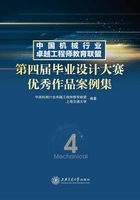
大涵道比风扇叶片加工变形振动机理研究与工艺创新
作者:梁嘉炜 指导老师:王辉 企业指导老师:陈贵林
清华大学 机械工程专业
1.设计目的
航空发动机是国防主战装备的强劲心脏,被誉为现代工业“皇冠上的明珠”。大涵道比航空发动机具有噪声小、热效率高、推进效率高、总推力大、可靠性高等优势,是世界航空发动机制造的重点发展方向。风扇叶片产生了大涵道比航空发动机75%以上的推力,是实现发动机性能的关键零部件。由于其尺寸大、强度高、精度高、形状复杂、材料难加工等特点,大涵道比风扇叶片的精密铣削加工是对航空发动机制造领域的重大挑战。目前采用的铣削加工工艺装备通过夹住风扇叶片的榫头和叶尖,然后对叶身和阻尼台进行铣削加工(见图1)。在叶身中部及阻尼台附近的刚度相对于铣削力度而言明显较低,容易出现较大程度的变形让刀和切削振动,导致风扇叶片尺寸精度和表面完整性无法达到要求。因此,设计研发大涵道比风扇叶片加工新型专用工艺装备,能够提升大尺寸薄壁异形叶片的加工刚度,减小加工变形与振动,提高叶片的尺寸精度和表面质量,这对于大涵道比航空发动机风扇叶片制造具有重要意义。

图1 风扇叶片铣削加工工艺
2.基本原理及方法
1)球头铣刀切削力模型
首先,通过斜角切削模型建立了球头铣刀微元切削力模型,并使用ABAQUS软件进行切削仿真,对模型参数进行了标定;接着,使用解析几何方法求解了球头铣刀与叶片曲面结构之间的切触区域,给出了球头铣刀整体切削力数值计算方法。该方法能够快速计算球头铣刀切削叶片的切削载荷信号,获取切削载荷的幅值、均方根和频率特征,计算结果与实验结果相吻合,如图2、图3所示。

图2 球头铣刀整体切削力数值计算模型

图3 球头铣刀切削力数值计算结果
(a)球头铣刀切触区域;(b)球头铣刀切削力信号
2)风扇叶片弯扭组合变形模型
基于球头铣刀切削载荷模型,对风扇叶片在切削载荷下的变形进行分析。风扇叶片在加工过程中采用两端装夹的方式:通过榫头和叶尖的卡盘将叶片两端夹紧,并以榫头为基准实现定位。根据叶片的装夹结构,得到简化模型的弯曲受力分析,如图4所示,薄板两个对边为固支边界,另外两个对边为自由边界。由图4(a)可得,此问题为超静定问题,建立的等价静定系统如图4(b)所示。建立变形协调条件并求解可得切削部位的弯曲变形让刀量:


图4 简化模型弯曲受力分析
(a)超静定系统;(b)等价静定系统
风扇叶片为宽弦薄壁结构,在切削加工过程中还会发生明显的扭转变形,得到简化模型的扭转受力分析如图5所示。同理可得切削部位的扭曲变形让刀量:


图5 简化模型扭转受力分析
(a)超静定系统;(b)等价静定系统
叶片的弹性变形主要是由弯曲和扭转组成,只考虑横向载荷的情况下,弯曲变形和扭转变形引起的位移方向相同,因此在切削载荷下的变形让刀量为弯曲变形让刀量和扭转变形让刀量之和,即

化简可得

3)风扇叶片模态分析原理
动力学分析用于考虑时变载荷对整体结构的影响,通常考虑刚度、阻尼和惯性效应的影响。其中,模态分析是动力学分析的重要内容,模态是指结构振动的固有动态特性,结构的各阶模态对应结构的各阶固有频率,与结构的质量和刚度分布直接相关。由动力学分析的基本方程可得工艺系统的传递函数为

式中,M、C和K分别为质量矩阵、阻尼矩阵和刚度矩阵,代表了结构动力学行为中的惯性、阻尼和刚度效应。
对于叶片切削加工过程,常常关注的是对p点施加激励的情况下,p点处的位移频率响应函数Hpp(ω)。对于大多数系统而言,系统的模态具有正交性,即系统的各阶模态之间耦合程度低,各阶模态之间的影响可以忽略不计。此时,位移频率响应函数Hpp(ω)可以近似表示为

式中,φi、ki、ωi、ξi分别为系统的第i阶模态对应的位移向量、模态刚度、固有频率及阻尼比。
由此可得

由式(7)可知,系统各阶模态的固有频率反映了系统的刚度。系统的刚度越高,固有频率就越高。
3.主要设计过程或试验过程
1)风扇叶片加工变形振动仿真分析
在ANSYS Workbench仿真平台中使用Static Structural模块建立风扇叶片加工变形有限元分析模型,如图6所示。在叶身上选取不同的部位施加切削载荷,计算叶片变形情况,获得变形让刀量。分析结果表明,在叶片加工过程中,进排气边和阻尼台附近刚度低,容易发生严重的变形。由于叶片变形分布不均匀、不规则,因此难以通过刀具轨迹补偿方法消除误差,需要提高叶片加工刚度,减小加工变形。

图6 风扇叶片变形仿真结果
在ANSYS Workbench中使用Modal模块和Harmonic Response模块建立风扇叶片振动状态分析有限元模型,对风扇叶片加工进行了模态分析和谐响应分析,得到了风扇叶片前六阶固有频率和谐响应谱线,如图7所示。分析结果表明,叶片在切削载荷的激励频率下会发生显著振动,在进排气边处尤为严重,对叶片加工产生不良影响。

图7 风扇叶片的一阶模态
由于切削载荷的激励频率低于一阶固有频率,因此,抑制切削振动的办法是提高叶片加工工艺系统的固有频率,即提升叶片加工刚度,从而实现减小振动的目标。
2)风扇叶片加工专用工艺装备设计
为了实现叶片加工刚度提升,本文提出了一种通过两端夹持和回转中心架实现定位、夹紧和辅助支撑从而提升工艺系统加工刚度的大涵道比风扇叶片专用工艺装备。首先,受到细长轴车削工艺中的中心架启发,结合风扇叶片的实际生产工艺,分析了风扇叶片专用工艺装备的功能需求,完成了工装概念设计;其次,确定了风扇叶片的定位夹紧方案,对专用工艺装备的机械结构和液压系统进行了详细设计,得到了专用工艺装备的装配体三维模型与加工图纸;最后,给出了专用工艺装备在风扇叶片加工工艺中的工作流程。大涵道比风扇叶片专用工艺装备包括底板、榫头叶尖夹持机构、回转中心架机构以及中心架体轴向移动机构,能够自适应叶身曲面结构进行夹持,避免过大的装夹变形,同时满足风扇叶片螺旋铣削加工方式的运动需求。
3)风扇叶片加工案例研究
以某型钛合金风扇叶片的加工过程为案例,建立了“叶片—工装”系统有限元仿真分析模型,对叶片加工过程的变形和振动进行了仿真研究,同时对比了3种工装方案在叶片加工过程中的表现。分析结果表明,本文设计的大涵道比风扇叶片专用工艺装备能够显著提高“叶片—工装”系统的加工刚度,提高工艺系统的固有频率,将加工叶片刚度薄弱部位时的变形让刀量和振动幅值降低50%以上,保证了叶片加工的稳定性,有助于实现提高叶片加工的尺寸精度和表面质量的目标,如图8所示。

图8 “叶片—工装”系统变形分析结果
4.结论
通过对风扇叶片加工过程的变形进行理论研究和仿真分析,建立了风扇叶片变形让刀量定量计算方法,揭示了风扇叶片变形让刀的机理与分布规律,得出结论:因叶片横截面厚度不均匀、刚度不一致,加工较薄部位时会产生严重的扭转变形;叶片具有复杂阻尼台结构,加工阻尼台附近区域时叶片变形让刀显著。由于叶片变形分布不均匀、不规则,因此难以通过刀具轨迹补偿方法消除误差,需要提高叶片加工刚度、减小加工变形。
通过对风扇叶片加工进行了模态分析和谐响应分析,得出结论:叶片在切削载荷的激励频率下会发生显著振动,在进排气边处尤为严重,对叶片加工产生了不良影响。由于切削载荷的激励频率低于一阶固有频率,因此,抑制切削振动的解决办法是提高叶片加工工艺系统的固有频率,即提升叶片加工刚度,从而实现减小振动的目标。
基于工艺系统刚度提升的思想,研制了大涵道比风扇叶片加工专用工艺装备。通过风扇叶片加工案例研究,得出结论:风扇叶片专用工艺装备能够降低的刚度薄弱部位的变形让刀量超过50%,并能够提高工艺系统的一阶固有频率,有利于减小振动,非常显著地提高扭转振型的固有频率,表明专用工装能够提高叶片加工刚度,尤其有利于抑制叶片的扭转变形,同时工装能使叶片加工过程振幅下降超过50%,而且使振动更加稳定,有利于提高叶片加工的尺寸精度和表面质量。
5.创新点
(1)本设计针对大涵道比风扇叶片加工的尺寸精度和表面质量提升这一难题,建立了风扇叶片加工动力学模型,揭示了风扇叶片加工变形与振动的机理。
(2)本设计基于工艺系统刚度提升的思想,研制了大涵道比风扇叶片加工专用工艺装备,实现了叶身自适应随动柔性的辅助支撑。
(3)通过案例研究与仿真分析,本设计研究了专用工艺装备在叶片加工过程中所起的作用,表明专用工艺装备能够显著减小加工过程的变形让刀量和振动幅值。
6.设计图或作品实物图
大涵道比风扇叶片加工专用工艺装备设计如图9所示,其实物如图10所示。

图9 大涵道比风扇叶片加工专用工艺装备设计

图10 大涵道比风扇叶片加工专用工艺装备实物