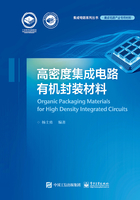
2.4.3 有芯积层基板(BUM)
随着激光钻孔技术的出现,制造可控深度的盲孔(BV)成为可能。目前,CO2激光和紫外线(UV)激光钻头技术占据主导地位,而准分子激光技术也可以使用,但数量有限。CO2激光可以穿透玻璃和有机物,但是会被Cu阻挡,目前的孔径限制为60μm或更大。因为不能钻穿铜层,所以需要通过常规光刻工艺形成所需的铜孔图案,即采用典型的曝光—显影刻蚀—剥离(DES)技术对铜箔进行刻蚀形成通孔后,采用CO2激光对树脂绝缘层进行烧蚀。
紫外线激光可以烧蚀铜及半固化片,但对两者的烧蚀速度不同,烧蚀至捕获垫处停止。如果顶部没有铜箔,则烧蚀成孔速度较快。UV激光的孔径通常为50μm或更小,可以实现最佳的生产效率。总之,CO2激光器的通量高,在市场上占据主导地位[29]。在完成激光钻孔后,形成的埋孔(BV)需要像标准PTH一样进行清洗和电镀。这在实际生产过程中遇到了许多挑战,主要包括:①由于流体动力学的局限性,溶液流动受到限制,会引起表面润湿性、扩散限制和气泡截留等问题;②在生产过程中,埋孔的典型长宽比(深度与直径之比)从0.7增加到1甚至更高,如何能够实现高质量的铜孔填充,即以最小的凹痕形成电镀埋孔是一个技术挑战。与通孔(PTH)的电镀一样,应保证电镀液向通孔中间流动,电镀发生在孔洞内而不是仅电镀在孔洞表面。
(1)两层过孔基板除钻孔过程不同外,两层过孔(ViP)基板的工艺流程与标准两层基板相同。在单侧(晶片一侧)形成的定型掩模,通过CO2激光实现通孔。芯板厚度低至80μm,顶部的埋孔直径也小至80μm。埋孔的可靠性是一个最大的技术挑战,通常要求通孔能够承受1000次以上-65~150℃的热循环而不会开裂。为此,设计了电阻变化测试考核,将数百个互连成环形链的埋孔进行热循环并定期进行电阻测试,只有当电阻变化低于百分之几时才能达到设计要求。经验表明,电阻变化主要取决于裂纹的形成,而裂纹的形成对通孔底部的清洁度、化学镀铜质量及底部的通孔形状都非常敏感。热循环测试考核也可以基于埋孔的热阻抗特性测试,可大幅缩短测试时间,主要原因是BGA焊盘可被用作埋孔的捕获焊盘。在过孔设计中,BGA焊盘旁边需要制作一个PTH焊盘,看起来像一块“狗骨头”,以提供更多空间。在激光钻孔过程中,每个面板都是一个接一个地钻孔,严重限制了产品的生产效率。另外,“狗骨式”设计具有很高的生产率,因为在机械钻孔过程中会堆叠两个或更多的核心,也可以使用没有“狗骨头”的PTH,但是PTH必须填充环氧树脂和镀帽,填充过程需要后填充研磨,以去除多余的环氧树脂。这个过程需要仔细控制磨削压力,以避免芯棒拉伸和撕裂。激光钻孔速度的提高促进了X通孔的引入。这些X通孔在电镀过程中很容易被铜填充。X通孔提供了更小的捕获板,从而提供了更高的布线密度。
(2)1+2+1四层基板是一系列依次构建的高密度基板中的第一个。最简单的形式是将带有PTH、常规PTH或X通孔的两层布线图形的芯板与半固化片和铜箔等通过层压形成四层空白芯板。激光通孔的形成和基板的完成工艺与两层ViP基板相同。将激光制作的埋孔放置在捕获板内部,要求激光器必须能够接近用于形成捕获垫的基准。理想情况下,电镀后再次使用相同的基准来显示图案。1+2+1基板也包含连接顶层和底层的PTH。需要对埋孔进行激光钻孔后再钻孔。需要修改电镀参数才能同时实现BV和PTH的电镀。BPTH呈“甜甜圈”状,即中心未被Cu覆盖,PTH在下一层的层压过程中充满了热固性树脂。为了增加布线密度,PTH可以采用Cu覆盖,因此需要额外处理:在对核心进行钻孔和电镀后,必须重新填充并电镀PTH。目前,脉冲电镀和改进的电镀化学工艺可以直接填充这些较浅的PTH,从而大大简化了工艺。BV可以位于PTH盖的顶部,在内核中使用X通孔可简化处理。
传统上,PTH封堵是通过在PTH中填充环氧树脂后,固化并研磨去除任何突出Cu表面的树脂残留物。研磨过程必须小心控制压力,否则芯棒将以不受控制的方式拉伸,从而导致较高的配准公差。另外,过度研磨也会使铜的厚度不均匀。堵孔用的环氧树脂通常填充陶瓷或二氧化硅颗粒,以减小热膨胀。在后续加工过程中,环氧树脂的高热膨胀会在铜帽上施加大量应力,并导致应力开裂。为了避免这种情况,可采用具有高玻璃化转变温度(Tg)和高填料含量的环氧树脂,以最大限度地降低热膨胀系数(CTE)。目前,批量生产的最薄1+2+1基板的厚度为180~220μm。
(3)1+4+1六层基板采用的四层芯板上带有PTH,每个PTH都有盖帽,BV则是VoP形式。除四层芯板外,其制作过程与相应的1+2+1基板基本相同。这种类型基板的应用范围有限,主要用于具有严格电源分配和屏蔽要求的情况。
(4)2+2+2六层基板从第二次层压开始,在1+2+1芯板上制作埋孔,以构建第二个积层布线层,其中埋孔为交错式BV。在电镀过程中,用铜堵住通孔,通过适当配准,实现通孔堆叠,实现进一步致密化。最终的设计是将埋孔堆叠在有盖PTH的顶部,通常PTH不存在从第一到第六层间的连接。除先进基板设计外,这种结构正成为模块和无线应用的一个非常普遍的设计。