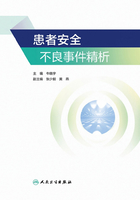
第二节 质量管理相关理论
一、全面质量管理
(一)概述
全面质量管理是把质量观念渗透到整个企业的每一项活动中,以实现质量的持续改进。它的特点为“三全一多”,即全过程的质量管理、全企业的质量管理、全员参与的质量管理和管理方法多样化。全面质量管理非常强调团队合作、提高顾客满意度和降低经营成本。在实施全面质量管理的过程中,企业鼓励管理者和员工进行跨职能、跨部门的合作,鼓励他们与客户及供应商合作,寻找各种改进机会,甚至是很小的改进。每一次质量改进都是朝着完美迈进了一步,组织追求的是零缺陷率。质量控制也就成了每一位员工日常工作的一部分,而不再是某一专门部门的责任。
(二)全面质量管理的工作方法
实施全面质量管理,可以采用许多技术方法,如质量管理小组、标杆管理、六西格玛质量原则、质量伙伴关系和持续改进等。
1.质量管理小组
质量管理小组(quality circle)是实施全面质量管理分权控制的一种方式。质量管理小组是一个由6~12名员工自愿组成的小组,这些员工定期会晤,讨论并解决影响工作质量的问题。因为他们比其他任何人更熟悉有关的工作情况,能够提出切实可行的解决办法。这些小组成员在某一规定时间召开碰头会议,发现问题,并努力找到解决办法。当然企业应训练团队成员如何组建团队,以及解决问题和控制质量的能力。
2.标杆管理
标杆管理(benchmarking)是施乐公司于1979年开始引入的管理方法,此后标杆管理迅速成为全面质量管理的一个主要方法。根据施乐公司的定义,标杆管理是参照最强劲的竞争对手或者公认的行业领袖的做法来考评本企业的产品、服务和经营的一个持续的管理过程。标杆管理分为计划、发现、收集、分析和改进五个步骤。计划包括确定研究的目标以及明显影响客户满意度的产品或服务的特征;发现是指确定需要收集信息的来源;收集是指收集相关数据;分析则是指分析收集的标杆管理数据并提出改进的建议;改进是指执行改进建议,并通过持续的标杆管理进行监测。
3.六西格玛质量原则
六西格玛质量原则(six sigma)最早由摩托罗拉公司提出。摩托罗拉公司于20世纪80年代中期开始探索提高产品质量之路,后来通用电气公司又将六西格玛质量原则发扬光大。六西格玛是一个非常了不起的质量标准,它规定每100万个零部件的缺陷率不超过3.4个,也就是要做到99.999 7%的工作时间都没有缺陷。
六西格玛质量原则建立在被称为 DMAIC,即定义(define)、测量(measure)、分析(analyze)、改进(improve)和控制(control)的五步法基础上,它为组织认识问题和解决问题提供了一种结构化的方法。有效实施六西格玛质量管理体系,需要最高管理层做出承诺,因为它要求整个组织进行广泛的变革;所有员工都需要了解六西格玛的基本原理,并支持“第一次就把事情做对”的理念。
4.质量伙伴关系
传统的质量控制人员是团队的“外部人员”,因为他们并不总是很了解自己所研究的流程,所以他们的工作可能会被怀疑或被看作是对正常工作程序的干扰。质量伙伴关系(quality partnering)则是在企业的特定功能区域内指定专业人员,质量控制人员在功能区域内与其他人员一起工作,在整个工作流程中确定质量改进的时机。这种整合式的质量伙伴关系方式得以在产品生命周期的早期发现并解决缺陷,而这个时候缺陷是最容易纠正的。这一方法的另一个优点是质量合作伙伴被视为是“内部人员”和同事,容易被工作团队接受。
5.持续改进
持续改进(continuous improvement)即在组织内部的各个领域不断地实施大量小的、累积性的、持续的改进。在成功的全面质量管理项目中,所有的员工都深知,他们被寄予厚望,要在各自的工作领域中寻找改进和变革的契机。持续改进最基本的理念就是每次改进一点,持续不断地寻求改进,日积月累,最终成功的可能性逐步增大。创新可以从最简单的事情开始,员工也可以在这种永无止境的过程中追求自己的成功。
(三)全面质量管理的工作程序
为了使质量管理活动能够有组织、有计划地按照一定的科学程序进行,在20世纪60年代,美国质量管理专家戴明把质量管理的工作过程分为计划(plan)、执行(do)、检查(check)、处理(act)四个阶段。PDCA循环是实行全面质量管理必须遵循的工作程序。
1.PDCA循环的含义
P、D、C、A分别是计划、执行、检查、处理四个英文单词的第一个字母。计划、执行、检查、处理这四个工作阶段依次运转,并且不是运转一次就完成,而是要周而复始地进行。一次循环结束、解决一些问题,但可能还有问题没有解决,或者又出现了新的问题、于是再进入下一次循环,周而复始,直到全部问题得到解决,把质量提升到更高的水平。
2.PDCA循环的内容
(1)P阶段:
即计划阶段。这个阶段的主要任务是确定质量方针与质量目标,以及与此有关的活动计划。
(2)D阶段:
即执行阶段。主要任务是按照所制定的计划,采取具体措施。
(3)C阶段:
即检查阶段。主要任务是根据计划,检查执行情况。
(4)A阶段:
即处理阶段。主要任务是根据检查的结果,采取措施,进行处理,总结经验,吸取教训。
3.实施PDCA循环的步骤
为了便于解决问题和改进工作,在具体实施PDCA循环时,可以把它分解为八个步骤。
(1)调查现状,找出存在的质量问题。
(2)分析问题,明确造成质量问题的各种原因。
(3)寻找主要原因,确定解决质量问题的方向。
(4)针对主要原因,制定解决质量问题的计划。
(5)执行所制定的计划,落实各种措施。
(6)明确应该巩固的成果,找出存在的问题。
(7)巩固所取得的成果,将成功的经验标准化。
(8)提出尚未解决或新出现的问题,将其转入下一个PDCA循环。在这些步骤中,(1)~(4)属于P阶段,(5)属于 D 阶段,(6)属于C阶段,(7)和(8)属于 A 阶段。
4.PDCA循环的特点
(1)按顺时针方向运转。
它围绕企业的方针、目标这个轴心向前转动,并且不断循环,周而复始。
(2)大环套小环。
PDCA循环不仅适用于整个企业,也适用于科室、车间、班组工序、产品以及个人。为了实现企业总的方针和目标,各级、各部门乃至每个员工,都有自己的PDCA循环。
(3)阶梯式上升。
PDCA循环不是原地转动,也不是沿水平线前进,而是在转动中逐级上升。每经过一次循环,它就上升到一个新的高度,解决一部分问题,取得一部分成果;到下一次循环,又有新的目标和内容。PDCA循环不断升级,质量也不断提高。
二、奶酪原理
(一)概念
奶酪原理是指放在一起的若干片奶酪,每一片奶酪上都有若干个洞,代表每一个作业环节可能产生的失误或技术上存在的短板,当失误发生或技术短板暴露时,光线即可穿过该片奶酪,如果这道光线与第二片奶酪洞孔的位置正好吻合,光线就穿过第二片奶酪,当许多片的奶酪的洞刚好形成串连关系时,光线就会完全穿过,此时就会发生安全事故或质量事故。
(二)基本思想
凡事只要有可能出错,那就一定会出错;或者可以说所有的漏洞只要有可能同时出现,那它们就一定会同时出现。
任何一次事故或差错的发生都并非偶然,其背后都有酿成事故的必然因素。
每个工作流程都是由若干个关键环节串联起来组成的,如果每个环节都存在一个漏洞,即上个环节提供的输出存在问题,而下一个环节把关不严,就有可能发生事故。
(三)管理应用
要尽可能地减少每一片奶酪上的“孔洞”,意味着安全生产中,“三查七对”的制度落实绝不能走过场,执行过程中不能有任何松懈和侥幸的心理。
善于发现安全隐患并有效堵塞漏洞,加强岗位风险提示和关键环节风险控制。
不要盲目相信上一个环节或前一个程序做到了准确无误,而是要不折不扣地对其进行把关,坚持从零做起。
三、海因里希法则
(一)概念
海因里希法则,又称“1∶29∶300法则”,或“300∶29∶1法则”,即1起严重伤害事故背后,有29起轻伤害事故,300起无伤害虚惊事件,以及大量的不安全行为和不安全状态存在。
1941年,美国的海因里希统计许多灾害后得出了这个法则。当时,海因里希统计了55万件机械事故,其中死亡、重伤事故1 666件,轻伤48 334件,其余则为无伤害事故。因此,他得出一个重要结论,即在机械事故中,死亡及重伤、轻伤和无伤害事故的比例为1∶29∶300,国际上把这一法则叫事故法则。这个法则说明,在机械生产过程中,每发生330起意外事件,有300件未造成人员伤害,29件造成人员轻伤,1件导致重伤或死亡。
对于不同的生产过程,不同类型的事故,上述比例关系不一定完全相同,但这个统计规律说明了在进行同一项活动中,无数次意外事件,必然导致重大伤亡事故的发生。要防止重大事故的发生必须减少和消除无伤害事故,要重视事故的苗头和未遂事故,否则终会酿成大祸。
(二)原理
海因里希首先提出了事故因果连锁论,用以阐明导致伤亡事故的各种原因及与事故间的关系。该理论认为,伤亡事故的发生不是一个孤立事件,尽管伤害可能在某瞬间突然发生,但却是一系列事件相继发生的结果。
海因里希把工业伤害事故的发生、发展过程描述为具有一定因果关系的事件的连锁发生过程,即:
(1)人员伤亡的发生是事故的结果。
(2)事故的发生是由于:①人的不安全行为;②物的不安全状态。
(3)人的不安全行为或物的不安全状态是由于人的缺点造成的。
(4)人的缺点是由于不良环境诱发的,或者是由先天的遗传因素造成的。
(三)影响因素
海因里希最初提出的事故因果连锁过程包括以下5个因素。
1.遗传及社会环境
遗传因素及环境是造成人的性格缺点的原因,遗传因素可能造成鲁莽、固执等不良性格;社会环境可能妨碍教育、助长性格上的缺点发展。
2.人的缺点
人的缺点是使人产生不安全行为或造成机械、物质不安全状态的原因,它包括鲁莽、固执、过激、神经质、轻率等性格上的先天缺点,以及缺乏安全生产知识和技能等后天缺点。
3.人的不安全行为或物的不安全状态
所谓人的不安全行为或物的不安全状态是指那些曾经引起过事故,或可能引起事故的人的行为,或机械、物质的状态,它们是造成事故的直接原因。
4.事故
事故是由于物体、物质、人或放射线的作用或反作用,使人员受到伤害或可能受到伤害的、出乎意料的、失去控制的事件。坠落、物体打击等使人员受到伤害的事件是典型的事故。
5.伤害
直接由于事故而产生的人身伤害。人们用多米诺骨牌来形象地描述这种事故因果连锁关系。在多米诺骨牌系列中,一颗骨牌被碰倒了,则将发生连锁反应,其余的骨牌相继被碰倒。如果移去连锁中的一颗骨牌,则连锁被破坏,事故过程被中止。海因里希认为,企业安全工作的中心就是防止人的不安全行为,消除机械的或物质的不安全状态,中断事故连锁的进程而避免事故的发生。
(四)管理应用
海因里希认为,人的不安全行为、物的不安全状态是导致事故的直接原因,事故预防工作的重点是消除人的不安全行为和物的不安全状态。海因里希的研究说明大多数的伤害事故都是由于人的不安全行为引起的。即使一些伤害事故是由于物的不安全状态引起的,但物的不安全状态的产生也是由于人的缺点、错误造成的。从这种认识出发,海因里希进一步追究事故发生的根本原因,认为人的缺点来源于遗传因素和人员成长的社会环境。
(罗碧如)
参考文献
[1]章帆,韩福荣 . 质量概念与质量管理理论的演化 .世界标准与质量管理[J]. 2005,4:29-31.
[2]温德成 .质量管理学[M]. 2版.北京:机械工业出版社,2018.
[3]RICHARD L. DAFT,DOROTHY MARCIC.高增安,张璐,马永红译.管理学原理[M].北京:机械工业出版社,2018.