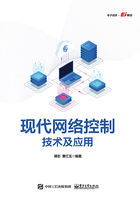
1.1 自动控制的发展过程
自动控制的发展与工业生产的发展是密不可分的,主要经历了气动控制系统、模拟控制系统、集中式控制系统、分布式控制系统、现场总线控制系统、工业网络控制系统、无线网络控制系统、物联网控制系统和信息物理系统等阶段。
1)气动控制系统
在20世纪50年代之前,工业生产的规模还相对较小,控制设备通常是气动控制器件,安装在生产设备之上,功能比较简单,且需要操作者在现场进行实时控制。这种控制系统称为气动控制系统。操作者只能通过在现场反复巡检来监控整个生产过程,人为地调节被控对象的预设值。另外,在气动控制系统中,仪表信息无法自动传输到管理系统,整个系统比较封闭,不利于信息的快速获取。
2)模拟控制系统
在20世纪50年代初期,随着工业生产规模的不断扩大,对自动控制的需求也在日益增加。模拟控制系统在生产设备上增加电动单元组合仪表,传输的信号是模拟信号,采用点对点的连接方式。电动单元组合仪表将釆集的信号传输到中央控制器进行检测,以便实现信号的远程控制。由于模拟信号的传输比较困难,且信号变化慢、抗干扰性差,因此模拟控制系统很难实现高精度的控制。
3)集中式控制系统
在20世纪60年代到70年代,现代控制理论得到了快速的发展,产生了PID控制、最优控制、自适应控制、鲁棒控制、智能控制等方法,出现了集中式控制系统。集中式控制系统是计算机控制系统(Computer Control System,CCS)的一个阶段。计算机控制系统的发展经历了三个阶段:直接数字控制(Direct Digital Control,DDC)系统、集中式控制系统和分层控制系统。直接数字控制系统使用一台计算机来代替模拟控制器,首先通过A/D转换器将生产过程中的模拟信号转换成数字信号,然后由计算机对数字信号进行处理,接着通过D/A转换器将处理后的数字信号转换成模拟信号,最后将模拟信号发送到执行器,从而使整个控制系统构成了一个闭环控制回路。
集中式控制系统通过一个功能强大的计算机来控制所有的被控对象,系统的组件采用有线的点对点连接方式。集中式控制系统可以看成单个系统控制理念和策略的扩展。由于集中式控制系统通过一台计算机来实现过程监测,数据收集、处理、存储和报告等过程控制功能,以及生产调度和管理的部分功能,将几乎所有的功能都集中在一起,因此存在一个潜在的致命问题,一旦计算机发生故障,就会导致所有的控制回路瘫痪。
集中式控制系统的潜在致命问题促使计算机控制系统进行了功能的分散化,形成了过程控制功能与显示功能分离的分层控制系统。在分层控制系统中,各控制回路的仪表调节器由计算机控制,并且各控制回路相互独立,可避免某一控制回路出现故障而影响其他控制回路的现象,使整个系统的可靠性得到了提高。现场信号传输到上一级计算机系统,计算机根据被控对象的数学模型进行优化处理,从而获得最优参数,并将最优参数当成设定值来传输到下层计算机。
4)分布式控制系统
随着工业生产规模的扩大,传感回路和控制回路的数量急剧增加,控制系统的布线变得非常复杂,成本也大大增加,抗干扰能力逐渐变差,并且维护和扩展也变得越来越困难。由相互独立的控制回路组成的控制系统难以满足工业生产对生产控制的综合要求。随着计算机技术的发展,在线集中处理大量实时数据成为可能,出现了集散控制系统。集散控制系统的网络拓扑特征是分层布线,通过数据通信实现分散控制、集中管理,并逐步发展成分布式控制系统(Distributed Control System,DCS)。分布式控制系统是控制系统发展史上的一个重要里程碑,是网络技术、计算机技术和控制技术相互融合的产物。
分布式控制系统不需要中央控制单元,在传感器中嵌入了成本低廉但功能强大的微处理器。传感器之间通过有线网络或无线网络来传输信号和数据,集成了控制功能和通信功能,实现了控制功能的模块化和智能化。分布式控制系统是一种对生产进行集中管理、分散控制的计算机控制系统,是一种集通信、计算机、显示和控制等多种技术于一体的控制系统。
分布式控制系统分为现场级、控制级和监控级,是信号处理、测量、计算机、通信和人机接口等先进技术互相发展、促进、渗透的产物。与集中式控制系统相比,分布式控制系统具有友好性、协调性、自主性、风险分散、可靠性高和成本低等特点。但由于早期计算机系统的封闭性,各厂家的分布式控制系统无法,不能连接在一起,难以实现互换与互操作,在组成更大范围的系统时存在很多困难。
1975年,美国霍尼韦尔(Honeywell)公司推出了第一套综合分布式控制系统TDC2000,该系统首次采用计算机代替模拟仪表。自此以后,分布式控制系统越来越成熟,随着计算机技术、网络技术、容错技术和人机接口技术的快速发展,以及数据通信链路的标准化、开放系统互连模型的出现和现场总线技术的日益成熟,使分布式控制系统得到了全新的发展。目前,分布式控制系统已经在石油、电力、冶金、化工、制药、建材等行业得到广泛应用。
5)现场总线控制系统
随着微处理器、控制、计算机、通信、网络等技术的发展和应用,出现了可进行数据采集、处理、传输和优化控制的智能设备。与此同时,工业生产对控制系统的精度、可操作性和可维护性等提出了新的要求,使控制系统的结构向扁平化、开放式的方向发展。信息技术的迅速发展,使自动化系统的结构发生了变革,分布式控制系统中通信必须由专用网络来实现的封闭性缺陷日益彰显。各大公司为保护自身的经济利益,在其推出的分布式控制系统中均采用了专用网络,不利于厂级、企业级设备的更新和维护。现场总线控制系统(Fieldbus Control System,FCS)就是顺应这一形势而发展起来的新技术。现场总线控制系统采用双绞线、同轴电缆或光纤来传输数字信号,可减少通信线缆的使用量,提高控制系统的可靠性和抗干扰能力。现场总线控制系统将控制功能彻底地分散到了现场设备中,是控制器在物理上彻底分散化、数据传输数字化和控制系统完全开放的新一代控制系统。
现场总线控制系统使用标准化的设计方案,改变了分布式控制系统的封闭性,解决了专用网络的问题,从而使遵循同一协议、不同厂商的设备可以通过现场总线网络连接成一个控制系统,实现了控制系统的自动化功能,逐步形成了以网络集成自动化系统为基础的企业信息系统。现场总线控制系统依靠现场的智能设备来实现基本的控制操作。
现场总线是一种连接现场设备及控制系统的双向数字通信协议,是控制系统的底层通信协议,具有双向数字传输的功能。在现场总线控制系统中,允许现场设备实现全数字化、多变量、双向、多节点,可通过一条传输线来交换信息。现场设备或现场仪表,如执行器、传感器、变送器等都是现场总线中的节点。虽然现场总线的结构遵循国际标准化组织(ISO)的开放系统互连(Open System Interconnect,OSI)模型,但不同现场总线的结构又不尽相同。现场总线既是计算机网络技术在控制系统底层的应用,也是现场网络技术和自动控制技术的有机结合。
现场总线技术,尤其是目前的无线总线技术,是未来控制技术发展的主要方向之一。凭借现场总线的技术优势和价格优势,现场总线技术已成为控制系统中的核心技术之一。现场总线控制系统的主要特点如下:
(1)现场总线控制系统广泛采用标准的数字智能设备,实现了信息处理的现场化,降低了控制系统对控制器的依赖,可实现边运行、边扩展。
(2)现场总线控制系统是开放的系统,遵循同一协议的不同设备可接入同一现场总线。
(3)现场总线控制系统在现场实现了D/A转换与A/D转换,实现了全数字化的通信,提高了信号的精度。
(4)现场总线控制系统的现场设备可以发送多变量信息,能够对现场设备进行远程诊断、维护和组态。
(5)与分布式控制系统相比,现场总线控制系统可以省去相当数量的I/O接口及其配套设备,可节省大量的线缆和敷设线缆用的桥架,因此可节省设计、安装和维护等方面的费用。
(6)现场总线控制系统具备本质安全的特征,适用于危险环境和恶劣环境。
6)工业网络控制系统
工业网络控制技术可分为工业以太网控制技术和工业无线网络控制技术。
无论分布式控制系统,还是现场总线控制系统,都根据控制系统对网络特性的不同要求将其分为若干层。层数越多,控制系统就越复杂,就越不利于控制系统的维护、诊断和扩展。由于现场总线有多种类型,不同类型的现场总线采用了专用的通信协议,现场设备之间无法相互兼容,无法实现互操作和协同工作,因此也无法实现信息的无缝集成。在工业自动化的发展过程中,通信协议已成为关键,用户对统一通信协议和网络的需求日益迫切。在这种需求下,基于TCP/IP协议的以太网开始进入工业控制领域并得到了快速的发展。工业以太网利用交换式以太网技术作为控制站、现场设备和监控站的连接通道,为现场设备的协同过工作提供一种交互机制,并可实现企业局域网与互联网的无缝集成,从而使控制系统的网络结构变得更加简洁。
目前,工业以太网已经成为工业控制领域的研究热点之一,在监控层上逐渐占据主流地位,正在向现场设备层发展。工业以太网将成为工业控制领域未来网络结构的主要形式,可真正实现控制系统一网到底的目标。以太网是应用范围最广的一种网络技术。20世纪70年代,DEC、Intel和Xerox等公司研发了以太网,采用带冲突检测的载波监听多路访问(CSMA/CD)。设计以太网的最初目的是使网络授权用户之间的通信不受传输媒介的限制,网络授权用户可以使用多种传输媒介,如同轴电缆、双绞线、微波、光纤等,从而有效实现网络资源的共享。正是由于这一功能,才使得以太网技术得到了迅猛的发展。
随着计算机网络技术的发展,以太网已渗透到了社会生活、企业管理的各个角落。企业局域网一般采用以太网,将以太网应用于工业控制系统并与企业局域网连接,可破除网络用户在地理位置上的束缚。用户可通过接入局域网的任何一台计算机来监控工业现场设备的运行过程,真正实现“管控一体化”。
随着以太网技术的广泛应用,人们积累了大量关于以太网技术的知识和技术,为工业以太网的持续发展提供了条件。在工业控制领域使用以太网,符合控制系统网络结构扁平化的发展趋势。随着计算机通信技术的进一步发展,在外因与内因的综合作用下,将激发工业以太网技术的发展潜力,促进工业过程自动控制领域的进步与发展。
以太网在信息网络领域获得了巨大的成功,得到了广泛的应用,几乎所有的编程语言(如Visual C++、Visual Basic、Delphi、Java等)都可以用于以太网的开发。以太网的特点如下:
(1)技术先进,发展迅速,数据传输速率高,能提供足够的带宽。目前,100 Mbit/s、l000 Mbit/s、10 Gbit/s、1000 Gbit/s的以太网已经得到广泛的应用。现场总线的数据传输速率一般在12 Mbit/s以下,以太网的数据传输速率要比现场总线快得多,完全可以满足工业网络控制系统不断增长的带宽需求。
(2)由于采用相同的通信协议,以太网容易和采用TCP/IP协议的产品集成到一起,应用范围广。
(3)以太网的资源共享能力强,可在同一总线上运行不同的传输协议,从而建立企业的公共网络平台或基础构架。
(4)以太网具有很强的发展潜力,在整个网络中,以太网采用交互式和开放的数据存取技术。
(5)以太网允许使用不同的物理媒介和网络拓扑结构,市场上能提供数量众多的用于设置、维护和诊断的工具,形成了统一的标准。
目前,几个主要的现场总线组织也在开发基于以太网的现场总线协议。例如,IEC 61158标准定义了高速以太网(High Speed Ethernet,HSE)协议,用高速以太网作为H2的一种替代方案,选用100 Mbit/s的以太网的物理层协议、数据链路层协议,可以使用低成本的以太网芯片、集线器、中继器和线缆。施耐德(Schneider)公司将以太网应用于信息管理层、监控层、现场设备层,采用互联网技术,推出了基于嵌入式Web的“透明工厂”。
浙江浙大中控信息技术有限公司推出了基于EPC(Ethernet for Process Control)的分布式控制系统,将以太网直接应用于变送器、执行器、控制器等现场设备的通信,用以太网统一从现场设备层、控制层到管理层等所有层次的网络,即所谓的“E网到底”。
以太网以其良好的开放性、广泛的适用性和低廉的价格等优势,不仅在商业领域得到了广泛的应用,而且在工业控制领域也得到了大规模的应用,如企业管理层的应用等。目前,以太网已成为工业控制系统管理层的通信方式,与各种现场总线的接口也在不断涌现,工业控制领域已将以太网看成其主要的通信标准。
工业环境中往往存在大量的设备和线缆,维修维护的成本非常高。负载驱动开环等引起的集簇电磁干扰,极大地影响了通信的可靠性。由于无线网络具有低成本、低能耗、高灵活性、强扩展性等特点,成为工业网络控制系统的研究和应用热点,引领着未来工业网络控制系统朝微型化、智能化、网络化、无线化的方向发展。
7)无线网络控制系统
在工业环境中,上述的网络控制系统都采用有线网络将大量的传感器、执行器、现场设备与控制器连接在一起,虽然能够实现被控对象的远程控制,但布线复杂、施工工期长、成本高、维护困难。
进入21世纪以后,随着低成本的传感器技术、快速计算技术和无线通信技术的发展,出现了无线传感器网络(Wireless Sensor Network,WSN)。无线传感器网络由大量的无线传感器组成,常用于军事、环境监测、健康护理、智能家居、城市交通、空间探索、大型车间和车库管理等领域。
目前,传感器技术已被《国家中长期科学和技术发展规划纲要(2006——2020年)》列入科技发展的前沿技术。无线传感器网络表现出的低成本、低功耗、自组织、易部署和易维护等特点,引起了工业控制领域的高度关注。由无线传感器网络衍生出的工业无线技术已形成国际标准(如无线HART、ISA100.11a和WIA-PA等),并进入了应用阶段。这些工业无线技术是继现场总线之后,工业控制领域新的研究热点,是降低工业控制系统成本、扩展应用范畴的革命性技术。一种面向工业应用、融合工业无线技术的新型网络控制系统应运而生,即无线网络控制系统(Wireless Networked Control Systems,WNCS)。无线网络控制系统的出现,突破了有线网络控制系统的体系结构,利用无线网络的优势,形成了新型的泛在控制方式,提高了系统的在线诊断能力,增强了系统的灵活性和可靠性,能够解决由于安装困难、位置偏远或安装费用高等原因产生的控制“盲点”难题,能够有效提高企业的生产效率和安全性,大幅降低运营和维护成本,受到工业控制领域的广泛关注。
8)物联网控制系统
网络控制系统是伴随着控制技术、网络技术和计算机应用技术的迅速发展而形成的一种新型控制系统,备受工业控制领域的关注。物联网概念的提出和物联网技术的不断涌现,又为控制系统的网络化发展提供了新的机遇和挑战,以物联网为基础的控制系统已成为下一代控制系统的发展方向之一。
物联网控制系统的优势在于,任何被授权的人或设备(Anyone or Any equipments)都可在任何地点(Anywhere)、任何时间(Anytime)安全地对现场设备进行监测和控制,简称“3个Any”和“1个控制”。
物联网控制系统具有组装简便、交互快捷、扩展容易和诊断准确等特点,是现代网络控制系统的延伸与扩展。可以预见,在制造业和智能家居等领域中,物联网控制系统及其应用具有巨大的商业价值。
9)信息物理系统
信息物理系统(Cyber-Physical Systems,CPS)是深度融合了物理环境与3C(Computation,Communication,Control)技术,注重计算资源与物理资源结合与协同的大规模、多维复杂系统。2006年,美国科学院提交的报告《美国竞争力计划》将信息物理系统列为重要项目;2007年,美国总统科学技术顾问委员会在报告《挑战下的领先——竞争世界中的信息技术研发》中将信息物理系统列为美国8个重要信息技术之首。2011年4月,我国工业和信息化部、科学技术部、财政部、商务部、国务院国有资产监督管理委员会联合印发了《关于加快推进信息化与工业化深度融合的若干意见》。由此可见,信息物理系统已经成为国内外工程与学术界密切关注的下一代智能系统。
近年来,随着信息物理系统的日益普及及其规模的不断扩大,信息物理系统在地域上分散的基本逻辑功能单元(如传感器、执行器和控制器等)将越来越依靠通信网络才能更有效地完成信息的交互,通过远程、安全、可靠、高效、实时、协作的方式监测和控制物理设备。可靠的大规模网络成为支撑信息物理系统发展的关键技术。当前,随着物联网、智能电网、无线传感器网络等技术的快速发展,面向大规模网络化智能泛在监测系统和基于反馈机制的网络控制系统的理论与应用越来越受到学者的重视,成为信息物理系统中最具挑战性的前沿课题。