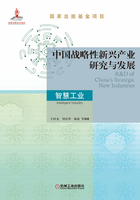
1.2.4 智能装备
人工智能、云计算、物联网等技术的快速发展推动主要工业国家提出了面向智慧工业的战略规划,助推制造业从数字制造向智慧工业转型升级,在以数据和信息处理为核心的数字制造系统的基础上,自动化装备融合智能感知、智能规划、智能控制等技术,构成了以知识和推理为核心的智慧工业系统。
在具体的转型升级方式上,工业机器人作为一种自动化装备,通过与智能技术、工艺数字化技术等先进技术融合,实现了面向不同作业场景、作业任务、作业工艺的智能化应用,加快了制造业的转型升级进程。工业机器人的关键技术有智能视觉感知系统、三维环境重建技术、位姿估计技术与运动规划技术。
智能视觉感知系统是机器人集成应用系统的重要组成部分,以非接触的方式为机器人提供丰富的二维和三维信息。冯明涛研究基于深度学习的机器人视觉三维感知与识别方法,在复杂的三维工业场景中,引入二维和三维视觉系统,基于视觉重建和理解技术,完成机器人智能化应用环节中的环境建模、位姿估计等任务。
三维环境重建技术是以数学的方式描述真实的三维作业空间内机器人、工件及障碍物的立体信息。三维重建的模型通常是以点云的形式进行描述和存储,研究者通常将基于点云数据的建模方法与三维栅格结合,离散化的栅格可以加快密集点云数据的处理。
位姿估计是对局部高精度三维重建模型的进一步处理,目的是获取目标工件相对于工业机器人基坐标系的立体位姿信息,主要分为基于点特征类算法、基于模板匹配类算法及基于深度学习类算法。Guo等研究了基于点特征的物体位姿估计算法,先根据待识别的物体外形提取显著特征点,并构建了基于点云的特征描述子,然后基于特征描述子在物体原始点云模型中搜索与其特征匹配的点位,利用点云配准中的迭代最近点(Iterative Closest Point, ICP)算法求解两者的相对空间变换矩阵。张昊若基于模板匹配的物体位姿估计算法,借鉴图像识别领域的思想,在离线阶段建立了待识别物体在不同位姿状态下的模板库,在线阶段将视觉传感器获取的数据与模板库中的模板快速匹配,获得相似度最高的模板,从而确定待识别物体的最终位姿。Fu等利用端到端的深度学习方式对视觉采集的数据进行训练,输出工件的位姿。Zhuang等根据RGB-D数据的特点,利用基于卷积神经网络的实例分割算法提取目标物体的轮廓及像素占据信息,获得目标物体的点云,再基于点云配准算法求解目标物体的位姿。
运动规划是基于约束条件在机器人的自由构型或工作空间中搜索出一系列中间位姿,使机器人从初始位姿安全地运动到目标位姿。面向静态环境的运动规划技术主要有随机采样算法和基于深度学习的运动规划算法等。基于随机采样的运动规划算法有随机路图(Probabilistic RoadMaps, PRM)法,在工作环境不变的情况下,在预处理阶段构建高维空间的路图,在查询阶段利用图搜索算法确定最优路径。基于深度强化学习的运动规划算法是将深度学习与自监督学习的强化学习相结合,通过机器人自主地与场景互动,观测并记录场景反馈,并以行动试错和奖励的方式进行训练,根据结果优化行动策略,获得贴近人类决策方式的结果。面向动态环境的运动规划技术通常也有两类方法:反应式控制和全局运动规划。反应式控制通常基于人工势场(Artificial Potential Field, APF)法构建控制策略,用于局部动态避障;全局运动规划则是在整个机器人构型空间内搜索可行的路径,典型的算法是一种基于PRM的动态路图法。
目前,我国的工业机器人发展仍与世界先进水平存在一定差距,需认清形势、明确发展目标,制定符合我国国情的发展战略与政策,攻克核心零部件、新型传感器、人机交互、人工智能等关键技术,把握市场动向,建立有效的监管和安全机制,顺利完成工业机器人的转型和升级。工业机器人应用应与大数据相融合、与模式识别相融合、与虚拟现实融合以及与精益生产相融合,只有通过与智能技术、工艺数字化技术等先进技术融合,才能实现面向不同作业场景、作业任务、作业工艺的智能化应用,才能加快制造业的转型升级进程,才能趋向于智能化、智慧化、“人机共融”发展。
传统的材料成型方法,在新时代、新需求下面临着效率不高、效果不好、甚至无法使用的问题。3D打印技术的出现和发展,并不是为了颠覆传统的材料成型方法,而是立足于在目前材料已有的加工和成型技术基础上,应对新材料成型技术上的挑战。3D打印已经在小批量、个性化的材料制造方面展现出了它的价值,比如航空制造业、医学人体影像的实体成型等。在需要大批量制备的产品开发过程中,3D打印也能发挥它在成型应用上的优势,为新的结构设计和外形设计提供宝贵的预研条件。
3D打印采用了一种分层制造、叠加成型的全新制造方式,是一种集计算机辅助设计(CAD)、计算机辅助制造(CAM)、计算机数字控制(CNC)、激光、精密伺服驱动系统等于一体的先进制造技术。其原理主要是依照在计算机上构建的三维模型,并通过相应的切片软件进行数字切片处理,获取三维模型垂直方向上各层截面的轮廓信息,相应的成型执行元件(激光头或喷头)在控制系统的驱动下按照各层截面的轮廓信息进行规律性的扫描动作,有选择地切割、固化每层材料,经过材料层层叠加、黏结,最终实现三维实体的制造。虽然目前传统的制造行业并不能够完全被新兴的3D打印技术所取代,但3D打印技术的问世无疑为制造业带来了美好的前景,尤其在工艺成型方面是一场全面的技术革新,减少了烦琐的工序,降低了工件的制造成本,提高了生产效率。
20世纪60年代,最先由美国的科研工作者将计算机技术与机床的制造工艺结合起来,生产出世界上第一台数控机床。由于集成了计算机技术,这台机床能够自动执行机械零件的加工任务。这项技术赋予了传统机床新的生命力。随着后续工业技术的发展以及新工艺在机床上的应用,数控机床在复杂精密的零件制造中大展身手。此外,数控系统也逐渐具备了数字化以及智能化的特征。继第一台数控机床研制成功后,欧美国家又对数控机床的结构设计进行了多次改进,并且对数控机床的应用领域也进行了更广泛的探索。数控机床的发展大体上可以分为三个阶段。科研人员首先对十字架形机床进行了研究与设计改进,在此基础上又研制出龙门形数控机床,解决了工业化不断发展的背景下大型零部件加工的难题,大大提高了工业生产的效率。目前,德国的多家机床厂商在数控铣床的研发领域表现出较高的水平。其通过在龙门形机床上安装专门的机械式手臂,然后搭配使用五轴控制系统,实现机械式手臂的灵活摆动,从而可以生产出对精密度要求更高的零件。与此同时,在机床运转过程中,还伴随有感应器和跟踪探头,能够对运行的轨迹进行模拟分析做出及时地调整,从而使数控技术更加智能化。