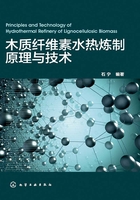
2.4.3 木质纤维素及其衍生碳水化合物生成乙酰丙酸的催化剂及生产工艺
相比于生成HMF而言,利用纤维素乃至生物质制备乙酰丙酸的技术要容易得多,这是因为乙酰丙酸在水中的稳定性较高。无机强酸如硫酸和盐酸经常被用于催化己糖水解生产乙酰丙酸[42,150-153]。早在1990—1997年,美国Biofine公司开发了一种以硫酸催化木质纤维素转化制备乙酰丙酸的生产工艺[138,154,155]。如图2-11所示,在Biofine工艺中,木质纤维素与硫酸[1.5%~3%(质量分数)]混合,在210~230℃的条件下进入第一个反应器反应13~25s,生成以HMF和单糖为主的降解液;随后,在第一个反应器中得到的反应液不断进入第二个反应器,在190~220℃的温度下继续反应15~30min而得到乙酰丙酸。利用Biofine工艺生产的乙酰丙酸收率高达70%~80%,高于其他工艺所生产的乙酰丙酸收率。然而,Biofine工艺生产乙酰丙酸及衍生物的技术在商业化生产上面临着严峻的挑战。第一,乙酰丙酸需要从无机酸催化剂中分离出来,以循环使用酸催化剂,避免在下游工艺中产生负面影响。第二,乙酰丙酸的生产浓度低,提纯/回收过程成本较高。第三,该技术中所产生的水热焦炭易堵塞管道。此外,该过程中副产物固体残渣作为燃料在进行燃烧之前需要去除其吸附的无机酸催化剂,这又导致新的污染。

图2-11 生产乙酰丙酸的Biofine工艺[138]
由于大量的文献都认为葡萄糖生成乙酰丙酸的过程涉及葡萄糖异构化为果糖和果糖脱水生成HMF这两个关键步骤,而路易斯酸对催化葡萄糖异构化为果糖具有较好的催化作用[77],因此一些路易斯酸,如CrCl3、FeCl3、CuCl2、AlCl3、CuSO4和Fe2(SO4)3等,也都被用于催化木质纤维素转化为乙酰丙酸,并发现具有较好的催化作用[19,156-158]。特别地,Peng等采用CrCl3在水热条件下催化纤维素降解能够得到67%的乙酰丙酸[19]。此外,部分研究尝试采用路易斯酸和布朗斯特酸协同催化葡萄糖转化为乙酰丙酸。如CrCl3+HCl、CrCl3+H3PO4等二元催化剂体系都被证明对转化葡萄糖制备乙酰丙酸具有较好的催化作用[158,159]。这些金属盐的腐蚀性相对较低,比使用液体无机酸更加安全。不过,从分离回收、毒性的角度考虑,这些金属盐并没有显著地优于液体无机酸。
为了解决均相催化剂使用中存在的催化剂分离回收的难题,部分研究报道了采用固体酸催化剂转化木质纤维素制取乙酰丙酸。例如,分子筛[37,160]、金属氧化物[161,162]、酸性(磺化或磷酸化) 金属氧化物[161,163,164]、酸性树脂[165-170]、磺化碳材料[171]等都被报道对转化木质纤维素及其衍生物己糖制备乙酰丙酸具有较好的催化作用。Zuo等[165]使用磺化的氯甲基聚苯乙烯作为固体催化剂转化纤维素制取了收率高达65%的乙酰丙酸。
值得一提的是,纤维素除了可以通过水解为葡萄糖,再由葡萄糖转化乙酰丙酸这一条路径,也在水相中直接部分氧化纤维素制备乙酰丙酸。Lin等使用ZrO2作为催化剂,在240℃下,以3.5MPa的N2-O2混合气体作为氧化剂去氧化纤维素得到收率为50%的乙酰丙酸。他们认为,该过程中纤维素首先转化为葡萄糖酸,葡萄糖酸再经脱羧转化为2-脱氧核糖,而2-脱氧核糖则脱水生成糠醇并进而转化为乙酰丙酸[172,173]。该方法的优势在于,反应过程中只产生极少量的水热焦炭,可以避免催化剂被水热焦炭包裹而失活,同时也避免反应过程中生成的大量水热焦炭堵塞反应器。
乙酰丙酸的分离和回收也是利用木质纤维素制备乙酰丙酸工艺的关键技术。由于反应过程中原料浓度不高,所以在生物质降解后得到的降解液中乙酸乙酯的浓度较低,而将这些低浓度的乙酸乙酯分离出来需要消耗大量的能量。Kang等将木质纤维素转化后得到的含有乙酸乙酯的降解液作为循环溶液去处理新的生物质原料,经过反应液的多次循环使用,可得到高浓度的乙酰丙酸(105g/L)和甲酸(39g/L),降低分离成本[174]。