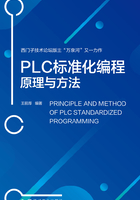
第1章 综述
在工业生产过程中,大量的开关量顺序控制按照逻辑条件进行顺序动作,并按照逻辑关系进行联锁保护动作的控制,以及大量离散量的数据采集。传统上,这些功能是通过气动或电气控制系统实现的。1968年美国GM(通用汽车)公司提出取代继电器控制装置的要求,第二年,美国数字公司研制出了基于集成电路和电子技术的控制装置,首次采用程序化的手段应用于电气控制,这就是第一代可编程序逻辑控制器(Programmable Logic Controller, PLC)。
1987年国际电工委员会(International Electrotechnical Commission, IEC)颁布的PLC标准草案中对PLC做了如下定义:“PLC是一种专门为在工业环境下应用而设计的数字运算操作的电子装置。它采用可以编制程序的存储器,用来在其内部存储执行逻辑运算、顺序运算、计时、计数和算术运算等操作的指令,并能通过数字式或模拟式的输入和输出,控制各种类型的机械或生产过程。PLC及其有关的外围设备都应该按易于与工业控制系统形成一个整体,易于扩展其功能的原则而设计。”
早期的PLC主要由分立元件和中小规模集成电路组成,可以完成简单的逻辑控制及定时、计数功能。20世纪70年代初出现了微处理器。人们很快将其引入PLC,使PLC增加了运算、数据传送及处理等功能,完成了真正具有计算机特征的工业控制装置。此时的PLC为微机技术和继电器常规控制概念相结合的产物。
20世纪70年代中末期,PLC进入实用化发展阶段,计算机技术已全面引入PLC中,使其功能发生了飞跃式提高。更高的运算速度、超小型体积、更可靠的工业抗干扰设计、模拟量运算、PID(比例-积分-微分)功能及极高的性价比奠定了它在现代工业中的地位。20世纪80年代初,PLC在先进工业国家中已获得广泛应用。这个时期PLC发展的特点是大规模、高速度、高性能、产品系列化。这个阶段的另一个特点是世界上生产PLC的国家日益增多,产量日益上升。这标志着PLC已步入成熟阶段。
20世纪末期,PLC的发展特点是更加适应于现代工业的需要。从控制规模来说,这个时期发展了大型机和超小型机;从控制能力上来说,诞生了各种各样的特殊功能单元,用于压力、温度、转速、位移等各种各样的控制场合;从产品的配套能力来说,生产了各种人机界面单元、通信单元,使应用PLC的工业控制设备的配套更加容易。目前,PLC在机械制造、石油化工、冶金钢铁、汽车和轻工业等领域的应用都得到了长足的发展。
为了使工程技术人员更好地使用继电器、接触器系统,早期的PLC采用和继电器电路图类似的梯形图(LAD)作为主要编程语言,并将参加运算及处理的计算机存储元件都以继电器命名。
LAD语言的主要特点是简单、直观。在早期的继电逻辑搭成的控制系统升级为PLC控制系统之后,所编制的LAD程序简直可以和继电器逻辑图完全等同。可以认为,由于LAD语言的发明诞生了整个PLC行业。
由于LAD语言过于直观,整个工业行业中所有的PLC品牌所编制的PLC程序都是平铺式的,按照电气控制柜或者按照生产工艺的顺序程序线性地平铺下来。由于技术的发展,一些品牌的PLC支持模块化,但也只是将平铺的程序简单地分割到若干模块中。从设计理念上来说,仍然是线性的。
近10年来,由于计算机技术的飞速发展,更快速、更大内存、更高性能的CPU应用到PLC系统中。同时各PLC厂商的软件系统也在不断地升级,各种新的功能接近计算机高级语言的编程语言加入到PLC的编程语言中,使得PLC编程更具灵活性,更接近计算机编程的方法。
但是,工业行业是个比较遵循传统的行业。虽然PLC的硬件和软件系统已经升级了多次,但很多行业,控制逻辑和程序还是遵循最早开始使用PLC做出的逻辑。在各PLC厂商推出新系统时,很多工业用户首要关心的是旧的控制程序能否直接升级使用?只有支持移植旧程序略加改造就能使用,才会接受,否则这些新产品新技术就会被市场拒绝。
于是,尽管计算机行业已经日新月异,并且PLC厂商提供的系统已经与20世纪80年代的旧产品性能上有翻天覆地的变化,但在大多数传统行业中,应用控制程序仍然与最早80年代的是一个套路,无非是细节上有一些差别。比如过去模拟量处理不方便,大量使用的纸质记录仪,而今换成了软件内部控制,数据直接传到上位机数据库中记录,仅此而已。
尽管计算机行业的编程方法飞速发展,但在工业控制领域,大量的PLC控制程序仍然沿用着40年前的套路。一代一代的工程师从入行开始,所接触的行业应用程序或者案例都是一样的,在他们自己设计出来的控制系统中逻辑程序也全都是继承效仿前人的,完全没有追随计算机行业那样有翻天覆地的变化。
基于LAD的线性编程方法,由于封装性不够好,一个重大的缺点是代码的重复使用性低,现场的调试工作量大,导致大批从事工业控制的工程师将大量的工作时间耗费在项目出差现场。一个工程项目,哪怕是相当多的重复性的项目,虽然已经做过了多次同样类型的项目,由于控制点数的变化和设备的具体参数的变化,导致应用程序逻辑总要有细微的差别。
诚然,一些自动化厂商推出了带有一定封装功能的控制软件产品,比如西门子公司的PCS 7和AB公司的PlantPAx,但这些封装还是比较原始的,仅仅是在基本控制设备层面上实现了封装,在高级的工艺相关的逻辑没有做到封装,已有的项目经验不能顺利继承并充分利用,大量的逻辑实现仍然需要工程师在项目实施现场完成。
出于安全的原因,即便细微的差别也都需要具有丰富工程经验的工程师亲自完成,而不敢轻易地交给初入行的学徒,或者助理工程师来完成,这极大地影响了工作效率,同时加大了项目实施的成本。
本书作者从事自动化技术工作20余年,从开始消化吸收引进生产线项目,到自己主导设计生产线,调试自动化设备,以及从事技术支持工作,为客户进行PLC及WinCC编程培训工作,并且还兼职担任西门子自动化技术论坛版主,一直关注工业自动化行业的发展。
在关注工业自动化产品升级换代的同时,也一直持续研究高效地进行PLC标准化编程的原理和方法,并从中积累了大量的素材和丰富的经验,并应用于工程实践。2018年作者结合西门子最新发布的TIA Portal V15.0新功能,实现了全方位、真正的标准化应用,示范项目已经在客户工厂成功运行。
这次标准化应用是史无前例的。不仅在同行之中是首例,在作者本人的项目经验中也是首例。
因此作者向广大同行推广标准化应用示范项目并开展了相关培训辅导,一批自动化行业的创新先行者参加了培训,并在各自从事的行业中进行了推广应用,取得了很好的效果。
作者本人在项目成功应用以及培训经验基础上又进行了理论总结,提取其中的理论精华,可以完全抛开原有的PLC硬件和软件,形成了面向整个自动化行业标准化应用的规范。继而又组织力量对罗克韦尔、施耐德、倍福等品牌的标准化设计方法进行了应用示范,进而在某些小型PLC中使用同一理论方法也进行了有效的实践。
实践证明,这一方法是成熟可靠的。采用这一标准化的设计方法设计的程序,效率高、代码可复用性高,大大地减少了现场的调试时间和难度,也大幅降低偶然因素出错的概率,这对于整个自动化行业必将是引领一场全新的潮流。
标准化设计方法的核心目的是提高程序的设计效率,如果不能提高效率,则标准化设计就没有意义。所以本书在讲述标准化原理方法的同时,会针对各品牌应用时重点介绍相关功能的高效实现。使读者在学习标准化方法的同时还可以复习强化对各品牌PLC软硬件的高效使用技巧。在学习本书之前,对感兴趣的品牌,只需要稍微学习了解其基本的使用方法即可。
小型PLC由于原始设计性能较低,先天不具备标准化编程的能力,为了使其具备这种能力,需要从基础进行较大的改造,因而需要较高的PLC应用能力,难度较大。本书作者虽然已经实现了在S7-200 SMART PLC中的标准化应用,但因篇幅的限制,相关的设计方法并没有在本书呈现。有兴趣的读者在阅读本书之后,在理解原理的基础上,可以联系作者进行咨询。