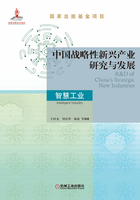
2.3 工业现场智能感知架构
2.3.1 工业现场智能感知需求分析
工业现场环境复杂,车间管理难度较大,传统的车间管理方式实时性较差,生产数据获取能力较弱,且存在较强的人员主观性、易出现数据遗漏或错误等问题,降低了制造车间的生产能力,影响了制造业的经济效益,难以满足管理层对车间制造过程高效化和透明化的需求。在“工业4.0”的浪潮之下,为实现传统工业现场向智能车间的转型升级,对生产过程的智能感知至关重要。工业现场智能感知技术可主动获取大量生产过程数据信息,帮助管理层实时掌握车间生产状况,提升车间决策的及时性和准确性。工业现场智能感知技术需求主要包括以下几个方面:
1)生产要素信息采集。采用RFID技术实现生产要素信息采集。RFID技术作为一种非接触式自动识别技术,具备非可视化识别、移动识别、多目标识别等能力,因此工业现场生产要素可采用附着或悬挂RFID标签的方式进行标识,RFID标签与生产要素为一一映射关系,即每个RFID标签仅对应一个或一批生产要素,RFID标签内存储了该生产要素的基本属性信息。RFID技术采集的信息不仅包括生产要素基本数据的静态信息,还包括制造过程中生产要素的实时状态等动态信息,根据RFID数据可实时更新在制品加工情况、物料使用情况、工装工具位置情况等。基于RFID技术的生产要素信息采集能够确保数据采集的实时性和准确性,完善工业制造过程中生产数据的管理。
2)生产要素区域定位。在传统的工业现场,生产要素的位置信息获取主要通过工作人员现场勘查的方式,存在位置信息迟延、不准确、所需时间成本高等问题,难以保证位置信息的可靠性和实时性。采用RFID技术可对制造现场的生产要素进行区域定位,当携带RFID标签的生产要素被RFID读写器感知后,将生成RFID感知记录。该条记录包含RFID标签编码、RFID读写器编码及读取时间等信息,通过感知记录内RFID读写器的编码,可以确定该生产要素的位置区域,帮助工作人员实时定位车间生产要素,避免了在车间大范围搜索某生产要素,减少了时间成本,提高了车间制造效率。
3)制造过程实时监控。传统工业制造过程仍处于黑箱状态,管理层不能直观了解车间生产状态,车间缺乏实时控制能力。传统工业现场出现机床故障或生产瓶颈时,管理层难以及时获得机床故障信息或生产瓶颈状态,无法重新进行资源分配与生产调度,严重影响了车间的生产效率,因此企业迫切希望能够对制造过程实时监控,实时掌握制造过程状态。在制造车间的生产工位和关键位置部署RFID设备,采集生产过程相关数据信息,为车间管理人员提供车间实时生产情况,以便及时调整生产计划,合理安排制造资源。
4)制造过程追溯。传统工业制造过程追溯性较差,仅通过纸质文档记录相关制造信息,难以帮助管理层掌握产品在车间的整个生产过程。在工业现场应用RFID技术时,若车间生产的产品出现问题,可通过产品的RFID感知记录快速查询到该产品的加工工位,各工位加工开始时间、结束时间,以及操作人员信息,从而确定导致该产品问题的原因,并针对该原因,如设备故障、工人操作不规范等,提出合理的改进策略,提升制造车间产品的良品率。基于RFID技术对制造过程追溯,可为评估车间设备部署的合理性和优化车间生产提供数据支撑。
5)数据处理与信息推送。工业制造过程采集到的RFID数据量庞大,且包含许多没有价值的信息,因此需对RFID数据预处理,消除冗余数据和错误数据,提高数据的信息粒度和应用价值。原始的标签读取事件难以被车间工作人员理解,采用RFID复杂事件处理技术可从大量的标签读取事件中推理出语义层级更高的复杂事件,并将复杂事件信息按照订阅规则推送给车间管理人员,使得管理层能够实时获取所需信息,对车间生产状况进行科学判断和合理决策。