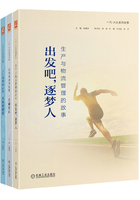
剥茧抽丝,生产平顺
作者:隋鑫
平顺有序的生产可以让汽车制造过程中的每一个环节都保持最高效率和最小偏差。然而,想要让汽车制造的每一个环节都顺起来并不容易,实现百分之百的平顺性生产更是近乎痴人说梦,毕竟大众集团排名第一的保时捷工厂也只有百分之九十多,但我们要做就做最好的!
2015年,中国汽车市场的微增态势让敏锐的生产管理人绷紧了神经,如何在真正的危机到来前成功转型,扭转粗放的生产模式,实现精益生产,以正确的姿态迎接市场变化,成为萦绕在生产管理人心头的一大难题。
恰逢此时,大众集团开始在全球推广描述整车生产过程中实际生产顺序与计划顺序一致程度的生产平顺性项目,其指数TST(日订单符合率,源于德语词汇Tagesscheibentreue)对提升生产效率、降低生产成本有着积极的指导意义。不管是提升效率,还是降低成本,都对公司在变幻莫测的市场变化中提升竞争力有至关重要的影响。生产管理部生产控制科敏锐地觉察到转型的契机,全体成员主动开始学习项目精髓,着手在一汽-大众推广平顺化生产。
5年从34%到95%
2015年6月,佛山工厂,初夏的骄阳炙烤着刚出厂的一辆辆高尔夫轿车,焊装311会议室里,研讨会的热烈气氛让炎炎夏日也黯然失色。来自大众集团的两位资深专家Meyer和Franz先生为生产管理部的同事们深入浅出地讲解着生产平顺性的基本原理。
部门中的绝大部分同事都是初次接触生产平顺性项目,对新理论的渴望和对企业美好未来的向往激励着我们,让我们如饥似渴地从外方专家的指导中汲取营养。在德方专家的讲解和指导下,生产平顺性项目组在佛山工厂开展了为期三周的研讨。随着对生产平顺化理解的逐步深入,我们心中的疑惑也一层层解开。
我带着取来的“真经”回到长春,并向窦恒言总监进行了汇报。总监对这一项目十分赞许,认为平顺化生产是供应链升级的基石,并提出了5年内实现TST 95%的目标。95%?几乎所有听到这个数字的同事都一脸惊讶。因为彼时,一汽-大众的TST仅有34%,大家都认为直接给出这么高的目标有些不切实际。“求上得中,求中得下,只有敢想才能实现。”窦总监的一句话有如一针兴奋剂,激发了大家敢想、敢拼的斗志。
90%的飞跃
秋去冬来,2015年11月,生产控制科牵头组织各工厂生产管理部、生产厂、质保、规划及管理服务部担起了这一关键任务,从无到有,组建起一汽-大众自己的生产平顺性团队。之后,我们的团队陆续对长春、成都、佛山等工厂开展调研,现地现物地分析影响因素、制定提升措施。

生产控制团队合影(右二为作者)
2016年7月,项目团队开展长春工厂奥迪A6L生产线研讨会,项目得到时任生产总监方永平、Germann先生,以及生产管理部总监窦恒言、Greaff先生的大力支持。两周时间里,团队详细梳理了奥迪A6L焊装及涂装的全部工艺过程,发现三检、奥迪特(AUDIT)、并行存储区、返修等六大类23处造成车辆滞留的具体问题点。其中,问题最严重的是返修导致的车辆滞留问题。在生产平顺性概念普及之前,几乎所有人对低平顺性生产带来的损失和严重性都没有足够的认识,返修车数量多,返修时间也没有严格掌控。生产平顺性要求提出之后,每个人都结合实际岗位反思了自己的工作。经过深入分析与反复研讨,我们决定最大化地发挥原有设备及系统的能力,制定了有效减少返修量等17项无须投资的改进措施,使生产平顺性得到了大幅提升。
之后的一年内,随着我们对生产平顺性认识的不断深入,以及行之有效的改进措施,团队陆续开展了长春工厂其他生产线及成都东、西工厂的调研。两三年的时间里,一汽-大众的生产平顺性由34%飞跃至75%。同时,项目团队结合平顺化要求,制定了平顺化生产的管理原则与指导手册,并在青岛和天津工厂建厂之初就跟进和改善生产平顺化。2018年,佛山、青岛和天津工厂部分生产线的TST陆续达到90%。
从95%到100%的质变
在新建工厂逐个取得骄人成绩后,作为“老大哥”的长春工厂,在生产平顺性问题上也必须积极面对。放任自流、等待生产线更新自行提升不是一汽-大众人的风格,凝心聚力深挖潜力实现再突破才最符合“老大哥”应有的气质。
2020年4月,新冠肺炎疫情的阴云刚刚消散,在冰雪消融的北国春城,长春工厂再掀生产平顺性提升高潮。每日开班,生产控制科计算出当日应发往总装的订单清单在团队内共享,焊装、涂装全力保障范围内订单如期发车。通过工艺重塑和人员分配,实现99%的返修工作在线完成,剩余1%的滞留返修车在4小时内修复回线。通过规范检测及奥迪特过程,实现离线检测车当日15:00前回线,保障当日发车不受影响。至此,我们已经实现了当年窦总监提出的“5年内实现TST 95%”的目标。
所有人都在为这样的骄人成绩而自豪,毕竟大众集团排名第一的保时捷工厂也只能维持这一水平。但我们该就此止步吗?显然是不行的!居功自傲、止步不前同样不是一汽-大众人的品质。此时,生产控制科陈悦经理大胆提出了100%的奋斗目标。
从34%到95%可以理解为从无到有,而从95%到100%,就需要把更细微、更复杂的问题点挑出来彻底解决,其难度不亚于5年实现TST 95%。
一汽-大众人的创变精神再一次被激发出来,通过创新的OPTIMO规则编制,创造性地发挥车身库能力,在保障发车能力的同时,保障三款奥迪车型完美发出当日计划订单,我们开展了控制到车、责任到人的全面提升工作。在返修车辆的储备环节,我们对现场做了更为精细的调整,将所有返修车按固定规律摆放。这样,在返回生产线时,就能做到先进先出,进一步提升了平顺性生产的整体水平。
2020年5月11日,在短短一个月的时间里,长春工厂AUDI-Q线TST率先实现100%,并开启了一汽-大众连续4个月蝉联大众集团全球工厂榜首之路。
勤奋终有回报,5年时间,从34%到100%。在创变精神引领下,一汽-大众平顺化生产团队依靠数字化方法和流程,在班次、小时层面继续提升着公司生产平顺性,支撑全供应链实现转型升级,塑造公司运营核心流程竞争力!使我们的企业在中国汽车市场的发展道路上拥有了更加强健的身躯。