构不同,虽然还原可以除去GO表面绝大部分的含氧基团,但是氧化过程对石墨烯碳骨架造成的破坏却是不可逆的,因此rGO无论是在导电性、热导率,还是在力学性能上都要远远低于石墨烯本征的优异性能。用氧化还原法制备石墨烯可以实现量产,生产工艺比较简单,成本较低。但是生产过程中需要消耗大量的水,而且难以做到可控制备。
2.2.4 液相剥离法
液相剥离法就是将石墨或可膨胀石墨置于与其表面能匹配的有机溶剂中,如N-甲基吡咯烷酮、邻二氯苯、表面活性剂[32]等,通过超声作用得到不同层数石墨烯与石墨片层的悬浊液,利用离心去除较厚的石墨片层,最终得到不同层数的石墨烯片的混合液,如图2.13所示[33],石墨片在水溶液中与胆酸钠(SC)结合,Horn超声波可去除由SC胶束封装的几层石墨烯薄片。利用液相剥离法获得的石墨烯的质量和产量与石墨烯和石墨片层之间的匹配程度有关,通常匹配程度越高,石墨烯及石墨片层在有机溶剂中的分散性越好,剥离程度也越高。并且利用该法制备的石墨烯的碳碳骨架基本不会遭到破坏,晶格完整性很高,可以获得高质量石墨烯片,而且制备方法简单,污染性小。实际上,石墨烯在上述有机溶剂中的分散浓度仍比较低,如在N-甲基吡咯烷酮中的分散浓度仅有0.01mg/ml,即便加入活性剂,仍低于0.2mg/ml[34]。因此利用该方法得到的石墨烯的产量仍然很低,而且后续需要长达上百小时的超声分散处理,费时费能,不适合工业化大规模生产。
除了上述方法,还有一些其他制备石墨烯的方法,如微波辐射法、碳纳米管纵切法、溶剂热法[35-37]等。在上述制备石墨烯的几种方法中,氧化还原法和CVD法是常用方法,主要是因为其制备方法简便,产量较高。石墨烯的层数明显影响着石墨烯的性能,因此可控制备石墨烯对实际生产十分重要。
2.2.5 等离子法
暴露在高温下(高达4000K)的石墨烯前驱体能在几毫秒内产生高纯度、低缺陷浓度的结晶石墨烯。因此,不少研究者通过采用射频感应加热和微波加热等离子体技术制备石墨烯,但是这类手段具有能耗高、难以工业化应用的缺点。在等离子体热解碳氢化合物合成石墨烯的过程中,由于等离子体的电导率随着温度增加迅速上升,导致电弧自动收缩到很小的范围,对于合成石墨烯要求的毫秒级反应时间,难以实现均匀加热,导致产品均匀性差、能耗高。采用磁分散电弧产生大面积均匀等离子体的技术解决了等离子体对物料快速均匀加热的问题,所制备的石墨烯平面尺寸为50~300nm,层数为2~5层,表现出良好的晶体结构和超大的比表面积,产品均匀性好。该制备方法及设备简单,可一步合成,无须还原,且无须基底、催化剂、溶液或酸,收率高,约为14%,能耗低,约为0.4kW·h/g,具备实现低成本、大规模、连续生产的前景。

图2.13 石墨烯液相剥离过程图解[33]
等离子体辅助石墨剥离成石墨烯的机理可分为三个阶段:热等离子体对石墨产生热冲击(第1阶段),石墨颗粒在热冲击下剪切为两阶段层流(第2阶段),等离子体流的湍流区域(第3阶段)。由于热冲击和随后的剪切在此过程中具有重要作用,因此反应温度和速度对石墨颗粒的剥离效率具有重要的影响。Islam[37]等研究了利用等离子体制备石墨烯的技术,如图2.14所示。图2.14(a)和图2.14(b)给出了温度和速度对飞行中的石墨颗粒的影响。随着等离子功率从10kW增加到40kW,一次气体流量从80SCFH增加到140SCFH,石墨颗粒的温度和速度均增加。参考图2.14(c)和图2.14(d),一旦石墨颗粒被注入热等离子体的层流区域,石墨将暴露在高温(3430℃)下,在如此高的温度下,需要使用惰性氩气罩和较短的停留时间(以μs为单位)来防止石墨被损坏。此外,快速的热量转移可以防止石墨被损坏。在较高的温度下,传热会更多,这将避免局部加热并进一步防止任何石墨被损坏。热冲击会导致石墨层间距增加和范德瓦尔斯力降低,从而起到弱化石墨颗粒的效果。除了热冲击,被弱化的石墨颗粒还受到以下因素的组合影响:第2阶段产生的湍流和层流区域的剪切力。通过将主要气体流量增加到120SCFH,湍流速度增加,随后,石墨颗粒的速度达到350m/s。反过来,等离子气体的黏度在较高温度时呈指数增加,将使向前移动的石墨颗粒减速。因此,这种相反的力可以帮助剪切石墨层,并有助于膨胀石墨层的剥离。已经弱化和部分剪切的石墨颗粒向下游越过湍流区域,如图2.14(c)和图2.14(e)所示,在那里遇到了大规模的冷涡环境气体(笼罩氩气)。夹带有石墨颗粒后,涡流将具有更高的密度,夹带的石墨颗粒将经历更大的惯性。因此,石墨颗粒将以较低的速度沿轴向移动,而热等离子体湍流具有较高的初级气体流量(120SCFH)。正是这种竞争现象使得被弱化和最初剪切的石墨颗粒在石墨层之间遇到强烈的剪切,导致石墨烯片自动剥离。

(a)等离子体功率与飞行中的石墨颗粒的温度的关系图;(b)主要气体流速与飞行中的石墨颗粒的速度的关系图,显示了所有气体流速和等离子体功率的线性趋势;(c)石墨剥离机制示意图;(d)部分图2.14(c)的等离子体湍流和层流区域的放大图;(e)湍流区域的放大图[37]
图2.14 等离子法制备石墨烯示意图
通过使用高分辨率透射电子显微镜(HR-TEM)分析被剥离的单个石墨烯薄片,如图2.15(a)、图2.15(f)、图2.15(k)所示,而图2.15(b)、图2.15(g)、图2.15(l)是它们的相应的放大图像。从薄片的边缘可以识别出石墨烯的层数。图2.15(c)中没有明显暗线的明亮边缘表明石墨烯的单层特性。原子分辨率傅里叶转换图像显示了一个完美的六边形单层石墨烯的图案[见图2.15(d)]和指示双层和三层石墨烯的重叠图案[见图2.15(i)和图2.15(n)]。此外,所选区域从各个表面收集的电子衍射(SAED)图像显示出了石墨烯独特的六边形图案,没有任何光晕[见图2.15(e)、图2.15(f)、图2.15(o)],表明石墨烯具有高度结晶性。通过(12-10)—(01-10)—(1-010)—(2-110)的线轴还提供了石墨烯层的证据。而强烈的(01-10)和(1-010)峰与(12-10)和(2-110)峰表示单层石墨烯,强烈的(12-10)和(2-110)峰与(01-10)和(1-010)峰相比表明不止一层石墨烯。通过使用原子力显微镜进行厚度识别。剥离的石墨烯的厚度,如图2.15(p)~图2.15(s)所示,几乎测量的所有薄片的厚度都小于2nm厚,其中,大多数厚度低于1nm的薄片为单层到几层石墨烯。

(a)和(b)单层石墨烯的透射电子显微镜(TEM)图像;(c)单层石墨烯边缘的高倍放大图像;(d)部分图2.15(c)巴特沃斯滤波图像;(e)单层石墨烯的选区电子衍射(SAED)图像;(f)和(g)双层石墨烯的TEM图像;(h)双层石墨烯的边缘显示两个石墨烯层;(i)部分(h)的过滤图像;(j)SAED图像;(k)和(l)三层石墨烯的TEM图像;(m)三层石墨烯的边缘;(n)部分图2.15(m)的过滤图像;(o)SAED图像;(p)石墨烯的原子力显微镜图像;(q)部分图2.15(p)中的沿虚线的高度剖面;(r)使用AFM获得的400个选定的任意石墨烯薄片的厚度直方图;(s)使用AFM获得的400个选定的任意石墨烯薄片的长度直方图;(t)剥离石墨烯(Si晶片上的滴铸石墨烯)的低倍SEM图像[37]
图2.15 等离子法制备石墨烯的结果表征
使用拉曼光谱可以评估剥离的石墨烯的结构完整性。如图2.16(a)所示的拉曼图谱,可将剥离的石墨烯看作单层、双层和三层石墨烯。通过拉曼图谱的形状可区分石墨烯层数、2D峰的大小和强度。以单层为例,石墨烯显示出尖锐且对称的2D峰,而带有Bernal(AB)堆叠的多层显示复杂的2D形状由多条洛伦兹线拟合。拉曼单层石墨烯的光谱更接近于液体剥离石墨烯,而不是广泛和高度热还原rGO的无序光谱。然而,因为拉曼光束光斑尺寸(<2μm)小于大多数剥离的石墨烯,可以假设为D峰可能受边缘效应支配。然而,不能完全排除在剥离过程中诱发的基面缺陷。因此,完成了石墨烯的拉曼映射和原位AFM表征。G波段生成的石墨烯薄片和D波段生成的石墨烯薄片的拉曼图[见图2.16(b)和图2.16(c)]表明沿石墨烯边缘的缺陷密度更高。对同一薄片的拉曼分析表明,强烈的D峰出现在边缘[见图2.16(d)和图2.16(e)],表明D峰的测量结果与薄片边缘有关。同时ID/IG沿边缘的比率(约为0.2)与LPEG的比率相似,并且显著低于球磨石墨烯,表明了剥离的石墨烯的无缺陷性质。剥离石墨烯的XPS结果如图2.16(f)所示,表明剥离的石墨烯的氧浓度约为4.5%,而石墨中非共价键吸附的氧低于6.1%。其中,碳氧原子比(C/O)约为21.2,高于先前报告的GO、rGO和EcG值,并且接近LPEG和CVD生长的石墨烯。C/O比率的增加表明去除了一些等离子化过程中的含氧官能团。剥离石墨烯碳1s峰的XPS光谱[见图2.16(g)]可以拟合为284.6eV、287.1eV和290.9eV的3个峰。前两个峰对应于C-C和C=O键,而290.9eV峰对应于剥离后的π-π*跃迁,表明共轭芳香结构在非常高的温度下仍能保留。此外,傅里叶变换红外光谱学(FTIR)揭示了剥离石墨烯的几乎无特征的光谱,这与GO的光谱形成对比,表明制备的石墨烯不是某种形式的衍生石墨烯。图2.16(h)将剥离的石墨烯与通过各种其他方法获得的石墨烯进行比较,基于两个重要因素(碳含量和sp2%)来定义石墨烯的质量。剥离的石墨烯的碳含量=95.5%,sp2%=95%,其性能远高于GO和rGO,与EcG、LPEG和CVD石墨烯相当。

(a)拉曼光谱,单层、双层、三层石墨烯和石墨的2D能带结构;(b)G波段生成的石墨烯薄片的拉曼图;(c)D波段生成的石墨烯薄片的拉曼图;(d)使用原位AFM-Raman从薄片的中部收集的拉曼光谱;(e)使用原位AFM-Raman从薄片的边缘收集的拉曼光谱;(f)石墨烯的X射线光电子能谱(XPS)调查。为了比较,还包括石墨的XPS调查。由于XPS是表面敏感的,因此将样品在RF等离子体中清洗,以避免外来碳的沉积;(g)石墨烯的核心级碳1s峰的XPS光谱;(h)GO、rGO、电化学剥离石墨烯(EcG)、液相剥离石墨烯(LPEG)、化学气相生长石墨烯(CVD)和石墨(包括HOPG)[37]
图2.16 石墨烯结构完整性的表征