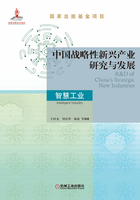
1.2.7 数字孪生
随着新一代信息技术(如云计算、物联网、大数据等)与制造业的融合与落地应用,世界各国纷纷出台了各自的先进制造发展战略,如美国工业互联网和德国工业4.0,其目的之一是借力新一代信息技术,实现制造的物理世界和信息世界的互联互通与智能化操作,进而实现智慧工业。其核心是促进新一代信息技术和人工智能技术与制造业深度融合,推动实体经济转型升级,大力发展智慧工业。因此,如何实现制造物理世界与信息世界的交互与共融,是当前国内外实践智慧工业理念和目标所共同面临的核心瓶颈之一。作为一种充分利用模型、数据、智能并集成多学科的技术,数字孪生面向产品全生命周期过程,发挥连接物理世界和信息世界的桥梁和纽带作用,提供更加实时、高效、智能的服务。
许多国际著名企业已开始探索数字孪生技术在产品设计、制造和服务等方面的应用。在产品设计方面,针对复杂产品创新设计,达索公司建立了基于数字孪生的3D体验平台,利用用户交互反馈的信息不断改进信息世界中的产品设计模型,并反馈到物理实体产品改进中。在生产制造方面,西门子基于数字孪生理念构建了整合制造流程的生产系统模型,形成了基于模型的虚拟企业和基于自动化技术的企业镜像,支持企业涵盖其整个价值链的整合及数字化转型,并在西门子工业设备的生产流程中开展了应用验证。在故障预测与健康管理方面,美国国家航空航天局将物理系统与其等效的虚拟系统相结合,研究了基于数字孪生的复杂系统故障预测与消除方法,并应用在飞机、飞行器、运载火箭等飞行系统的健康管理中。美国空军研究实验室结构科学中心通过将超高保真的飞机虚拟模型与影响飞行的结构偏差和温度计算模型相结合,开展了基于数字孪生的飞机结构寿命预测。在产品服务方面,PTC公司将数字孪生作为智能互联产品的关键性环节,致力于在虚拟世界与现实世界间建立一个实时的连接,将智能产品的每一个动作延伸到下一个产品设计周期,并能实现产品的预测性维修,为客户提供高效的产品售后服务与支持。此外,车间是制造活动的执行基础,为践行智慧工业和智能生产理念,陶飞等于2016年探索了数字孪生车间的概念,设计了数字孪生系统(DTS)的组成与运行机制,阐述了实现DTS的四个特点和五大类关键技术,为数字孪生在生产制造环节落地应用提供了基础理论支撑参考,探讨了数字孪生模型在产品构型管理中的应用。张浩等提出了基于数字孪生的个性化产线快速定制设计方法,将数字化模型和物理装备虚实同步,形成整线的数字孪生系统;提出生产过程中耦合优化问题的解耦算法,作为引擎驱动数字孪生;通过订单模拟投放与运行,进行整线性能评估与调控。王军强等面向物联制造车间,立足工件、机器的主观能动性,提出了主动调度模式,探讨了主动调度的交互体系、响应机制、运作模式和互调度行为。张迎峰等针对智能工厂制造资源自组织配置与自适应协同控制需求,提出了基于CPS的底层制造资源加工服务状态实时感知和自主决策的智能化建模方法。屈挺等利用数字孪生思想将物联制造下的在线控制理念进行扩展,提出多系统联动优化控制思想、机制及定量优化方法,并应用于生产过程的精准计划、实时跟踪与动态控制三个阶段,相应技术和系统已在嘉宝莉化工集团等行业龙头企业应用实施。